In metal processing, annealing, normalizing, quenching and tempering are the most common heat treatment methods used by the relevant personnel, heat treatment improves the performance of the metal as well as the characteristics of the metal to able to improve, and then be able to ensure product quality meet the use of the requirements of the industry is very important, at present, normalizing can be used as the final or preheating treatment, widely used in the mechanical industry.
Characteristics and precautions of the normalizing process
Normalizing, also known as normalizing, is to heat the workpiece to Ac3 (Ac is the end of the heating of free ferrite all transformed into austenite temperature, generally from 727 ° C to 912 ° C between) or Acm (Acm is the actual heating of the eutectic steel fully austenitized critical temperature line ) above 30 ~ 50 ° C, after holding for some time, removed from the furnace in the air, or water spray, spray, or blowing the cooling of the Metal heat treatment process.
The normalizing heating temperature is mainly based on common steel grades. This ensures the metal forms an austenitic structure. Storage time depends on several factors, including metal type, machine size, number of generators, and equipment type. Details are shown in Tables 1 and 2.
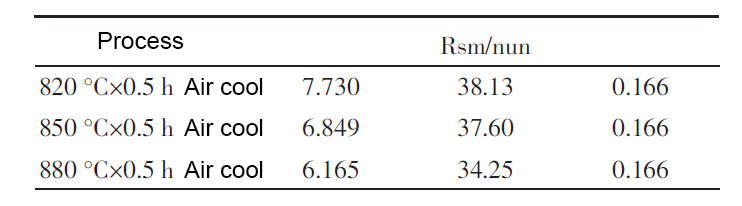
Table 1 Surface roughness of parts after normalizing.
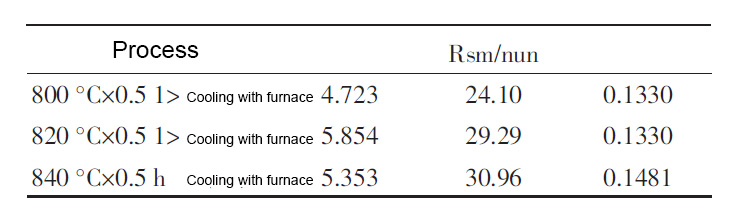
Table 2 Surface roughness of parts after annealing
It is important to note that normalizing cooling ensures that the rules (maximum and maximum hardness) are scientifically sound and naturally stable structures, e.g., for pearlitic materials.
The cooling of the equipment is usually air-cooled, high-quality normalizing can make fan cooling or spray cooling to achieve the desired results. Pay attention to the following points when making:
(1) The host is the core of the CNC machine tool. It consists of the column, bed, and cutting parts. It is responsible for bearing the force and ensuring the stability needed during processing.
(2) The drive powers the CNC lathe. It includes the spindle drive, spindle motor, and feed motor. It uses electronic or electro-hydraulic servo systems to control the spindle and feed movements accurately.
(3) The numerical control device includes both hardware and software for the CNC lathe. It inputs and stores the parts processing program and processes large amounts of data. It ensures the lathe performs all processing tasks accurately.
(4) The auxiliary devices support the stable operation of the CNC lathe. These include the cooling, lighting, lubrication, and chip removal systems. They ensure the equipment operates smoothly and efficiently during the machining process.
(5) After the workpiece is removed from the oven, it should be cracked, placed in a dry place and cooled, do not store the device or store it in a damp place.
Application of normalizing
1.For low carbon steel
Due to low carbon content after annealing, cutting can cause adhesion. Cutting performance improves. Annealed hardness and toughness increase slightly. Therefore, annealing can be used as a preheating treatment before cutting.
2.For medium carbon steel
Normalizing instead of annealing improves the performance of the product. For some stress-free operations, normalizing can change the tempering according to the final heat treatment to make heat treatment easier, also can be used for pre-surface heat treatment, induction heating quenching.
3.For tool steels, bearing steels, etc.
Hypereutectoid steels are annealed spherically, normalized, and heated to the top Acm before secondary normalizing to dissolve the entire primary reticulated carburite in austenite and to carburize at high rates in the austenitic grains.
The formation of reticulated carbon is inhibited to obtain the good structure required for normalizing spheroidization.
