In modern mechanical manufacturing engineering, one very important industry is the injection mold industry, and many new product development and production are mainly based on mold manufacturing technology, especially in the fields of automobile, light industry, electronics and aerospace industry.
Mold manufacturing technology is changing fast. Future growth depends on intelligent, automated, and green manufacturing. Global market competition is also increasing. Enterprises must keep innovating and improving quality to stay competitive.

Development situation
At present, many countries, especially some countries with rapid economic development and advanced technology, pay great attention to mold manufacturing technology research and development, and actively promote the development of the injection mold manufacturing industry, the extensive use of a variety of technologies and advanced equipment to improve and optimize the mold manufacturing process, and thus improve the quality of mold development.
Among them, the injection molding process mold mold technology has ordinary injection molds, inverted injection molds, three-plate molds, in-mold transfer injection molds, stacked molds, two-color injection molds, low-pressure injection molds, high-gloss injection molds, as well as micro-foam injection molds.
Interdisciplinary and many related fields of application
Mold technology development is the key to the development of the mold industry, including interdisciplinary and many related areas of application. Specifically including the following aspects:
1.Mechanical Engineering
Processing and manufacturing: mold technology needs to be combined with machining processes, such as CNC machining, wire-cutting, EDM, milling, turning, etc.
Material selection: it involves the study of the characteristics and processing performance of materials such as die steel, aluminum alloy and copper alloy.
2.Material Science
Metal materials: mold making usually requires high-strength, wear-resistant metal materials.
Polymer materials: molds are mainly applied to plastic molding, which requires knowledge of the plastic’s fluidity, thermal conductivity and other characteristics.
Composite materials: used in the manufacture of special molds or complex shaped parts.
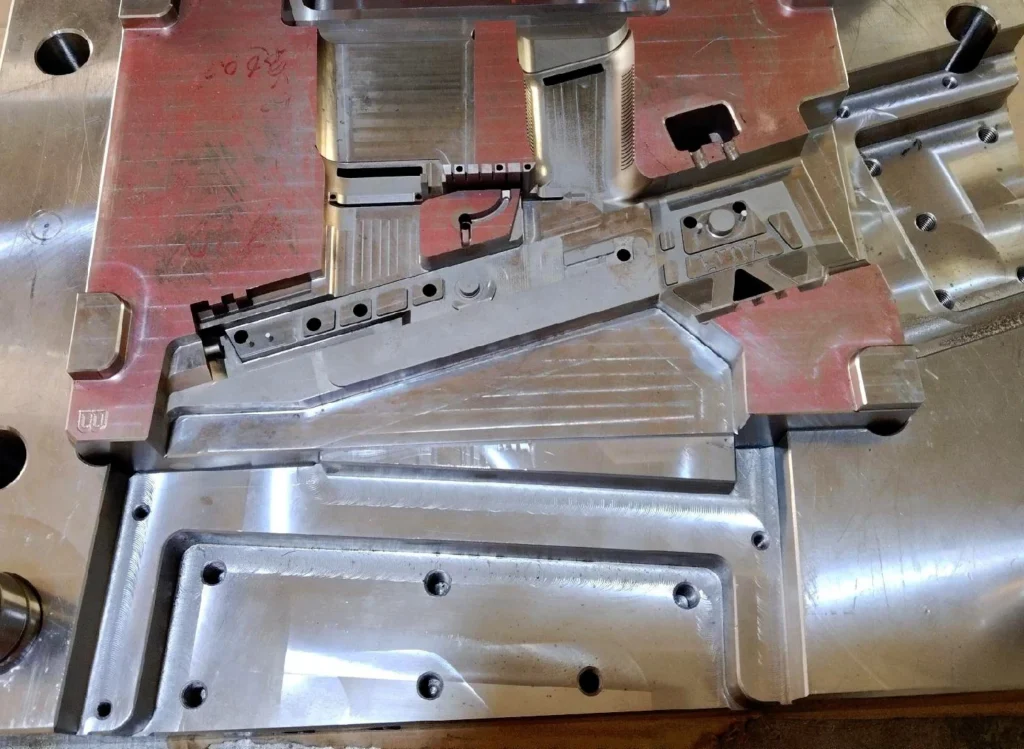
3.Industrial design
Product design: the design of the mold needs to be customized according to the product structure, appearance and functional requirements.
User experience: In order to meet ergonomic requirements, industrial design principles may need to be referred to in mold design.
4.Computer Science
CAD/CAE/CAM: Computer-aided design, simulation analysis and processing programming are widely used in mold design and processing.
Numerical simulation: The flow behavior of materials in the mold cavity is analyzed through fluid simulation and heat conduction simulation.
5.Electronic technology
Intelligent molds: Molds with integrated sensors and control systems can monitor parameters such as pressure and temperature in real time to improve yield.
Electrical control: Mold forming equipment (e.g., injection molding machines, die casting machines) needs to work with the mold system.
6. Chemical Engineering
Polymer chemistry: involves the relationship between the molecular structure and properties of polymer materials in the injection and blow molding process.
