Under normal room temperature conditions, the effective storage time of immersion gold and HASL (Hot Air Solder Level, spray tin) boards in sealed packages is 180 days, while immersion silver, immersion tin, OSP (Organic Solderability Preservatives, organic coating) The effective storage time of the board is 90 do. The storage process is a slow aging process. During the period, the surface treatment will be oxidized or deteriorated due to the influence of temperature or humidity in the environment, which will eventually affect its solderability. Due to fluctuations in market demand, PCBs often exceed the shelf life. If the light board is directly scrapped, it will often bring huge economic losses to the enterprise, but the direct use of the expired board will bring huge quality risks. Therefore, it is necessary to study the reliability of overdue PCBs and provide guidance for the use of overdue PCBs in enterprises.
1. test plan
There are a total of 285 test PCB samples, the storage period of the selected 12-layer immersion gold board is 26 months, and the storage period of the OSP board is 14 months. All test samples need to be baked at 120 degrees Celsius for 4 hours (except for water absorption test), see Table 1 for details.
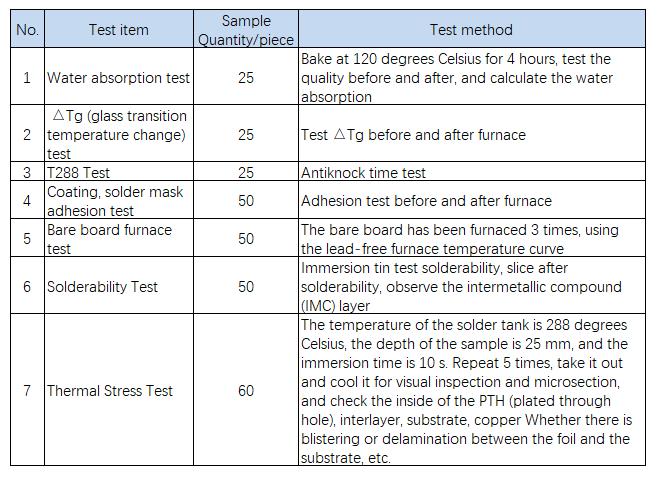
2. test results
2.1 Water absorption test
1) Sample preparation: randomly take a 3 cmX3 cm sample in the plate, and smooth the edges around the sample with sandpaper, and no burrs are allowed.
2) Test: Weigh its mass with an electronic balance, accurate to 0.1 mg, expressed in m1; bake the plate at 120 degrees Celsius for 4 hours, then take out the sample and cool it to room temperature; weigh its mass again, accurate to 0.1 mg, expressed in m2 .
3) Evaluation method: water absorption = (m1-m2)/m2xl00%
4) Test results: Take 25 pieces of bare boards for water absorption test, and the results are all qualified, indicating that the overdue period has little effect on the water absorption of the boards, see Table 2 for details.
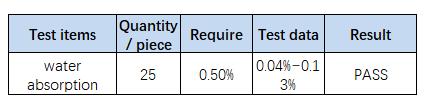
2.2 △Tg test and T288 test
1) Sample preparation: Randomly take the flat area of the outer layer, with a diameter of 2-4mm and a mass of 15-25 mg, and select the copper-containing area of each layer (the size can be
According to the actual situation); sand the edges around the sample smooth with sandpaper, no burrs are allowed.
2) Test method: The condition of the baking board is to bake the board at 120 degrees Celsius for 4 hours, and test according to the requirements of the IPC-TM-650 2.4.24 standard.
3) Evaluation method: △Tg standard requirement is less than or equal to 3 degrees Celsius, if △Tg exceeds the standard (3 degrees Celsius), it is unqualified; T288 standard requirement is greater than or equal to 5 minutes, if the test result is less than 5 minutes, it is unqualified.
4) Test results: △Tg and T288 tests were carried out on 25 bare boards. As a result, 18 pieces failed the △Tg test and 7 pieces failed the T288 test. It shows that the overdue period has a great influence on the quality and T288 of the plate, see Table 3 for details. This is because when the PCB is overdue, the resin of the PCB will absorb more water (the moisture of the overdue PCB mainly comes from the storage environment), and the moisture will be converted into plasticizers in the resin, which not only causes the Tg to drop, but also makes the rubbery state come earlier. , which will cause instantaneous expansion in the Z-axis direction and rapid cracking. This phenomenon is most likely to occur between 100 degrees Celsius and Tg.
