Fundamentals of Rapid Prototyping Technology
Rapid Prototyping (RP) is an advanced manufacturing technology that creates three-dimensional solid models by stacking materials layer by layer. The basic principle involves layering 3D CAD model data and building the object by stacking materials layer by layer. This fast, flexible, and efficient technology significantly shortens product development cycles, reduces costs, and enables the manufacturing of complex structures.
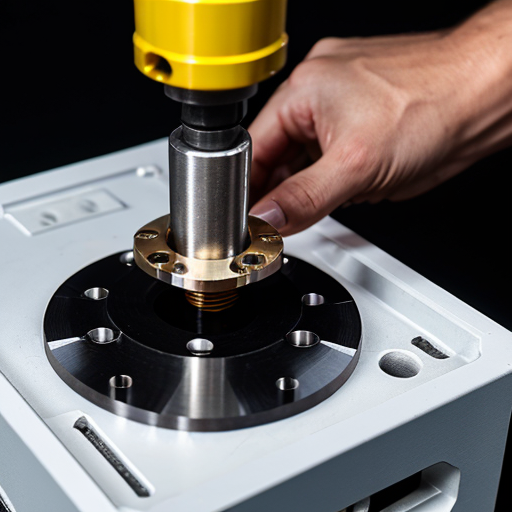
Key Applications of Metal Rapid Prototyping Technology
1. Key Percentage of Solid Particle Content in Metal Materials
The solid particle content of metal materials is an important factor affecting the quality of forming. A reasonable solid particle content can ensure the fluidity and uniformity of materials, thereby improving forming accuracy and material performance. In practical applications, the optimal proportion of solid particle content can be determined through experiments and simulations.
2.Analyze the dynamics of rapid prototyping of metal materials
The study of rapid prototyping kinetics for metal materials covers processes like heating, melting, flow, cooling, and solidification. These dynamic processes affect molding speed, quality, and accuracy, requiring experimental and numerical analysis to optimize parameters and ensure quality.
3.Rapid Prototyping of Metal Materials in Mechanical Manufacturing
In mechanical manufacturing, combining traditional techniques like CNC machining, casting, and heat treatment enables high-quality rapid prototyping of metal materials. Optimizing process parameters and equipment configuration improves molding accuracy and efficiency to meet various application needs.
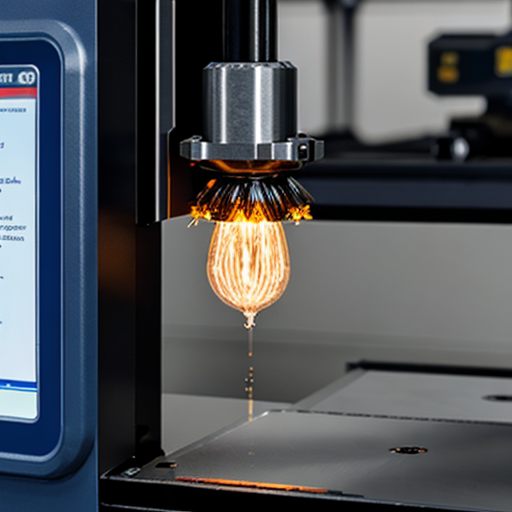
Application of Rapid Prototyping Technology in Micromechanical Manufacturing
1. Point curing unit
The point solidification unit uses a laser or electron beam to locally heat and solidify the material, allowing precise control of the forming area and enabling high-precision microstructure manufacturing. This technology is valuable in micro-mechanical manufacturing, enabling the precision production of complex microstructures.
2.Constraint liquid sheet
Constrained liquid sheet technology controls the flow and solidification of liquid materials by applying constraints. It enhances forming accuracy and surface quality, making it widely used in the precision manufacturing of micro-mechanical components.
3.Scraping device
The scraping device is used to flatten the surface of stacked materials, ensuring uniform thickness of each layer, thereby improving forming accuracy and interlayer bonding strength. In the rapid prototyping process, the use of a scraping device can effectively reduce molding defects and improve product quality.
4. Vector scanning
Vector scanning technology controls the scanning path and speed to accurately depict each layer’s cross-sectional shape. It improves detail and complexiformorming, making it ideal for manufacturing high-precision, complex structures.
5.BMP data format
The BMP data format stores and transmits cross-sectional images of 3D models, ensuring data integrity and consistency. Using this format improves molding quality and efficiency, accommodating various levels of model complexity.
