With the rapid development of machinery manufacturing intelligence, host factories in the construction machinery industry are undergoing transformation. This upgrade aims to improve the lean level of production and create an intelligent production workshop.
By configuring non-standard automation equipment to improve production efficiency and reduce the degree of manual intervention in the production process;
Automatically collecting data through the IoT platform, accumulating data samples and analyzing them, and ultimately improving the production process;
Pre-completion of production preparation through measures such as machining simulation, offline programming and centralized tool management.
Building an intelligent workshop not only improves the lean management level of the factory, but also significantly reduces labor costs.
This paper will illustrate the current situation and development trend of intelligent machining workshop from 3 aspects.
Application of non-standard automation equipment
As labor costs rise, factories are focusing on non-standard automation equipment. Machines replace manual labor for repetitive, low-tech tasks, such as using handling robots for loading and unloading.
Through the use of advanced workpiece conveyor chain and reasonable arrangement of the location of the machine tool, a robot can complete the loading and unloading of more than one CNC machining center, reducing labor costs to a greater extent.
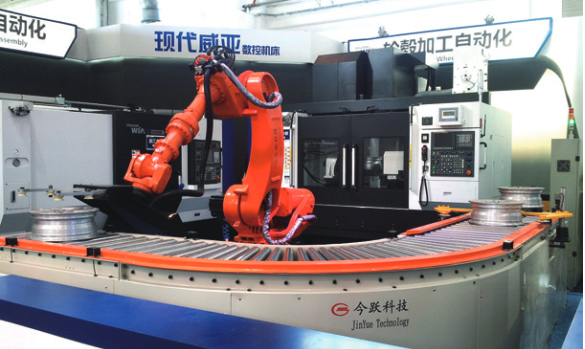
Figure 1 Six-degree-of-freedom articulated handling robot
In the machining process of the workpiece, often encountered tool wear and breakage, etc., non-standard automation equipment manufacturers in the design of automated production lines, will monitor the spindle torque of the machine tool, motor temperature and other data, according to the value of the spindle torque to automatically determine whether the tool is broken, or through the T S27R broken tool detection system to determine the degree of wear of the tool, and then notify the robot to replace the tool.
Some robots with higher automation are equipped with various hand grips. These grips can automatically change the tooling fixture, the CNC lathe’s tailstock, the tool’s collet, and other functional accessories.
Figure 2 shows a robot configuration that uses a vision camera to detect the workpiece’s burr location and shape. It automatically completes burr cleaning, achieving fully automated processing.
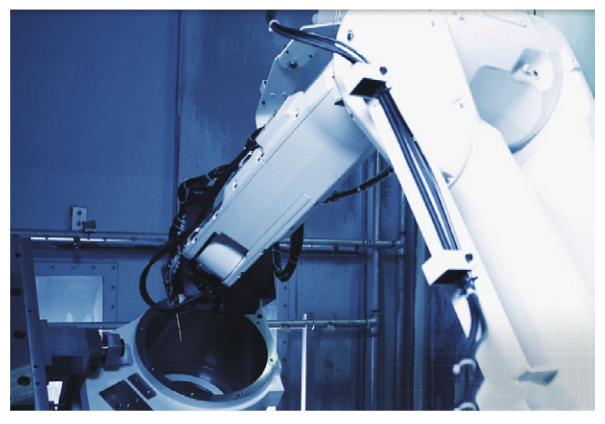
Figure 2 Robot cleaning workpiece burrs
In addition to automated processing, the intelligent workshop also focuses on the configuration of intelligent logistics tools, such as the use of A G V, unmanned forklifts and automatic stacker cranes to realize material transfer and storage, and through the logistics management system, the use of ID identification function for data management of workpiece information.
The logistics management system can automatically identify the handling priority of the workpiece to achieve optimal logistics management.
Figure 3 shows the storage rack, the MES manufacturing system notifies the stacker crane to pick up the workpiece, arranges AGV to transfer the workpiece, and then uses the robot to automatically load and unload the workpiece, and finally completes the machining on the machine tool.
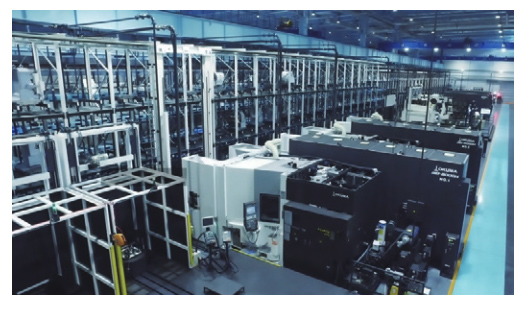
Figure 3 Warehouse type shelf
Application of SCADA platform
In the traditional machining workshop, managers manage according to the feedback from the scene and need to make judgments based on experience, which is not conducive to refined management.
