In today’s manufacturing industry, CNC machining and 3D printing are two major manufacturing technologies, each showing unique advantages and limitations. CNC machining is widely used in traditional manufacturing due to its high precision and material diversity, while 3D printing has gradually attracted attention for its design freedom and rapid prototyping capabilities. When facing different manufacturing needs and application scenarios, it becomes particularly important to choose the right manufacturing technology.
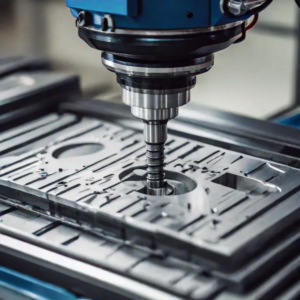
CNC machining
CNC machining (computer numerical control machining) is a method of material processing by computer-controlled machine tools. It is characterized by high-precision and high-quality parts manufacturing.
CNC machining can be applied to a variety of materials, including metals, plastics, etc., and is suitable for the production of complex components and precision parts.
1. Advantages
· High precision and high surface quality: CNC machining provides micron-level accuracy, ideal for precise parts and high-quality surfaces.
· Material diversity: CNC machining is suitable for a variety of materials, including metals, plastics, composite materials, etc. Its wide adaptability to materials makes it widely used in different application fields.
· Mass production capacity: CNC machining is ideal for mass production, delivering high consistency and large quantities of parts quickly.
· Mature processing technology: After years of development, CNC processing technology has matured, ensuring product quality and production efficiency.
2. Disadvantages
· Complex programming and setup: CNC machining requires professional programming and setup, which can take time for complex parts.
· Material waste: CNC machining generates significant material waste, especially when processing high-cost materials.
· Limitations of complex geometries: CNC machining has limitations for complex internal geometries or shapes that conventional tools cannot machine.
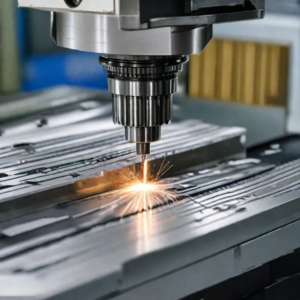
3D printing
3D printing (three-dimensional printing) is a manufacturing method that creates three-dimensional objects by stacking materials layer by layer. It is characterized by rapid prototyping, customization, and the realization of complex structures. 3D printing applies to a variety of industries, including medical, aerospace, automotive, etc.
1. Advantages
· High design freedom: 3D printing enables complex shapes and internal structures that traditional methods can’t, allowing designers to fully unleash their creativity.
· Reduce material waste: 3D printing is an additive manufacturing technology that forms parts by stacking materials layer by layer, with high material utilization and less waste.
· Rapid prototyping: 3D printing can quickly convert digital models into physical prototypes, greatly shortening the product development cycle, and is suitable for concept verification and design iteration.
· Adapt to small batch production: 3D printing does not require molds or special tooling, is particularly suitable for small batch and customized production, and can flexibly respond to changes in market demand.
2. Disadvantages
· Material performance limitations: Although the variety of 3D printing materials is increasing, in some applications with high strength or special performance requirements, 3D printing materials may not meet the needs.
· Poor surface quality: Compared with CNC machining, 3D printing has lower surface quality and accuracy, and additional post-processing steps may be required to achieve the required surface finish.
· Printing speed limitation: For large-sized or high-precision parts, 3D printing has a slow production speed and is not suitable for mass production.
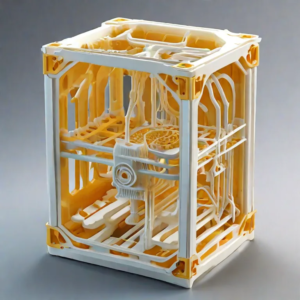
Which process to choose?
3D printing is an ideal choice in the early stages of product development, especially when rapid prototyping, testing design concepts, and customized production are required. 3D printing can quickly create samples, allowing design iteration and verification. In addition, when the product has a complex structure, internal space, and personalized needs, 3D printing can better meet these requirements.
However, in cases where high-precision, high-quality parts, and large-scale production are required, CNC machining is still a more suitable choice. CNC machining can provide higher precision and surface quality and is suitable for producing a large number of parts with the same specifications.
In general, CNC machining and 3D printing each have their applicable fields and advantages. At different stages of product development and production, choosing the right processing method according to needs will help achieve more cost-effective manufacturing.
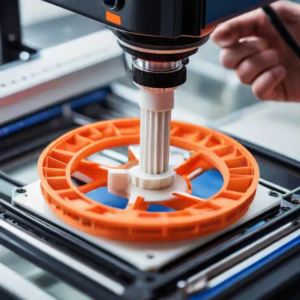
Conclusion
CNC machining and 3D printing are key technologies in modern manufacturing, each with unique advantages. CNC machining offers high precision, stable production, and material versatility, making it ideal for large-scale and complex parts production. In contrast, 3D printing excels in innovative product development, rapid prototyping, and small-batch customization due to its design flexibility.
When choosing a manufacturing technology, companies must consider factors like product design, production volume, time efficiency, and cost. Proper use of these technologies can enhance competitiveness, create market opportunities, and drive flexible, efficient, and innovative industry growth.