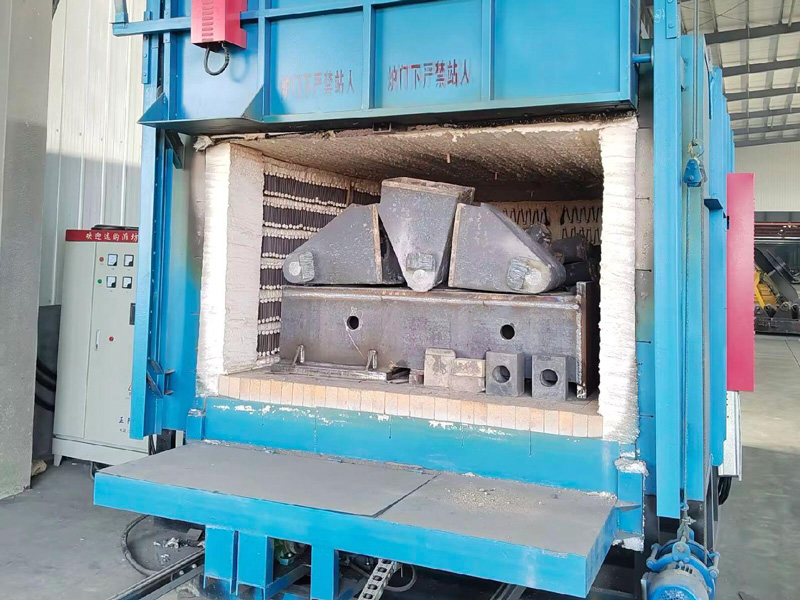
Normalizing processing
4.Used to eliminate hot working defects
Medium carbon steel castings, forgings, lap joints and welded surfaces are often the cause of overheating defects and coarse grains after heat treatment. Normalizing process can eliminate these problems and achieve the purpose of improving grain quality, organizational differences and eliminating internal stress.
For example, for the need for strong welds in the region, the use of normalizing to improve the weld structure, to ensure the strength of the weld, especially for oil welded joints, the applicable way is normalizing and tempering heat treatment, the main reason is that in the oil weld region and the heat-affected zone is the presence of coarse grains, with all the coarse grains is the need to miniaturize, but if the normalizing is not able to comprehensively eliminate the defects of heat processing, you need to first Elimination of high temperature stress before the full elimination of defects.
5.Used in the heat treatment process of reworked parts treatment
If a part is overheated, lacks hardness, has soft spots or other defects after quenching, it can be treated by normalizing and rehardening. Equipment required for machine operation must be refined, fine-tuned and strengthened to meet the requirements of machine operation.
Medium and high alloy steel and large forgings should be hot tempered after normalizing to eliminate the internal stresses generated during normalizing.
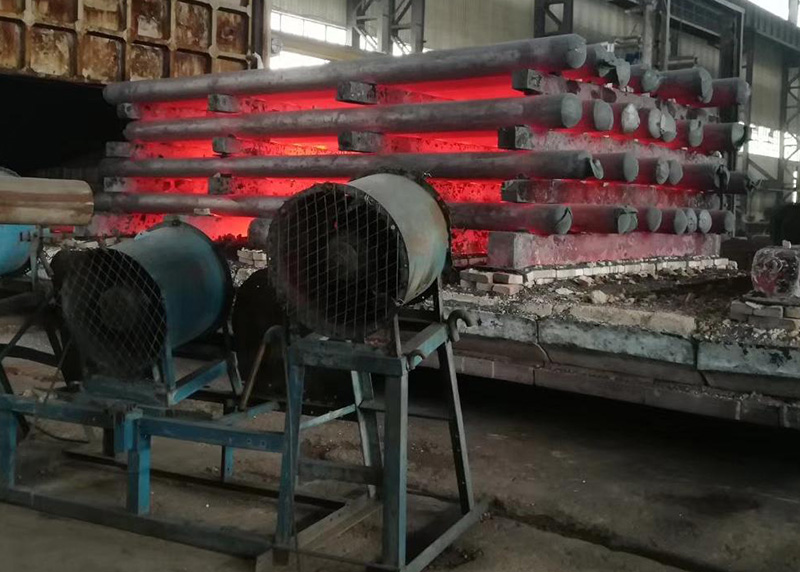
Normalizing defects and remedial measures
1.mesh carbide
For eutectic metals, in the use of normalizing process, need to ensure its cooling rate, if the speed is not up to the requirements, then the carbide will be directly distributed to the austenite grain boundaries of the reticulation.
For this type of defect often occurs in equipment with a large number of overlaps. Therefore, in order to effectively solve this defect, the remedial measures used are to increase the cost of air-conditioning, blast cooling, water spray cooling, etc.
2.Coarse Widmanstatten
Coarse Widmanstätten structures usually appear in high-temperature, coarse austenitic grains. They are common in fast-cooled, medium carbon steels. In these cases, ferrite is distributed as flake-like structures along specific crystallographic planes within the original austenitic grains.
The remedy adopted for this defect is to allow the crystal to be refined by complete annealing or modification.
3.Banded organization
The metal is subeutectic, which means it contains both ferrite and pearlite. Due to their different shapes during fabrication and slow cooling, ferrite forms in some areas and pearlite in others.
Therefore, the remedy for this defect is mainly through the improvement of the cooling process can reduce the electrical design to implement.
4.Parts produce large internal stress and deformation
Parts of the image in the production up, very difficult, due to the high pressure of normalizing, the material will produce internal stress and deformation, including cracks. Therefore, the main remedy for this defect is the recommended annealing process.
