Surging demand for energy efficiency and sustainability is fueling over 20% annual growth in global magnesium alloy interest.
Magnesium and magnesium alloy characteristics, process characteristics
Magnesium alloys melt at 650 ℃, weigh 1.74–1.85 g/cm³, and offer high specific strength and stiffness.
Also offers excellent damping, electromagnetic shielding, machining, polishing, and surface treatment.
Magnesium alloy is called the metal of the 21st century.
Manufacturers leverage magnesium alloys’ low density to create lightweight, efficient products.
Magnesium alloys match the specific modulus of strong metals, ideal for rigid parts.
Magnesium alloy exhibits good welding performance and fatigue resistance.
Low elastic modulus ensures uniform stress distribution, preventing excessive concentration.
It provides high vibration damping capacity, high vibration damping, and low inertia.
Their plasticity allows forming into bars, tubes, forgings, and castings.
Excellent machinability supports high cutting speeds and precise casting.
Stability in alkaline environments provides strong resistance to salt spray corrosion.
Weak reactivity with iron reduces die wear, prolongs die life, and accelerates casting.
High adaptability enables use in almost all special casting processes.
Its high reactivity leads to oxidation, so flux or protective gas is needed during melting.
Processing and powder workshops must prioritize fire prevention.
The development history and current situation of magnesium industry
In 1808 Humphrcy was the first to distill mercury and magnesium from amalgam.
Buhscn carried out the first electrolysis of magnesium in gasified magnesium in 1852.
Magnesium electrolysis began near Bremen in 1886, growing from 10 tons in 1910 to over 1,200 by 1930.
The magnesium industry developed rapidly during the Second World War.
From 1935, Germany, France, the Soviet Union, Austria, and Italy built new magnesium plants.
During WWII, US magnesium output grew tenfold; global production hit 235 kt in 1943.
Military and aviation used magnesium mainly in bombs, flares, and vehicles.
After WWII, global magnesium output fell to 25 kt in 1946; the US made 4,834 t.
To boost the industry, countries began exploring magnesium alloys for civilian applications.
Over 20 years, Dow Chemical advanced magnesium alloy production and expanded its use.
Since WWII, global magnesium grew 7% yearly, surpassing the 1943 peak by the mid-1970s.
Global raw magnesium capacity exceeds 550 kt annually; 2000 production was about 430 kt.
Manufacturers cast about 70% of magnesium alloys into vehicle and electronics parts.
Metallurgy uses over 15% of magnesium as raw material.
Manufacturers process 10% of magnesium alloys for aerospace and defense.
Companies use magnesium powder to make fireworks and paint.
The development level and trend of magnesium alloy processing technology
New magnesium alloy and its special performance research and development
Over 100 magnesium alloys exist, including common deformed types MB2, MB3, MB8, and MB15.
Magnesium casting and die-casting developed a more complete, diverse alloy system.
This discusses a few newly developed magnesium alloys with special properties.
- The development of high corrosion resistance magnesium alloy
Corrosion seriously affects magnesium alloy application, a major problem.
Reducing Fe, Cu, and Ni impurities improves magnesium alloy corrosion resistance.
High-purity magnesium ingots from new electrolysis are used for AZ91HPAZ91D and AZ91E alloys.
The second step uses S gas melting to prevent impurities and boost corrosion resistance.
High-purity AZ91D resists salt spray 100× better than AZ91C, beating mild steel and A380 aluminum.
Ford Ranger clutch housing made of AZ91D remained intact after 10 years in salt spray.
- Poor performance at high temperatures
Magnesium alloys’ limited high-temp use has improved, with resistance rising from 150 ℃ to 300 ℃.
US Mg-Th alloys resist up to 350 ℃; Russian Mg-Nd and Mg-Y alloys also exceed 150 ℃.
High-temp magnesium alloys replace aluminum and titanium in aircraft engines.
AS-series alloys boost strength by reducing Al, adding Si for MgSi, and cutting Mg17Al12.
Adding element I improves high-temperature performance of A-series magnesium alloys.
AE42 (Mg-4%Al-2%IE-0.3%Mn) nearly doubles AS21 alloy’s fatigue strength.
Adding 1% Ca to AZ91 or AS alloys improves creep strength but worsens casting, unlike Mg-N-Cu alloys.
Adding Cu greatly improves performance at room temperature and 150 ℃.
