Clamp thread processing is one of the basic operating skills that pliers need to master, including tapping threads (commonly known as tapping) and sets of threads (commonly known as sets of threads). The use of taps to process internal threads known as tapping threads; the use of plate teeth set of external threads that is for the set of threads.
Although the technology is not complex, in practice, issues such as incorrect threads, damaged teeth, messy buckles, or even tap breakage often arise due to improper or unstandardized operation. Therefore, the following thread processing technology has been analyzed and discussed to address these issues.
Tapping thread operation technology analysis
1. Threading tools
Tap is a tool for tapping threads, the types of organic taps, hand taps and pipe thread taps and so on.
Processing ordinary triangle thread with machine tap and hand tap. A set of machine taps has one tap, and a set of hand taps has 2-3 taps.
Usually, there are two taps in each set of M6-24, and three taps in each set of M6 or M24 or above.
Small taps have low strength and are prone to breaking. Therefore, it is recommended to use a set of three taps, with the large, medium, and small diameters all being the same. This ensures a taper distribution of the cutting load. If the head of the cone becomes chipped or broken, the two or three cones can be regraded and used as the head cone for continued use.
Large tap tapping is labor-intensive, so the cutting process should be divided into several stages. The head taper and the two larger and smaller tapers have smaller diameters compared to the three tapers (which distribute the cutting load in a columnar manner). This ensures a reasonable distribution of the load, making the operation more labor-saving.
A reamer is a tool used for clamping taps and is divided into two types: ordinary type and D type. Each type comes in two forms: fixed type and adjustable type.
For taps below M5, a fixed ordinary reamer should be used. The handle length corresponds to the thread specification, ensuring reasonable operating force and reducing the risk of tap breakage.
For taps above M5, an adjustable reamer should be used, with the handle length chosen based on the tap size.
When tapping near workpiece steps or inside a box, use a D-type reamer to prevent interference with the workpiece during operation.
2. Determination of the bottom hole of the thread
During the cutting and extrusion tapping process, the greater the plasticity of the material, the more likely it is to be pushed toward the tip of the threaded part.
If the diameter of the threaded hole is the same as the minor diameter of the thread, there will be no gap between the thread crest and the root of the tap teeth. This can cause the tap to be squeezed by the metal, leading to jamming or even breakage.
Therefore, the material’s extrusion deformation should be considered when tapping. The diameter of the drilled bottom hole should be slightly increased to ensure the threaded hole maintains the correct size.
This can generally be determined by looking up the relevant manuals or by empirical formulas. For plastic materials, D bottom hole = D – P; and brittle materials, D bottom hole = D – (1.05 ~ 1.1) P. Where D bottom hole for the diameter of the bottom hole, D for the thread diameter, P for the pitch of the thread, the unit is mm.
Blind hole tapping, because the cutting part of the tapping can not be complete thread, so the depth of the hole should be greater than the effective depth of the thread, according to the H drilling = h effective + 0.7D selection.
Where H drill hole is the depth of the bottom hole, h effective for the effective depth of the thread D for the thread diameter, unit are mm.
3. Operating methods for tapping threads
There are two methods for tapping threads: hand tapping and machine tapping. Hand tapping is more difficult, relying on both hands to control the center line of the tap and the center line of the threaded hole when tapping, which is easy to produce skew and swing, so the clamping of the workpiece before tapping is very important.
Place the side to be tapped in a horizontal or vertical position, so that it is easy to observe and judge whether the tap is perpendicular to the plane of the workpiece.
In order to make the tap easy to locate and cut into the bottom hole, the hole should be chamfered and the depth of the chamfer should be greater than the pitch of the thread.
3.1 Initial Tapping and Alignment
When starting the tapping process, place the tap and use one hand to press the top of the reaming bar, applying pressure along the tap’s axial direction. Use the other hand to gently turn the reaming bar.
After the tap enters 1 to 2 turns, check if the tap is perpendicular to the workpiece plane by observing in two directions. If needed, use a 90° angle ruler for correction.
Once the tap has entered 3 to 4 turns, the direction should be mostly aligned. If the direction is incorrect, reverse the tap, use two cones for correction, and then continue tapping with the head cone.
When the tap reaches the bottom of the hole, do not apply additional axial force. Instead, use both hands to rotate the reamer smoothly.
3.2 Key Considerations for Starting Tapping
Start tapping stage is the key point and difficult, for larger thread diameter can choose glossy nut or special sample plate for correction (as shown in Figure 1 (a), (b));
For small workpiece inconvenience clamping, it is not easy to correct the taper perpendicularity, this time can be used to assist the tapping fixture tapping (shown in Figure 1 (c)) [2].
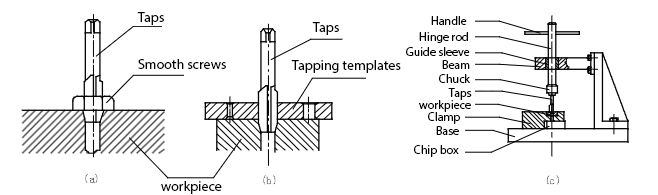
3.3 Swarf Removal and Tapping Speed Control
During the tapping process, each time the reamer rotates 12-15 rounds (for M5), the tap should not rotate more than 12 rounds per cycle. It is important to reverse the tap by 1/4 to 1/2 round to cut off and remove the swarf. This helps prevent swarf clogging, which could damage or break the taps.