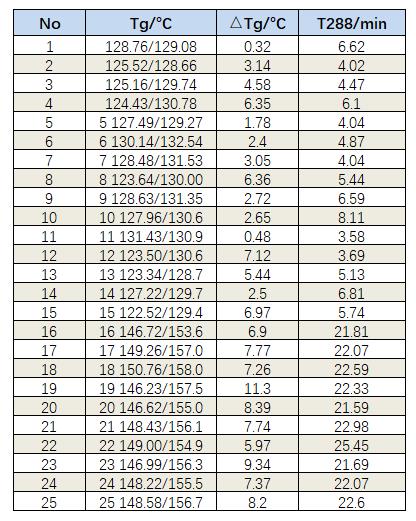
2.3 Adhesion test
1) Wash the surface of the sample with ethanol and dry it.
2) Use your fingers to press the test tape (12.7 mm wide, 50.8 mm long) vertically on the surface to be tested, forcefully remove all the air in the tape, so that there are no air bubbles between the tape and the surface to be tested, and place it for 1s.
3) Apply a force perpendicular to the surface to be tested by hand, and quickly pull off the tape.
4) Observe the tape and make a record.
5) Repeat steps 2)~4) at least twice on different positions of the sample, and a new tape must be used for each test.
6) Evaluation method: There should be no traces of the test object sticking to it on the tape.
7) Test results: 25 overdue bare boards were taken for solder mask and coating adhesion tests, and the results all met the standard requirements. See Table 4, indicating that the overdue period has little effect on solder mask and coating adhesion.
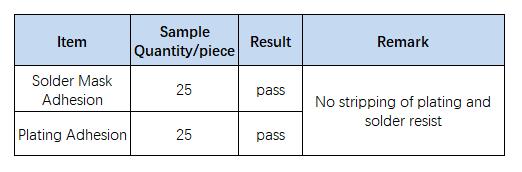
2.4 Solderability test and bare board furnace test
The lead-free reflow soldering curve shown in Figure 1 was used to test 50 pieces of long-term bare boards (see Table 5). There was no abnormality in the appearance of the bare boards; The white spots shown in Figure 2.
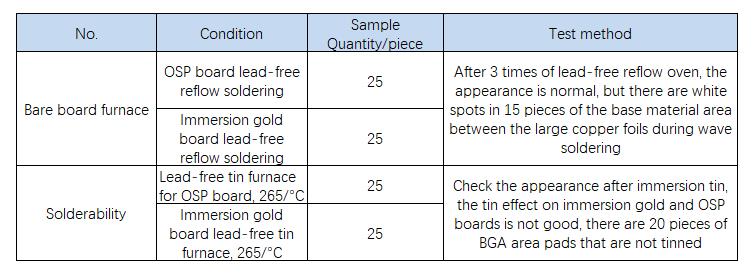
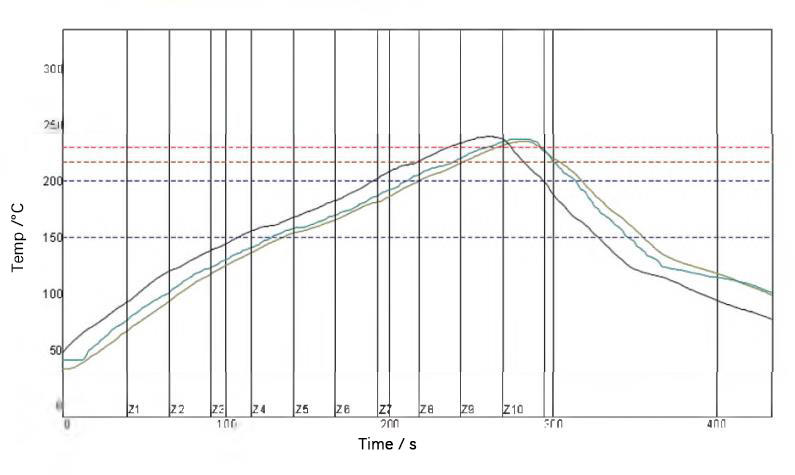
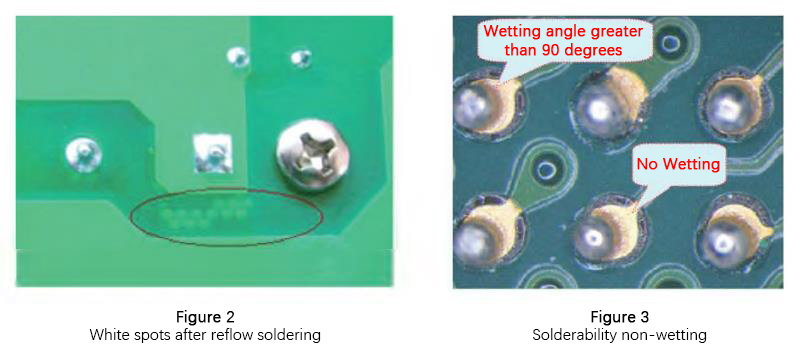
2.5 thermal stress test
Perform appearance inspection and slice analysis on 60 thermal stress test panels. After the thermal stress test, no delamination and blistering was found in the appearance inspection, but in the slice analysis, there were defects such as hole pad lifting, resin shrinkage, hole wall and inner layer separation (as shown in Figure 4). The reason for this defect is that the PCB board has been stored for a long time, and the board absorbs moisture. Simply baking before reflow soldering cannot remove the moisture. During reflow soldering, the hole pad is lifted, the resin shrinks, and the hole wall is separated from the inner layer and other serious defects. The lifting of the hole pad will cause quality problems such as open circuit; the shrinkage of the resin and the separation of the hole wall and the inner layer provide a channel for ion migration, which is likely to cause quality problems such as short circuit. In addition, this kind of defect is difficult to distinguish from the pure appearance, and generally needs to be seen through destructive slice analysis. Therefore, the hidden risk is extremely high.
