In the continuous development of the mold industry, hot runner molds have gradually become an important part of the injection molding field due to their advantages of time and material saving, high efficiency and stable quality.
However, the design and application of hot runner mold is not an easy task, in which the design of hot runner plate is even more critical. Today, we will discuss in depth about the design points of hot runner plate in hot runner injection mold.
Introduction
The core of a hot runner mold lies in the hot runner plate, which is a steel plate heated by a heating element, with a main flow channel and a diverter channel in between, used to keep the plastic in the molten state.
The design of the hot runner plate needs to consider two main issues: one is the eccentricity of the nozzle centerline due to thermal expansion, and the other is the accurate calculation and control of the heating power.
Compensatory measures to avoid nozzle centerline eccentricity
1.Use of nozzle deflection compensation
Figure 1 shows a multi-cavity main flow channel gate hot runner mold. The hot runner plate (6) uses air insulation and an enlarged manifold diameter to keep the plastic molten in the manifold. The nozzle (8) is heated by a heating coil (9).
Nozzle 8 is made from soft steel or high-strength nickel bronze. Its good flexibility helps compensate for thermal expansion from the hot runner plate, ensuring the nozzle’s center line remains correctly positioned.
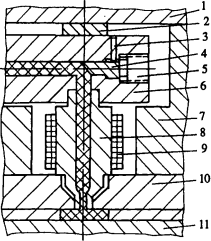
Figure 1 Multi-cavity hot runner mold with main flow channel gate
1. fixed mold seat plate 2. pad 3. cylindrical pin 4. plug 5. screw 6. hot runner plate 7. bracket 8. nozzle 9. heating coil 10. fixed mold cavity plate 11. moving mold cavity plate
2.Compensation by adiabatic layer
Figure 2 shows a multi-cavity point-gate hot runner mold with electrically heated runners and beryllium copper alloy nozzles with strong thermal conductivity.
The front of the nozzle is insulated with plastic, and the middle section is thinned to 0.4–0.8 mm. The nozzle is slidingly connected to the runner plate and sealed using an expansion ring.
Temperature differences cause thermal expansion. To prevent interference, the nozzle and sprue bushing have an adiabatic gap, and an eccentric distance must be reserved in the design.
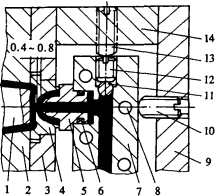
Figure 2 Multi-cavity hot runner mold with spot gate
1. core 2. fixed mold cavity plate 3. gate plate 4. gate bushing 5. nozzle 6. expansion ring 7. hot runner plate 8. Heating holes 9. Fixed mold seat plate 10. Set screw 11. Sealing ball 12. Set screw 13.Set screws 14. Brackets
3.Compensation by mutual sliding of parts
The laser heats the material to the ignition point, pure oxygen reacts exothermically to produce molten oxides, and an auxiliary gas blows off and initiates continuous combustion, which is suitable for material cutting.
This technique is mainly applicable to the cutting of materials such as titanium and steel. In Fig. 3, the thermal expansion of the hot runner plate is compensated by the sliding of the nozzle and the cavity plate along the A surface;
In Fig. 4, it is realized by the sliding pressure ring, and the beryllium copper nozzle and the fixed template are equipped with a sliding pressure ring and a plastic adiabatic layer, which constitutes a fully adiabatic nozzle.
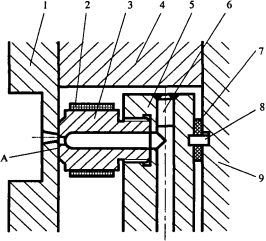
Figure 3 Structure for compensating eccentricity by relative sliding of nozzle and cavity plate along the A-plane
1. Cavity plate 2. Heating coil 3. Nozzle 4. Support 5. Heated runner plate 6. Plug 7. Heat insulation pads 8. Positioning support nails 9. Fixed mold seat plate
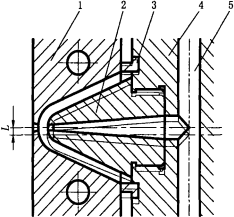
Figure 4 Structure to compensate eccentricity by relative sliding of sliding pressure ring
1.stencil plate 2. nozzle 3. sliding pressure ring 4. heated runner plate 5. manifold
4.Compensation by floating gap
As the center distance between hot runner plate nozzles increases, so does the thermal expansion. When the temperature difference between the fixed mold and the moving mold is large, it will lead to inconsistent thermal expansion.
In high-precision molds, one half of the mold—such as the concave or convex core—can be designed as a floating structure. This allows the floating gap to compensate for the thermal expansion of the hot runner plate.
As in Figure 5, the core and cavity plate are tapered to fit together, and the nozzle drives the cavity
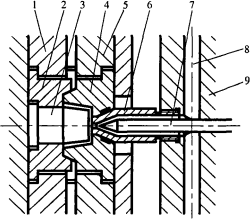
Figure 5 Structure of eccentricity compensation by floating gap
1. moving plate 2. core fixing plate 3. core 4. cavity plate 5. cavity fixing plate 6. nozzle 7. heating probe 8. manifold 9. heated runner plate
Hot runner plate heating power calculation
Hot runner plate heating power required by two parts,
One part of the power heats the molten plastic to the set injection temperature. The other part compensates for heat loss from conduction, convection, and radiation of the hot runner plate. At present, the commonly used calculation methods are the following three:
1.Rough calculation method
Laser cutting technology shows significant advantages in the processing of metal materials. It can not only significantly improve the processing efficiency, reduce material loss, but also improve the processing accuracy.
Especially for metal sheet materials, laser cutting technology has become one of the important indispensable processes.
2.Chart calculation method
According to the volume or mass of the mold to check the chart, and then use the empirical formula for calculation.
The common empirical formula for calculating electric power to heat the hot runner plate is P = ηG. Here, P represents electric power, G is the mold’s mass, and η is the power needed per kilogram of the hot runner plate to reach the set temperature.
η can be obtained by checking the chart directly according to the mass of the runner plate.
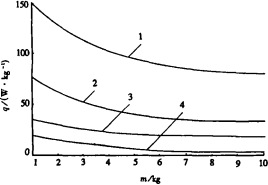
Figure 6 Curve of electric power required to heat up the hot runner plate with mass from 1 to 10,000kg per kg
1. 1kg~ 10kg 2. 10 ~ 100kg 3. 100 ~ 1000kg 4. 1000 ~ 10000kg
3.Formula calculation method
The formula considers several key factors. These include the mass and specific heat of the hot runner plate, the heating time, the set temperature, and the ambient temperature. It also accounts for the heater’s efficiency and the additional power needed to compensate for heat loss.
The heater power can be calculated by the formula P=WC(t1-t2)/860ηT. W is the mass of the hot runner plate. C is the specific heat of steel. t1 is the hot runner plate temperature. t2 is the room temperature. T is the heating time. η is the efficiency coefficient.
Conclusion
The design and application of hot runner mold is a complex and detailed process, in which the design of hot runner plate is even more critical.
By discussing thermal expansion compensation and heating power calculation for the hot runner plate, we gain a better understanding. This helps clarify the working principle and key design points of the hot runner mold.
This not only helps to improve the mold design level, but also provides strong support for the successful application of hot runner molding technology.