In carrying out a specific number of large parts machining process, such as automotive engine parts, as well as box parts, most of which will use a two-pin type of positioning jigs and fixtures, by the center of the CNC machine tool to control the machining, so this paper for the enterprise to carry out the production of parts processing process of a comprehensive summary of the relevant issues and analysis, for the problem gives a corresponding Countermeasures.
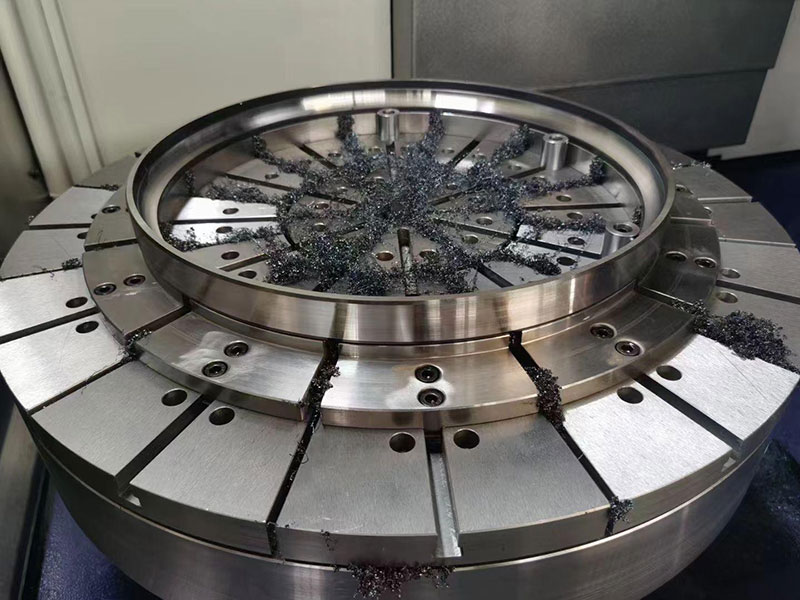
fixture
Parts processing fixture important role
1. Improve processing efficiency
In the entire machining process, the position of the workpiece has been controlled by the fixture, which is also to ensure that the workpiece is not deformed due to the influence of external forces.
Workpiece and fixture between the clamping method must be steel cutting mutual cooperation, the tighter the clamp, the lower the amplitude of vibration of the workpiece in the machining process, and the workpiece parts can not have a large change, may not have to fix the workpiece many times, not only saves time, but also improves the accuracy of the workpiece processing.
2. Improvement of machining accuracy
Enhance machining accuracy optimization of CNC machining fixture design has an important impact on the enhancement of parts machining accuracy.
First of all, the reasonable design of fixture structure, can effectively reduce the vibration and deformation of the parts in the machining process, to ensure the stability of the machining process.
Secondly, carefully select the fixture material to ensure sufficient rigidity and stability, so as to provide reliable fixation and support, to prevent the parts due to fixture instability caused by the error.
In addition, scientific arrangement of fixture positioning, clamping and support points can accurately control the position and attitude of the parts to further improve machining accuracy.
Therefore, through the optimization of CNC machining fixture design can significantly improve the machining accuracy of parts to meet the requirements of high-precision machining, improve product quality and competitiveness.
3. Expansion of the machine’s field of application
The extension of a machine without fixtures only positions the tool in the form of a mechanical structure, which affects the variety of products that can be produced at the same time, and in this case only a certain product can be produced.
If the tool is clamped to the machine, the range of tools can be effectively expanded.
In addition, for some of the larger parts, the selection of special type of fixtures for fastening operations, greatly increasing the use of tools, effectively reducing the use of restrictions.
CNC machining fixture design affects the accuracy of the parts of the main issues
(1) Choosing the right fixture
The work must be designed and produced parts have a full understanding of the standard selected according to the design and manufacture of suitable fixture varieties, but also the design and manufacture of fixtures to deal with.
Fixture product design should meet the precise positioning of parts, rigidity standard requirements.
If the clamping style can not meet the design and manufacture of parts and components of the conditions, often increase the complexity of the parts manufacturing process and increase its weight, may also lead to the design of the parts can not meet the required size.
(2) Keep coordinates
Machine coordinate system and processing parts plane coordinates should ensure their consistency, as well as as as far as possible to make the plane coordinates between the relatively simple transformation to ensure that in the process of machining to obtain less omission.
