Statistics show that at least half of China’s 29 manufacturing industries need deep-hole machining technology and equipment. Over one-third of these industries have urgent needs. However, the lack of advanced technology and cost-effective equipment is a bottleneck for China’s equipment manufacturing industry.
In mechanical manufacturing, hole machining is divided into shallow and deep hole machining. Shallow-hole machining has a length-to-diameter (L/D) ratio of less than 5, while deep-hole machining has an L/D greater than 50. Holes with an L/D over 100 are called ultra-deep holes. Deep-hole machining, a key branch of machining, has become a major research focus. Scholars worldwide have studied its dynamic theory and ways to improve efficiency and accuracy.
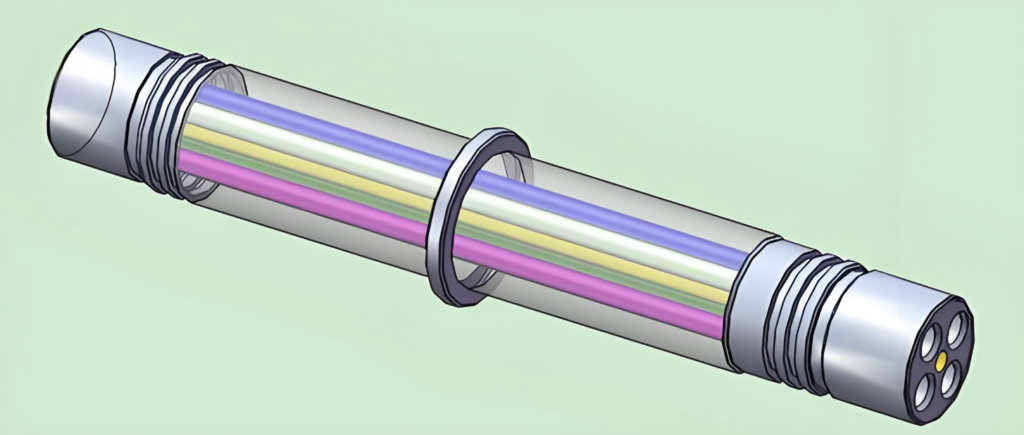
This paper outlines the current development of deep hole machining technology, covering drill pipe behavior, machining processes, and drilling monitoring. It also discusses the progress of deep-hole machining machines, analyzes existing technical challenges, and presents future development trends.
Development status of deep hole machining technology
Deep hole machining technology originated in the military industry for processing gun barrels and tubes. As technology advanced, deep hole machining evolved with new methods, including gun drilling, BTA drilling, spray suction drilling, and DF drilling systems.
1. Main systems sole machining technology
- Gun drilling: It is mainly used for the processing of small diameter holes, suitable for Φ2~Φ30mm holes. It is the most common deep hole drilling method, widely used in small and medium-sized mass production.
- BTA Drilling: BT A drilling is ideal for deep hole machining with diameters over 12mm. It suits mass production and offers high load capacity and continuous operation.
- Jet Suction Drilling: Jet suction drilling efficiently machines deep holes but is suitable for holes with diameters of 18mm or more.
- DF Drilling System: The DF drilling system combines the benefits of BTA and jet suction drilling. It can machine larger holes, starting from Φ6mm, improving accuracy and efficiency.
