Box parts processing, should be reasonable to determine the type of production and blank processing mode, reasonable selection of positioning reference, scientific combination of machining processes, accurate calculation of machining allowances and other process parameters, to ensure that box parts machining accuracy.
Fixture quality and performance of box parts machining efficiency and accuracy has an important impact, so it should be combined with the actual requirements of box parts design fixture.
The design of fixtures should strictly comply with the relevant design specifications and technical standards, according to the design points to reasonably determine the relevant parameters, and constantly optimize the design scheme, so that the design of fixtures has a stronger practicality.
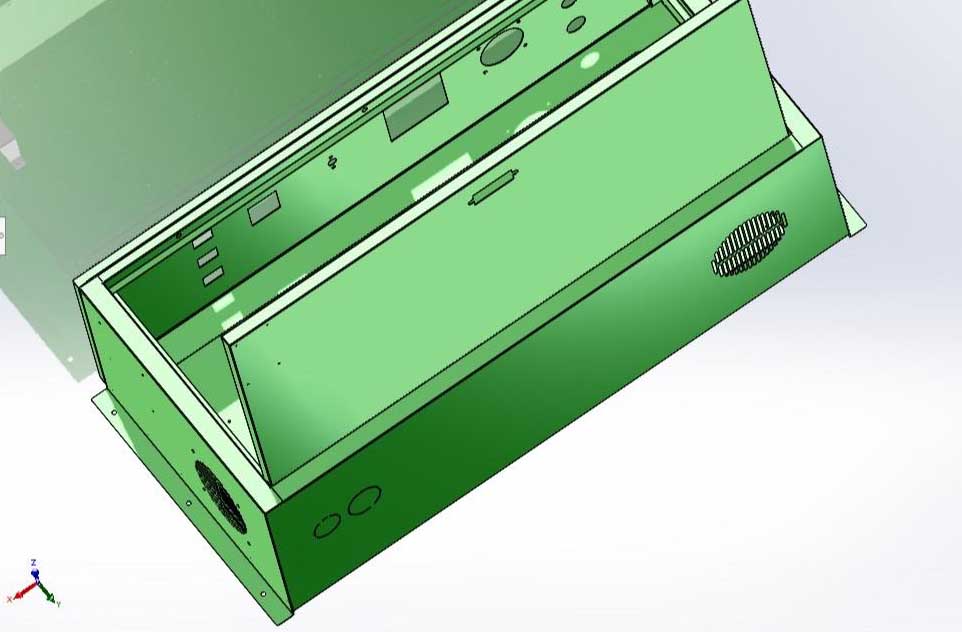
Box parts machining process
Box parts have high requirements for machining processes. This paper takes an inclusive support drive mechanism as an example to explore fixture design. The machining process of box parts is analyzed to guide the fixture development.
1. Box parts production type
Box parts machining should be based on the planned output, production schedule and other calculations to analyze the average scrap rate and spare parts rate, to reasonably determine the type of box parts production. In this paper, the box parts production using small batch processing.
2. Box parts blank processing mode
Blank casting process, small batch processing generally choose pressure casting, metal molding and die forging and other processing techniques.
Combined with the yield and accuracy requirements, the box parts machining metal mold casting process, can improve the internal structure of the box parts and unit area of the organization of the density of the yield, in addition to a reasonable choice of blank material type.
3. Select workpiece positioning reference
According to the machining accuracy requirements, the positioning datum includes coarse datum and fine datum.
Box parts machining in the reasonable choice of positioning reference, is an important part of the machining process.
Initial processing, workpiece positioning reference is usually the blank surface. Determine the rough datum is the first process of box parts machining.
Selection of coarse datum, should choose the unprocessed surface of the blank, the surface should be important but shall not be reused, at the same time the surface should be easy to clamp and machining allowance control.
When selecting the fine datum, should ensure that the benchmark coincides with the unity, not only to be able to since the benchmark, but also for each other as a benchmark, in order to effectively control the value of the positioning error, to improve the box parts of the product qualification rate.
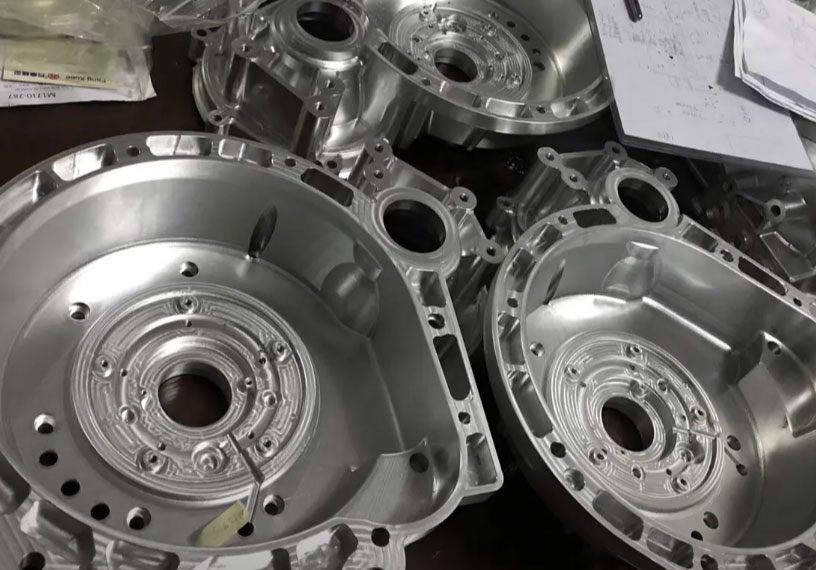
4. Box parts machining process
In the box parts machining involved in the processing technology and process links more, so in the processing practice should be a combination of scientific processes to improve processing efficiency and reduce processing costs.
