The shift from traditional three-axis to widely used multi-axis CNC processing technology has expanded machining possibilities. The introduction of multi-axis, especially five-axis, CNC machines has made complex shapes and curved surface processing more achievable. However, this advancement brings both advantages and challenges.
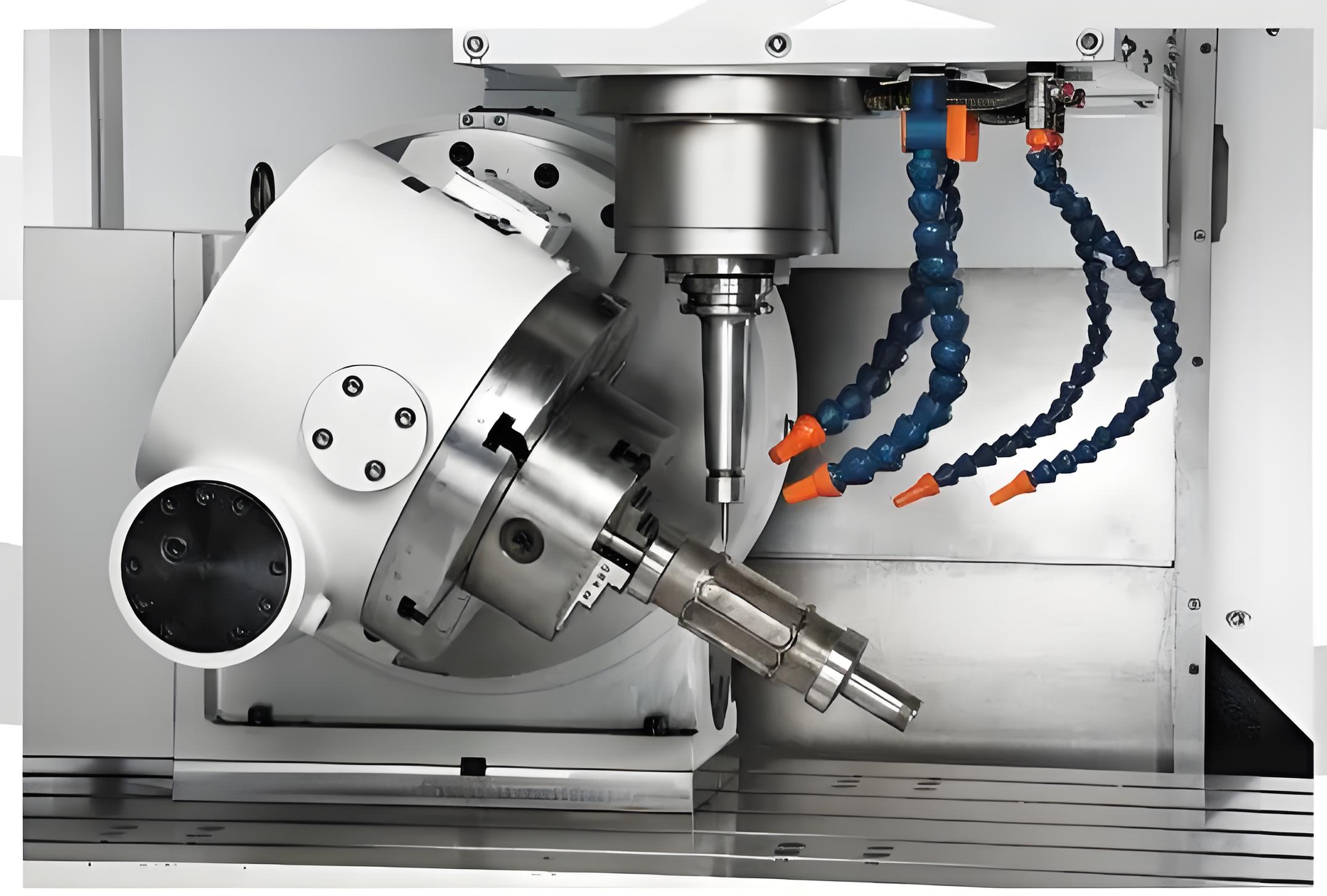
The basic concept of multi-axis CNC processing
In traditional three-axis CNC processing, the tool moves along the X, Y, and Z axes. This method works for simple parts but struggles with complex geometric shapes and curved surfaces. To address this, multi-axis linkage technology was developed.
