Additive manufacturing technology, or 3D printing, has rapidly grown and now leads advanced manufacturing. Its main advantage is the ability to quickly and freely create complex three-dimensional structures. This makes it ideal for new product development and small-lot production.
In this paper, we will explore the current equipment and applications of additive manufacturing. We will analyze both domestic and international developments and discuss future trends and key technologies. As this technology advances, it will reshape manufacturing and drive both innovation and efficiency
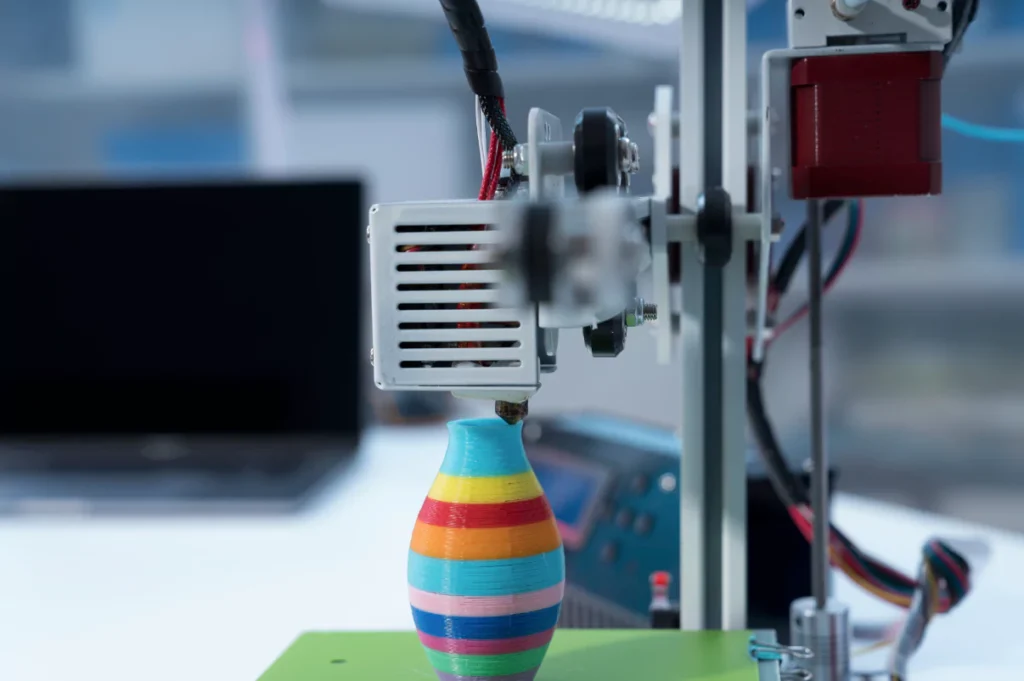
Overview
Additive Manufacturing (AM) technology manufactures solid parts based on CAD design data by adding materials layer by layer. In contrast to traditional material removal techniques (cutting), Additive Manufacturing utilizes a “bottom-up” approach. Since the late 1980s, additive manufacturing has evolved and has been referred to as “rapid prototyping,” “layered manufacturing,” “solid free manufacturing,” and “3D printing. “3D printing technology” and so on. These names reflect the characteristics of the technology from different perspectives.
1. Definition of Additive Manufacturing and 3D Printing
The International Committee F42 of ASTM defines additive manufacturing and 3D printing clearly. Additive manufacturing joins materials layer by layer to create objects from 3D CAD data. 3D printing uses print heads, nozzles, and other technologies to deposit materials and create objects. While 3D printing often refers to additive manufacturing, it specifically applies to lower-end devices.
2. How Additive Manufacturing Works
Additive manufacturing automates the accumulation of materials like liquids, powders, wires, or blocks to create solid structures from design data. This technology eliminates the need for traditional tools, fixtures, and machining processes. It can quickly and accurately produce complex parts on a single machine, overcoming past manufacturing challenges.
