In the machining industry, the application of CNC machine tools helps to improve machining efficiency and make machining more accurate. And through the exploration and improvement of technicians, the development of CNC machine tools has been promoted.
However, in the practical aspects, there are still machining problems, in this regard, the enterprise can cleverly use CNC machine tools, optimize machining, and carry out a good exploration, clear processing efficiency improvement methods.
CNC machine tools for machining efficiency improvement significance
1. Guarantee production efficiency
In machining activities, the integration of CNC machine tools can help improve processing efficiency.
Operators are the main body of traditional mechanical processing, work practices are easily affected by human factors.
CNC machine tools rely on pre-written programs to carry out automated machining activities, which not only improves the effectiveness of machining, but also helps a variety of processes at the same time, and achieve good production results.
At the same time, CNC machine tool technology in the field of machining can carry out accurate judgment, analyze the mechanical processing activities, clarify the parameters, and reduce the impact of human factors.
In a word, the application of CNC machine tool technology to mechanical processing can improve the precision of products, better reduce the problems of errors and repeated processing brought by traditional processing, and significantly improve the production efficiency.
2. Improve product quality
CNC machine tools can improve machining precision and implement stable machining to ensure the quality of mechanical parts.
In traditional machining activities, it is easy for operators to operate incorrectly, resulting in insufficient product accuracy.
CNC machine tools, however, mainly with the help of automation, clarify the processing process and parameters, carry out high-precision processing, and improve the accuracy of mechanical parts.
In addition, CNC machine tools can apply a variety of processing methods to deal with complex processing tasks and improve the accuracy of parts.
In short, automated processing can reduce the influence of human factors and improve product quality.
3. Saving processing resources
In machining activities, the clever use of CNC machine tools, can grasp the cutting situation, reduce the traditional machining problems, such as data waste problems.
At the same time, the CNC machine tool adopts automation technology, analyzes the cutting parameters, and reasonably uses the cutting tool, so as to improve the service life of the cutting tool, reduce the frequency of tool replacement, and effectively avoid the emergence of resource waste.
In addition, the application of CNC machine tools to machining can better carry out batch processing and automated production, effectively reducing the consumption of human resources.
Compared with traditional machining, the application of CNC machine tools requires fewer operators, and can be well monitored and adjusted to implement mass production.
In short, the skillful use of CNC machine tool technology can help save human resources and improve processing efficiency.
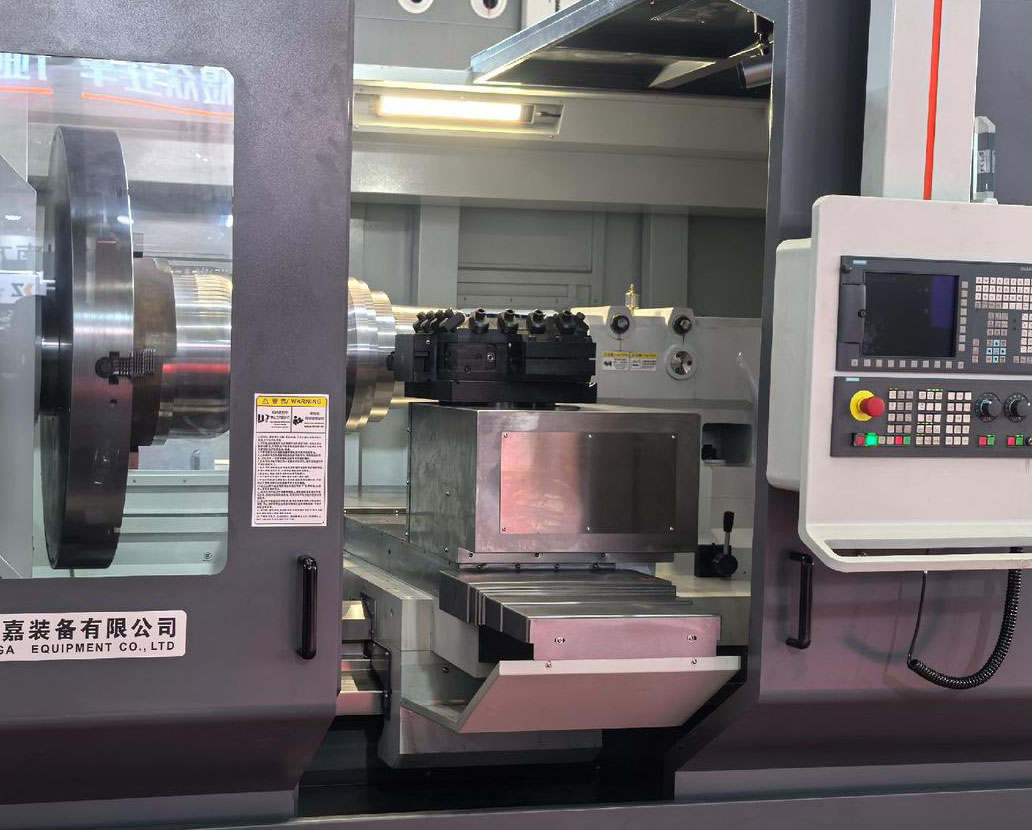
Current situation of CNC machine tool machining
1. Operator quality needs to be improved
In machining, the mechanical production process is often complex. As a result, using CNC machine tools can be challenging. Operators must have strong professional skills and theoretical knowledge to carry out the work successfully.