Multi-axis CNC processing typically includes four-axis and five-axis processing. Four-axis processing adds a rotation axis (usually the A axis, rotating around the X or Y axis) to the three-axis setup. Five-axis processing adds two rotation axes (the A and C axes). This increased freedom of movement allows the tool to approach the workpiece from more angles, improving the ability to process complex shapes.
Advantages of multi-axis CNC machine tools in complex geometric shapes and curved surface processing
1. Complete multi-faceted processing in one clamping
In multi-axis CNC processing, the workpiece processes multiple faces in one clamping. This reduces clamping time and avoids positioning errors. This is crucial for high-precision parts, as each re-clamping may cause slight offsets, affecting accuracy.
2.Improve processing accuracy
Multi-axis CNC machines position the tool at the optimal angle to cut the workpiece. This reduces tool path complexity and cutting load, improving processing accuracy. Five-axis machines excel in processing complex shapes and curved surfaces. They dynamically adjust the tool to maintain optimal cutting conditions, preventing overcutting or undercutting.
3.Shorten the processing cycle
Multi-axis CNC machine tools shorten the processing cycle by completing more faces and complex tasks in one operation. This boosts production efficiency and reduces costs, making multi-axis CNC processing ideal for mass production.
4.Adapt to the processing needs of complex surfaces
Modern industrial products, such as aerospace devices, medical equipment, and automotive parts, increasingly feature complex surface designs. Multi-axis CNC machines enable continuous tool movement in space, perfectly meeting the needs of complex surface machining. This ensures workpiece smoothness and precision.
5. Reduce tool wear
In three-axis machining, the tool may need to change direction drastically, increasing wear and causing uneven surface roughness. Multi-axis machining optimizes the cutting angle and path, evenly distributing forces, reducing tool wear, and extending tool life.