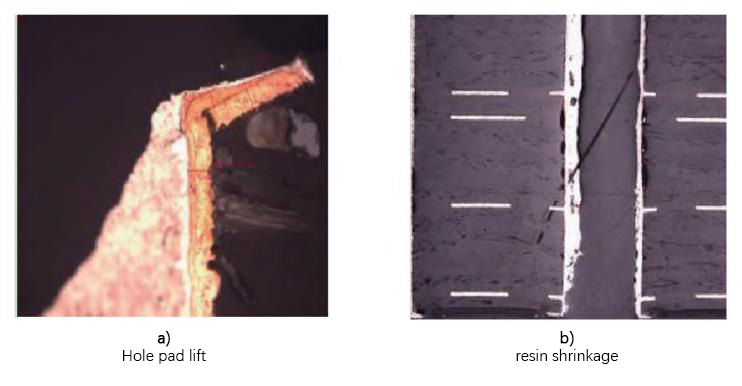
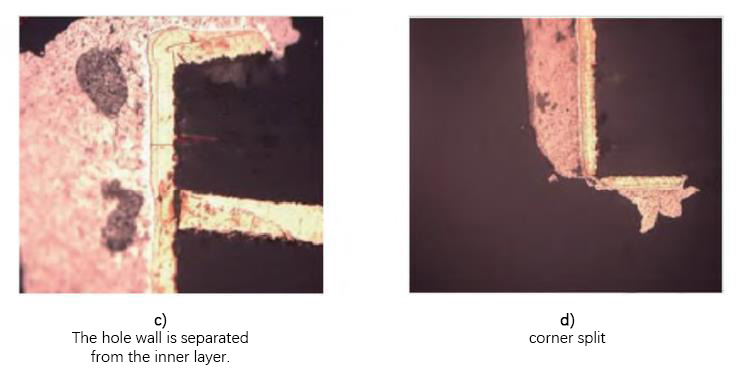
3. Conclusion
After seven tests including water absorption test, △Tg (glass transition temperature change) test, T288 test, coating and solder mask adhesion test, solderability test, thermal stress test, and bare board furnace test, the main conclusions are as follows:
1) Although the water absorption test results of the overdue board are too large, they are all within the specification requirements, indicating that the overdue period has little effect on the water absorption of the PCB board.
2) The △Tg and T288 test results of the overdue board exceed the standard requirements, and it is easy to cause delamination and explosion when the PCB passes through the reflow oven.
3) The overdue board coating and solder mask adhesion tests meet the standard requirements, indicating that the overdue period has little effect on the PCB coating and solder mask adhesion.
4) The overdue immersion gold board and OSP board failed the solderability test, and there is a phenomenon that they cannot be soldered. Poor welding seriously affects the performance of the single board.
5) When the immersion gold board is wave soldered for an extended period, white spots appear in the base material area between the large copper foils, indicating that the extended period of moisture absorption has an impact on the quality of wave soldering°
6) After the thermal stress test, no delamination and blistering was found in the appearance of the PCB, but there were defects such as hole pad lifting, resin shrinkage, hole wall and inner layer separation during slice analysis, and there were hidden dangers in the long-term reliability of the board.
7) For OSP boards with a storage period of more than 1a, it is recommended not to use them because they fail the solderability test. For OSP boards with a storage period of more than 90 days and less than 1 year, it is recommended to return to the factory to remove the OSP film and then perform OSP again before use.
8) For immersion gold boards with a storage period of more than 2 years, due to thermal stress tests, there are serious defects such as hole pad lift, resin shrinkage, hole wall and inner layer separation, and there are hidden quality risks. It is recommended not to use them. In order to eliminate the influence of moisture absorption as much as possible, the storage period is more than 0.5 a and less than 2 a. It is recommended to bake it at 125 degrees Celsius for 4 hours before using it every time it goes online.