Table 1 Comparison table of 4 main deep hole machining technologies
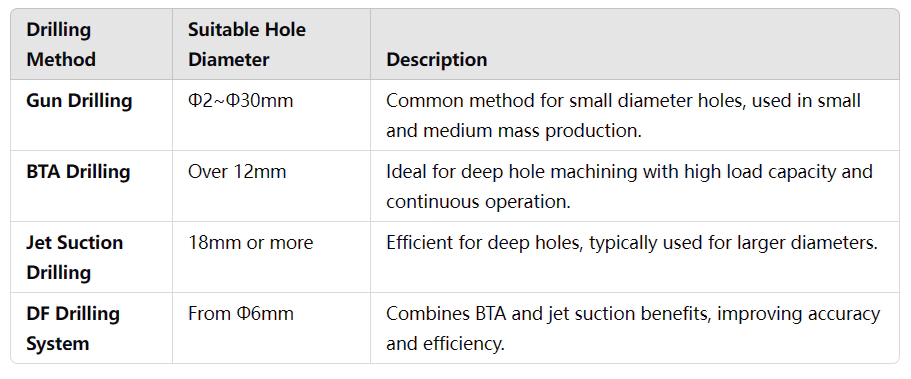
2. Research Direction of Deep Hole Machining
The development of deep-hole machining technology has been studied by a large number of scholars in the past decades. The main research directions include the mechanical behavior of drill pipe, deep hole machining process, and monitoring of the drilling process.
(1) Mechanical behavior of drill pipe
The force on the drill pipe during deep hole drilling significantly affects processing quality. Research shows that drill pipe behavior closely relates to machining accuracy. Bai Wanmin and colleagues proposed a mechanical model for dee deep-hole filling. They studied the force on the drill lance and suggested using both measurement and calculation to analyze cutting force.
In recent years, drill pipe dynamic behavior has become a research focus, especially the vortex issue during rotation. Studies indicate that vortexing is often caused by self-excited vibration, affecting drilling accuracy and stability.
For example, Hu Zhanqi and colleagues analyzed vortex formation in rotating drill pipes. They studied how cutting fluid impacts vortex behavior and identified self-excited vibration as the main cause of instability.
(2) Deep hole machining process research
Process innovation in deep-hole machining is essential for improving efficiency and quality. In the 1980s, Wang Jun from North Central University invented the single-tube internal chip evacuation spray suction drill (SIED). This technology solved the issue of processing small-diameter holes and improved cutting performance.
Xi’an Petroleum University developed the multi-tooth folding edge deep hole drill, improving cutting force and centering. These enhancements stabilize the drilling process.
Additionally, deep-hole machining technology has addressed chip breakage in deep holes using vibratory cutting. Prof. Wanfu Xue’s vibratory deep hole machining equipment has increased efficiency and reduced chip breakage risk.
(3) Deep hole drilling monitoring technology
Due to the large aspect ratio of deep holes, deep-hole machining usually occurs in a closed or semi-closed state. This makes it difficult to directly observe the tool’s condition and monitor the drilling process in real time, leading to extensive research on this issue.
For example, researchers at Xi’an University of Technology monitored tool wear by analyzing vibration signals using orthogonal wavelet transform. Beijing University of Technology used fuzzy pattern recognition with acoustic emission signals to identify tool wear online.
Some advanced equipment, like Japan’s Machida Iron Works automatic drilling machine, features a torque detection system. This system protects the drill by stopping the feeding mechanism when the drill experiences excessive torque.
3. Development of international deep-hole machining technology
Deep-hole machining technology has advanced significantly worldwide. ATI Stellram (USA) develops tools for difficult-to-machine materials, leading in tool materials.
Sandvik (Sweden) has serialized BTA deep hole drills and introduced drills for various machining needs. They also excel in vibration-damping tools.
BOTEK (Germany) has standardized gun drill specifications from Φ0.9 to Φ50mm, offering more options for global deep-hole machining.