The operator needs to design the required plane coordinates of the part, and adjust it with the plane coordinates of the CNC lathe to the same, and then according to the plane coordinates of the starting point and the target position, and then determine the location of the clamping coordinates.
(3) Fixture rigidity standards
If the rigidity standard of the fixture can not meet the rigidity requirements of its processing parts, often resulting in parts in the manufacturing process is easy to deform and cause its dimensional accuracy is not enough.
In the specific production of CNC lathe parts in the process, in the production and processing of the same type of parts in the various processes, but also always use the same type of fixture.
(4) Removal and replacement
Fixture removal and replacement is a difficult problem in the process of CNC lathe work, the same series of dimensions of the product workpiece reprocessing process, the designer must start from the practical characteristics of the fixture to carry out the design of the fixture, to facilitate the replacement of fixtures to obtain a further reduction in the frequency of work.
In the fixture removal and replacement process, the staff should also carry out strict control of the fixture’s surplus.
Fixture design process affects the accuracy of the parts of the problem examples and improvement measures
1. Introduction to Fixture Design Challenges
Fixture design plays a crucial role in CNC lathe machining, as improper fixture positioning can negatively impact processing accuracy. Through case studies, this section explores potential issues arising from non-designed parts affecting machining precision.
2. Key Features of the Part Design
Figure 1 presents a critical part containing:
- A large central hole (D38.015 mm ± 0.015 mm)
- Two rolling bearing holes (D14 ± 0.015 mm)
- A required centerline distance accuracy of 0.025 mm
During machining, two positioning pins are used to align and process the large hole and rolling bearing holes. However, errors in fixture design can introduce positional deviations that affect precision.
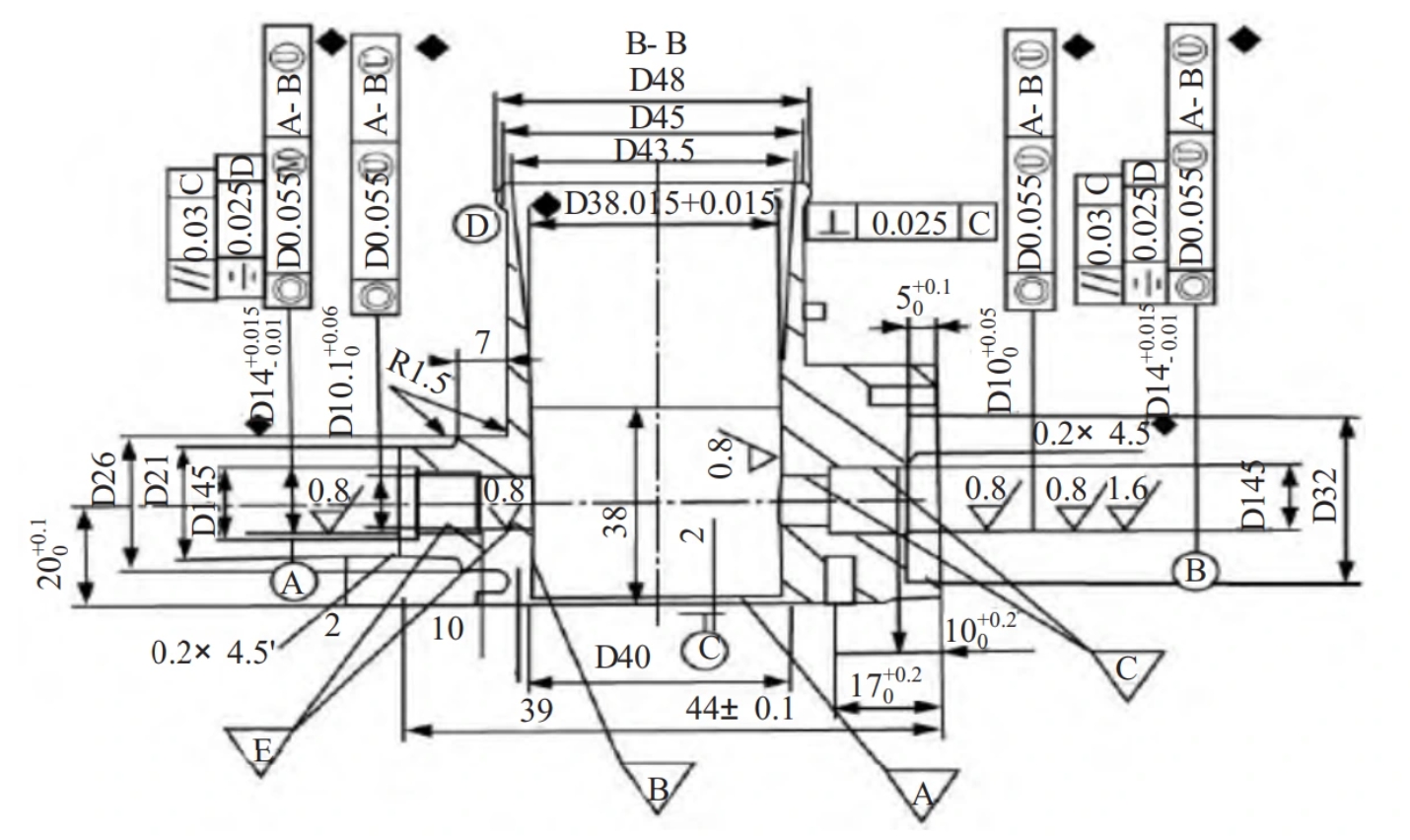
Figure 1 The main structural engineering of a part (unit: mm)
3. Common Issues in Machining and Clamping
(1) Positioning Challenges
- The two pins on one side create difficulties in ensuring accurate alignment.
- The upper-bottom holes (A and B) serve as locating pins, but their alignment with the central hole differs.
- This mismatch can result in rotation errors during machining, affecting part quality.
(2) Impact of Positioning Gaps
- The gap between the positioning pin and port allows unintended movement and angular shifts.
- These deviations cause fixture misalignment, leading to precision loss and declining part performance.
(3) Parallelism Errors in Hole Processing
- Minor misalignment during machining results in deviations in the centerline of the rolling bearing holes.