- Development of ultra-light Mg-Li alloy
Mg-Li alloys are ultra-light (1.35–1.65 g/cm³) with high strength and toughness, ideal for aerospace and defense.
Currently, the US, Japan, and Russia actively research Mg-Li alloys, covering theory to applications.
The development of magnesium alloy melting technology
Magnesium casting requires coverage to prevent oxidation and inclusions that weaken properties.
Most factories use SF6 and Ar3 or CO3 for protection;
SF6 raises warming concerns, while SO2 is a polluting alternative.
Strict control in melting prevents oxide-induced brittleness in magnesium alloys.
Optimize AE, AZ, AM alloys by controlling eutectic growth to improve strength.
Higher co-crystal content boosts engine and suspension toughness, strength, and heat resistance.
Melting AE, AZ, and AM alloys demands strict control for strong properties.
- Alloy components
Crude metal production requires burn rate control or strict alloy composition limits.
If added metals have low solubility, amounts approach the standard upper limit.
Calculate metal balance to ensure alloy quality and minimize impurities.
- Melting temperature
Melting AE, AZ, or AM alloys at 760–780 ℃ demands temperature control and impurity removal.
Stable melting temperature is vital;
excess secondary phase during cooling lowers toughness, strength, and machinability.
Alloy melting is completed, the static temperature of 740 ~ 770 ℃, static time for 30 ~ 90) min.
Magnesium alloy casting and die casting technology development new direction
Casting accounts for 70% of magnesium alloy use, driven by advances in die-casting technology.
In the 1980s, major countries improved casting quality with siphon transfer and SF6.
Magnesium alloy die casting commonly uses cold- and hot-chamber machines.
PBINCE built 13.72 MN magnesium die-casters with melting and robotics in 1986 and 1990.
Cold-chamber die-casters make large auto parts like Audi dashboards and GM seat frames.
Hot-chamber die-casters (<7,840 kN) are twice as efficient and ideal for thin castings under 2 kg.
Kirk’s bike frames and White Metal’s shells are made by hot-chamber die-casters.
By 1992, the US and Japan had 160+ magnesium die-casters for auto parts and electronics.
Semi-solid shot casting rapidly grows as automated magnesium casting method.
Magnesium alloy die-casting technology development trend
In 20 years, vacuum, oxygenated, and semi-solid die casting emerged and spread.
Traditional die casting excels in defect elimination and quality improvement.
- Vacuum die-casting method
Vacuum die casting removes gas, reducing porosity and improving strength and surface quality.
This method doubled AM60B hub and steering elongation from 8% to 16%.
- Oxygenated die-casting method
Oxygenated die casting uses active gas to reduce defects and allow heat treatment.
Used by Japan Light Metal for magnesium alloy parts like computer brackets and wheel hubs.
- Semi-solid rheological die-casting technology
Semi-solid rheo-die casting provides smooth filling and fewer defects.
This method reduces shrinkage, mold resistance, and improves accuracy.
In 1987, Dow Chemical pioneered magnesium semi-solid die casting, securing three patents.
Commercialized in the US, Canada, and Japan, the technology saw second-gen equipment in 1991.
Magnesium semi-solid die-casting parts include transmission covers and ignition shells.
SiC-reinforced magnesium composites promise die casting but lack commercialization.
- Magnesium alloy metal compression molding technology (MCF)
Ohio Precision Molding developed full-surface pressure die casting for magnesium molding.
Pressure solidification refines structure, reduces porosity, and yields dense, strong castings.
The development trend of magnesium alloy processing technology
Equipment is constantly updated, automation improves;
semi-solid casting leads, die casting lags in developing countries.
Die-casting automation includes melt supply, mold coating, part removal, and logistics.
New mold development covers rapid prototyping, CAD/CAM, high-speed cutting, EDM, standards, and CAE.
Die-casting tech advances from alloys to finished parts, covering the full process.
Key areas: melting, purification, vacuum casting, mold release, sizing, finishing, safety.
Figure 1 for magnesium alloy castings or die casting common process flow.
Figure 1: Magnesium alloy casting and die casting process flow
Magnesium advances as a lightweight material for vehicles and aerospace.
Figure 2 shows the deformed magnesium alloy processing flow.
Key issues in magnesium alloy processing technology are.
Design a reasonable processing flow and supporting production tools.
