Sheet metal processing has processing flexibility and is suitable for small-batch production. Therefore, it has been widely used in many industries such as chassis cabinets, home appliances, hardware products, etc. This article analyzes how to arrange processing technology in small-batch production, addresses potential issues in sheet metal processing, and proposes improvements.
As home appliances and instruments are replaced faster, products are becoming more miniaturized and lightweight, highlighting the advantages of sheet metal processing. Meeting diverse product needs quickly has become a key challenge. Sheet metal technology has evolved from manual to stamping, and now CNC, making it more precise and intelligent.
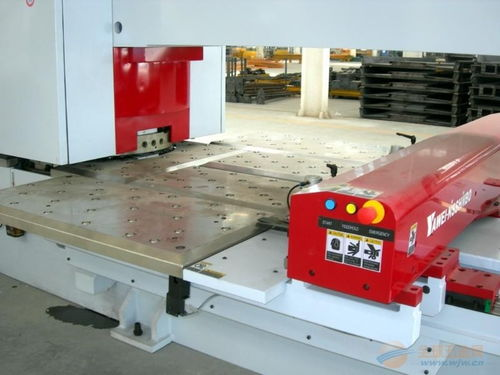
Sheet metal processing development trend assumptions
A few years ago, sheet metal processing equipment mainly included ordinary punching machines, laser machines, and bending machines. The equipment’s disadvantages include low positioning accuracy and reliance on experienced operators, making it difficult to process small, precise products.
With the rise of automation, CNC bending machines and laser punching compound machines are widely used in sheet metal processing. Advanced programming software improves processing quality and efficiency, allowing operators to use pre-edited programs, reducing skill requirements, and ensuring high-precision results.
Although CNC sheet metal processing technology has been popularized, the current bending process still mainly relies on manpower. When producing products with larger sizes and heavier weights, the labor intensity of operators is still very high. Although bending manipulators have begun to be used, their application in the sheet metal processing industry is not yet widespread due to the limitations of product characteristics.
In the future, a bending follower that captures machine tool signals via the API interface could reduce labor intensity in producing large-size products. As automation advances, bending robots may replace manual labor, becoming a trend in sheet metal processing.
Introduction to sheet metal processing technology
Sheet metal processing mainly includes cutting, bending, welding, riveting, forming, and other processes, among which the most commonly used basic processes are cutting, bending, and welding. The following is a brief introduction to these three basic processes:
1. Cutting
Sheet metal cutting can be divided into two types: punching and laser processing.
· Punching processing: This is a process that uses a punch combined with a mold for processing. Its advantage is the high dimensional and positional accuracy of holes, making it ideal for porous products with efficient processing. However, the mold gap must be adjusted based on material thickness and properties: too large a gap causes burrs, while too small a gap reduces mold life and may cause damage. When punching the product’s outer dimensions, there will be “cutting points” remaining, which will affect the appearance.
· Laser processing: A focused high-power beam melts the material’s surface, with auxiliary gas blowing away the residue. Its advantages include reduced mold costs, fast processing, minimal deformation, and clean, precise cuts. The introduction of laser punch machines has significantly improved processing efficiency and dimensional accuracy in sheet metal blanking.
