In today’s fast-paced manufacturing environment, speed and precision are crucial. CNC (Computer Numerical Control) machining has revolutionized the industry by providing a high degree of accuracy, but increasing the speed of CNC machining without sacrificing quality is a challenge many manufacturers face. This blog post explores practical techniques to boost CNC machining speed while maintaining product integrity.
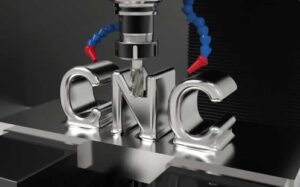
Optimize Tool Paths for Efficiency
1. Minimize Travel Distance
By optimizing tool paths, you can reduce the time the tool spends traveling between cuts. Techniques like trochoidal milling or high-speed machining strategies help minimize tool engagement and increase cutting speeds.
2. Reduce Tool Retracts
Reducing the number of times a tool needs to retract and reposition can significantly cut down cycle times. Continuous tool paths and smarter toolpath strategies can be programmed to maintain high speeds.
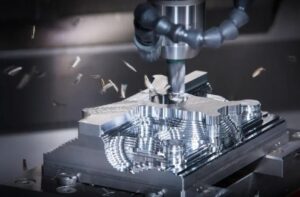
Utilize High-Speed Machining Techniques
1. High-Speed Spindles
Invest in machines with high-speed spindles that can handle faster tool rotations. High-speed spindles, coupled with the right tooling, enable faster material removal rates, especially on softer materials like aluminum or plastic.
2. Advanced Cutting Tools
Use cutting tools designed for high-speed machining. Tools made from materials like carbide or coated with specialized layers reduce heat buildup and wear, allowing for higher speeds and longer tool life.
Choose the Right Materials and Tooling
1. Optimize Material Selection
Some materials are better suited for high-speed machining. Lightweight metals such as aluminum and magnesium, or engineered plastics, can be machined at higher speeds without compromising on quality.
2. Tool Geometry
Selecting tools with the right geometry—such as sharper angles, optimized flute designs, and coatings—can significantly improve machining speeds. High helix angles, for example, help in quick chip evacuation, reducing downtime and increasing cutting speed.
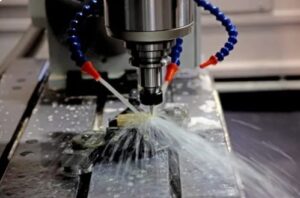
Leverage Advanced CNC Software
1. Adaptive Clearing
Modern CAM (Computer-Aided Manufacturing) software includes adaptive clearing strategies that adjust toolpaths dynamically to maintain optimal speeds. This reduces the load on the tool and allows for faster, more efficient machining.
2. Simulation and Analysis:
Use CNC software that provides accurate simulations and analysis. By previewing toolpaths and machine movements, you can identify potential bottlenecks and optimize before actual machining begins.
Maintain and Upgrade Equipment Regularly
1. Machine Calibration
Regular calibration of CNC machines ensures that they are operating at peak efficiency. Misalignments and wear can slow down operations and decrease accuracy.
2. Upgrade Controllers
Older CNC machines can benefit from controller upgrades that allow for faster processing of complex toolpaths. Modern controllers are better equipped to handle high-speed machining operations.
Implement Real-Time Monitoring and Adjustments
1. Machine Monitoring Systems
Utilize real-time monitoring systems to track machine performance. These systems can provide insights into tool wear, spindle speed, and feed rates, allowing for on-the-fly adjustments to maintain high speeds.
2. Feedback Loops
Implement feedback loops that automatically adjust machining parameters based on real-time data. This ensures consistent speed and precision throughout the machining process.
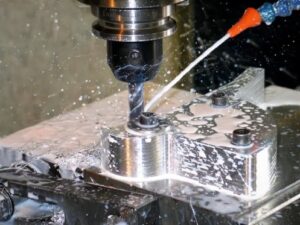
Use Efficient Cooling and Lubrication
1. High-Pressure Coolant Systems
High-speed machining generates more heat, affecting both tool life and material integrity. High-pressure coolant systems can remove heat quickly, allowing for higher speeds without damaging the tool or workpiece.
2. Minimal Quantity Lubrication (MQL)
MQL systems apply just enough lubricant to reduce friction and heat, which can improve cutting speeds and extend tool life, especially in high-speed operations.
Conclusion
Improving CNC machining speed involves optimizing tools, materials, and machine settings. By implementing these techniques, manufacturers can reduce cycle times, increase productivity, and maintain high-quality outputs. As the industry evolves, staying ahead with the latest machining strategies and technologies is crucial for maintaining a competitive edge.
By following these best practices, your CNC operations can achieve faster machining times, leading to greater efficiency and profitability. Whether you’re optimizing for small-batch production or large-scale manufacturing, these strategies will help you meet your speed goals without compromising quality.