Plasma cutting is an advanced process that uses a high-temperature plasma jet to cut metal. Since it was first introduced in the 1950s, this technology has been widely used in a variety of industries, such as manufacturing, automotive, aerospace, and shipbuilding. Plasma cutting has become an important means of modern metal processing due to its high efficiency, precision, and adaptability. By conducting an electric arc to the material being cut, the high-temperature plasma generated melts the material and blows it away from the cut, resulting in a fast and clean cut.
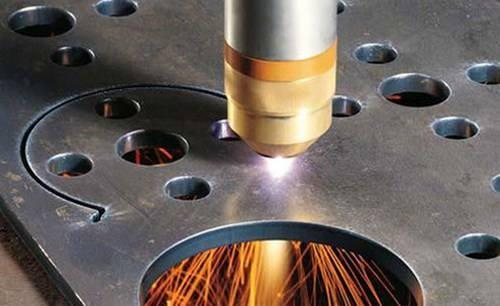
What is plasma cutting?
Plasma cutting is a metalworking process that cuts metal materials by using a high-temperature plasma jet. Plasma is an ionized gas with extremely high temperature and energy. When a high-pressure gas (usually air, nitrogen, or oxygen) passes through a narrow nozzle and is ionized by an electric arc, the resulting plasma jet can quickly heat and melt the metal material. During the cutting process, the plasma jet not only melts the metal but also uses its high-speed gas flow to blow the molten metal away from the cut, resulting in a clean and precise cut.
Working principle of plasma cutting
The working principle of plasma cutting mainly relies on the heating and melting of metal materials by high-temperature plasma jets, and the blowing away of molten metal by high-speed airflow. The specific process is as follows:
1. Arc formation
The cutting process begins with the power supply of the plasma cutting machine, and an arc is formed between the electrode and the nozzle. The high temperature generated by the arc ionizes the gas (usually air, nitrogen, or oxygen) to form plasma.
2. Plasma jet generation
The ionized gas is heated to an extremely high temperature (usually up to 30,000 degrees Celsius) and ejected at an extremely high speed through a narrow nozzle to form a plasma jet.
3. Heating and melting metal
When the plasma jet contacts the metal material, its high temperature causes the metal to heat and melt rapidly. Due to the highly concentrated energy of the plasma jet, the temperature in the cutting area is extremely high, which can quickly melt the metal.
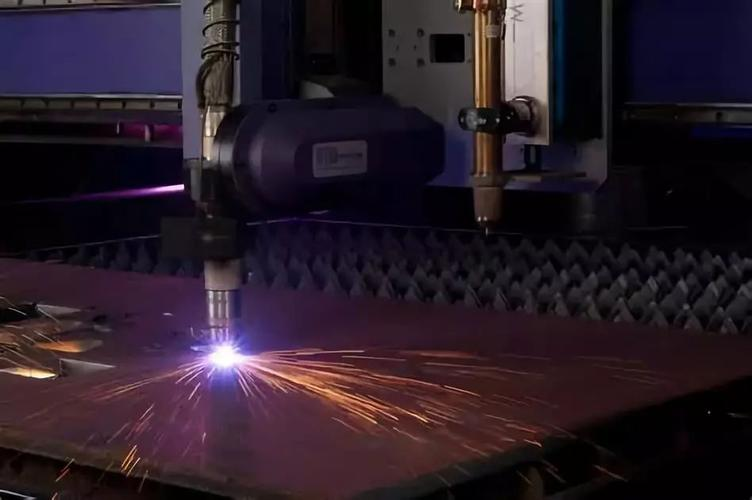
4. Blowing away molten metal
The high-speed airflow not only heats and melts the metal, but also blows the molten metal away from the incision through its kinetic energy. This process makes the incision clean and neat, reducing the generation of slag and burrs.
5. Cutting is complete
As the plasma jet moves along the cutting path, the metal material is continuously melted and blown away, ultimately achieving the purpose of cutting.
Material for plasma cutting
1. Aluminum material
Aluminum is conductive, making plasma cutting an ideal process for manufacturing it. In addition, the process has the advantage of processing thicker metals compared to other aluminum manufacturing methods such as laser cutting. It can cut aluminum up to 160 mm thick. In addition, it is more cost-effective to use plasma cutting to manufacture aluminum due to lower operating and equipment costs.
2. Mild steel
Mild steel is a type of steel with a low carbon content, usually up to about 2.1%. It is one of the most commonly used steels due to its suitability for a variety of uses. In addition, mild steel is not expensive to obtain, and it has properties such as high impact strength, weldability, and ductility.
3. Stainless steel
Stainless steel is an iron alloy that is both corrosion-resistant and rust-resistant. Plasma cutting is one of the most effective methods for manufacturing this metal because it allows cutting thicknesses up to 30 mm. Stainless steel grades suitable for cutting include 304, 304L, 316, 316L, 321, 310S, 317, etc.
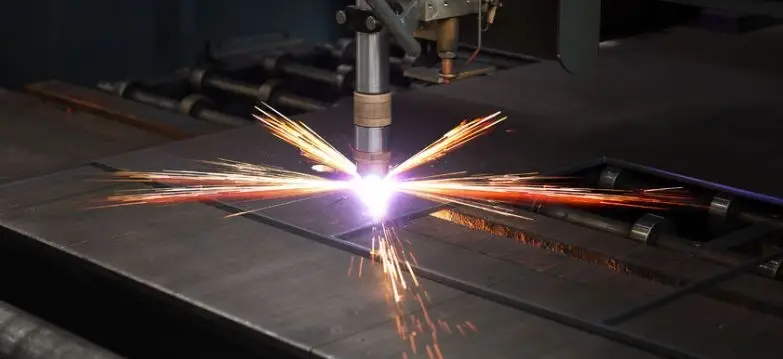
4. Brass
Brass is another metal that is easy to make using plasma cutting. This is due to its high electrical conductivity. However, when making brass using this method, it is best to do it in a well-ventilated area. This is because brass contains zinc, and breathing combustion fumes containing zinc is harmful to health.
