As the processing volume of steel structures continues to increase, the cutting of steel components is an essential technology for steel structure processing.
CNC laser cutting machine based on CNC machine tools and laser technology to make up for the shortcomings of the traditional cutting technology, with cutting precision, accuracy, and stability of the same magnitude.
In order to further optimize the effectiveness of construction steel cutting, and promote the organic integration of CNC technology and laser cutting, it is necessary to analyze the processing principle and structural composition further.
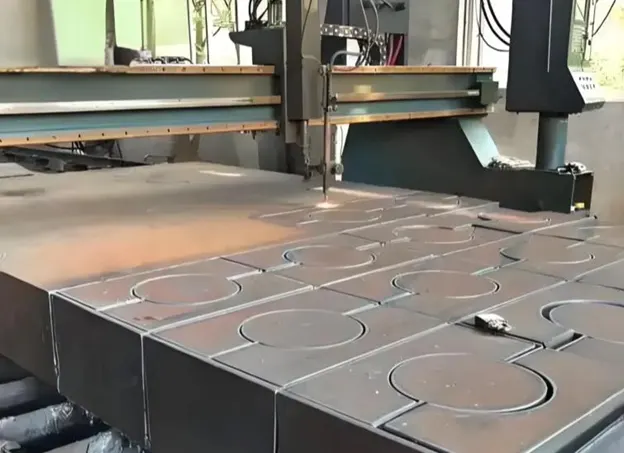
CNC laser cutting machine basic overview
Technical characteristics
CNC laser cutting machine effectively integrates digital control and laser technology, which is a high precision, high speed, and high safety technology.
CNC laser cutting support for high-precision repeated cutting, and its precision does not change in the repeated cutting.
At the same time, when cutting rigid metal materials, the cutting speed and capacity of the CNC laser cutting machine far exceeds that of conventional grinding machines.
In addition, compared to grinding wheel and saw-tooth cutting technology, the risk factor of CNC laser cutting technology is relatively low, and safety is ideal.
Uses and advantages
The CNC laser cutting machine, in addition to cutting various metal materials, special materials, and mechanical parts with application functions, can also be used for punching and other precision machining processes.
At present, CNC laser cutting has been popularized in the food machinery, elevator manufacturing, tool processing, agricultural and forestry machinery, laser external processing services and other machinery manufacturing and processing industries, playing an irreplaceable role.
CNC laser cutting in the operation process, cutting efficiency and application range, etc., has the advantages that traditional mechanical cutting can not compare to, and its cutting gap and heat-affected zone area are relatively smaller, the overall cutting performance is superior.
Common classification
Although the functional needs of various industries for CNC laser cutting machines differ, high efficiency, precision, and safety remain the eternal pursuit in the cutting process of the machinery manufacturing industry.
At the present stage, there are three common classifications of CNC laser cutting machine common to all fields: (1) YAG solid laser cutting machine.
(1) YAG solid laser cutting machine
Through high-power beam irradiation to accelerate the melting/vaporization process, and high-speed air pressure flow to realize the blowing operation, and then complete the component cutting work.
This type of cutting machine offers relatively high cost performance and ideal stability, making it popular in the field of mechanical cutting.
(2) fiber laser cutting machine
Its cutting principle is similar to the YAG, that is, with the help of a laser beam to complete the cutting operation, but its beam from the fiber laser has higher beam quality and a compact size, suitable for flexible processing and metal components cutting; in non-metallic components cutting, it is slightly inadequate.
(3) CO2 laser cutting machine
Its laser beam comes from CO2, N2 and He and other major gas molecules of energy transfer and vibration movement, laser kinetic energy conversion efficiency and effect is relatively ideal, especially in high-power cutting operations.
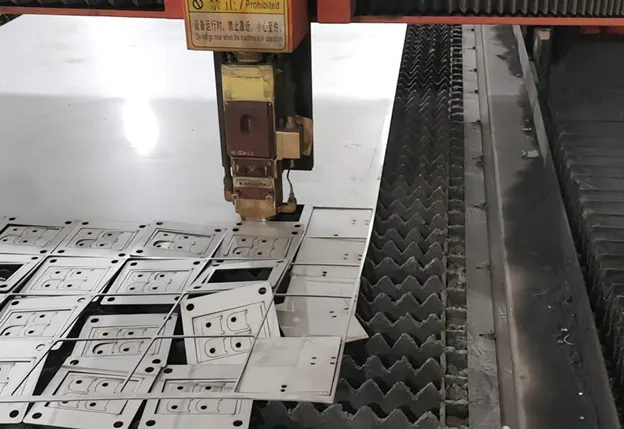
CNC laser cutting machine processing principle
The CNC laser cutting machine uses a high power density laser as its processing energy. The focusing mirror significantly reduces the spot diameter while dramatically increasing the laser beam power density.