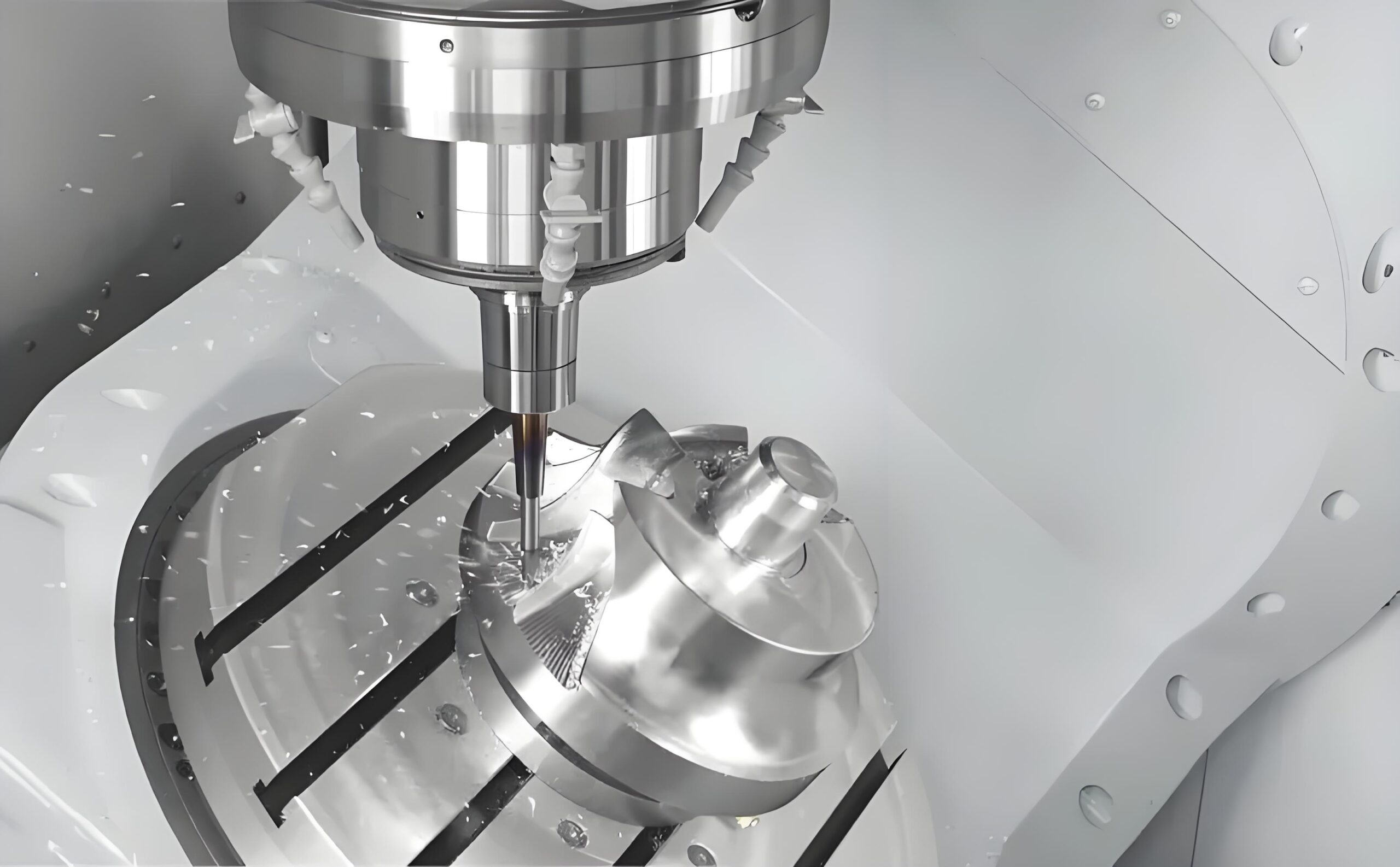
Challenges in the application of multi-axis CNC machine tools
Although multi-axis CNC machine tools have shown many advantages in the processing of complex geometries and surfaces, they also bring corresponding challenges, especially in programming, operation, and maintenance.
1 . Complex programming
Compared with three-axis CNC, the programming of multi-axis CNC is more complex. Multi-axis linkage requires skilled programmers who can control the tool’s path and angle to avoid interference or collisions. To address this, companies must use advanced CAM software and virtual simulation tools. However, this also means investing more in software and staff training.
2.High cost of equipment
The cost of multi-axis CNC machine tools is much higher than that of traditional three-axis machine tools. In addition to the expensive equipment itself, special fixtures, ,, tools and maintenance equipment are also required. This makes the initial investment of multi-axis CNC machining large, and its economy can usually only be reflected in thman-machine’s-value-addedd or complex parts.
3. Complex operation and maintenance
Multi-axis CNC machines require operators to have excellent skills and regular maintenance for optimal performance. Their complex structure makes maintenance difficult and costly when failures occur. Additionally, multi-axis CNC machining demands a stable power supply and precise temperature control.
4. Accurate control of tool path
Multi-axis linkage machining requires precise control of tool paths. Even a slight error can cause machining failure. Operators must have both strong theoretical knowledge and extensive practical experience. During machining, operators must constantly monitor the tool’s status and path to ensure accuracy and surface quality.
5. Solving interference problems
