What is a rapid tool?
Rapid tooling, as the name implies, is a mold made through rapid prototyping technology and efficient manufacturing processes. Rapid tooling is usually used in the development stage of a product for small batch production, trial production and functional testing. It can be transformed from design drawings to actual molds in a short time, greatly shortening the traditional mold making cycle. The core of rapid tooling lies in the rapid prototyping technology it uses, such as 3D printing, CNC machining, vacuum casting, etc.
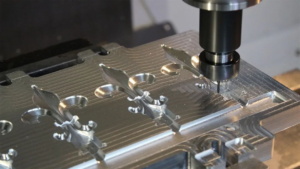
Why is the rapid mold called a rapid mold
The mold has a wide range and involves a wide range of industries. The mold can be called the mother of industrial manufacturing. It can even be said that there would be no new products without the mold. Today we will talk about the rapid steel mold within the mold range, also known as the soft mold.
Rapid steel mold itself is not the mainstream in the industrial manufacturing process. Many manufacturing professionals are not very clear about what the rapid mold is and its purpose. The industry has different names. Rapid mold, rapid soft mold, rapid steel mold, rapid aluminum mold, etc. are all its names. Although they are called differently, the needs are actually similar, that is, “seeking speed”.
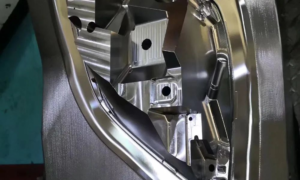
Classification of rapid molds
1.Rapid metal molds: metal molds are directly manufactured through metal 3D printing, CNC processing, etc. This type of mold has high strength and durability, and is suitable for small batch production and functional testing.
2.Rapid non-metal molds: non-metal materials such as resins and plastics are used and manufactured through 3D printing or other rapid prototyping technologies. This type of mold has a low cost and a short production cycle, and is suitable for prototype design and verification.
3.Composite molds: Combines the advantages of metal and non-metal materials and is manufactured through a variety of processes. This type of mold strikes a balance between strength and cost and is suitable for a wider range of application scenarios.
Advantages of Rapid Tooling
1.Shorten the development cycle
The manufacturing cycle of traditional molds is usually long, taking weeks or even months. The manufacturing cycle of rapid molds usually only takes days to weeks, which greatly shortens the time from design to market. This rapid response capability is particularly important in a highly competitive market environment.
2.Reduce costs
The rapid prototyping technology used by rapid molds can reduce the steps and processes of mold manufacturing, thereby reducing overall costs. Especially in the small batch production and prototype testing stages, rapid molds can effectively reduce production costs.
3.High flexibility
The manufacturing process of rapid molds is highly digitalized, and both design and modification can be done by computer. This makes mold design highly flexible and can quickly respond to design changes and optimization needs. This flexibility is particularly critical for the iterative product development process.
4.High precision and complex structure
Modern rapid prototyping technology can achieve the manufacture of high precision and complex structures to meet the needs of high-demand product development. Whether it is tiny details or complex geometries, rapid molds can be achieved through precise processes.
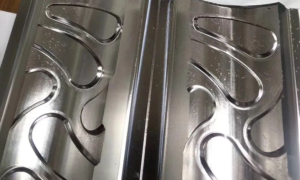
What kind of products are suitable for rapid tooling
1.Prototype products
One of the most common applications of rapid tooling is the production of prototype products. During the product development process, rapid tooling can quickly produce design prototypes, which is convenient for designers and engineers to test and verify the appearance, size, function, etc. This rapid iteration helps to discover and solve problems as early as possible, and improve the efficiency and quality of product design.
2.Small batch production
Rapid tooling is an ideal choice for products with small market demand or products in the trial production stage. Traditional mold manufacturing is costly and time-consuming, and is not suitable for small batch production. Rapid tooling has a short production cycle and relatively low cost, which can meet the needs of small batch production and respond to the market quickly.
3.Customized products
Customized products need to be designed and produced according to the specific needs of customers. The high flexibility and rapid response capabilities of rapid tooling enable it to quickly adapt to design changes and produce customized products that meet customer needs. For example, medical devices, personalized electronic products, customized home accessories, etc.
4.Complex structure products
Modern rapid prototyping technology can realize the manufacture of complex geometric structures and is suitable for the production of complex structure products. For example, mechanical parts with complex internal channels, finely decorated artworks, products with complex curved surface structures, etc. Rapid molds can realize these complex structures through high-precision processes.
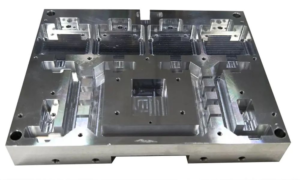
Conclusion
Rapid tooling plays an increasingly important role in modern manufacturing. It can not only significantly shorten the product development cycle and reduce costs, but also provide highly flexible design and manufacturing solutions. Whether it is a metal mold or a non-metal mold, the application of rapid prototyping technology makes mold making more efficient and convenient.
For enterprises, the use of rapid tooling technology can not only enhance the market competitiveness of products, but also respond to customer needs more quickly and achieve rapid iteration and optimization of products. In the future, with the continuous advancement of technology, rapid tooling will be applied in a wider range of fields to promote the development and innovation of the manufacturing industry.