Formulate magnesium alloy ingots, slabs, semi-finished products, and hot rolling, extrusion, forging specs.
Formulate specs and heat treatment for magnesium alloy fine rolling and cold forming.
Magnesium alloy surface treatment research mainly focuses on chemical conversion technology.
Anodic oxidation, electroplating, and non-chromium low-pollution surface treatments.
Expand magnesium use by collaborating to surpass steel, aluminum, and plastics in cost, weight, integration, and durability.
Collaborate with manufacturers to optimize alloys, molds, casting, and produce quality magnesium parts.
Magnesium alloy semi-solid shot casting technology development
Semi-solid shot casting is a high-tech in rapid development and improvement.
This casting method greatly enhances surface quality of alloy parts.
Improving yield rate is the key competitive focus in die casting; higher yield means market success.
Semi-solid injection casting will become the mainstream for magnesium alloy production.
Lower costs and cycle time drive semi-solid shot casting development.
Magnesium recycling is harder than aluminum due to higher chemical activity.
Die casting produces magnesium alloy waste like heads, runners, chips, and scrap.
Chip recovery, storage, transport, and melting require caution to prevent explosions or fires.
US plants recycle 90kt magnesium annually, producing low-cost, quality ingots from waste.
Development and application of magnesium alloy
Magnesium production capacity and main application fields
World magnesium production was 337 kt in 1997 and consumption exceeded 430 kt in 2000.
Large magnesium plants boosted capacity beyond 550 kta.
Table 2 shows global magnesium production capacity and supply-demand from 1995 to 2005.
Industries mainly use magnesium in metallurgy, die casting, pressure processing, and chemicals.
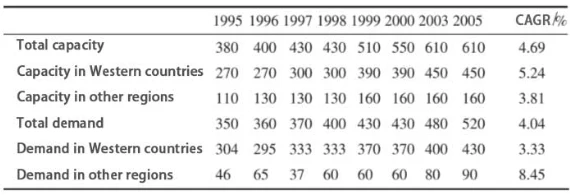
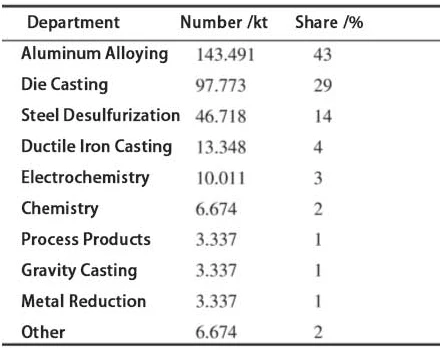
Development and application of magnesium alloy in automobile and motorcycle industry
The current situation of magnesium alloy application in automobile and motorcycle
In 1930, Louris used magnesium alloy pistons in racing cars.
Beetle’s engine and transmission contain 20+ kg magnesium alloy.
Experts at the time viewed magnesium as a niche material.
Magnesium alloys gained auto importance after the 1970 oil crisis.
In 1980, Dwain M. Magers predicted rising magnesium alloy use in autos.
Ford pioneered magnesium alloys in clutch and steering parts.
Ford first used magnesium alloys in pickups, then cars.
European, Japanese, and North American automakers soon used magnesium alloys for heads.
Mercedes-Benz used magnesium seat frames in the SLL sports car.
Audi applied it to the V8 sedan dashboard, and Toyota expanded its use to steering shafts.
Since the 1990s, automotive magnesium use rose from 24 kt to 64 kt, projected at 200 kt/year by 2006.
These regions’ magnesium alloy demand will keep growing, driven by the auto industry.
Magnesium Alloy Applications and Industry Impact
Foreign automakers use magnesium alloys in 60+ parts like wheels, dashboards, engines, seats.
By 2005, magnesium parts like blocks, covers, roofs, doors, and hubs were set for mass production.
Volvo CP2000 (700 kg) uses 50 kg magnesium in hubs, transmission, steering, suspension, and engine.
In 1980, Volkswagen’s Beetle set a record for magnesium alloy use in cars.
Ford, GM, and Chrysler use magnesium castings in 30, 45, and 20 models.
Italy’s second-gen magnesium wheels weigh 5.4 kg, 28% lighter than 7.4 kg aluminum wheels.
By 2020, 100 kg per car may push magnesium demand to 6 Mt, sparking a revolution.