Due to the complex movement of multi-axis CNC machine tools, interference problems may occur between tools, fixtures, and workpieces. This interference will not only lead to machining failures but may also damage the machine tool or workpiece. Operators must plan and simulate in detail when programming and setting fixtures to avoid potential interference risks.
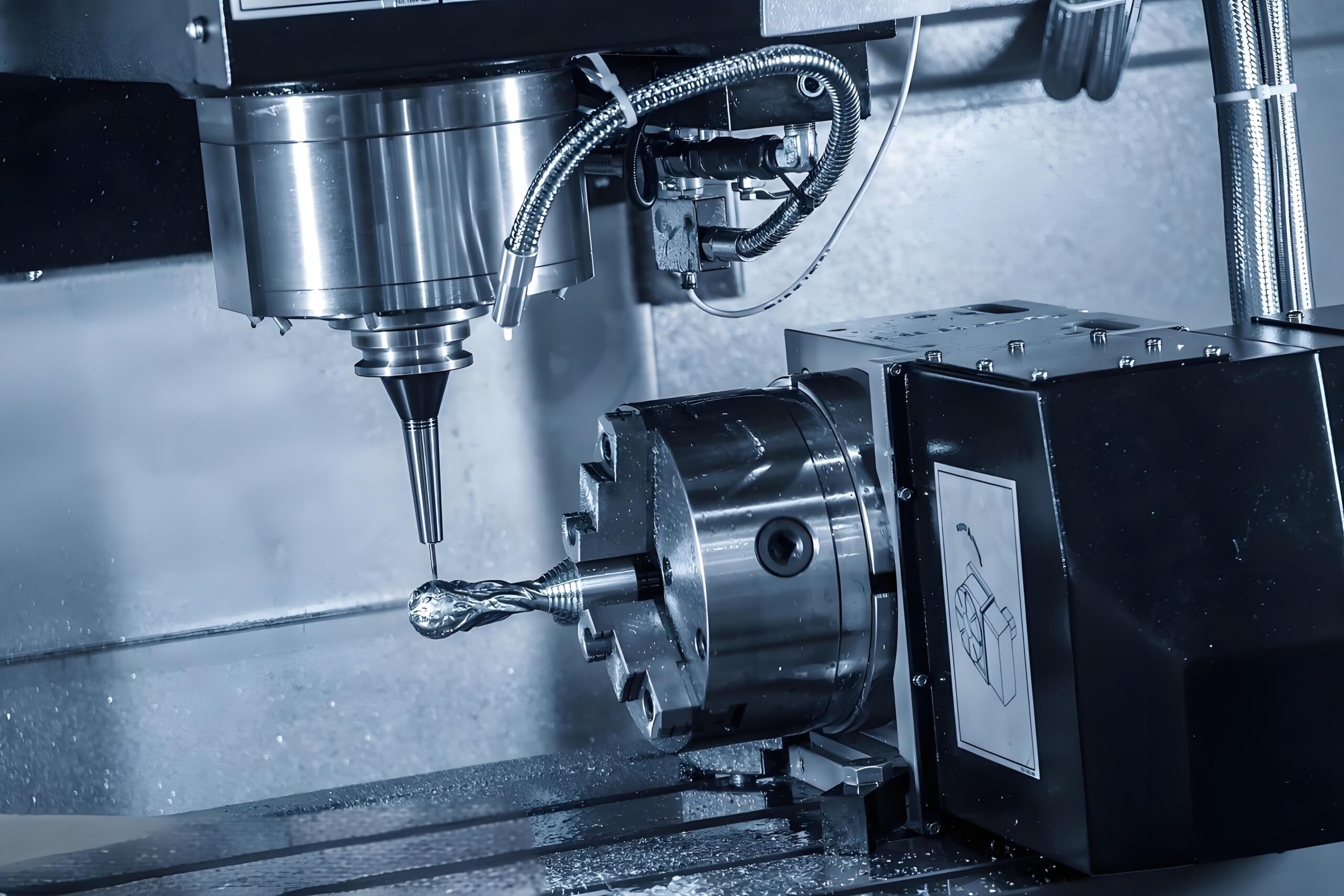
Application areas of multi-axis CNC machine tools
Multi-axis CNC machine tools have been widely used in multiple industries, especially in machining tasks that require high precision and complex shapes.
1.Aerospacece industry
Aerospace devices usually have complex surfaces and structures, requiring extremely high machining accuracy and consistency. Multi-axis CNC machine tools can efficiently and accurately process these complex parts to meet the stringent requirements of the aerospace industry.
2. Automobile manufacturing
The shapes of automotive parts are becoming increasingly complex, especially key parts in engines and transmission systems. Multi-axis CNC machine tools can complete the machining of these complex parts in one clamping, ensuring the consistency and high quality of the parts.
3.Medical equipment
Medical equipment and instruments often require processing of complex shapes and surfaces, such as prostheses, implants, etc. Multi-axis CNC machines can accurately process these parts to ensure that they meet strict medical standards.
4.Mold manufacturing
Mold manufacturing is an important area of application for multi-axis CNC machine tools. Complex molds usually contain various surfaces and cavities, and only multi-axis CNC machines can efficiently complete these processing tasks.
5.Energy industry
In the energy industry, such as wind turbines, oil drilling equipment, etc., the processing of large and complex parts requires the support of multi-axis CNC machines. These parts usually have complex geometries and high precision requirements.