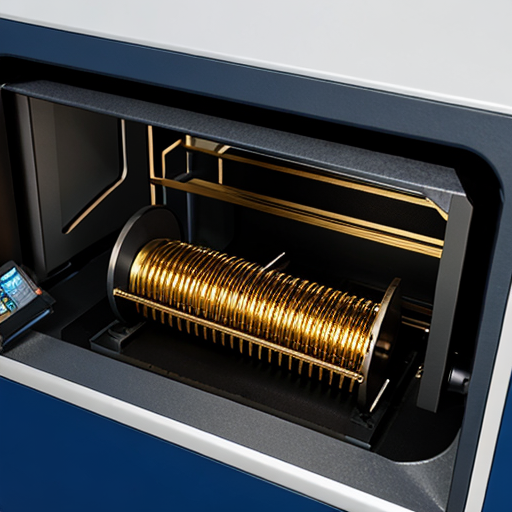
Challenges in Metal Rapid Prototyping for Mechanical Manufacturing
1.The cost of technical equipment is relatively high
Metal rapid prototyping equipment, especially high-precision molding machines, is expensive, and requiressignificant initial investment. This limits its adoption in small and medium-sized enterprises and calls for technological advancements and large-scale production to reduce costs.
2.Limited synthetic metal materials
Currently, the types of metal materials for rapid prototyping are limited, and their properties fall short of those used in traditional manufacturing. Advancing materials science and innovation is needed to develop high-performance, diverse materials to meet various application needs.
3.There are certain issues with the software
Current rapid prototyping software has limitations in data processing, path planning, and process control, impacting molding efficiency and quality. Improving software algorithms, functionality, stability, and usability is essential to enhance overall molding performance.
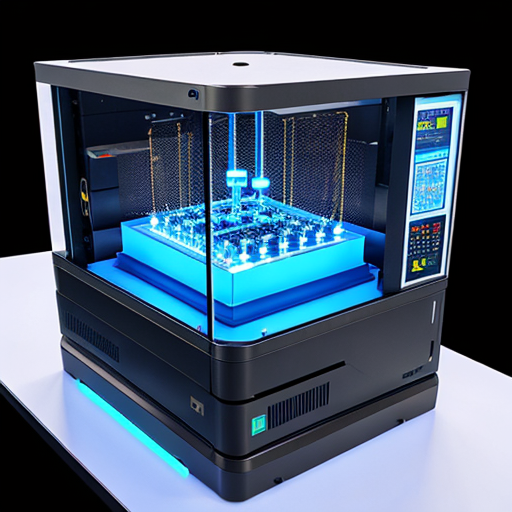
Strategies for Metal Rapid Prototyping in Mechanical Manufacturing
1.Improve enterprise management system
Improving the enterprise management system, optimizing production processes, and enhancing the skills of technical personnel can boost equipment utilization and production efficiency. Additionally, developing a solid technical training plan will elevate the overall expertise of the team.
2.Develop new RP materials
Developing new rapid prototyping metal materials can enhance performance and variety to meet the needs of different applications. This progress will expand the scope of rapid prototyping technology across various industry es.
3. Develop new membrane methods
Develop new membrane methods to improve material utilization and molding efficiency, and reduce production costs. Through technological innovation, explore more efficient and economical membrane manufacturing processes, and promote the popularization and application of rapid prototyping technology.
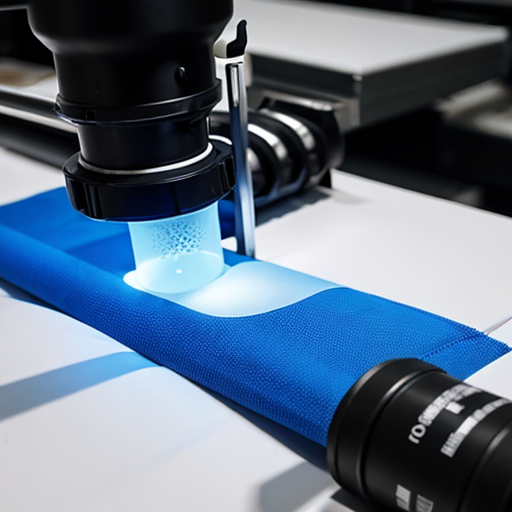
conclusion
Metal rapid prototyping technology has great potential in mechanical manufacturing. By optimizing processes, developing new materials, and improving management systems, current challenges can be overcome, advancing micromechanical manufacturing. As technology evolves, metal rapid prototyping will drive innovation and transformation in the industry.