As a high-precision and high-efficiency processing method, laser processing technology is being widely used in the field of engineering machinery manufacturing. With the engineering machinery manufacturing industry’s continuous pursuit of product quality and production efficiency, the application of laser processing technology is developing and evolving.
Laser processing technology can achieve cutting, welding, punching, engraving and other processing operations on a variety of materials, which brings many advantages for engineering machinery manufacturing.
Overview of laser processing
This technology is the use of laser beams on the material processing methods, just focus the laser beam to a very small point, so that the material in its role in the melting, evaporation, combustion or stripping and other physical or chemical changes, so as to achieve the processing of the material and change.
Cutting of materials using a laser beam of high energy density, where the laser beam generates high temperatures on the surface of the material, causing it to melt or evaporate, and cutting the material into the desired shape by air flow or mechanical force.
Welding of materials using a laser beam, where the laser beam generates high temperatures at the welded joint, causing the material to melt and form a weld, and high quality welding is achieved by controlling parameters such as the power, speed and focus position of the laser beam;
The laser beam can cause local melting or evaporation to form holes or patterns, and can also melt or change the organisational structure to form a hardened layer or improve material properties; the laser beam can even be used to melt metal powders or welding wires layer by layer to achieve rapid prototyping and customised production of metal parts.
Laser processing has a high degree of controllability. By adjusting laser power, frequency, and focus, precise control of depth, speed, and shape can be achieved. It also offers high precision and fast processing. With its controllability and efficiency, laser processing is widely used in machinery manufacturing.
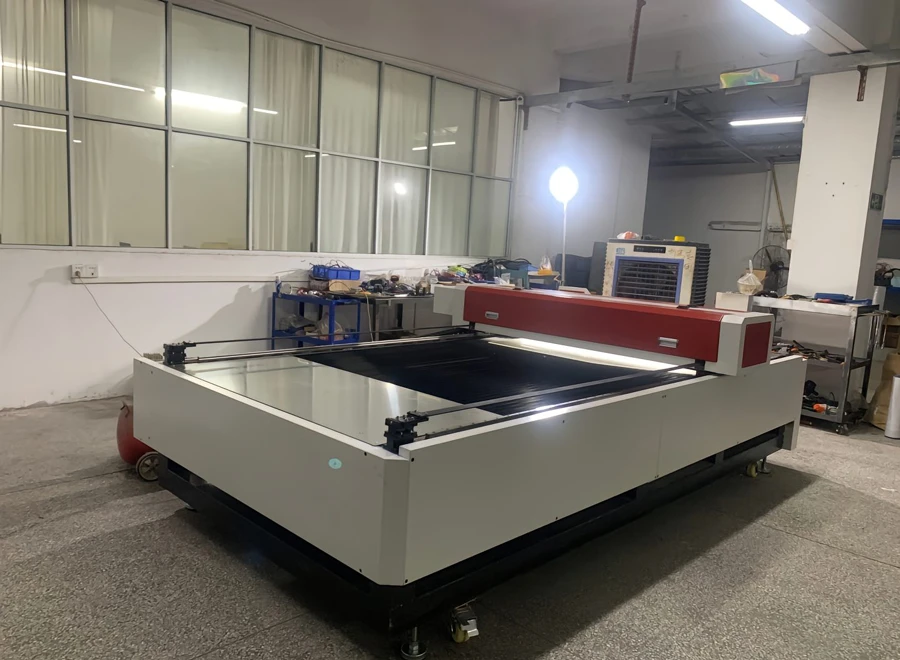
Laser machine
Applications
1.Application of cutting and dowelling
Cutting down is a common application of laser processing technology, used to cut the material into the required shape and size.
Laser cutting has high precision and fineness, and the diameter of the laser beam can be controlled between a few microns and a few millimetres, which can realize the cutting of fine structures and complex shapes, and the cutting precision is affected by the quality of the laser beam, the precision of the focusing system and the characteristics of the material.
Laser cutting offers high speed and processing efficiency. The laser beam can cut materials in a very short time. It is suitable for mass production and high-efficiency operations. Cutting speed is affected by laser power, material thickness, and quality requirements.