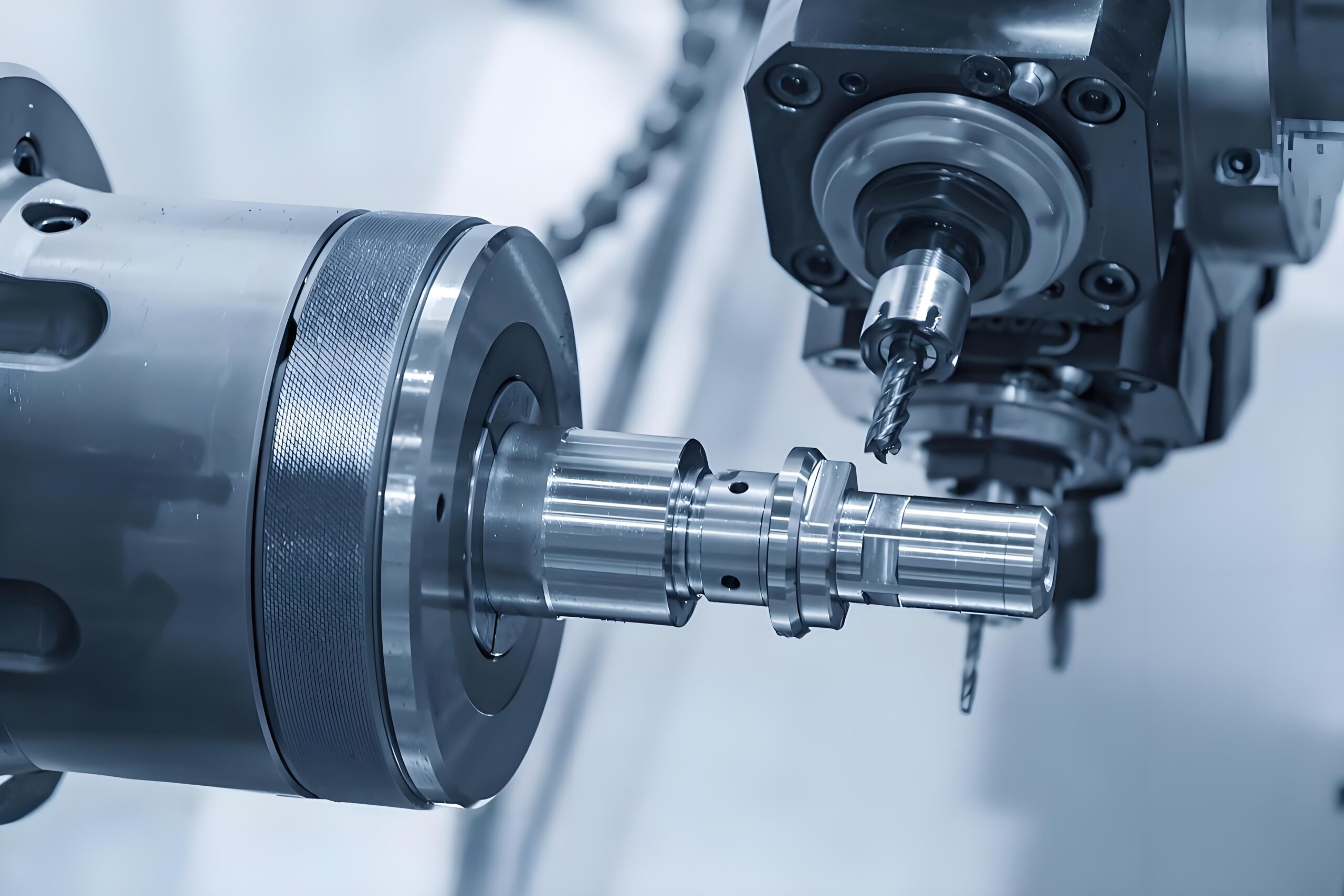
Future development trend of multi-axis CNC machine tools
Looking to the future, multi-axis CNC machine tools will continue to develop in the direction of intelligence, and AIautomautomationfficiency.
1. Intelligence and automation
With the development of artificial intelligence and machine learning technology, multi-axis CNC machine tools will become more and more intelligent. Intelligent algorithms can help optimize tool paths, predict tool wear, and automatically adjust processing parameters. This will greatly reduce the burden on operators and improve processing efficiency and quality.
2. Human-machine collaboration
In the future, multi-axis CNC machine tools will pay more attention to collaboration with operators, helping operators better manage complex processing tasks through human-machine interface optimization and intelligent assistants.
3. Virtual simulation and digital twin
Virtual simulation technology will become more popular, helping operators to foresee possible problems and solve them before actual processing. Digital twin technology will also develop further, allowing real-time monitoring and optimization of machine tools and processing processes.
4 . Environmental protection and sustainable development
In the context of sustainable development, multi-axis CNC machine tools will develop in a more efficient and environmentally friendly direction. Reducing energy consumption, improving material utilization, and reducing emissions will become the focus of future development.