Coating technology: through chemical coating technology to enhance the mold wear resistance, corrosion resistance.
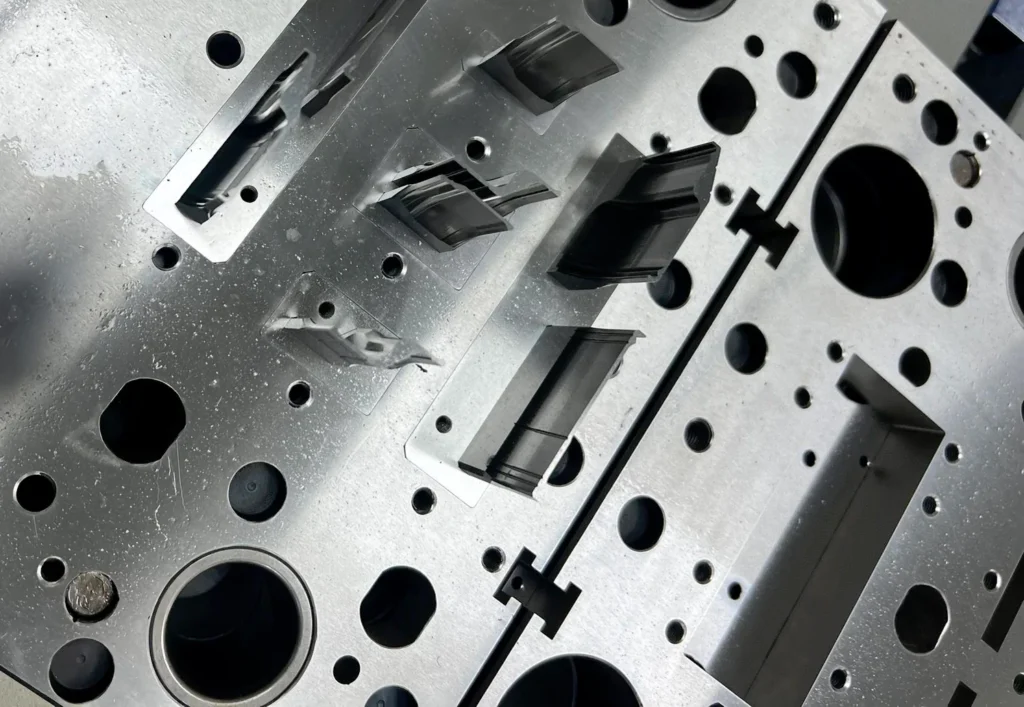
7.Physics
Thermodynamics: mold design involves the coefficient of thermal expansion of materials, thermal conductivity.
Mechanical analysis: the mold must withstand high pressure, involving mechanical stress and deformation calculation.
8.Automation and Robotics
Automated production: mold technology is combined with automated equipment to maximize production efficiency.
Injection molding robots: for product pickup, assembly, etc.
9.Management Science
Project Management: Mold development requires coordination of multiple aspects of design, manufacturing and delivery.
Cost control: Balancing quality, delivery time and cost in the mold development process.
10.Environmental Science
Green Manufacturing: Research on how to reduce material waste and energy consumption by optimizing mold design.
Sustainable Materials: Explore the application of environmentally friendly plastics and renewable resources in molds.
As a production tool, mold technology is widely used in automotive manufacturing, home appliances, medical devices, aerospace, consumer electronics and other industries, and its interdisciplinary use significantly improves production efficiency and product quality.
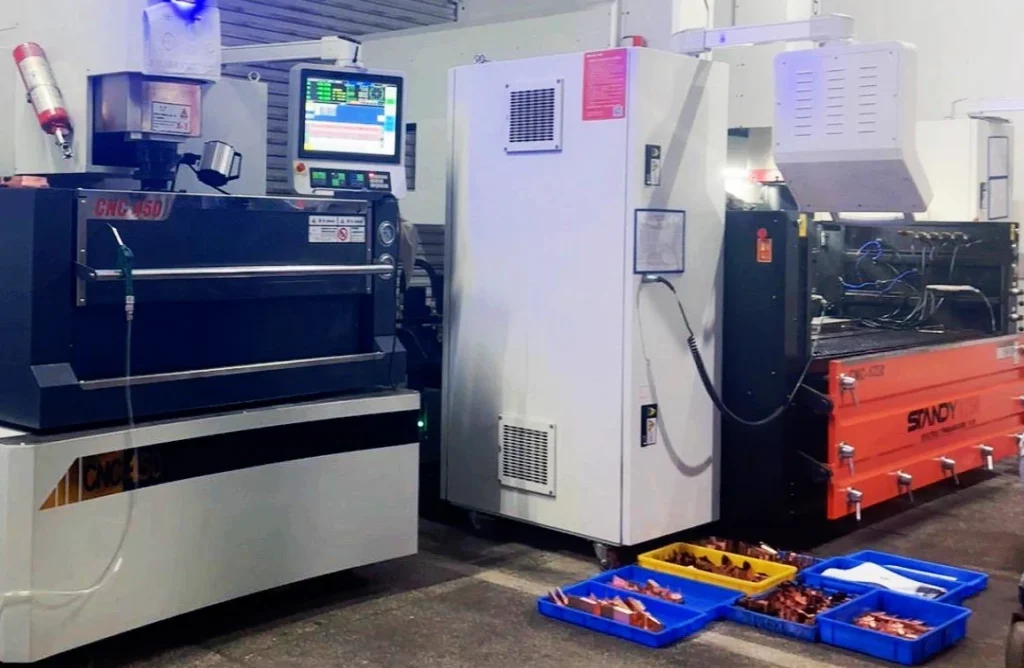
Advanced technology of computer processing-assisted machining
1.Highly efficient mold processing technology
Basically all mold processing uses a microcomputer control computer program, its system must be very reliable, each functional system should be configured with a standard program model.
