In recent years, the market economy has developed, increasing the demand for higher precision in high-precision parts processing. The CNC lathe, as an important processing tool, is widely used to manufacture high-precision parts.
However, traditional CNC lathes struggle to meet high-precision requirements as processing technology improves. Controlling factors that affect machining quality has become the key to improving machining results.
Currently, the quality of CNC lathe machining still needs improvement, especially for parts with irregular shapes that require high precision. Adjusting CNC lathe processing parameters and processes can effectively enhance processing quality.
This paper analyzes the factors affecting high-precision parts processing and suggests control measures to improve CNC lathe machining quality.
Composition and Principle
1.The Composition of CNC Lathe
The CNC lathe plays a crucial role in the production and processing of high-precision parts. Its main components include the following:
(1) Host
The host is the core of the CNC machine tool. It consists of the column, bed, and cutting parts. It is responsible for bearing the force and ensuring the stability needed during processing.
(2) Drive
The drive powers the CNC lathe. It includes the spindle drive, spindle motor, and feed motor. It uses electronic or electro-hydraulic servo systems to control the spindle and feed movements accurately.
(3) Numerical Control Device
The numerical control device includes both hardware and software for the CNC lathe. It inputs and stores the parts processing program and processes large amounts of data. It ensures the lathe performs all processing tasks accurately.
(4) Auxiliary Device
The auxiliary devices support the stable operation of the CNC lathe. These include the cooling, lighting, lubrication, and chip removal systems. They ensure the equipment operates smoothly and efficiently during the machining process.
With these components, the CNC lathe can efficiently and accurately complete complex machining tasks.
2.The Operating Principle of CNC Lathe
CNC lathes process parts based on the process model’s characteristics. Fig. 1 shows their operating principle.
CNC machine tools have multifunctional workstations and processing areas. They handle large workloads, offer wide processing surfaces, and support compensatory and compound processing for high-speed, high-precision cutting.
CNC lathes combine computers and machinery, with measurement, control, power supply, and sensing devices.
They achieve precise machining through automatic control. Operators input the machining process to ensure the machine follows system instructions, achieving high-precision machining.
Thus, CNC lathes are essential for precision machining.
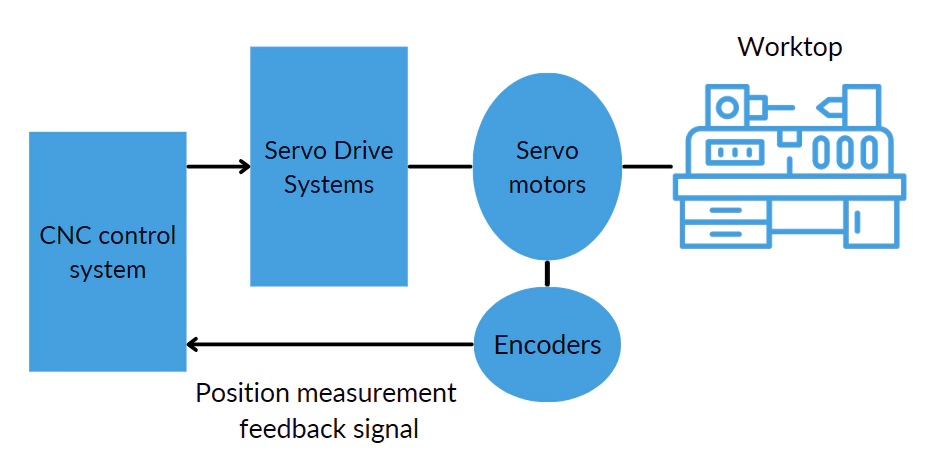
Fig. 1: CNC Lathe Operation Principle
Importance of Quality Control
Before CNC lathes, traditional lathes relied on manual operation. Operators had to control equipment errors, such as human eye adjustments and chuck misalignment, to improve machining quality.
This method had low efficiency and poor accuracy, limiting mass production and failing to meet growing social and economic needs.
CNC lathes have become key tools in addressing these challenges.
With advancements in technology, demand for high-precision parts has grown. CNC machines now replace traditional lathes for manufacturing parts.
By inputting NC code, CNC lathes cut along specified paths, boosting productivity and machining accuracy.