This process follows the formula d=2.44λD−fd = \frac{2.44 \lambda}{D} – fd=D2.44λ−f, where ddd represents the focused spot diameter, λ\lambdaλ is the fixed wavelength (10.6 μm), DDD is the laser beam diameter, and fff is the focal length of the lens. This formula applies primarily to single-mode output.
However, the application of laser cutting machine can not be separated from the high-power laser, that is, for the multi-mode output, power density using Po = 4W/πf2θ2 this formula (W represents the output power, f represents the focal length, θ represents the angle of divergence).
With high-power density irradiation, the material temperature is difficult to diffuse in time. At this time, the temperature of the focus point will rise linearly, which will trigger melting and vaporization. This response will be significantly accelerated, and then complete the cutting operation.
The application of numerical control technology can transform the shape of the workpiece into a numerical control device can understand the information, the numerical control device can be based on the input information to give the corresponding pulse command, through the drive motor to manipulate the operation of the table, through the continuous feed to promote the implementation of the laser beam to cut continuously, in the absence of mold conditions at will processing of plane graphics and spatial curved surface parts.
CNC laser cutting machine structure analysis
20000W fiber laser cutting machine
This kind of cutting machine is suitable for the mechanical manufacturing field of two-dimensional plane cutting, cutting objects that involve carbon steel, stainless steel, aluminum alloy, brass, copper, silicon steel plate, titanium alloy, and other materials.
The weight of the machine is about 27t, the processing width is 14000mm×3000mm, the effective cutting length is up to 14000mm long and 3000mm wide, the cutting speed of 20mm thick plate can reach 1000~1200mm/min, and the cutting speed of 20mm thick plate with 45°bevel can reach 600~800mm/min.
Detailed structural composition is as follows.
》Machine base
The machine base is the fundamental part of the cutting machine, and it is also the most critical structural component, ensuring the stable and efficient operation of the cutting machine.
In high-speed operation, cutting machines often experience high kinetic acceleration. At the same time, the power parts generate a certain impact that affects the stable operation of the machine base and the quality of the laser beam, significantly reducing the cutting effect.
Therefore, during the machine base design stage, we should focus on optimizing and improving dynamic stability.
In the welding bed and beam, actively implement annealing treatment, second vibration aging treatment, and other processes to eliminate stress generated from welding, processing, and other aspects. This will help realize the stability of the machine tool, enhancing overall precision and effectiveness.
In order to enhance the performance of the machine tool in terms of rigidity, convenience, and precision, etc., it can increase the special datum, and the configuration of the excellent performance of the precision reducer, rack and pinion, and linear guide and other transmission institutions, to provide protection for the transmission accuracy.
In designing the machine base and cutting platform, designers should fully consider application convenience.
They should comprehensively apply splicing assembly, modular assembly, dust extraction structures, and other methods to improve the user’s experience.
》Z-axis following mechanism and air circuit design
During the operation of the cutting machine, capacitive sensors support the Z-axis follower as it accurately detects the flatness of the machined surface of the cutting element. The servo drive from an internationally renowned brand then manipulates the cutting head to ensure the laser energy focuses on the surface of the cutting element.
The precision of the focusing point directly affects the kerf gap and cutting quality, so we must strictly control the detection accuracy of the follower device, ensuring it is no less than 0.010mm in principle.
In addition, operators should control the drive speed because it also impacts the cutting effect; generally, they prefer to set it at 5m/min.
If operators run the cutting head at too high a speed, it will vibrate and affect cutting accuracy, while running it at too low a speed will reduce cutting speed and exacerbate resource waste.
The cutting machine divides the gas circuit into O2, N2, and air, allowing operators to freely switch between each gas.
To improve the accuracy and stability of gas pressure control, it is essential to carefully select gas components, such as a pressure-regulating valve with a pressure rating of ≤ 1.2MP and a solenoid valve with a pressure rating of ≤ 3MP.
》Numerical control device
The CNC system primarily follows the prescribed instruction code and relevant program format, which include process parameters, routes, the diameter of the optical plate, the trajectory, cutting parameters, and auxiliary functions. It transfers the entire machining program list to the computer, which then manipulates the machine tool to carry out parts processing operations.
FACUT for full-featured CNC laser cutting control system, but also more commonly used in the field of machinery manufacturing beveling CNC system, automated model calibration, normal vector to follow the plane perpendicularity compensation, two-dimensional map import, interpolation to follow the control of the three-dimensional error judgment, as well as the corner processing and so on, the system’s core functions.
The assembly and reasonable application of FACUT can automatically calibrate and compensate for the horizontal offset, tilting error in the model and the positioning deviation that occurs when following vertically at a large angle, and add the verticality compensation of the plate surface based on the compensation of the cut seam, and project the overall tilting information of the machining area by using the collected data point information, to realize the high-precision machining.
At the same time, FACUT’s interpolation following control function also improves the overall stability of the oscillating mechanism, which not only eliminates the problem of jittering at the end of the cutting head, but also avoids the risk of head collision under pure interpolation control, thus enhancing safety protection.