Laser cutting can achieve high-quality cutting edges with small heat-affected zones and deformation. Cutting quality is affected by laser power, cutting speed, gas assist and material properties, and appropriate gas assist can help remove molten material and improve cutting quality.
A company working with RuiYI operates an offloading centre equipped with various advanced machines. These include fine plasma cutters, fibre laser cutters, and flat bevel cutting equipment. It also features pipe penetration line cutters, drilling and cutting compound machines, and profile cutting tools. The centre offers offloading services for products from many manufacturing industries.
This discharging centre covers a wide range of products. It processes parts like hoods, fuel tanks, and cabs. These are used in nearly all major types of construction machinery. The material thickness it handles ranges from 1mm to 25mm. It can cut ordinary Q235A steel and high-strength plates up to 1000MPa.
The centre is also equipped with three 2D laser cutting machines (Fig. 1) and two 3D laser cutting machines (Fig. 2).
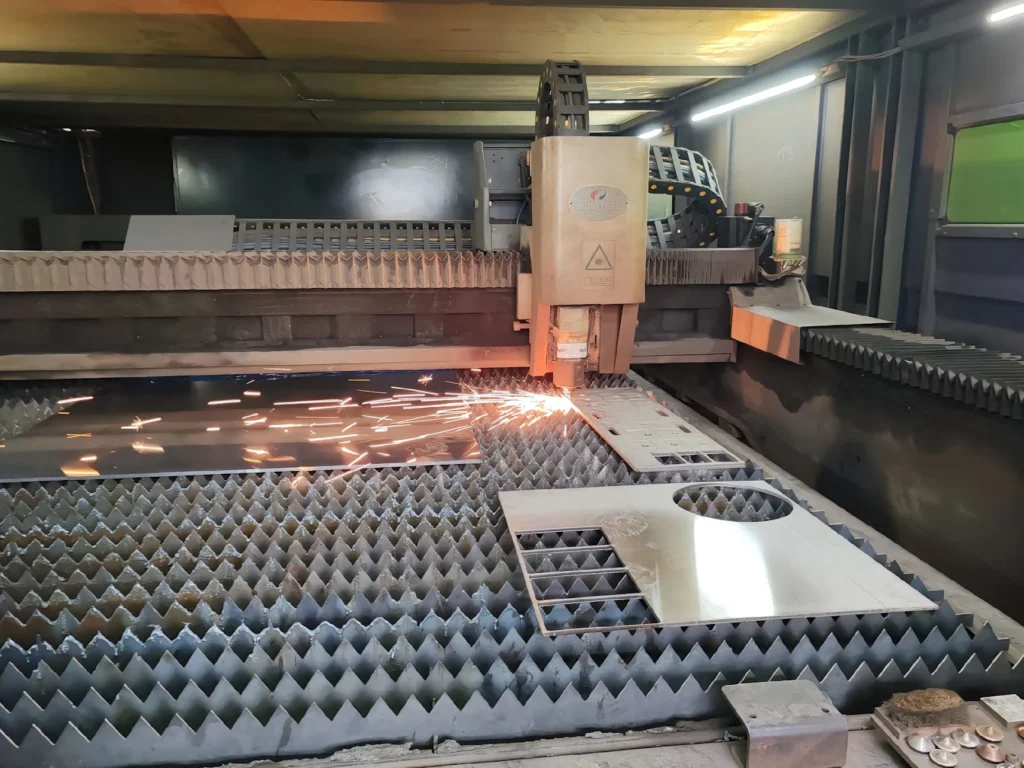
Fig 1 2d laser cutting
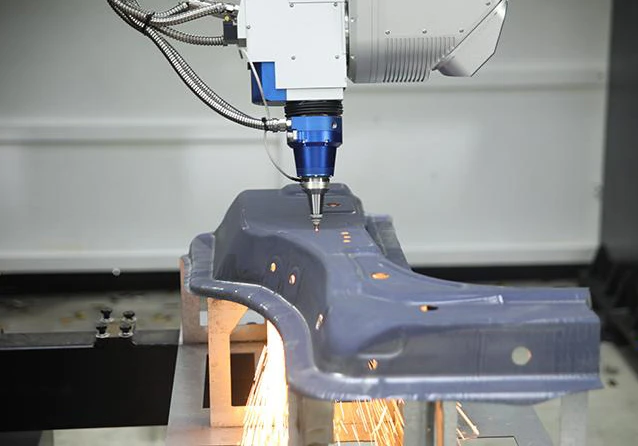
Fig. 2 3D laser cutting
Fig. 1 2D laser cutting machine Fig. 2 3D laser cutting machine These machines allow for finer and more complex cutting requirements. The company’s discharging centre has a wide range of laser cutting equipment, which can meet the discharging needs of construction machinery manufacturers and ancillary enterprises, providing high-quality and high-efficiency cutting services.