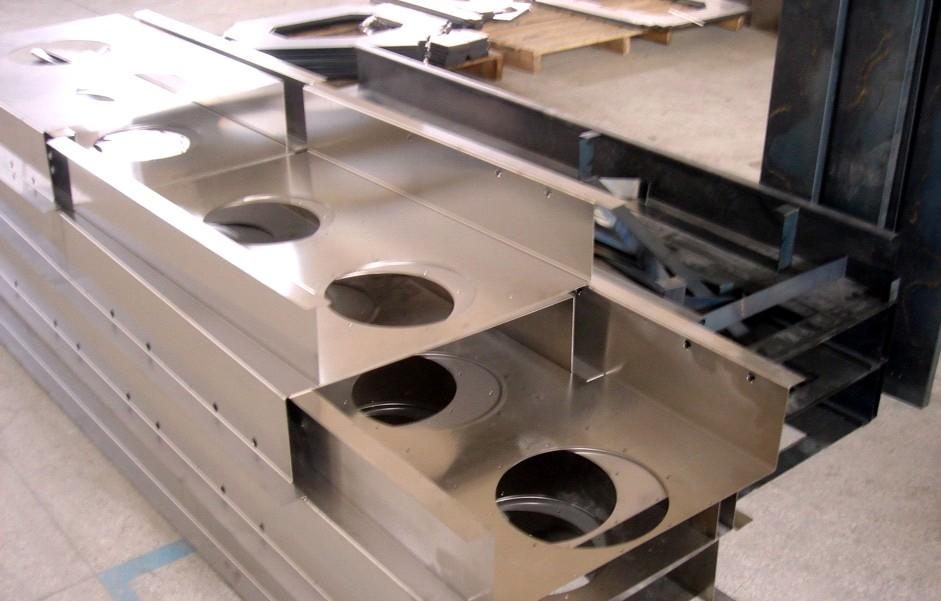
2. Bending
2.1 Minimum bending radius
If the radius is too small, the tensile ductility of the material will become stronger. When the ductility reaches the limit, the material will break.
2.2 Bending ductility coefficient
Bending dies of different materials and different V-groove widths will affect it. For example, among aluminum plates, steel plates, and stainless steel plates, when the thickness is the same, the ductility coefficient of stainless steel is the largest, and that of aluminum plates is the smallest.
For the same material, different V-groove widths will also affect the ductility coefficient. Generally, the wider the V-groove, the greater the ductility coefficient. To achieve accurate bending dimensions, select an appropriate V-groove and calculate the material’s ductility coefficient. Due to plate rebound, a bending tool with a smaller angle than required is usually needed.
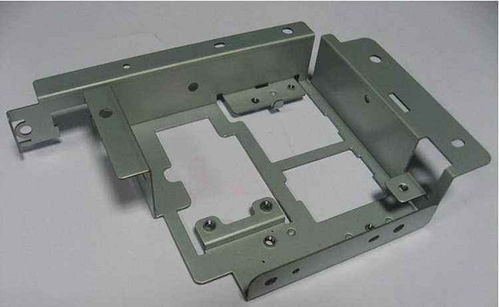
3. Welding
In the process of sheet metal processing, welding is usually performed to enhance the strength of the joints. Common welding methods include gas-shielded welding, laser welding, and resistance welding.
· Gas-shielded welding: welding wire is required, the welding effect is more beautiful, but the plate is greatly deformed by heat.
· Laser welding: welding wire is also required. Compared with gas shielded welding, the welding effect is better but the cost is higher, and the plate is greatly deformed.
· Resistance welding: welding is performed by contact heating and pressurizing the upper and lower electrode heads, as shown in Figure 2. No welding wire is required, and the plate is less deformed after welding. The welding position of complex shapes will have higher requirements on the shape of the electrode head.
These three processes are the most basic and important parts of sheet metal processing, each with its own characteristics and application scenarios. Through reasonable selection and application, the processing quality and efficiency can be effectively improved.
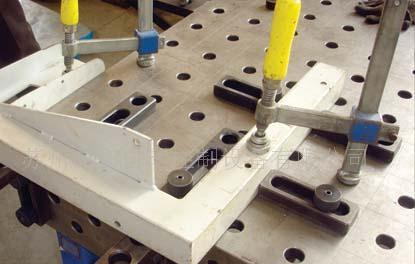
Difficulties in sheet metal processing
In sheet metal processing, whether cutting, bending or welding, an optimal sequence must be designed to meet the product’s appearance and quality requirements. As society develops, product structures are becoming smaller and more complex, increasing the technical demands on sheet metal processing.
1. Difficulties in the cutting process
Special attention should be given to processes like deep drawing and convex hull due to their differing forming directions and sizes, which affect the machine tool’s impact on the structure and require tailored treatment.
2. Difficulties in the bending process
As the structural parts become more complex, the use of non-standard tools in the bending process is increasing. Therefore, in processing programming, it is necessary to break the conventional thinking and design different forms of non-fixed and non-patterned processing procedures.
3. Difficulties in the welding process
The welding process also faces similar challenges, especially in the welding process of complex structural parts, the welding parameters must be precisely controlled to ensure the welding quality.