1.Advantages of CNC Lathes
Modern CNC machine tools improve both production quality and manufacturing level. In the global economy, the market competitiveness of machine tools increases.
A country’s machine tool manufacturing level reflects its production strength and enhances machinery competitiveness.
2.International Competition and Development Trend
Many Western countries have made CNC machining equipment and technology a key development strategy. They focus on strengthening technology.
By learning from advanced technology and experience, these countries have improved their manufacturing and driven global progress.
Influencing Factors
Studies show a large error between CNC machining accuracy and production requirements. In high-precision workpiece manufacturing, factors like programming, equipment, and programs affect machining quality.
We usually evaluate this by comparing machine tool manufacturing error to process error. Higher accuracy in casting parts typically leads to increased CNC machine tool error.
To improve casting process accuracy, we must control factors affecting machine tool precision strictly.
Thus, combining processing realities with machine tool accuracy management and targeted optimization can improve CNC lathe machining accuracy. (Table 1)
Table 1 CNC Lathe Machining Error
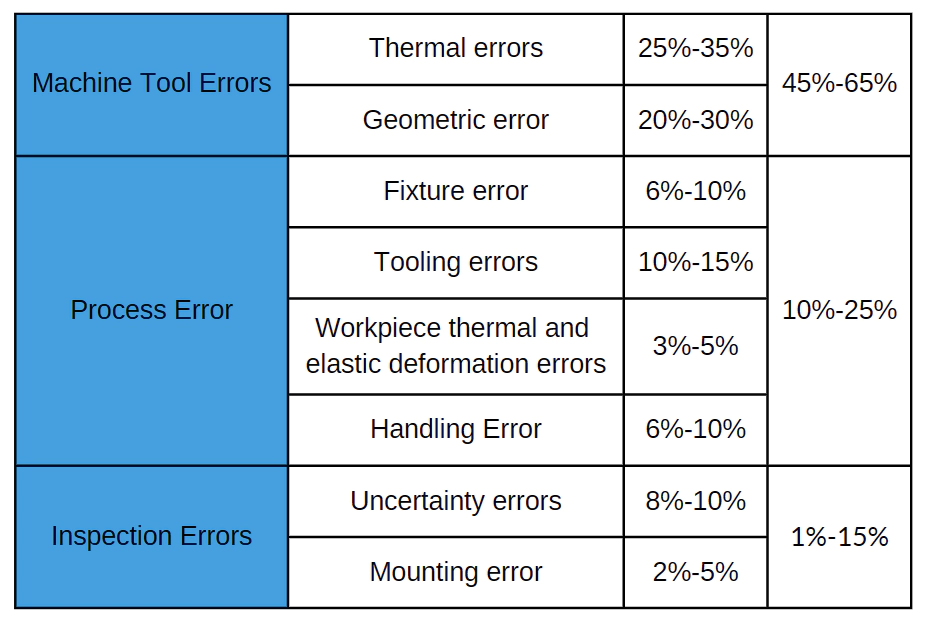
1.Servo System Driving Factors
The servo control system’s actuator significantly impacts high-precision workpiece manufacturing. The servo drive ensures machining by driving the fixture device.
The CNC lathe ensures precise manufacturing by monitoring the ball screw, servo, and motor.
However, errors in the ball screw drive can affect machining accuracy. During operation, the screw’s reversal mechanism is prone to idling, causing backlash deviations.
CNC machine tools also twist under external forces, creating elastic gaps and restricting machining accuracy.
Optimizing the servo control system’s precision can improve machine tool performance.
2.Turning Tool Control Factors
In CNC machine tool mold making, selecting the right tool is essential to meet the mold’s shape requirements.
The cutting tool’s control surface and spindle size can cause errors, leading to cutting deformation. Thus, optimizing the cutting process is crucial.
Selecting optimal cutting parameters during CC machine programming improves machining accuracy and reduces cutting errors.
However, controlling the tool’s motion path accurately remains challenging, causing potential cutting errors.
Quality Control Strategy
1.Control Servo System Drive Error
The servo drive control is crucial in CNC machine tool design. Close control ensures optimal performance.
To control the manufacturing deviation of the servo drive, optimize the operating characteristics of the transmission equipment.
Efficient regulation of the drive system ensures proper management of the machine tool travel process.
Further optimizing the loads and air pressures of the servo drive system improves control accuracy.