Types of normalizing treatment
1.General Normalizing
General normalizing, also called normalizing, involves heating sub-eutectic metal for a set time. This allows the metal to gradually austenitize. The process produces high-quality austenitic material and removes defects from earlier stages. After cooling, it forms uniform equiaxed ferrite and pearlite. This improves both the structure and coating performance of standard steels.
At present, most of the normalizing treatment obtained through the production of hot rolled mild steel and low alloy steel plate is widely used.
2.Sub-temperature normalizing
Sub-temperature normalizing, also called critical normalizing, involves heating the metal to a specific temperature. This temperature is maintained for a period to allow the metal to austenitize into a fine structure. However, this process does not remove defects from earlier stages. Most of the ferrite does not take part in the recrystallization process.
Therefore, sub-temperature normalizing is used only for rolling control and cooling of the metal. The page is free of defects. The sheet metal is then normalized.
In this way, a generalized technique has emerged which combines a controlled rolling and cooling system with sub-temperature normalizing, and two normalizing processes, general normalizing and sub-temperature normalizing.
Sub-temperature normalizing slightly reduces the properties of the plate, but improves plasticity and temperature resistance, and is also required to improve bending temperature properties.
3.Intensive Normalizing
Strengthened normalization is also known as cooling normalization. The principle of controlled rolling followed by controlled cooling is designed for cooling the austenite after normalizing.
The key to this process is the same austenitizing temperature as before, then spray cooling to 550~700 ℃, cooling water after the influence of cooling to create a better process than ferrite and pearlite.
As the temperature changes, the pearlite not only becomes cleaner, but it also deteriorates, allowing the pearlite value to increase and a small amount of bainite organization to occur.
This over-organization increases strength and tensile strength and decreases elongation and impact toughness compared to normalizing, but does not reduce the cold impact toughness of the plate. Controlled normalizing temperature is suitable for steel plates with low grade content or thick steel plates.
4.Normalizing for high temperature tempering
During low and medium temperature changes, materials that undergo high-temperature tempering and normalizing show certain characteristics. Their chemical composition is below the limit for the normalizing grade of steel. While their energy properties are generally higher, their plasticity and toughness remain similar.
When in the completion of normalizing, although its strength will be reduced, but plasticity will be improved, especially in terms of temperature, remittance toughness, as well as cold bending properties have a great influence.
At the same time, because the temperature between normalizing and tempering is very close, the tempering temperature reaches 620~680 ℃, but when the normalizing is done, it does not need a special furnace for high temperature tempering.
The process is to quickly maintain the temperature, or to normalize the furnace temperature to room temperature. The tempering temperature is usually hot tempered.
5.In-Line Normalizing
The sheet metal is moved from place to place on the ZX before entering the furnace for recovery.
During normalizing, the specimen undergoes supercooled austenite phase transformation and recrystallization to obtain the proper organization and function. In-line normalizing is more than just normalizing.
6.Deformation Normalizing
The main function of deformation normalizing controlled rolling is deformation normalizing, i.e., improving the organization and properties of the metal. It serves the same function as normalization.
This is usually used for low carbon and low iron ores and not for normalizing. It is generally referred to as deformation normalization.
True transformation and normalization is a combination of transformation and normalization. Low carbon and low alloy steels are heated to the normalizing temperature (900 to 950 °C), deformed to a certain degree above Ar3 and then air cooled.
Due to the presence of fine austenitic particles during the normalizing process, they are deformed when heated.
The deformation zone is formed by the addition of ferrite particles to the austenitic particles after normalizing, which improves the strength and toughness of the steel. Normalization of deformation is also known as the NIC method.
7.Inline Rolling Solid Heat Deformation Normalization
The in-line rolling solid heat deformation normalization process, also called the HT method, involves several steps. First, hot-rolled plates are cooled below 550 °C on the flow line. Then, they undergo Ar3 deformation in a medium-temperature furnace at 900–950 °C. Finally, they are air-cooled to achieve optimal results.
Conclusion
In summary, normalizing is an essential heat treatment process widely used in metalworking industries to improve the mechanical properties and performance of steel products.
Normalizing involves heating the workpiece to a set temperature, then cooling it in air or under control. This process improves structural uniformity and removes defects and internal stresses.
This process is particularly useful for low carbon and medium carbon steels, tool steels, and bearing steels, as well as in the treatment of reworked parts.
Normalizing improves properties such as hardness, toughness, and machinability, making it ideal for preparing materials for further heat treatment or for achieving desired characteristics in finished products.
However, attention must be paid to factors like cooling rate, equipment temperature, and correct handling of workpieces to avoid defects such as mesh carbide, coarse Widmanstatten, and banded structures.
Additionally, there are various types of normalizing treatments, including general, sub-temperature, intensive, and deformation normalizing, each suited for specific materials and applications.
By carefully controlling the normalizing process and applying remedial measures when necessary, industries can ensure improved material quality, extended service life, and enhanced product performance, which are crucial for maintaining competitive advantage and meeting industry requirements.