5. Copper
Copper has the thermal and electrical conductivity of all materials except precious metals. Important qualities of this metal include corrosion resistance, high ductility, and weldability. These properties, including its high electrical conductivity, make copper an ideal metal for plasma cutting. However, like brass, it is important to cut this metal in a well-ventilated area.
6. Cast Iron
This metal is popular for its low cost and ductility. It contains trace elements such as manganese, sulfur, phosphorus, and silicon. Cast iron has good electrical conductivity, high compressive strength, and a low melting temperature, making it ideal for plasma cutting.
Why choose plasma cutting?
1. High efficiency
Plasma-cutting technology is known for its high cutting speed and efficiency. Because the plasma jet can quickly heat and melt the metal, it can complete the cutting task faster than traditional cutting methods (such as oxygen cutting). This high efficiency makes plasma cutting an ideal choice for handling large-scale metal cutting needs, especially in production lines and manufacturing workshops.
2. Precision cutting
Plasma cutting provides a high degree of cutting accuracy. Because the temperature and energy of the plasma jet are highly concentrated, it can achieve very smooth and clean cutting edges, reducing the need for secondary processing. The high quality of the cutting edge and small errors are suitable for precision processing and applications requiring high-quality cuts.
3. Wide range of applications
Plasma cutting can handle a variety of conductive metals, including carbon steel, stainless steel, aluminum, copper, etc. It can cut metal materials of different thicknesses, whether thin or thick plates. This wide range of applicability has made plasma cutting widely used in various industries, including manufacturing, construction, auto repair, etc.
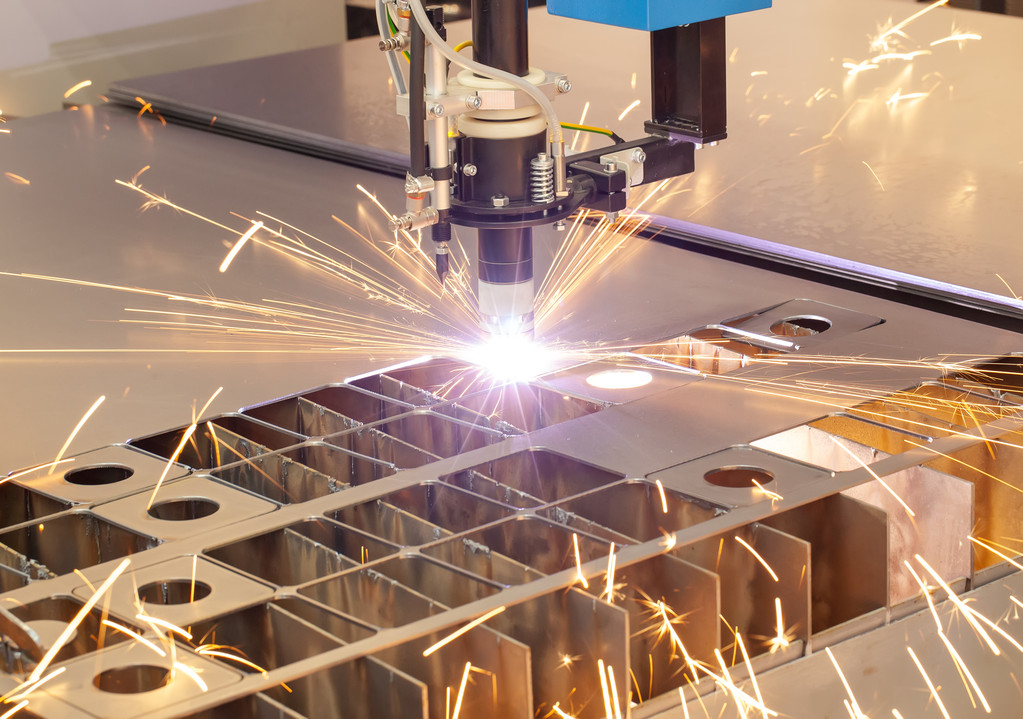
4. Low maintenance cost
Compared with many traditional cutting methods, plasma cutting has low maintenance costs. The structure of plasma cutting equipment is relatively simple, the parts are less worn, and the consumables (such as cutting nozzles and electrodes) are replaced less frequently. In addition, less slag and residue are generated during plasma cutting, which reduces the workload of subsequent cleaning and processing.
5. Flexibility and ease of operation
Plasma-cutting equipment is simple to operate, highly flexible, and suitable for manual and automated operations. Operators can adapt to different cutting needs by adjusting cutting parameters (such as current intensity and gas flow). In addition, plasma cutting can handle cutting paths of various shapes and complexities, providing a high degree of design flexibility.
Conclusion
Plasma-cutting technology occupies an important position in modern manufacturing with its efficient and precise cutting capabilities. It can not only handle a variety of metal materials, but also provide smooth cutting edges and lower heat-affected zones, making subsequent processing easier. With the continuous advancement of technology, plasma-cutting equipment is becoming more and more intelligent and automated, which improves production efficiency and reduces operating costs. Understanding and mastering the applications and advantages of plasma cutting is of great significance to improving manufacturing quality and efficiency. In the future, with the development of technology, plasma cutting will continue to bring more innovations and breakthroughs to the manufacturing industry.