5.Personalized customized production
As market demand for personalized products rises, multi-axis CNC machine tools will play a bigger role in small-batch, multi-variety production n. Its high flexibility and precision make personalized production possible.
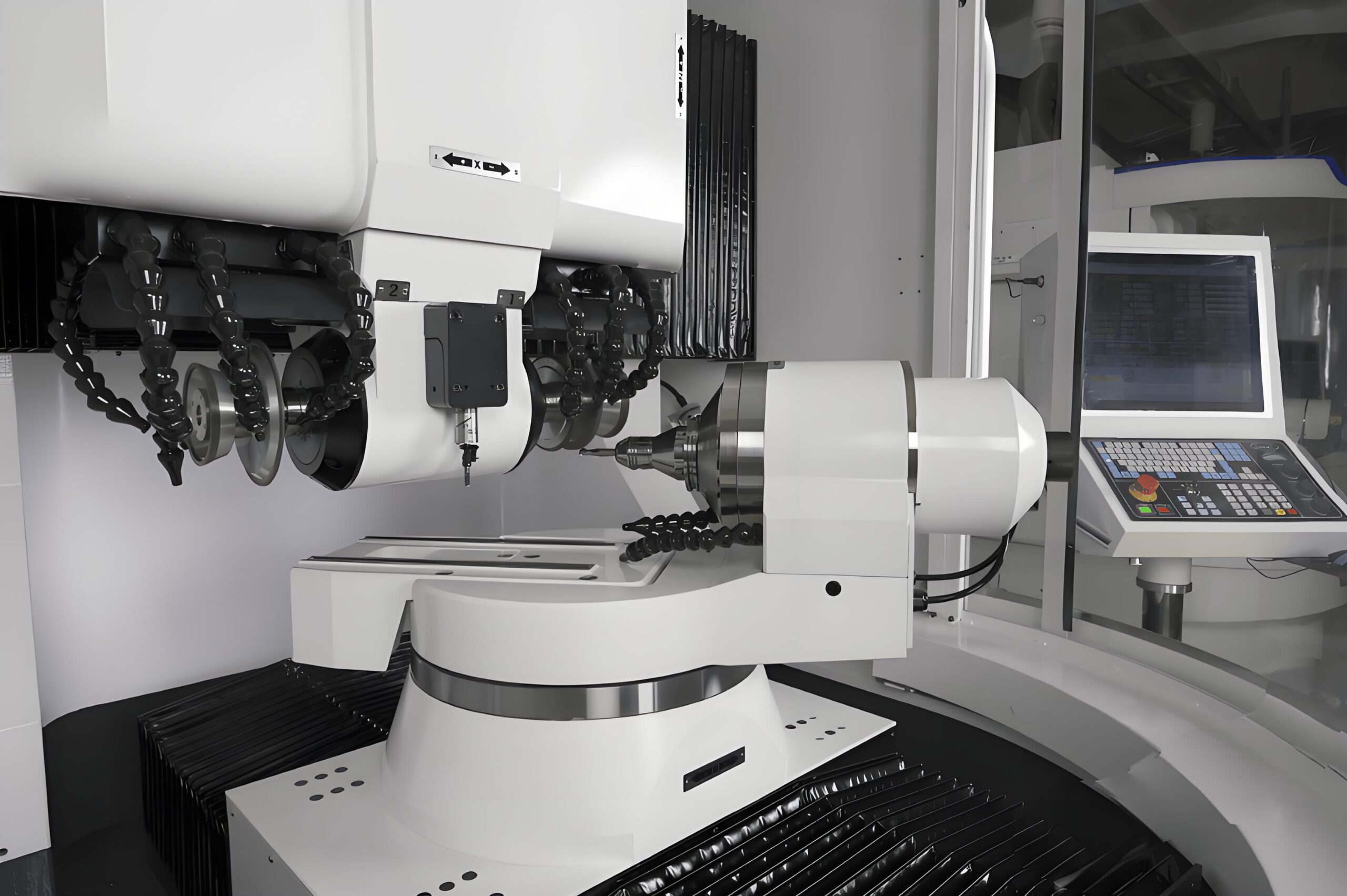
Conclusion
Multi-axis CNC machines offer powerful processing capabilities and flexibility, enabling complex geometric shapes and curved surface processing. However, technological advancements also bring new challenges. As CNC professionals, we must master existing technologies while adapting to new tools and methods. Continuous innovation and optimization will drive progress in multi-axis machining.