CNC machining centers and CNC lathes are key in modern manufacturing, differing in processing technology, application, and functions. Understanding these differences helps choose the right equipment for better efficiency and product quality.
Basic definition and use
A CNC machining center is a versatile machine that combines milling, drilling, boring, and reaming, with an automatic tool change system (ATC) for multi-step processing. It is commonly used in the mass production of complex parts.
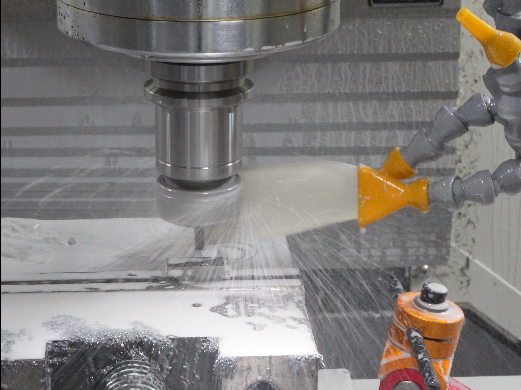
CNC lathe is a CNC machine tool used for turning processing, mainly used for processing rotating parts. It rotates the workpiece with a fixed turning tool, ideal for machining inner/outer circles, end faces, cones, and threads on shafts and discs.
Structure and working principle
CNC machining center usually consists of a machine tool body, CNC system, servo drive system, automatic tool changer, etc. Its core component, the CNC system, controls tool and workpiece movement through pre-programmed programs for multi-axis linkage and high-precision processing.
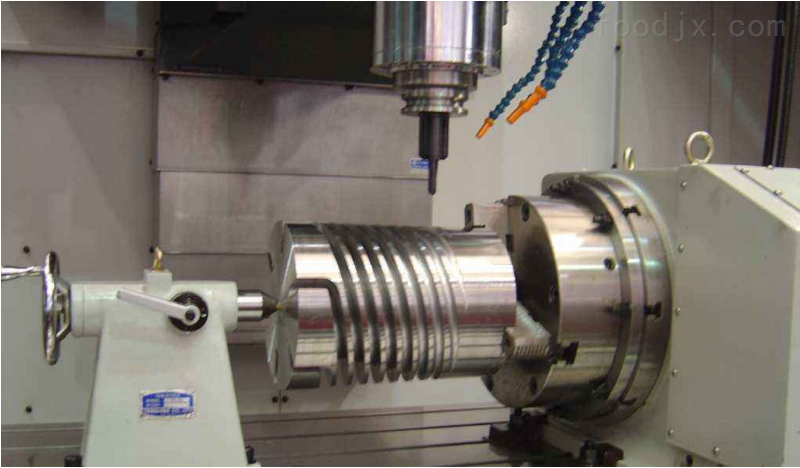
The main components of CNC lathes include a machine bed, spindle box, feed system, CNC system, and tool holder. The working principle of CNC lathes is that the workpiece rotates on the spindle, and the tool moves along the set trajectory to cut the workpiece. The CNC system controls the spindle speed, tool feed amount, and motion trajectory according to the pre-programmed program.
Processing objects and process characteristics
CNC machining centers are suitable for machining complex plane and curved parts, especially parts with multiple processes and high precision requirements. Its processing range is wide, including planes, grooves, gears, molds, etc. The machining center can complete multiple processes in one clamping, improving production efficiency and processing accuracy.
CNC lathes are mainly used for the processing of outer circles, inner holes, end faces, and threads of rotating parts. It is efficient and precise, ideal for mass production of simple, high-precision rotating parts like shafts and discs. The CNC lathe rotates the workpiece while the tool moves, making it suitable for parts with a large aspect ratio.
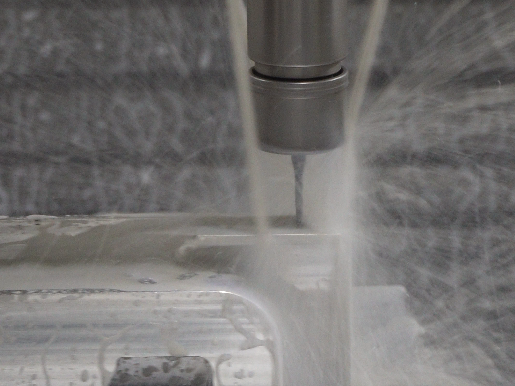
Tool system and degree of automation
CNC machining centers feature automatic tool changers and magazines for quick tool switching, while high-end models include automatic measurement systems and intelligent programming for enhanced automation and efficiency.
CNC lathes use tool holder systems, with some high-end models featuring automatic tool changers, though their speed and versatility lag behind machining centers. While their automation is lower, they still excel in efficiency and accuracy for specific parts.
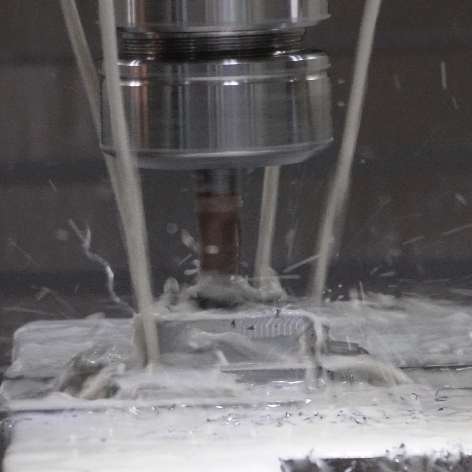
Operation and programming
The operation and programming of CNC machining centers are relatively complex because they involve multi-axis linkage and multi-process machining. Programmers need to have high programming skills and process knowledge, be able to reasonably arrange machining steps, optimize tool paths, and improve machining efficiency and quality.
The operation and programming of CNC lathes are relatively simple because they mainly perform cutting machining on two-dimensional planes. Programmers only need to consider the shape and size of the workpiece and write simple turning programs. For some complex turning processes, such as thread and taper processing, although some special programming skills are required, the overall programming difficulty is relatively low.
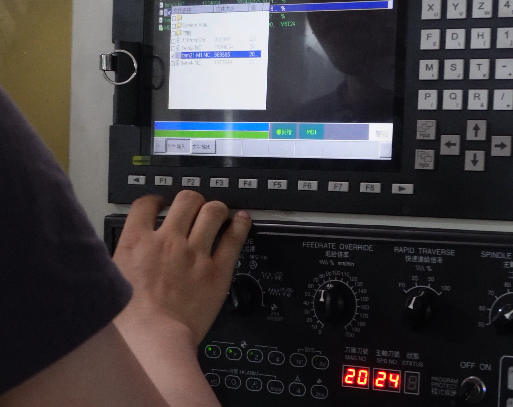
Applicable industries and application scenarios
CNC machining centers are widely used in aerospace, automobile manufacturing, mold manufacturing, precision instruments, and other industries. Its versatility and high precision make it suitable for manufacturing complex parts and high-precision components.
CNC lathes are widely used in machinery manufacturing, automobile parts, power equipment, and other industries, especially suitable for processing rotating parts with regular shapes and mass production. Its efficient processing capacity and precision make it an ideal choice for the production of shaft and disc parts.
Conclusion
CNC machining centers and CNC lathes each have their advantages. The former performs well in the processing of complex parts with multiple processes, while the latter has an advantage in the efficient turning of rotating workpieces. The selection of appropriate equipment should be determined according to specific processing requirements, production batches, and budgets. If your processing tasks involve complex shapes and multi-process processing, CNC machining centers will be a more suitable choice; if it mainly involves the processing of rotating workpieces, CNC lathes can provide higher production efficiency and precision.