After installing the servo unit, optimizing the machine’s machining state ensures each step operates optimally.
The optimization of each link ensures an efficient and accurate machining process.
2.Machine Tool Cutting Parameters Control
(1) Tool Selection
Before CNC machine tool cutting, consider the material of the tool. The tool should have good toughness, hardness, wear resistance, and high-pressure and high-temperature resistance.
Carbide and high-speed steel are the most common tools. Carbide performs better at high temperatures (up to 1000°C) and offers excellent hardness and wear resistance.
(2) Tool Parameter Selection
Select tool parameters such as tip offset, tip radius, and main inclination to control the workpiece in both radial and axial directions.
Consider the workpiece material, processing requirements, and models to determine the optimal machining process.
(3) Workpiece Positioning
Minimize the cutting amount and use CNC machine tools with clamping to improve workpiece clamping efficiency.
This method saves machining cycles and works well for various parts, offering better economic results.
3.Precision Control in Tooling
(1) Precision Importance
In CNC lathes, the geometric accuracy of the turning tool directly affects the processing quality of high-precision parts.
High-precision parts require the tool to maintain precise geometry to guarantee machining accuracy.
CNC lathe designers must focus on maintaining and optimizing the tool’s geometric accuracy during production.
(2) Optimization Measures
To improve turning tool accuracy, designers should optimize the tool’s guidance during manufacturing.
This enhances extrusion performance, overall accuracy, and tool stability and precision during machining.
(3) Design Considerations
Designers often use an inclined structure in tool manufacturing to maximize CNC machine tool functionality.
This improves bearing capacity and bending performance, ensuring high precision and stability during machining.
By optimizing these measures, the geometric accuracy of the turning tool improves, ensuring CNC lathe performance for high-precision parts.
4.Improvement of Error Compensation
When the CNC lathe processes high-precision parts, error compensation technology boosts processing efficiency.
It improves the inadequacy of the current coordinate axes by combining hardware and software to optimize machining.
(1) Effect of Reverse Deviation
Studies show that 0.5-level closed-loop control encounters reverse deviation, reducing workpiece positioning accuracy.
Reverse error compensation solves this problem and improves machining accuracy.
(2) Part Machining Accuracy and Error Compensation
Error compensation technology saves production costs by using existing resources without altering the original design.
It enables CNC lathes to achieve higher precision and efficiency with minimal investment.
(3) Ball Screw Error Compensation
In CNC machine tools, fluctuations in peg feeding accuracy cause errors.
Gap compensation technology improves ball screw accuracy, extends its service life, and enhances machine tool stability.
Combining these methods boosts CNC machining quality and efficiency.
5.Application of Optimal Machining Process
To improve the machining accuracy of a CNC lathe, first optimize the handling. Efficient control directly affects the machining effect of high-precision parts.
Additionally, regulating cutting methods and manufacturing processes is key to improving efficiency and precision. This approach effectively improves the manufacturing quality of the workpiece.
(1) Tight Process Design and Optimization
To ensure machining accuracy, strictly design the production process. Strive for one-time high-precision machining. If that fails, minimize the number of workpiece replacements.
Using separate fine and roughing machine tools improves high-precision zero-point machining quality. This method boosts production efficiency and ensures accuracy at each stage.
(2) Path Optimization
Optimizing the CNC lathe’s process path is crucial. A well-chosen machine tool trajectory shortens the work cycle and improves cutting efficiency.
Eliminating unnecessary steps boosts economic efficiency. After optimization, the machine tool’s efficiency increases, leaving more room for subsequent machining.
(3) Commissioning and Automated Production
Before processing high-precision workpieces, debug and reprogram CNC machine tools.
After debugging, the CNC machine enters automated production until the process completes. The operator enters the program, makes tools, programs, monitors production, and assembles and disassembles parts.
This series of operations makes the process more intelligent and reduces work intensity.
(5) Precise Control and Workload Reduction
During CNC lathe machining, the manipulator must accurately control surface roughness and accuracy values and streamline calculations.
This reduces the machine’s workload and improves machining accuracy, leading to more efficient and economical production.
By implementing these optimization measures, CNC lathe machining accuracy and work efficiency improve, significantly enhancing the quality of manufactured parts.