When tapping deep hole threads, the reversal stroke should be larger, and should be repeated several times.
The reamer rotation speed should be adjusted according to the material being tapped. For brittle materials, such as cast iron, the speed can be faster compared to plastic materials, like steel, which require slower speeds to prevent damage.
3.4 Balanced Force and Handling Resistance
The strength of both hands turning the reamer should be balanced, avoid excessive force and shaking. .
If there is significant resistance, avoid applying strong force. Instead, reverse to break the chips and then continue tapping. Alternatively, switch to the second cone tap for a few rounds to reduce the load before returning to the main taper tap.
If you hear a “cluck, cluck” sound from the tap and metal friction, stop tapping immediately. Reverse the tap and check for the cause. Continuing to tap without addressing the issue could lead to tap breakage.
3.5 Transitioning Between Taps
After tapping with the first tap, switch to the next tap. The tap should be manually screwed in first before using the reamer. This prevents the back of the tap from misaligning with the front threads, which could lead to improper force application and thread damage.
When the end tap is tapped and the tap is withdrawn, the reamer is first used to rotate smoothly in the reverse direction, and when the tap can be rotated by hand, the reamer is stopped to prevent the reamer from driving the tap out of the tap, which will produce swinging, vibration and damage the surface roughness of the threads that have already been processed.
3.6 Special Considerations for Blind and Through-Hole Tapping
When tapping blind hole threads, mark the depth on the tap and exit the tap frequently to remove chips from the hole to prevent chips from clogging the effective thread depth. The chips should be removed thoroughly after tapping.
When tapping through-hole threads, the calibrated part should not exit the head completely to avoid damaging the last few threads.
To facilitate chip removal, use a special left-hand fluted tap for through-hole threads, as chips are discharged downward. For blind-hole threads, a right-hand fluted tap should be used, as chips are discharged upward.
3.7 Cutting Fluid Selection for Improved Tapping Performance
To improve cutting performance and thread accuracy, select the appropriate cutting fluid based on the material’s properties. This helps reduce cutting resistance, minimize surface roughness of the screw hole, and extend the life of the tap.
Generally, the composite cutting fluid containing both oily agent and extreme pressure agent should be used.
Set of thread operation technology analysis
1. Tools for Threading
The tool for setting threads on plate teeth is known as a thread-setting tool. Types include round plate teeth, square plate teeth, and live tube plate teeth. The cutting parts on both sides of the plate teeth wear down over time, allowing for the use of the opposite side once one side is worn. Plate tooth outer circle has 4 cone pit and a deep groove.
The center line of 2 cone pits through the center of the plate teeth, used to locate and fix the plate teeth; the other 2 cone pits center line does not pass through the center of the plate teeth, when the plate teeth are worn, sawing through the deep groove can be used to tighten the plate teeth of the 2 cone pits, so that the diameter of the threads become smaller, so that the plate teeth can continue to be used.
A plate rack is a tool used for clamping plate teeth. There are three types: round plate teeth racks, adjustable plate teeth racks, and pipe plate teeth racks.
2. Determination of the diameter of the round bar before threading
Similar to tapping threads, when setting plate threads, there is some extrusion. Therefore, the diameter of the round bar should be smaller than the thread diameter. The size can be determined manually or using an empirical formula.
The formula is d rod = d-0.13P, where d rod is the diameter of the rod, d is the diameter of the thread, P is the pitch, the unit is mm.
3. Threading operation method
3.1 Chamfering and Cleaning Before Threading
In order to facilitate the plate teeth cut into the workpiece, the end of the round rod should be chamfered before the set of threads, and the diameter of the chamfer should be smaller than the small diameter of the thread. Clean up the chip groove of the plate teeth and the cutting eyebrow inside the thread.
3.2 Proper Clamping for Stability
Cutting torque is large when setting thread, round rod workpiece should use hardwood V-shaped clamping block or thick copper plate liner clamping fixed in order to firmly clamp.
3.3 Initial Threading and Alignment Check
The method for starting the set is similar to tapping. One hand should hold the center of the plate tooth frame and apply axial pressure, while the other hand lightly turns the tool. At the same time, ensure that the plate tooth’s end face is perpendicular to the axis of the round rod.
After the plate teeth are turned 2 to 3 times, check if they are coaxial with the round rod. If misalignment is found, correct it immediately. Otherwise, the threads may be uneven—deep on one side, shallow on the other—or even result in damaged threads..
3.4 Natural Introduction and Chip Breaking
Divide the cut into four sections and avoid applying axial force. Allow the plate teeth to engage naturally to prevent damage to the teeth and existing threads. Frequently reverse the tool to break chips during processing.
3.5 Use of Cutting Fluid
Sleeving should be added when the cutting fluid, generally can be added to the thick emulsion or oil.
3.6 Improving Thread Accuracy with Guide Sleeves
When the need to improve the accuracy of the thread, the plate tooth frame can be added guide sleeve!
Conclusion
Clamping work is done manually, using various tools to complete part processing, assembly, and repairs. Skill level depends on standardized and rational operations, which require a solid understanding of basic theory.