The main processes of mold processing can be divided into rough milling, tempering heat treatment, fine milling, EDM, fine milling, high-speed milling, drilling, deep hole drilling, grinding machine, mold, and surface corrosion texture.
These advances rely on advanced equipment like mirror spark machines, five-axis high-speed milling, profiling drilling, and laser engraving for surface textures. Each technology depends heavily on computer-aided design and programming control.
2.High-speed CNC grinding manufacturing technology
High-speed spindle use needs to maintain high-speed dynamic balance, and can be equipped with electric balance system or electro-hydraulic balance system.
High-speed CNC grinding machine has many advantages, such as large grinding volume, high dynamic accuracy, high vibration resistance and stability, etc., the whole process requires a combination of high automation and high reliability.
High-speed CNC grinding wheels require high mechanical strength, must be fast and absolutely reliable, and also have high bond strength and wear resistance to further reduce the degree of wheel wear.
3.Three-dimensional control mold design, evaluation and manufacturing technology
The previous two-sided mold design can no longer meet modern high-tech production and integration standards. Mold design now requires advanced technology to evaluate, identify, and support diversified production needs. It also demands electronic data and clear 3D visual simulation of the mold parts production process.
Three-dimensional program control data processing software is now widely used in industrial design data analysis, mold condition assessment, and digital cutting process control. It can generate visual simulations of programs and integrate and process related information.
4.3D Cavity and Mirror EDM Integration
When parts are finished using EDM, very little discharge energy and clearance is required to process them. As a result, when the processing area is large, a large parasitic capacitance is formed between the working area and the electrode, a concentrated discharge occurs, and the quality of the surface machining finish deteriorates even more.
A solid fine powder is added to the kerosene working medium. This increases the distance between electrodes, reduces capacitance, and disperses the discharge path. This method helps accurately form a 3D cavity in the mold and mirror EDM integration.
Technology Development Trends
1.In the network trend of mold software applications
With the development of globalization, mold enterprises in competition, cooperation, production and management of rapid development. In such a social context, the mold industry in the virtual design and flexible production technology is very necessary.
The United States in the “21st Century Manufacturing Enterprise Strategy”, said that as of 2006, will be the automotive industry for the rapid production of the implementation of three virtual engineering solutions, and automotive development time from 40 months into 4 months.
The latest integrated system includes mathematical and geometric modeling, reverse engineering, diverse industrial design, simulation, rapid prototyping, CNC programming, and standardized measurement and analysis;
Each functional module of the system can work independently, but also through the data interface with other systems compatible with the work, the real realization of specialization and openness unity.
2.Integrated mold digital control software functions
Mold manufacturing process of digital control software integration function so that the software management module is relatively comprehensive, can provide resources and information integration and sharing, and then each module function corresponds to the structure of the corresponding mold design.
The same parameter model applies to different functional modules. It covers mold product design, assembly, performance verification, and operational testing. This controls the entire production process to maximize operating profit.
For example, a British company offers a complete mold manufacturing management software. It supports mold production, workpiece surface structure, and 3D shape design. It also handles complex structural solutions, engineering design, and plastic mold design. Together, these form an intelligent control system.
Mold manufacturing can also support engraving process modeling design. Its reverse production process and on-site monitoring system bring great benefits. Today, many automotive manufacturers actively use mold manufacturing engineering software.
3.Intelligent mold software trends
The new generation of mold software and CAD modeling moves beyond simply copying traditional design and calculation methods. It applies advanced design theories and expert casting guidance. This software draws on a wealth of knowledge and successful experience. It helps overcome the limitations faced by individual mold designers and operators.
With the help of artificial intelligence, CAI and other methods, scientific rationalization of design can be further realized;
The whole process, from design, research and analysis, evaluation of expectations to the production process in practice, can be fully automated;
In addition, production-oriented knowledge-based intelligence functions are key indicators for assessing the usability of mold software.
Conclusion
In modern society, science and technology develop rapidly. Advanced mold manufacturing technology drives progress in information and control technologies. These technologies are integrated systematically in every step of mold production. This integration makes them applicable to the entire mold manufacturing process. Further realize the mold high quality and flexible production, so that the whole production process efficiency is reduced.