In addition, FACUT can also make a scientific judgment on the state of coordination and hysteresis of each axis to assist debugging.
Corner processing function by adjusting the normal vector and tangent line speed and direction in the plane where the section is located in advance, it can realize the effect of continuous cutting.
12000W Fiber Laser Tube Cutting Machine
This type of cutting machine is suitable for space cutting in the field of mechanical manufacturing processing, such as square pipes, round pipes, channel steel profiles, and other similar objects. The cutting objects include carbon steel, galvanized pipes, stainless steel, silicon steel pipes, and more.
The weight of the whole machine is about 38t, the processing range of round pipe is 60~500mm in diameter and 12200mm in length, the size of square pipe is 60×60~350×350mm and 12200mm in length, and the cutting speed of 16mm wall thickness with 35°bevel can be up to 600~800mm/min.
Detailed structural components are as follows.
》Machine base
The whole machine bed can be divided into 3 sections, for the square tube welding structure, beam part of the wall plate welding structure, are processed by annealing to eliminate internal stress, the second aging and other processes, the stability is considerable.
》Running mechanism
12000W Fiber Laser Pipe Cutter uses Z-axis, Y-axis, and W-axis follower mechanisms, which further optimizes the cutting quality and processing accuracy while realizing the up and down movement of the cutting head.
Drive mechanism
The 12000W Fiber Laser Tube Cutter applies its transmission mechanism mainly in three key areas
(1) Clamping
The system uses a pneumatic chuck that automatically calibrates the axis after clamping. Designers design the jaws to adjust and accommodate various pipe shapes, ensuring efficient clamping of different types of pipes.
(2)Loading
A V-shaped bracket serves as the material frame, supporting the placement of pipe materials. Using a chain-driven feeding system controlled by servo motors, the setup automatically adjusts its height based on the pipe’s size. his system accurately transports all types of pipes to the center of the chuck, providing optimal conditions for automatic chuck clamping and enhancing the precision of pipe processing.
Configuration of imported servo motors with screws to realize the comprehensive improvement of loading efficiency and accuracy.
(3)Unloading
Here, workers receive the material in different zones, set up the waste bin, and install the rollers.
When cutting long materials, four chucks will operate simultaneously to ensure stability during cutting. The chain will automatically transfer the materials out after entering the receiving frame.
Air and water systems
The gas circuit consists of two parts.
(1) for the cutting gas, mainly involving compressed air, high-purity nitrogen and high-purity oxygen;
(2) for the movement of auxiliary gases, mainly compressed air, which can directly drive the cylinder, with the help of a dust removal fan, with a powerful dust removal function to eliminate soot.
The water circuit can also be divided into two parts. One part of the cooling water from the chiller flows through a section of the laser refrigeration cycle and is then discharged and returned to the chiller. The other part is directed to the laser cutting head.
Cutting head part
In principle, the cutting head should support high-efficiency focal length lens replacement (such as 5′, 7.5′ focal length lens). It ensures that operators can replace the lens without making any adjustments to the optical path system.
In addition, designers should install an anti-collision security system as a reasonable device in the cutting head part. This system ensures that the cutting head can return to its original position shortly after being impacted by external forces, thereby maintaining machining accuracy.
To accurately control the cutting angle, the cutting head swing part still utilizes imported servo motors. The cutting head is the most advanced, featuring an internal structure with an absolute seal on the laser head, thereby reducing the possibility of contamination to the optical lens.
In the servo motor’s auto focus, the laser head part implements a two-point centering adjustment to optimize piercing efficiency and quality.
CNC control
The most professional TubePro laser processing CNC system is adopted. Its compact structure, modular assembly and high cost performance satisfy the user’s performance requirements of the CNC system. Its advantages are reflected in five aspects:
(1) Architecture.
Unlike the previous dual-CPU design, TubePro runs all the system software on the main PC processor, which is a reasonable and advanced system design framework.
(2) Technology.
CNC technology enables developers to make the system’s functions accessible to the public through modularization, eliminating the need for hardware changes.
(3) Performance.
The increasing improvement of 5-axis linkage and coordinate transformation can realize the good control of multi-axis and multi-channel, which can provide guarantee for the good operation of CNC equipment, and can automatically correct the processing of defective pipes with mild distortion and deformation.
(4) Function.
The system can meet the diversified functional requirements of users, and the implementation of functional optimization in the field of application can achieve maximum cost-effectiveness.
(5) Interface.
The real-time kernel of this system addresses the real-time control issues of the Windows system, while guaranteeing real-time performance, it also highlights the characteristics of convenient operation and a friendly interface.
Conclusion
In summary, the CNC laser cutting machine is starting to play a crucial role in cutting and processing architectural steel structures, and it will undoubtedly become an indispensable piece of machinery in the field of architectural steel structure production and manufacturing in the future.
To further improve CNC laser cutting technology, researchers must continue exploring its processing principles and structural composition and thoroughly investigate its potential value, thereby enhancing the level of CNC laser cutting technology in the field of construction steel materialization.