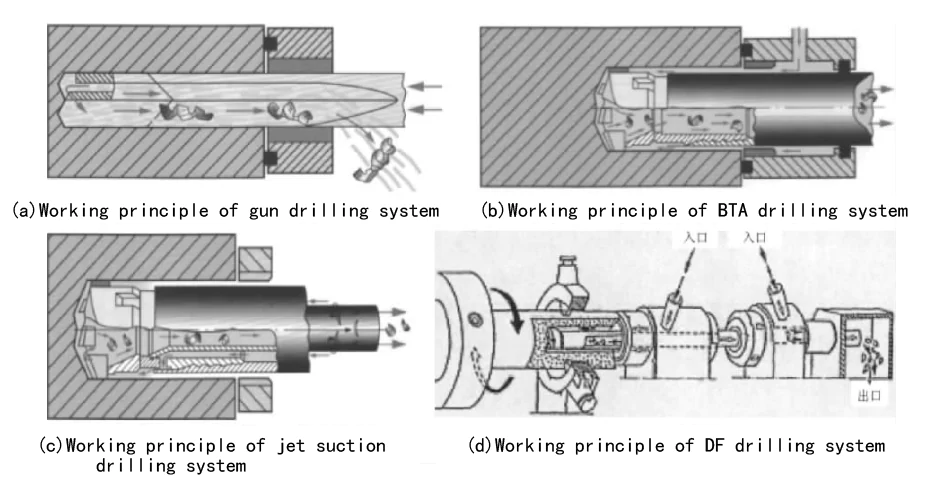
Fig. 1 Schematic diagram of deep hole machining system
4. Current Challenges and Future Trends
Although deep-hole machining technology has advanced, challenges remain in microfine and ultra-long deep-hole machining. Drilling ultra-long, microfine holes with diameters under 1mm and L/D ratios over 200 lacks a mature machining system.
Future deep-hole technology will focus on improving efficiency and precision. With advancements in automation and intelligence, monitoring and regulating deep-hole machining will become more accurate. New tool materials, optimized chip removal, and advanced equipment will increase the importance of deep-hole machining in various industries.
Development status of deep hole machining machine tools
Deep-hole machining is essential in precision manufacturing. However, the high costs and maintenance of deep-hole machining tools discourage many companies. Most companies lack dedicated deep-hole machining equipment, often modifying standard machines to meet basic needs.
For example, Zhang Yong and his team at Soochow University converted ordinary lathes into deep-hole machines. They used PLC and AC frequency conversion technology to control the machines, reducing costs while improving machining efficiency and precision.
Despite these improvements, modified standard machines still struggle to meet high precision requirements. To achieve better precision, specialized deep-hole machining tools are entering the market. These include horizontal and vertical deep-hole drilling machines, deep-hole gun drills, and deep-hole honing machines.
1. Common types of deep hole drilling machine
A deep hole drilling machine is the most widely used deep hole machining equipment. There are three main types:
- Common single-coordinate deep hole drilling machine: this kind of machine is the most basic, usually used for simple deep hole drilling.
- Specialized deep-hole drilling machines: These machines are designed for specific needs and offer higher machining accuracy.
- Multi-coordinate CNC is deep-hole drilling machines: these machines are more advanced and capable of accomplishing complex deep-hole machining tasks with a high level of automation.
Table 2 Types of common deep hole drilling machines and their characteristics
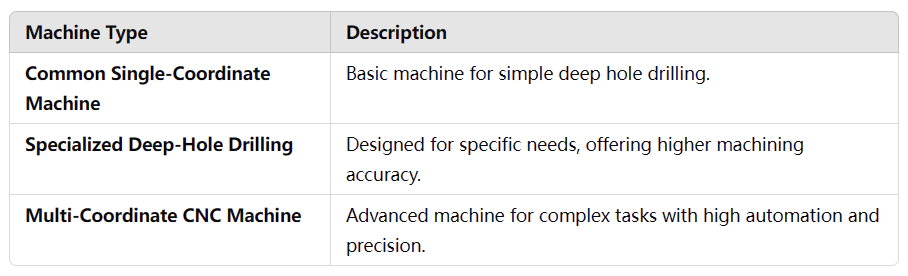
In 1989, Shandong Delong Machine Tool Company designed and manufactured the Z2102 single-coordinate deep hole drilling machine. It processes holes with diameters ranging from Φ3 to Φ20 mm and a maximum depth of 1,000 mm. This was China’s first single-coordinate deep-hole drilling machine using the gun drilling process.