3. Advantages of additive manufacturing
Additive manufacturing simplifies processing and shortens cycles. Its speed advantage is especially clear for complex structures. Recently, the technology has rapidly evolved, integrating various materials and processes. Over 20 types of additive manufacturing equipment are now available. This technology is widely used in industries like consumer electronics, automotive, aerospace, and medicine.
4. Market prospects of additive manufacturing
Here’s a revised version with active voice and shorter sentences:
Additive manufacturing drives product innovation. Time magazine called it one of “the ten fastest-growing industries in the U.S.” The Economist believes it will fuel the third industrial revolution, reshaping production and life. Additive manufacturing will impact the global economy and lifestyles, enabling anyone to become a “factory.”
The Wohlers Association’s 2013 report showed that the global market for additive manufacturing equipment and services reached $2.204 billion in 2012, growing 28.6% from the previous year.
Equipment materials accounted for $1.003 billion, a 20.3% increase. Services totaled $1.2 billion, growing 36.6%. Consumer electronics and automotive sectors lead, but medical and aerospace industries are growing faster.
The U.S. holds 38% of the world’s additive manufacturing equipment, while China ranks fourth with 9%.
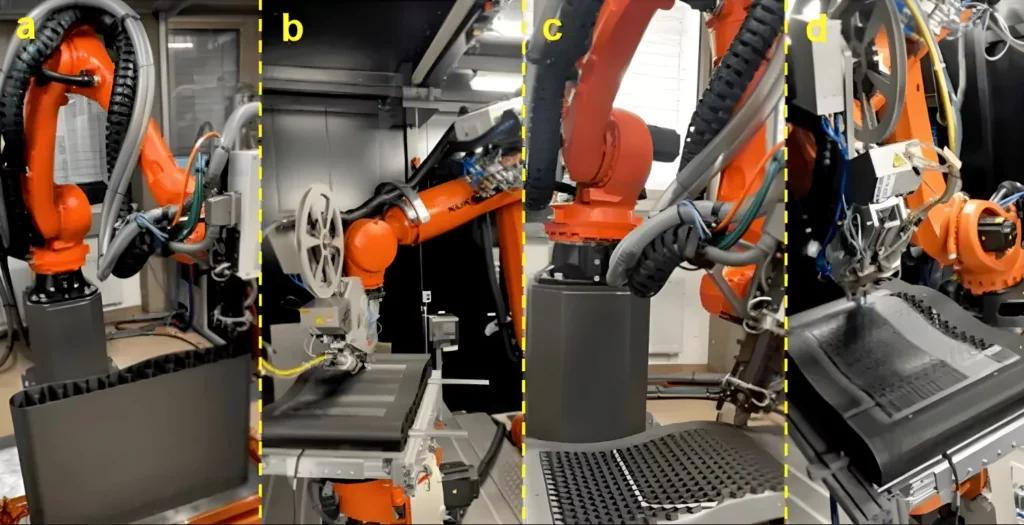
International development situation
Additive manufacturing technology has advanced significantly worldwide after over 20 years of development. The United States now leads in additive manufacturing. 3D printing is widely used in industries like food, clothing, furniture, medicine, construction, and education, creating new sectors.
Additive manufacturing equipment has evolved from a manufacturing tool to a creative tool. It allows people to design freely and fosters social development.
1. Government Support and Strategy
In 2012, former U.S. President Barack Obama proposed the “National Network for Manufacturing Innovation” (NNMI) program to revitalize manufacturing and regain leadership. He aimed to reduce product development time and costs while promoting the “designed in the United States, made in the United States” initiative. The government initially invested $30 million to support research and development of additive manufacturing technology with businesses, universities, and non-profit organizations. This effort helped establish the U.S. as the global leader in material manufacturing.
2. Additive manufacturing market dynamics
The market for additive manufacturing equipment continued to grow in 2012, with sales figures and revenues rising, further boosting stock prices. The year saw 3D printing technology come into the public eye in a variety of ways through publications, TV programs, and movies. For example, a fashion show held by Materialise in Belgium featured fashion hats and accessories made from additive manufacturing.