In the construction machinery plate processing industry, there are two main types of laser cutting machine technology products, namely CO2 laser cutting machine and fibre laser cutting machine. Choosing a laser cutting machine requires consideration of factors such as material thickness, cutting requirements, productivity and economic considerations.
CO₂ laser cutting machines use CO₂ gas as the laser medium. Electronic excitation generates the laser beam. These machines are suitable for cutting thick materials like steel and stainless steel plates. They offer higher power and large cutting capacity. CO₂ lasers are ideal for cutting large plates. Although their cutting speed is slower, the cutting quality is high.
Fibre laser cutting machine uses a fibre laser as the laser source, and transmits the laser beam to the cutting head through the fibre.
Fiber laser cutting machine is suitable for cutting thin materials, such as thin steel plate, aluminium plate, etc. It has high cutting speed and small heat-affected zone, and is suitable for high-speed cutting and fine cutting.
In addition to conventional laser cutting down, the laser cutting technology also has obvious application advantages in round hole cutting, reserving craft openings and craft sample making.
Laser cutting technology can realise high-precision round hole cutting, whether it is a single hole or an arrangement of multiple holes, which can be accurately completed by the laser cutting machine. Compared with the traditional drilling process, laser cutting can save the time of drilling and improve production efficiency.
In engineering machinery plate processing, sometimes need to reserve process openings on the plate for subsequent welding or assembly process, laser cutting technology can accurately cut out the required shape and size of the openings, to ensure the quality and accuracy of the openings, and improve production efficiency.
In engineering machinery plate processing, often need to make process samples, used to test and verify the cutting process, laser cutting technology can be designed to cut out the shape of the sample plate accurately, to ensure the accuracy and consistency of the sample plate. Compared with the traditional template production methods, laser cutting can save production costs and time.
2.Application in the field of welding
Structural parts in engineering machinery usually require large-scale welding, laser welding can achieve efficient, high-quality welding of structural parts, the high energy density of laser welding and the small heat-affected zone of the weld can achieve deep welding and reduce deformation, to ensure the strength and stability of the welded joint.
Laser welding can achieve high-speed, high-precision pipe welding, laser welding can be completed in a shorter period of time, reducing the production cycle and improving production efficiency.
Sheet metal parts in construction machinery usually need sheet metal welding, laser welding can achieve high precision, no deformation of the sheet metal welding, laser welding can be welded in a smaller heat-affected zone, reducing deformation and thermal damage, to ensure the quality and appearance of the welded joints.
Engineering machinery in some complex structural components, such as curved parts, shaped parts, etc., need to carry out complex structure welding, laser welding can achieve high quality welding of these complex structures, laser welding flexibility and focusing so that it can be welded in a narrow space and difficult to reach the region to meet the needs of complex structure welding.