The auto industry drives magnesium alloy applications and demand.
Magnesium alloy parts widely cut car weight.
Table 4 shows Toyota sedan’s weight savings from cast and die-cast magnesium parts.
Tables 5 and 6 show magnesium alloy parts in European Fiat Dinc and Boscher 911 cars (1970 data).

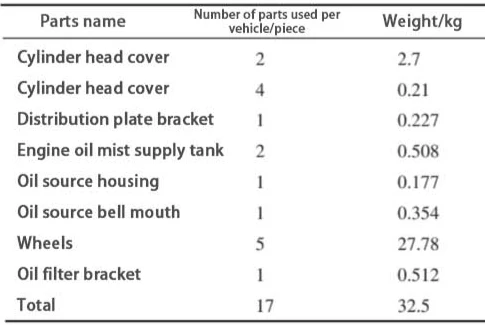
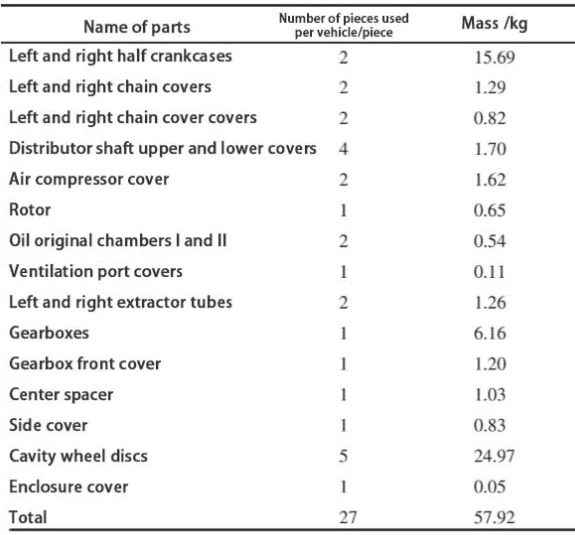
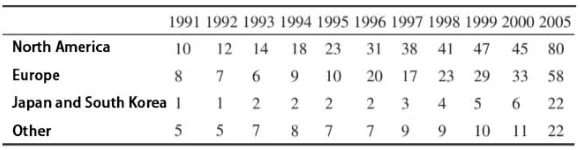
Prospect of magnesium alloy application in automobile industry
Prospects for Magnesium Alloy in the Automobile Industry
Recent auto magnesium alloy uses include large die-cast parts like door frames.
Goals: cut weight, optimize castings, reduce costs, boost assembly, enable automation.
European automakers want to produce cars with fuel economy of 3L/100 km (79 milc/gal).
This provides new opportunities for the development of magnesium alloys.
Magnesium alloys with good plasticity, toughness and formability were required.
Mercedes-Benz needed 15% elongation magnesium alloy, but AM20 and AM50 failed molding.
In 1996, GM and Norsk Hydro Canada signed a deal to supply magnesium parts from 1997.
Volkswagen and suppliers signed a long-term deal for magnesium die-cast parts.
Automakers’ deals affirm magnesium alloy’s promising future.
At present, the car using magnesium alloy parts are.
Internal parts: seats, pedals, steering, airbags, audio frame, mirrors, engine, and wiring.
Also used in headlight cages, ABS brackets, wheels, fuel doors, and transmission housings.
Future magnesium alloys will extend to large parts like roofs and dashboards.
Magnesium alloys will expand to seats, steering, body, and engine supports.
Magnesium alloy in electronics, aviation, aerospace, weapons and other industrial sector development and application
The electronics industry is rapidly expanding for magnesium alloy parts.
In Japan, magnesium alloys increasingly replace plastic in electronics like laptops, TVs, and phones.
US White Metal Casting made a 610×610 mm magnesium alloy computer shell by die-casting.
1997 Panasonic magnesium shells showed promise for autos, electronics.
Lower magnesium prices and new alloys boost aerospace and defense use.
Engineers use MB5/8/15 forgings and Ф20–95 mm bars in aircraft maneuver systems.
MB8 and MB15 (7–18 mm plates) are used in rods, doors, and missile structures.
Alloys serve electronics, textiles, packaging, arms, and luggage.
Conclusion
Magnesium alloys are the lightest structural metals and among the most promising of the 21st century.
Global magnesium alloy investment fuels rapid growth in autos, aerospace, electronics, and new materials.