3. Industry Characteristics
(1) Growth of the additive manufacturing industry
The additive manufacturing industry is experiencing a wave of mergers, mainly involving equipment suppliers and service companies. For example, ZCorp. was acquired by 3D Systems and Stratasys plans to merge with Objet. Meanwhile, Delcam acquired Fabbify Software to enhance its additive manufacturing software capabilities.
(2) New materials and equipment
Objet introduced VeroClear, an ABS-like material and transparent material. 3D Systems introduced Accura CastPro for making investment casting models. Other companies such as Kelyniam Global and Optomec have also introduced new materials and print heads for medical and electronic devices.
(3) Newmarket products are emerging
New 3D printers such as the Objet260Connex and Stratasys’ Fortus250mc have emerged with smaller footprints and multi-material printing capabilities. In addition, MakerBot launched a new model, MakerBot Replicator, which can print larger volume models, attracting more consumers.
(4) Development of new standards
In 2011, the American Society for Testing and Materials (ASTM) released a specialized Additive Manufacturing File (AMF) format that supports more information on materials and functions. This initiative will reduce duplication of effort in the industry and drive the standardization process.
Additive manufacturing technology is rapidly changing the traditional way of production and life, becoming an important strategic direction for the global manufacturing industry. As technology continues to advance and new materials, equipment, and markets emerge, additive manufacturing will play an even more critical role in the future of manufacturing.
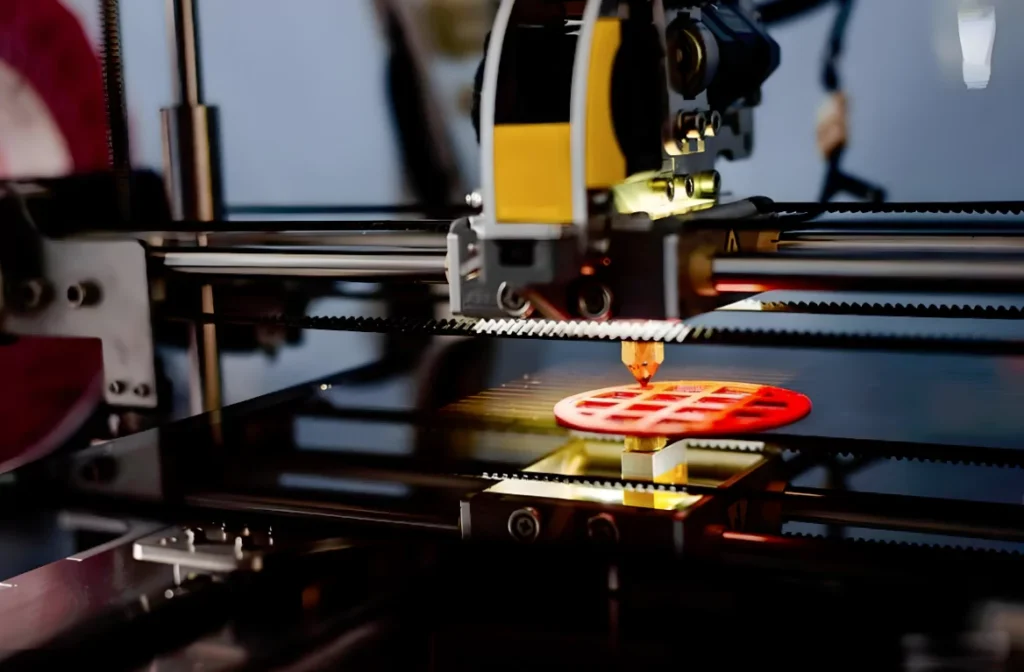
Development of additive manufacturing technology in China
China has made significant progress in additive manufacturing since the 1990s, with strong backing from the Ministry of Science and Technology (MOST) and other government agencies.