Improvement measures for sheet metal processing
1. Sheet metal processing material selection
When selecting sheet metal materials, ensure they meet the product’s material and thickness requirements. Accurately measure the thickness upon receipt to confirm it falls within the acceptable tolerance. Prioritize material utilization by optimizing size specifications, limiting to no more than three sheet types for the same material and thickness to avoid material waste and reduce processing costs.
Select materials based on the shape and size of the processed product to ensure consistency. Additionally, use waste from large parts’ internal structures for small parts to improve material utilization and reduce costs.
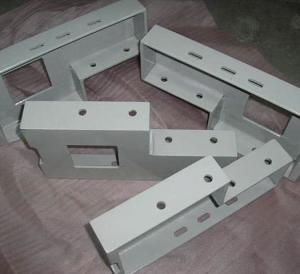
2. Hole structure design
In sheet metal processing, hole structure design is crucial. When designing, it is necessary to take into account the product’s appearance and quality requirements to ensure easy processing. First, design the hole’s position, size, shape, and quantity based on the product structure and purpose, and plan the processing steps. To ensure strength and quality, maintain a hole margin at least twice the material thickness. Next, optimize processing to address specific issues, such as controlling the hole’s distance from the bending area to prevent deformation due to material extension.
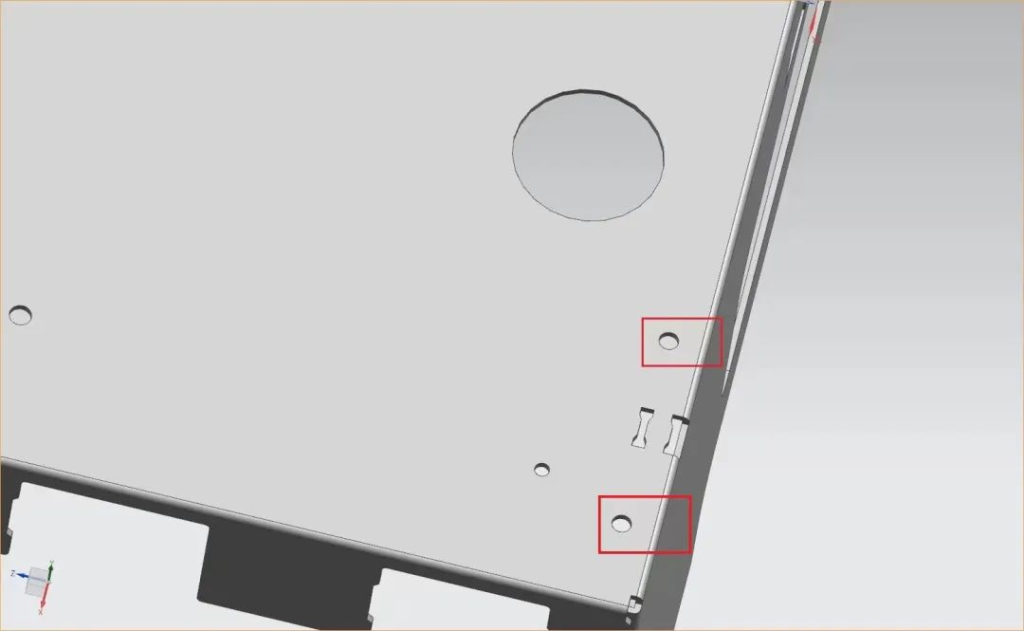
3. Welding structure design
Welding structure design covers many aspects. First, in the design stage of sheet metal structural parts, reserved space must be considered to avoid welding quality problems caused by insufficient space. Secondly, the design of welding time and welding seams should be appropriate to prevent the deformation of sheet metal sheets. The welding point design should be symmetrical and avoid excessive distance from the weld, which not only ensures aesthetics but also ensures that the sheet metal parts meet the load-bearing standards.
Conclusion
Sheet metal processing has become an indispensable part of our lives. To meet market demands, we must study sheet metal processing principles, optimize technology, and quickly design and produce high-quality products. This can promote the sheet metal manufacturing industry to move forward in a better direction of development.