The intelligent workshop realizes full-time data collection of CNC machines. It builds a stable and efficient data platform. The platform is reliable for equipment networking. SCADA is used for data collection and analysis. This ensures complete and accurate data collection.
Figure 4 shows the equipment data acquisition architecture. The SCADA platform is able to collect key production data from various types of machining centers, and transmit programs to and from CNC machine tools through network transmission protocols.
Through the collection and analysis of machine tool data, the utilization rate of machine tools can be maximized.
SCADA platform can not only realize equipment data collection and equipment interconnection, but also can be connected with MES production system in both directions, automatic statistics of equipment production and order completion, machining program can be automatically transmitted to CNC machine tools with MES work orders to realize production order management;
It also provides online inspection functions. It analyzes collected equipment and alarm information. It predictively proposes spare parts replacement and maintenance needs. This helps reduce downtime.
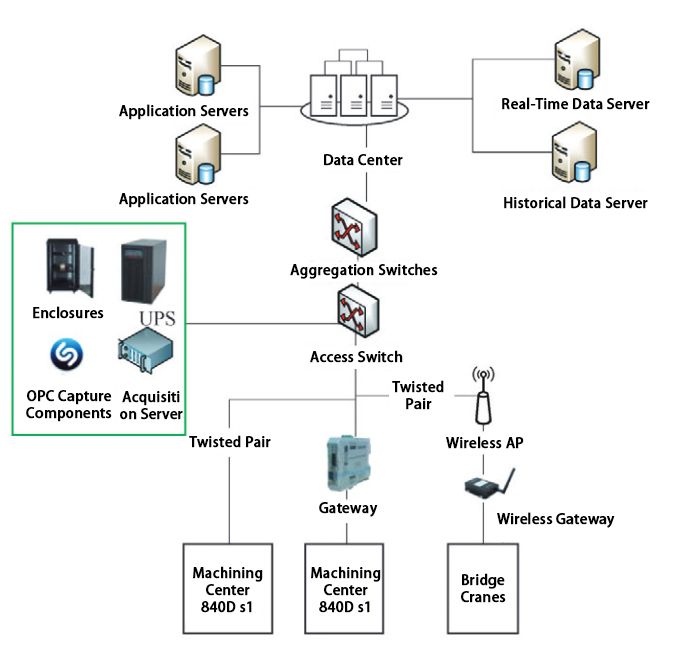
Figure 4 Machining equipment data acquisition architecture
Application of machining simulation and offline programming technology
In the production process, in order to improve the effective utilization of machine tools, it is often necessary to complete programming, tool pre-setting and other auxiliary work in advance to avoid the machine tool in standby mode.
At present, the machining simulation software is relatively mature (such as VERICUT, etc.), according to the actual size of the machine tool, fixture, workpiece and tool modeling and processing simulation.
Figure 5 shows the use of VERICUT software for wire rope slider processing simulation.
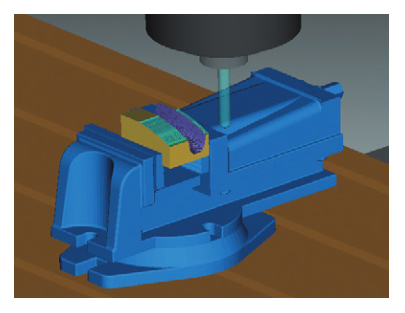
Figure 5 Using VERICUT software on the wire rope slider machining simulation
The use of simulation software can quickly detect syntax errors in CNC programs, tool and workpiece interference collision analysis, a greater degree of shortening the program debugging time.
In order to reduce the standby time of the machine tool caused by tool presetting, the workshop with a higher degree of intelligence will be centralized management of tool coding.
Figure 6 shows the tool presetting instrument, without machine downtime, can be completed beforehand tool presetting.
Through the ID code function, centralized management of the tool is realized. The system can automatically identify the tool’s location. It manages tool information and usage conditions. This helps accurately predict tool life. Timely replacement is ensured. Substandard product production can be avoided.
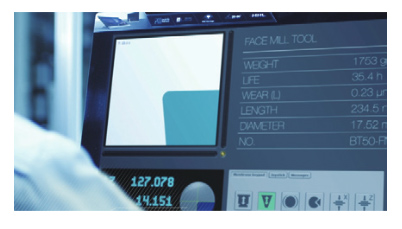
Figure 6 Tool presetting instrument
Conclusion
The construction of digital, networked and intelligent factories with the deep integration of information technology and industrialization can not only improve the level of lean manufacturing to a greater extent, but also significantly reduce labor costs, which is an important development direction for the transformation and upgrading of enterprises.