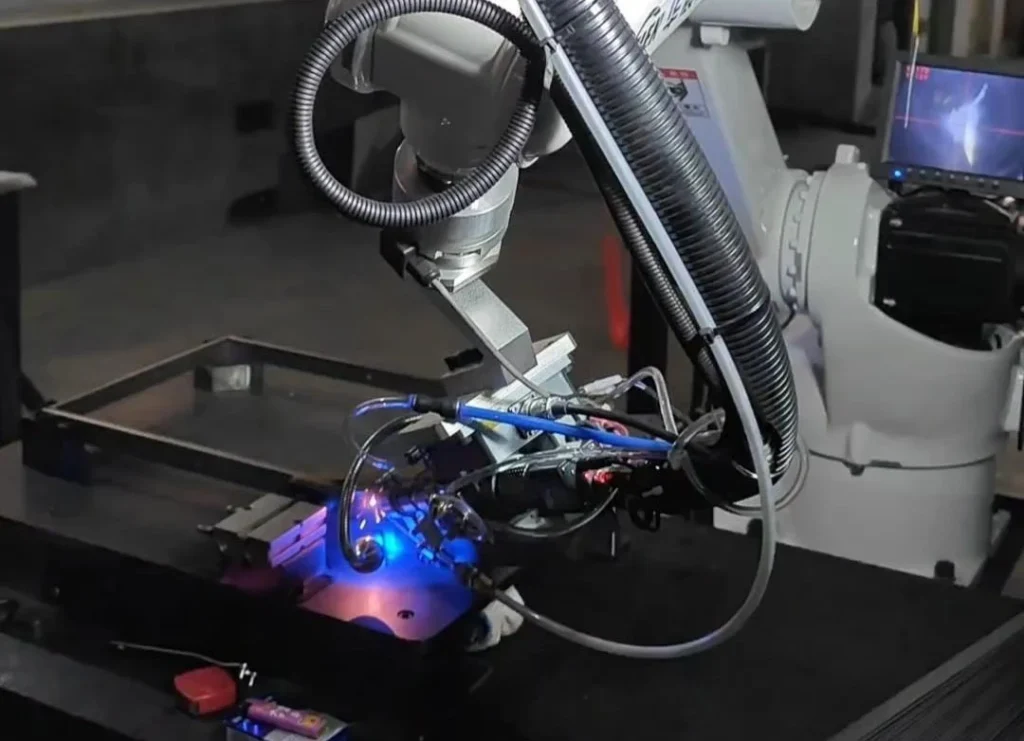
For example, laser-dual wire MAG composite welding combines the technology of laser and composite MAG welding. It combines the advantages of laser and composite MAG welding to achieve a high quality and efficient welding process.
Laser welding is a high energy density welding method, through the focusing of the laser beam, the welding material will be rapidly heated to the melting or fusion state, to achieve the welding. Laser welding has the advantages of small heat-affected zone, fine weld seam and small deformation, and is suitable for precision welding and deep welding.
Composite MAG welding can provide higher welding speed and better seam quality, suitable for large-scale welding and high-efficiency welding.
The combination of the high energy density of laser welding and the stable welding process of composite MAG welding can achieve high-quality welded joints.
The small heat-affected zone of laser welding reduces distortion and heat damage, while composite MAG welding provides a stable welding arc and better weld quality.
For the specific welding requirements of construction machinery, it is necessary to select and adjust the laser power of laser – composite MAG welding, laser beam diameter, laser focal length, composite MAG welding current, voltage, wire type and wire feeding speed and other parameters, in order to achieve the best welding results.
According to the requirements of construction machinery welding, select the appropriate welding material, and clean, de-oil, de-oxide, to ensure the quality of the welding material and the surface state, in order to improve the welding quality and strength.
Laser-composite MAG welding needs both laser and MAG welding equipment to work together. The system must be debugged and optimized. Laser alignment and focus must be adjusted precisely. MAG welding parameters like current, voltage, and gas flow must also be tuned. This ensures both welding methods work in synergy.
In the laser-composite MAG welding process, real-time monitoring and control are essential. Sensors and systems track welding temperature, weld shape, and speed. They also detect defects and quality issues during welding. Feedback control allows timely parameter adjustments to maintain weld quality and consistency. After welding, quality inspection and evaluation are necessary. This includes mechanical performance tests and fatigue life assessments of the joints. Mechanical performance testing and fatigue life assessment to ensure the reliability and durability of welded joints.
3.Application of cladding technology
Laser cladding technology uses a laser beam to heat and melt the material’s surface. Then, it clad a layer of alloy material on the surface. This forms a protective layer with specific properties. The layer can repair damaged parts or improve performance. It enhances abrasion resistance, corrosion resistance, and high-temperature resistance.
The surface of construction machinery will be affected by wear and tear, corrosion or fatigue and other factors, the performance will be reduced. And laser cladding technology can be used for surface repair. By cladding alloy materials on the damaged area, the original size and performance of the surface can be restored and the service life of construction machinery can be extended.
