In addition to the main application areas, CNC turning technology is also widely used in other fields. CNC turning ensures fine craftsmanship and high quality in consumer goods like jewelry and watches. In the energy sector, it processes key components such as turbine blades, valves, and pipe joints, enhancing performance and reliability. Additionally, CNC turning supports scientific research by providing precision for experimental equipment and components.
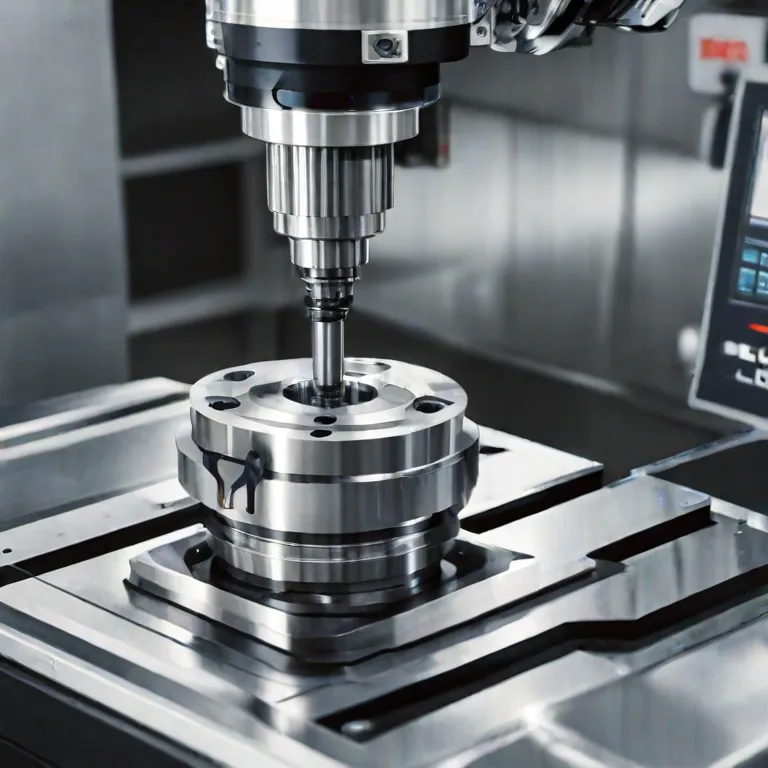
What is CNC-turning technology?
CNC turning technology is a turning processing technology based on computer control. It controls the movement of the machine tool through a computer program to achieve precision processing of metal or non-metallic materials. CNC turning machine tools usually include a rotating spindle, a movable tool holder, and a workpiece clamping device. During the processing, the workpiece is fixed on the lathe and rotated by the spindle, while the tool cuts according to the preset path, thereby realizing the processing of various shapes and sizes.
Compared with traditional turning technology, CNC turning has significant advantages. CNC turning can achieve complex processing paths and precise dimensional control through programming, reducing the errors of manual operation. CNC turning can also realize automated production, improving production efficiency and consistency. CNC turning technology is suitable for a variety of materials, including metals, plastics, composite materials, etc., and has broad application prospects.
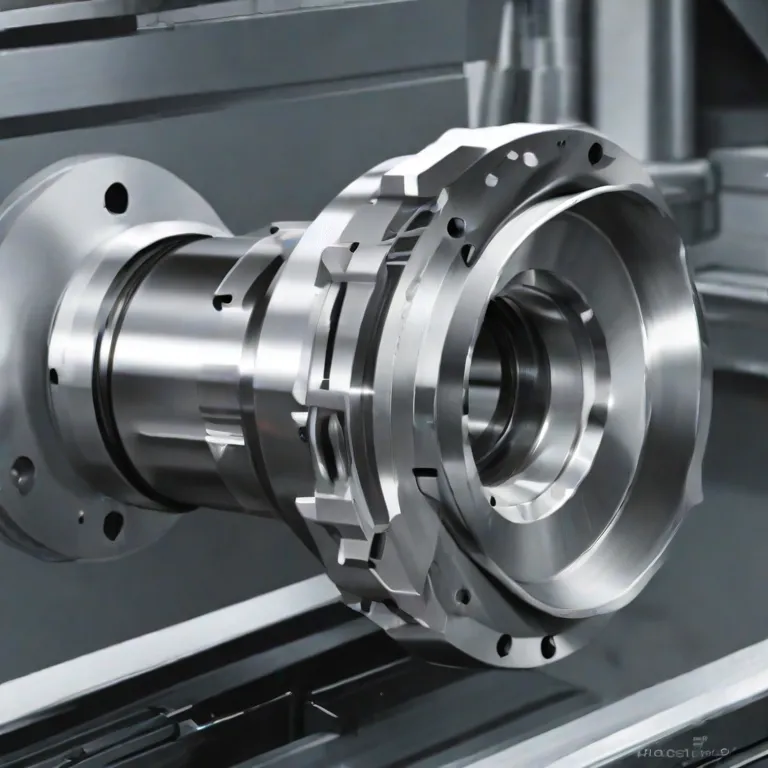
Application areas of CNC turning technology
1. Automobile industry
CNC turning technology plays a vital role in the automobile manufacturing process. The automotive industry demands high accuracy, durability, and consistency in parts, and CNC turning meets these needs through precision processing. It is used for engine parts like cylinder blocks, cylinder heads, and pistons to ensure performance and reliability; transmission components such as gears, shafts, and housings for stability; and suspension parts like control arms, brackets, and ball joints for improved handling and comfort.