6.Error prevention strategy
To develop an effective error prevention strategy, continually improving the accuracy of lathe fixture parts is essential during CNC lathe design and production. This reduces overall process accuracy deviations.
However, part manufacturers often struggle to improve machining accuracy with existing CNC lathes.
As a result, retrofitting existing CNC lathes is often necessary. Such modifications bring high costs, creating economic pressure for implementing error prevention strategies.
Table 2 Quality control strategy for high-precision parts
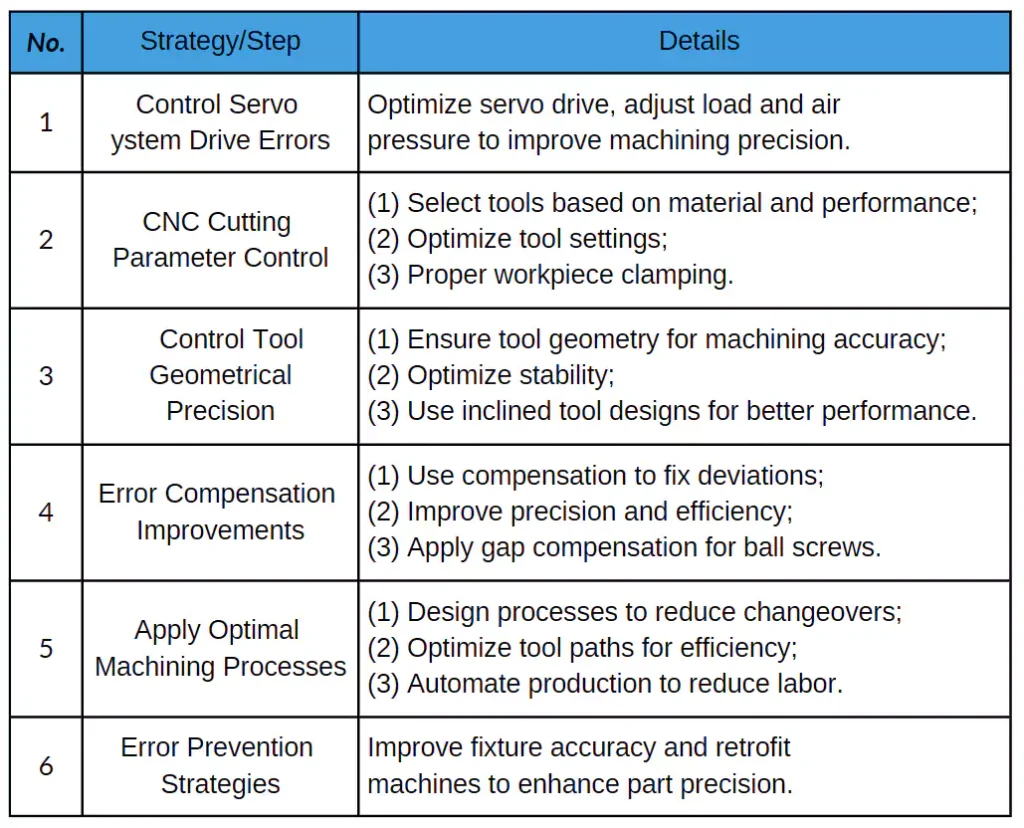
Optimization program
1.Improve Operator Tool Setting Accuracy
Tool control is a key step in high-precision machining on CNC lathes, but it’s difficult to operate. The accuracy of tool calibration and clamping directly affects machining accuracy and workpiece quality.
Upgrading operator skills to ensure correct tool alignment and clamping accuracy is essential for improving high-precision part manufacturing.
Currently, tool setting is done manually or automatically. Manual tool setting is more common but can cause abnormal tool wear due to improper setup.
Strengthening operator training and improving tool setting skills are key to better machining quality.
2.Enhance CNC Program Accuracy with Simulation
With rapid technological advancement, various simulation software, including CNC simulation systems, help designers verify programming code.
In actual production, CNC simulation systems visualize machining high-precision parts.
By simulating cutting, designers can identify problems and optimize the source program, improving machining quality.
Conclusion
CNC lathes are essential for machining production, offering high automation and efficiency.
Optimizing CNC lathe technology improves high-precision part quality and strengthens China’s position in global manufacturing. This effort enhances national prestige and comprehensive strength.