Xi’an Jiaotong University (XJTU), Huazhong University of Science and Technology (HUST), Tsinghua University (TWU), and Beijing Longyuan Corporation (LYC) have led key research and industrialization efforts in forming equipment, software, and materials.
More universities and research institutes, such as Northwestern Polytechnical University, Beijing University of Aeronautics and Astronautics, and South China University of Technology, have joined to advance research and applications.
1. Progress of Industrialization
By 2000, China had initially realized the industrialization of additive manufacturing equipment, and the product level was close to international standards, breaking the early dependence on imports.
With national and local support, more than 20 service centers have been established across the country, and additive manufacturing equipment is widely used in industries such as medical, aerospace, automotive, military, mold, and electronic appliances. These efforts have significantly boosted the development of manufacturing technology in China.
2. Market Status and Challenges
Although the Chinese additive manufacturing market has developed slowly over the past five years, focusing mainly on industrial applications, the consumer goods sector has yet to form a fast-growing market. In addition, insufficient investment in R&D has caused China to lag behind the United States and Europe in terms of industrialized technology development and application.
3. International Comparison and Advantage
In the United States, additive manufacturing technology has developed rapidly in recent years, mainly due to the popularization of low-cost 3D printing equipment and the application of direct manufacturing technology for metal parts.
China has also achieved international leading research results in metal parts direct manufacturing technology, such as Beijing University of Aeronautics and Astronautics and Northwestern Polytechnical University to manufacture large-size metal parts, successfully applied to the development of new aircraft, significantly improving the efficiency of research and development.
4. Status of technology research and development
Although the technical level of some of China’s additive manufacturing equipment has been comparable to the international advanced level, there are still gaps in key components, materials, intelligent control, and application scope. China’s additive manufacturing is mainly used for modeling, and there is still much room for improvement in the direct manufacturing of high-performance end parts.
(1) Basic research
In terms of the basic theory of additive manufacturing and forming micro-mechanisms, China has carried out some research, but foreign research is more systematic and in-depth.
(2) Technology
Foreign additive manufacturing process technology is controlled based on theoretical foundations, while China’s R&D relies more on experience and experimental verification, resulting in the overall process level lagging behind.
(3) Material research
There is a big gap between China and foreign countries in the basic research of materials, preparation process, and industrialization, and most of the core components rely on imports.
China’s additive manufacturing technology is at a critical stage of rapid development. Despite the many challenges, by strengthening basic research, improving process level, and expanding application areas, China has the potential to occupy a more important position in the global additive manufacturing market.
Additive manufacturing technology development trend
1. Difficulties and challenges
Additive manufacturing technology changes the modern production model. Future production will shift from mass manufacturing to customization, meeting society’s diverse needs.
In 2012, the direct value of additive manufacturing was about 2.2 billion dollars, just 0.02% of the global manufacturing market. However, its potential impact and prospects are vast.
Additive manufacturing offers several advantages, including shorter production cycles, personalization for single-piece needs, and the ability to create complex parts in aerospace and medical fields.
Despite its benefits, additive manufacturing faces challenges compared to traditional methods. Currently, it is costly ($10 to $100 per gram), inefficient (e.g., gold is formed at a rate of 100 to 3,000 grams per hour), and lacks accuracy.
Additionally, research and development in related processes and equipment are insufficient. Additive manufacturing has not yet entered large-scale industrial use and remains a supplement to traditional high-volume methods.
To promote its growth, we need to strengthen R&D, nurture industries, and expand applications. By fostering collaboration and driving technological development, we can transform additive manufacturing from a product development tool into a mass production model, advancing market growth and improving lives.
2. Development trend of additive manufacturing technology
(1) To the development of daily consumer goods manufacturing
3D printing has become an international development hotspot in recent years. 3D printers can output three-dimensional graphics in the computer directly into three-dimensional color objects, which are widely used in the fields of science education, industrial design, and arts and crafts. The future direction of development includes improving precision, reducing costs, and developing high-performance materials.