According to the characteristics of the box parts machining production type, in accordance with the principle of process concentration of process combinations, in order to shorten the process route, to ensure that the machining accuracy of the parts.
5. Box parts machining process
Box parts machining, should be based on parts processing size, geometry and machining accuracy requirements to select and optimize the process route.
In this paper, the box parts processing mainly includes blank casting, aging treatment, scribing, rough milling, rough turning, drilling, reaming, rough reaming, boring, tapping, deburring and cleaning.
Determine the process route, should be based on the machining accuracy requirements, positioning benchmarks, whether easy to clamp, whether the fixture can be reused, the number of required machine tools, and whether the process of machining needs to change the machine tool and so on to determine a reasonable process route.
At the same time, should also give full consideration to the processing of parts, parts of the scrap rate to further optimize the process route to reduce the number of clamping and replacement of machine tools, improve productivity and processing quality.
6. Box parts machining allowance
Machining allowance refers to the thickness of the metal layer removed from a workpiece surface during machining. A reasonable allowance is crucial for achieving the required accuracy of box parts.
Therefore, the machining allowance for each process should be calculated and analyzed according to relevant technical specifications. Accurate determination of process parameters ensures part quality and helps reduce machining costs.
7. Machine tools for case parts machining
Box parts processing, should be based on the outer contour of the parts size, parts processing accuracy and production type selection of machine tools.
Drilling and boring and other machining processes need to use specialized machine tools, tapping, milling and chamfering and other machining processes generally use general-purpose machine tools.
Production units should be based on the box parts machining process requirements to choose the type of machine tool.
8. Box parts machining fixture
Cutting processing, the need to use fixtures for workpiece positioning, so a reasonable choice of fixtures is conducive to the performance of the machine tool process, improve machining accuracy and efficiency.
Box parts machining in a variety of types of fixtures, different fixtures of the application range and power source, there are some differences. General-purpose fixtures are mainly suitable for small batches or single parts processing;
Specialized fixtures are mainly suitable for more than a batch of parts processing. Production practice should be based on the type of production, machining accuracy requirements, such as the choice of fixtures.
9. Box parts machining tools
Different processing techniques, workpiece size specifications and machining accuracy of different tool requirements. Box parts machining should be based on the requirements of the process manual to select the appropriate standard tool.
Box parts machine fixture design
1. Box parts machining lathe fixture design
Lathe fixture is an important auxiliary tool for parts end face and rotating surface machining. Lathe fixture design to ensure that the axis of rotation of the machine tool spindle and the centerline of the workpiece to maintain consistency.
> Design principles
When designing lathe fixtures for box parts machining, the structural form of the positioning device should be scientifically selected, attention should be paid to the rationality of the layout position, and the design should be based on the fixture rotary axis positioning element benchmark.
The design of the clamping device should be a comprehensive analysis of the cutting torque, centrifugal force and gravity, etc., to ensure that the clamping force and self-locking performance of the clamping mechanism to meet the requirements of box parts machining.
Fixture design using angle iron type design, should fully consider the drag force mode. Designers should fully understand the characteristics of the machining process and the benchmark to determine the way to improve the feasibility of the design program.
When designing lathe fixture positioning elements, their structure and layout should follow axial coincidence requirements. This ensures the machining accuracy of parts meets the specified process standards.
When the lathe fixture design adopts the disc type or angle iron type structure, pay attention to the fixture balance, can take the configuration of counterweight block and other ways to reduce the vibration caused by asymmetric fixture structure.
Fixture structure layout should be compact, the center of gravity and spindle similar, if conditions allow, should be as short as possible to shorten the size of the cantilever.
The design should also be based on the fixture contour line to determine the size of the components, to avoid components beyond the fixture contour; can be set up on the fixture shield and other devices to avoid the coolant or cutting splash damage to the fixture.
> Design points
In the rough machining of box parts, only the left and right end faces have length requirements. The left end face is used as the design reference. To control movement, elastic sleeves or supports are applied to limit degrees of freedom.
Designers should follow design specifications and select a suitable safety factor. This ensures accurate calculation of cutting force, clamping force, and other parameters.
They must also choose an appropriate clamping mechanism based on the production characteristics of box-type parts. Positioning, clamping, and wear errors should be calculated and controlled according to design standards to keep them within acceptable limits.
2. Box parts machining drilling machine fixture design
> Scientific selection of positioning reference
In drilling fixture design, only the dimensional accuracy of the holes is critical. Therefore, the center hole axis is used as the positioning reference. A mandrel is applied along with the left end face and the bottom surface to restrict the workpiece’s degrees of freedom.
> Accurate calculation of the design parameters
In fixture design, the designer should select the cutting and clamping force formulas based on design specifications. These calculations should also consider spindle feed rate, drilling diameter, and safety factors.
Once the fixture structure form is determined, clamping force must be analyzed further. Key factors include original fixture force, force arm, helix angle, thread friction angle, and part friction coefficients. Designers must also consider screw-end friction and thread equivalent friction angle. This analysis helps validate clamping reliability and optimize the fixture structure.
> Accurate control of positioning error value
In drilling machine fixture design, designers must calculate and analyze various errors. These include positioning error, clamping error, wear error, and drilling sleeve hole spacing error. The analysis should follow fixture design specifications. The goal is to ensure all error values remain within the allowable range.
Conclusion
With the development of manufacturing industry, the level of parts processing technology is constantly improving. Box class machining should actively introduce advanced processing technology, and continuously improve the quality and efficiency of parts processing.
At the same time, practical production experience should be summarized. On this basis, bold innovation is encouraged to optimize the box parts machining process. This helps improve product qualification rates, reduce resource waste, and lower processing costs.
In addition, fixture design should be based on the actual machining needs of box parts. Properly designed fixtures support machining accuracy and help improve the overall quality of part production.