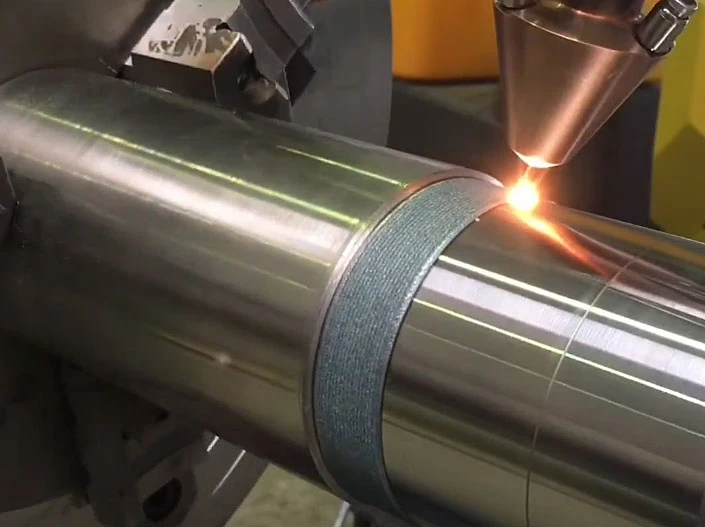
When construction machinery parts need special properties, laser cladding can modify the material surface. It adds a layer of special alloy. This improves strength, hardness, or wear resistance. The enhanced surface meets the special requirements of the machinery.
For example, laser phase change hardening technology improves the hardness and wear resistance of materials by forming a high hardness phase change layer on the material surface through laser heating and rapid cooling.
The working principle is that the laser beam has high energy density. It rapidly heats the material surface. At the same time, the scanning speed and power are controlled. The material surface cools rapidly. This forms a phase change. During the phase change, the material’s crystalline structure changes. A phase change layer with high hardness forms.
After the formation of the phase change layer will be rapidly cooled and solidified to form a hard surface layer, the control of the cooling rate can affect the organisation and hardness of the phase change layer.
Development prospects analysed
1.Automation direction
The development of laser processing automation is an important trend. It improves productivity in engineering machinery manufacturing. It also enhances product quality and production flexibility. Automation promotes the industry’s overall development. The engineering machinery sector is moving toward smarter and more efficient production.
Automated processing systems enable automatic control and monitoring of laser processing. They include automated workpiece clamping, laser head control, and process parameter adjustment to automate the entire process.
Robotic laser processing systems combine laser and robot technologies to automate workpiece processing. They follow preset paths and parameters, adapting to different shapes and sizes to improve flexibility and efficiency.
Automated process planning can generate optimal laser paths. It uses workpiece geometry and processing requirements as input. This reduces manual intervention and trial and error. It improves consistency and processing efficiency. Automated data analysis enables timely feedback control. Processing parameters are adjusted in real time. This ensures stable and consistent processing quality.
Laser processing technology can integrate with automation equipment like conveyor lines and loading manipulators. This enables automated workpiece handling and processing, improving production line automation and productivity.
2.Miniaturisation trend
The miniaturisation trend in laser processing focuses on small-sized workpieces and micro-structure applications. With ongoing advancements, lasers achieve smaller beam sizes and greater processing precision. Laser microfabrication is widely used in micro parts and microelectronic devices.
Through the high energy density and focusing ability of the laser beam, precise cutting can be achieved on microfine structures, such as microholes and microgrooves.
Laser micro-welding technology can be used for precise welding of micro-sized workpieces. The laser’s heat and focus enable encapsulation of micro-electronic devices. It also connects micro-wires on fine structures.
The laser’s energy and focus enable fabrication of micro-hole filters and micro-channels on fine structures.It supports high-throughput, high-precision micro-hole processing.
The laser’s high energy density and focus allow micron-level engraving on microfine structures. This ensures precise and high-resolution results.
Conclusion
In conclusion, through an in-depth understanding of the application of laser processing technology in engineering machinery manufacturing, we can better understand its advantages and potential, and provide useful reference and guidance for the development of the engineering machinery manufacturing industry.
The application of laser processing technology will bring higher production efficiency, better product quality and broader development prospects for engineering machinery manufacturing.