In 2002, the Shanghai Machine Tool Research Institute developed a specialized deep-hole drilling machine for small diameters. It successfully met the domestic industry’s needs for small-diameter deep-hole processing. The demand of the domestic industry for small-hole diameter deep-hole machining has been successfully met.
2. Development of international deep-hole machining machine tools
Foreigneep-hole machining machines have developed much faster than domestic models, especially in advanced manufacturing countries. These countries offer not only three-axis deep hole drilling machines but also four-axis, five-axis, and even six-axis fully automatic CNC gun drilling centers. Such equipment often features an automatic tool-changing system, enabling complex processes like drilling, milling, and tapping. Some machines also include the internal chip drilling (BTA method) function, which broadens their application.
While China has similar equipment, there is still a gap in precision, stability, and specification variety compared to international standards. For example, Germany’s five-axis CNC deep hole drilling and milling center leads the world in design accuracy and machining efficiency.
3. Reconfigurable deep hole machining machine tool research
To improve the flexibility and adaptability of deep-hole machining machines, scholars introduced reconfigurable machine tools. The University of Michigan started research on reconfigurable manufacturing systems in 1996. Meanwhile, the University of Stuttgart in Germany advanced modular machine tools, standardized interfaces, and integrated functional modules.
In China, Prof. Wu Fujia and his team at North Central University are studying reconfigurable deep-hole machine tools. They verified the machine’s feasibility through kinematic model analysis and by dividing the machine structure and functional modules. This machine adjusts its functions as needed and reduces redundant functions and conversion costs.
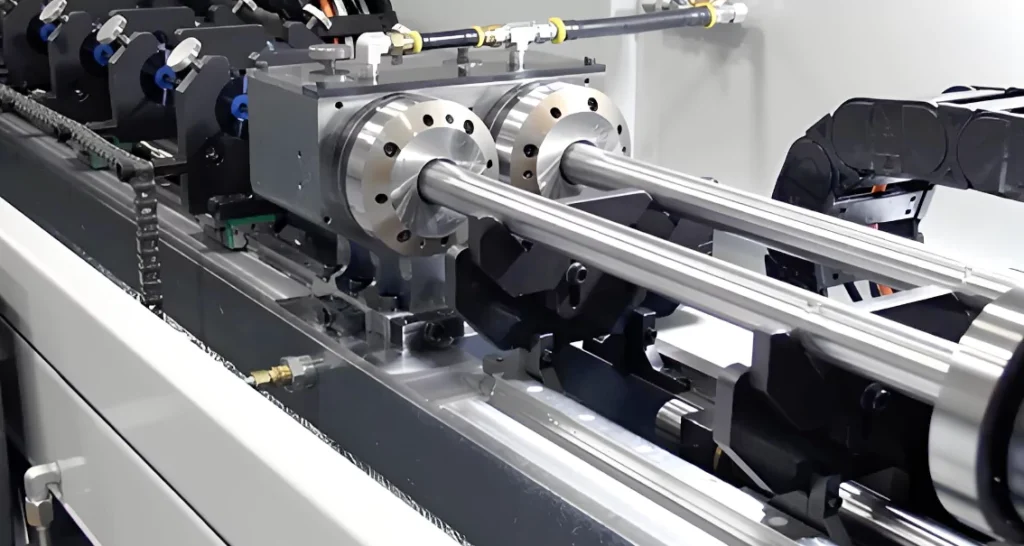
Fig. 2 Reconfigurable deep hole machining machine tool
4. Design and Optimization of Deep Hole Machining Machines
The design and improvement of machine tools are critical to the accuracy and efficiency of deep-hole machining. In recent years, dynamic and static optimization of key components of machine tools, especially lightweight design, has become an important direction to improve machining performance. For example, Wu et al. conducted a modal analysis for the M2120A model internal grinder and proposed measures to improve the bed structure, which enhanced the dynamic performance of the machine tool. Similarly, Li Bin identified the weak points and optimized the sliding saddle of a horizontal machining center through dynamic analysis.