2. Aerospace
CNC turning is crucial in aerospace for meeting high precision and quality standards. It processes turbine blades for aircraft engines, ensuring accuracy under high temperatures and pressure. It also manufactures fuselage parts like beams and supports, ensuring aircraft strength and stability. Additionally, CNC turning is used for spacecraft components such as satellite brackets and probe housings, meeting the harsh demands of space.
3. Medical equipment
Medical equipment manufacturing requires extremely high precision and hygiene standards, and CNC turning technology is crucial in this field. It can accurately process surgical instruments such as scalpels, tweezers, and scissors to ensure their sharpness and safety. CNC turning technology processes biocompatible parts for implants like artificial joints and dental implants, ensuring compatibility with human tissue. It also accurately processes sensors and components for diagnostic instruments, enhancing accuracy and reliability. These applications demonstrate the key role of CNC turning technology in medical equipment manufacturing.
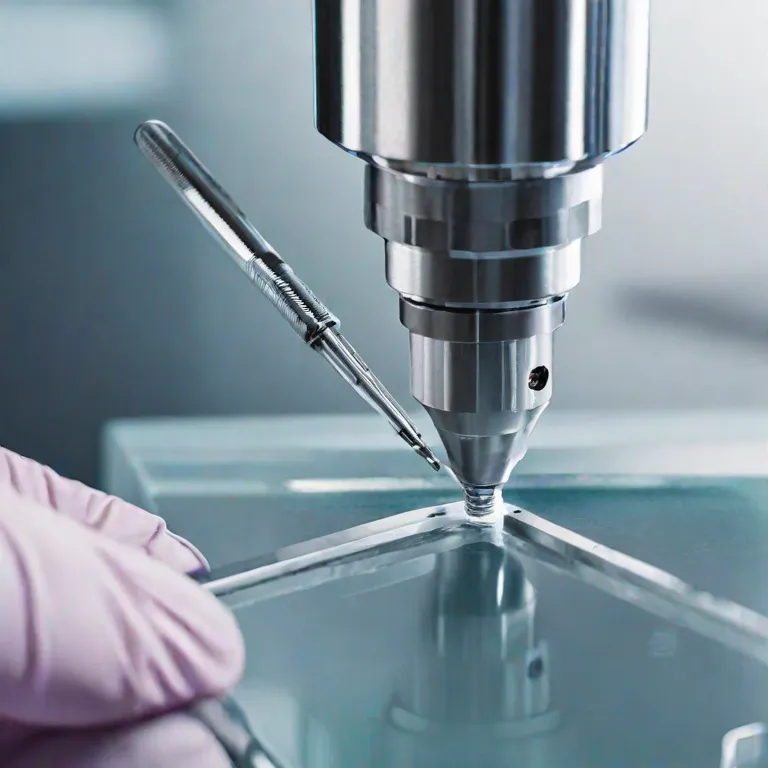
4. Mold manufacturing
Molds are key tools for producing various products, and CNC turning technology is widely used in mold manufacturing. It can accurately process complex cavities and cores to ensure that mold parts meet design requirements. CNC turning technology is widely used in injection molds, such as plastic bottles and auto parts molds, to ensure the high quality and long life of the molds. At the same time, it is also used in the manufacture of die-casting molds, which can process high-temperature and high-pressure molds, and improve production efficiency and product quality. These applications reflect the important role of CNC turning technology in mold manufacturing.
5. Electronics Industry
In the manufacture of electronic products, CNC turning technology plays an important role. It is used to precisely process electronic component housings, such as mobile phone cases and computer cases, to ensure the appearance and functionality of the product. For radiators, CNC turning can process complex heat sinks and heat pipes, thereby improving heat dissipation efficiency. The housings and internal structural parts of various electronic connectors also rely on CNC turning technology to ensure dimensional accuracy and assembly quality, ensuring the stability and performance of electronic equipment.
6. Other fields
In addition to the main application areas, CNC turning technology is also widely used in other fields. CNC turning ensures fine craftsmanship and high quality in consumer goods like jewelry and watches. In the energy industry, it processes key components such as turbine blades, valves, and pipe joints, enhancing equipment performance and reliability. It also supports scientific research by providing high-precision processing for experimental equipment.
