In today’s competitive manufacturing landscape, speed and efficiency are paramount. CNC (Computer Numerical Control) machining has revolutionized the industry by providing precise and automated machining processes. However, as demands for faster production cycles increase, manufacturers are constantly seeking ways to enhance CNC machining speed without compromising quality.
In this blog post, we’ll explore the latest technologies and techniques that can help boost CNC machining speed, ensuring you stay ahead of the competition.
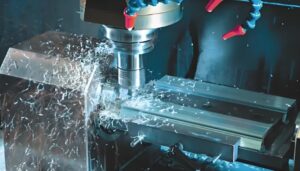
High-Speed Machining (HSM) Techniques
High-Speed Machining (HSM) is a game-changer for reducing machining time. By utilizing advanced cutting tools and optimizing cutting parameters, HSM allows for faster feed rates and spindle speeds. This technique not only shortens production time but also improves surface finish and accuracy. Key aspects of HSM include:
1.Optimized Tool Path Strategies
- Shortest path method: Select the shortest tool path to reduce cutting time and machine tool movement time.
- Spiral cutting: Use a spiral path to gradually cut deeper, reduce cutting forces and improve surface finish.
- Step-by-step cutting: Cut material in stages to avoid removing too much material at one time, reduce cutting forces and tool wear.
- Balanced cutting: Evenly distribute the cutting load throughout the entire machining process to avoid local overheating and excessive tool wear.
- Zigzag cutting: Use a zigzag cutting path to optimize material removal efficiency and reduce unnecessary tool movement.
2.High-Speed Spindles
These spindles enable faster rotations, which can significantly increase material removal rates.
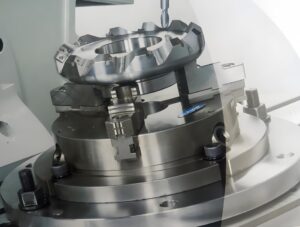
Advanced Tooling Technology
The choice of tooling plays a crucial role in machining speed. Investing in high-performance cutting tools can drastically improve machining efficiency. Technologies in advanced tooling include:
1.Ceramic and CBN Tools
These materials are designed for high-speed cutting and can handle tougher materials more efficiently.
2.Coated Tools
Applying coatings like TiN or TiAlN reduces friction and heat, extending tool life and maintaining cutting speed.
Adaptive Machining
Adaptive machining technology uses real-time feedback to adjust machining parameters dynamically. This approach helps in maintaining optimal cutting conditions, even as tool wear or material variations occur. Benefits of adaptive machining include:
1.Increased Stability
Real-time adjustments prevent tool breakage and improve machining consistency.
2.Enhanced Speed
By continuously optimizing cutting conditions, adaptive machining reduces idle time and speeds up the overall process.
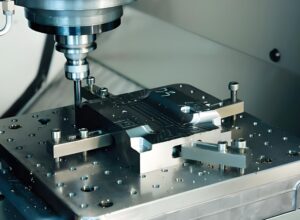
Automation and Robotics
Integrating automation and robotics into CNC machining processes can lead to significant speed improvements. Automation systems, such as robotic arms and automated tool changers, streamline production workflows by:
1.Reducing Manual Intervention
Robots handle repetitive tasks, allowing CNC machines to run continuously and at higher speeds.
2.Minimizing Setup Times
Automated tool changers reduce the time required to switch between tools, speeding up production cycles.
Enhanced Machine Control Systems
Modern CNC machines come equipped with advanced control systems that enhance machining speed. These systems include:
1.High-Speed Controllers
Advanced controllers process commands faster, enabling quicker response times and smoother operations.
2.Improved Feedback Systems
High-resolution encoders and sensors provide accurate feedback, allowing for finer control and faster machining speeds.
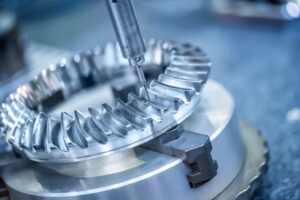
Optimized Coolant and Lubrication Systems
Effective cooling and lubrication are crucial for maintaining high speeds during machining. Optimized systems ensure that cutting tools remain cool and well-lubricated, which can:
1.Prevent Overheating
Proper cooling reduces the risk of tool failure and maintains cutting efficiency.
2.Improve Surface Finish
Effective lubrication helps in achieving a better surface quality while machining at higher speeds.
Conclusion
Increasing CNC machining speed is essential for staying competitive in the manufacturing sector. By adopting high-speed machining techniques, investing in advanced tooling, leveraging adaptive machining, integrating automation, utilizing enhanced control systems, and optimizing coolant and lubrication, manufacturers can significantly boost their machining efficiency. Embracing these technologies not only enhances production speed but also improves overall quality and cost-effectiveness.
Stay ahead of the curve by exploring these cutting-edge technologies and implementing them in your CNC machining processes. For more insights and personalized solutions, contact our team of experts today!