- This misalignment compromises the parallelism relative to the central hole (D38.015 mm ± 0.015 mm).
4. Countermeasures for Fixture Optimization
(1) Improving Fixture Assembly
- Ensure material selection meets required width and thickness specifications.
- Follow design drawings precisely for accurate cutting and slotting.
- Properly align fixture plates on the CNC machine for consistent stamping and positioning.
(2) Enhancing Machining Precision
- Establish long diagonal reference lines to improve part mounting.
- Drill guide holes in critical locations for better attachment alignment.
- Consider early hole opening to prevent difficulties in placing parts with recessed grooves.
(3) Optimizing Fixture Thread and Hole Processing
- Adhere to standard design dimensions for threaded and screw holes.
- Create slightly larger small holes to minimize machining intervention difficulties.
- Implement fixture slots to enhance clamping efficiency and reduce deviations.
5. Advanced Solutions for Positioning and Precision Control
(1) Adjusting Positioning Pins
- Modify pin A and hole B to enhance centerline alignment.
- Adjust pin B and pin C placement to minimize rotational errors, improving machining precision.
(2) Optimizing Tool-Setting Center Alignment
- Adapt X-axis design criteria by placing the tool changer center at the pressure casting hole (D10.01 mm).
- Secure drilling centers on both sides of mounting pins C for enhanced X-axis stability.
(3) Improving Fixture Reusability and Precision Control
- Reduce basic deviation in positioning, engineering, and manufacturing processes.
- Use small tapered pin C and A hole to control symmetry precision, ensuring fixture accuracy.
- Minimize gaps in measurement detection, improving new product quality and standard compliance.
By refining fixture design, positioning methods, and machining processes, CNC lathe processing can achieve higher precision, improved efficiency, and superior product quality.
Conclusion
Through the summary of the parts processing and production process and reflection found that in the actual operation of CNC machining process, relative workpiece fixture setup and tool change position relative direct relationship between the efficiency of processing parts.
So the need for relative technology production and processing, and, engineers and technicians in the process of CNC lathe design, but also need a clear understanding of the basis of the standard design program, as well as the precise benchmark design and manufacturing technology basis of the interconnections between to ensure that in the production process of specific clamping design will be the three to achieve a reasonable coordination with the process, which effectively improves the accuracy and efficiency of the production of parts. Thus effectively promote the rapid development of the machining field.