Advantages of CNC turning technology
1. High-precision processing
CNC turning technology can achieve extremely high processing accuracy. Through computer control, the motion trajectory and cutting parameters of the machine tool can be accurately set to ensure that the dimensions of the processed parts are accurate and consistent. This high precision is particularly suitable for high-end manufacturing fields that require strict tolerance control, such as aerospace and medical equipment.
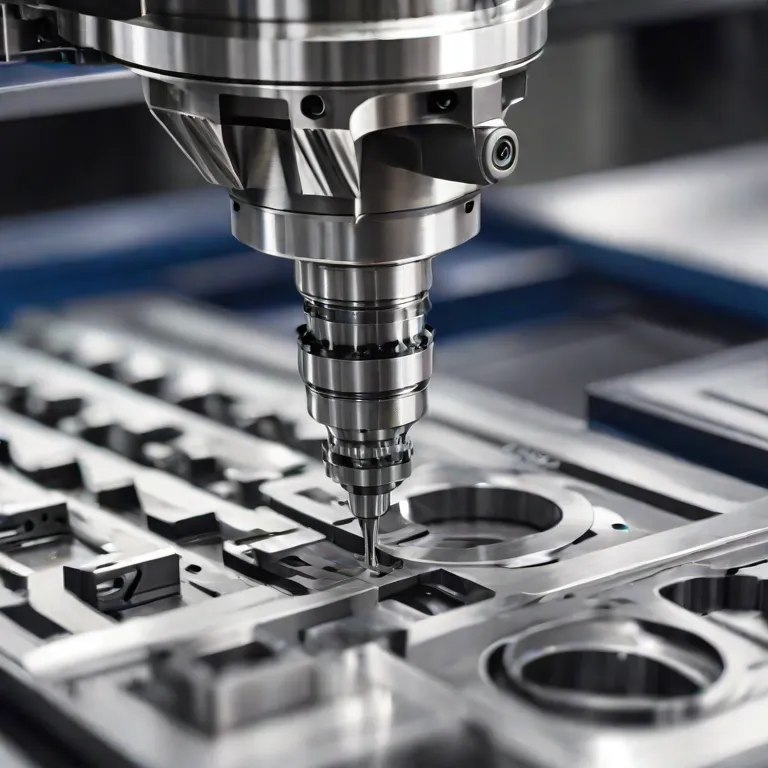
2. High production efficiency
Compared with traditional turning processes, CNC turning technology can significantly improve production efficiency. The automated processing process reduces manual operation time and can complete complex processing tasks in a short time. CNC machine tools often feature automatic tool changers, enabling quick tool swaps and boosting efficiency.
3. Consistency and reliability
CNC turning technology maintains consistency in processing quality in continuous production. Since the machine tool is controlled by a computer, the error caused by human operation is reduced, so that the processing quality of each part remains stable. This consistency is particularly important for large-scale production and demanding application scenarios.
4. Flexibility and adaptability
CNC turning technology supports a variety of processing tasks through programming. Users only need to modify the program to process different parts, greatly improving the flexibility of production. CNC turning is ideal for multi-variety, small-batch production, and fast response to market demand.

5. Complex processing capabilities
CNC turning technology is capable of complex shapes and difficult processing tasks. CNC turning, with advanced programming and control technology, can process complex shapes and fine surface textures, making it ideal for precision and complex parts.
6. Automation and reduction of human errors
The automated nature of CNC turning technology reduces dependence on operators and reduces errors caused by human operation. The automated system improves accuracy and reduces process adjustment and maintenance time, optimizing production.
7. Adaptability to a variety of materials
CNC turning technology is suitable for a variety of materials, including metals, plastics, composite materials, etc. CNC turning technology’s material adaptability meets diverse manufacturing needs, from automotive and aerospace to consumer products and medical devices.
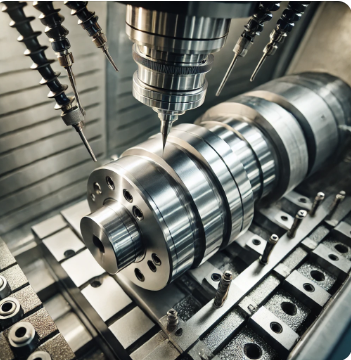
8. Cost-effectiveness
Despite the high initial cost, CNC turning machines offer long-term cost benefits through efficient production and low failure rates. Automated production reduces labor costs and scrap rates, thereby improving the economic efficiency of overall production.
Conclusion
CNC turning technology, a key driver in modern manufacturing, offers high precision, efficiency, and flexibility. From simple controls to today’s intelligent, interconnected systems, it has advanced the industry. Looking ahead, with ongoing technological evolution, CNC turning will continue to drive innovation in smart manufacturing, high-performance materials, and green manufacturing.