(2) To the functional parts manufacturing development
Additive manufacturing using laser or electronic east directly melting metal powder, layer by layer buildup to form metal parts. This technology can directly manufacture complex structures of metal parts, and its mechanical properties can be beautiful forgings. Future developments will focus on improving precision and performance, and explore ceramics. Additive manufacturing technology for composite materials.
(3) to the development of intelligent equipment
The current additive manufacturing equipment still needs to be optimized in terms of software functions and post-processing. For example, support is needed in the forming process, and the intelligence and automation level of the software urgently needs to be improved:
The matching of process parameters and materials in the manufacturing process needs to be intelligent; problems such as the removal of powder or support after the completion of processing also need to be solved. These factors directly affect the promotion of equipment, equipment intelligence is the key to the popularization of additive manufacturing.
(4) To the organization and structure of the integrated manufacturing development
Future additive manufacturing will achieve controlled manufacturing from micro-organization to macro-structure. In the case of composite materials, for example, design and manufacturing will be synchronized so as to achieve overall manufacturing on a micro-to-macro scale. This advancement will support the fabrication of biological tissues and complex structural parts, driving a revolution in manufacturing technology.
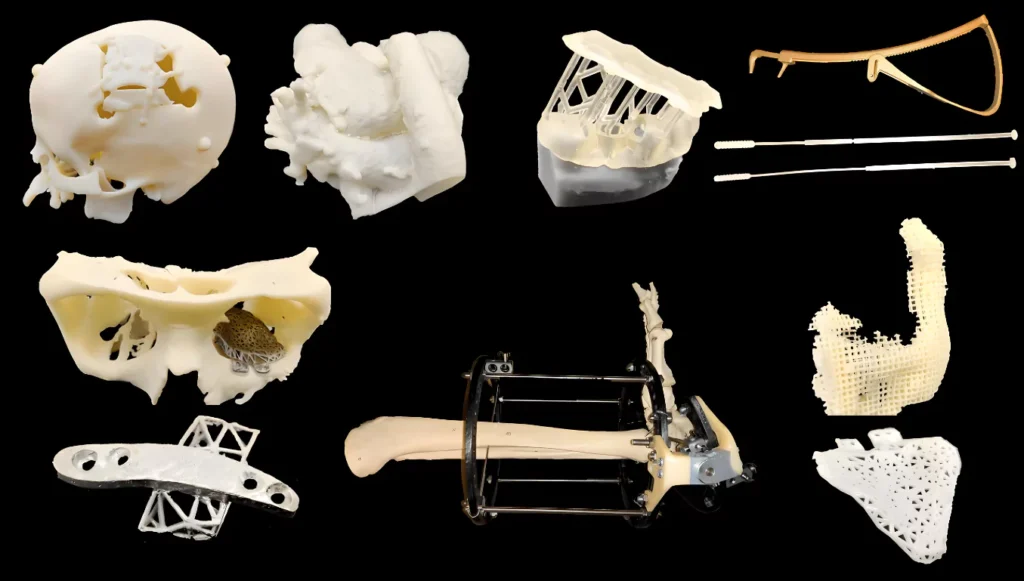
Conclusion
Additive manufacturing shows great potential for development with its unique manufacturing principles. As the range of material applications expands and manufacturing precision improves, additive manufacturing technology will revolutionize the manufacturing industry.
Vivek Wadhwa, vice president of Singularity University, wrote in the Washington Post that new technologies could lead to China’s decline over the next 20 years, similar to the U.S. experience. He believes digital manufacturing, especially 3D printing, will drive this shift.
Wadhwa pointed out that while 3D printing currently produces basic objects, rapid advancements in equipment, falling costs, and growing capabilities will enable precise molecular-level production by the mid-2020s. He questioned how China could compete in this new landscape. His message underscores the importance of innovation and progress to stay ahead in future competition.