5. Development trend of deep hole machining technology
Although the BTA (internal chip drilling) method hasn’t changed much since its introduction, optimizations have been made. For example, cutting tool development, optimized guide block arrangements, and negative pressure chip removal devices have improved precision and efficiency. Quasi-dry and dry deep-hole machining technologies, based on the green machining concept, are gaining more attention.
Modern deep-hole machining machines are evolving rapidly in efficiency, precision, intelligence, and modularization. Modular reconfigurable machines have seen significant research progress in recent years. However, challenges remain, especially in machining difficult materials and complex profiles. Traditional methods have limitations in these areas. As a result, special technologies like laser machining, water jetting, EDM, and electrolytic deep-hole machining are opening new development areas.
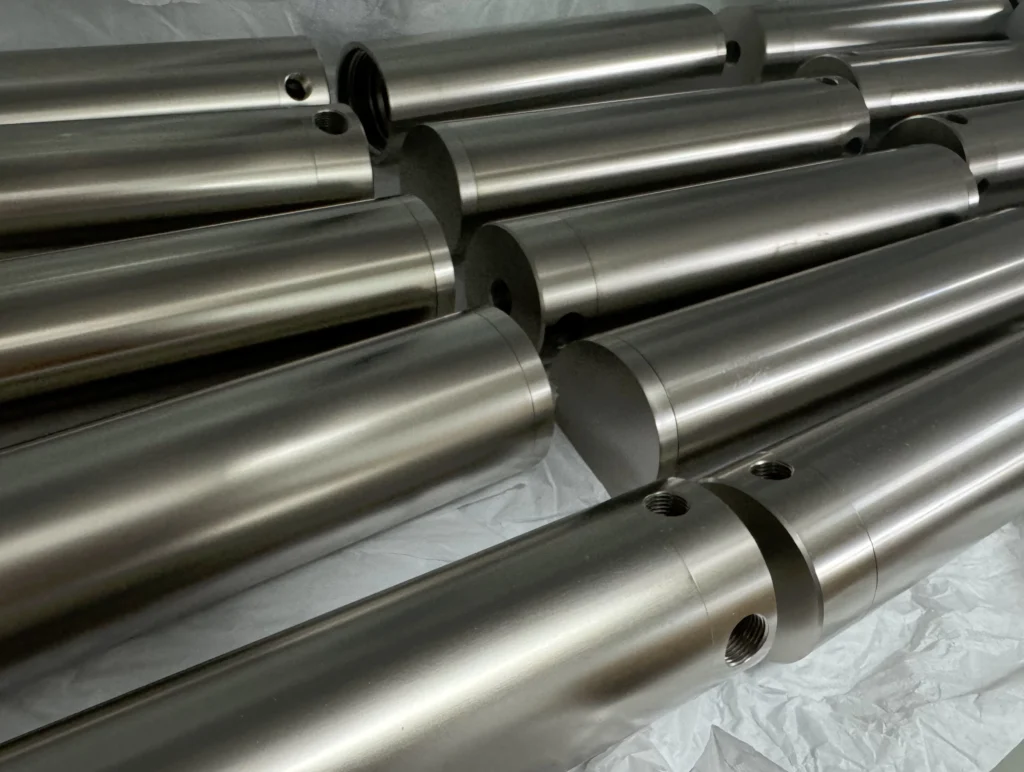
Fig. 3 Deep hole machining products
Summary
The continuous development of deep-hole machining tools and technology is driving the manufacturing industry toward higher precision and efficiency. Although there is a gap between domestic and international deep-hole machining, technological advancements, especially reconfigurable machine tools, will enhance flexibility and adaptability. In the future, deep-hole machining combined with green machining technology will become a key trend in the industry.