However, from a practical point of view, the operator lacks professional ability, encountering production problems, it is difficult to carry out targeted measures, the effect of machining is insufficient.
In the context of today’s times, some operators of enterprises have a poor understanding of CNC machine technology, professionalism needs to be improved, it is difficult to carry out good program writing activities.
In practice, there are problems such as instruction writing errors and insufficient writing speed.
At the same time, due to the operators’ lack of understanding of CNC machine tool knowledge, it is difficult to participate in complex operations, and it is easy to make machine tool operation errors and lack of precision.
2. Insufficient frequency and rationality of tool-operating design
Currently, there is a lack of rationality in the design of frequency and operation in the machining process of CNC machine tools.
In the actual machining, many enterprises in the process of using CNC machine tools, the frequency and operation of the problem of insufficient, the actual machining effect to be improved.
At the same time, in the practice of machining, business operators lack of attention to detail, ignoring the fixture and tool walking, is not conducive to the smooth progress of machining.
3. Problems with the use of CNC machine tools
CNC machine tools not only help to improve the efficiency of machining, side drive the development of the manufacturing industry.
However, in the actual development of enterprises, has not yet applied good measures, CNC machine tool service life to be improved, at the same time in the long-term production link, due to the lack of professional and technical personnel, resulting in the application of CNC machine tools is not effective.
In addition, when there is a decline in precision, the lack of effective measures to carry out, the actual use of CNC machine tools is less effective.
Although some enterprises have clarified the value of CNC machine tools, the actual implementation of the effect is poor, such as maintenance and refurbishment effect.
4. Lack of rationality of machining program
In the enterprise machining activities, CNC machine tools need the assistance of various types of programs, take computer equipment, carry out good machining activities, and ultimately complete the production task.
However, from the actual CNC machine tool machining situation, there is a lack of rationality in program design, poor machining results, not conducive to the healthy development of enterprises.
CNC machine tools to improve machining efficiency methods
1. Strengthen staff training, improve operator quality
1.1 Enhancing Training for CNC Operators
CNC machining involves complex processes such as tool changes, design execution, and precise operations. The operator’s skill level directly impacts machining quality.
To boost efficiency, enterprises should invest in staff training, encourage participation, and cultivate professional expertise.
A structured training system, combined with performance assessments and a reward-punishment mechanism, can motivate operators to engage actively.
Recognizing skill mastery and participation with incentives while addressing underperformance ensures continuous improvement and higher machining efficiency.
1.2 Improving Operator Competence for Technological Advancements
As CNC technology evolves, operators must stay updated with the latest advancements. Enterprises should focus on comprehensive training, ensuring that staff understands technical operations before starting work and actively pursues certification.
Pre-employment training programs can integrate theoretical knowledge with hands-on practice, fostering professionalism.
Additionally, enterprises should evaluate qualifications and skill levels during recruitment. Implementing a mentorship system, where experienced employees guide new hires, helps enhance practical skills and ensures consistent operational quality.
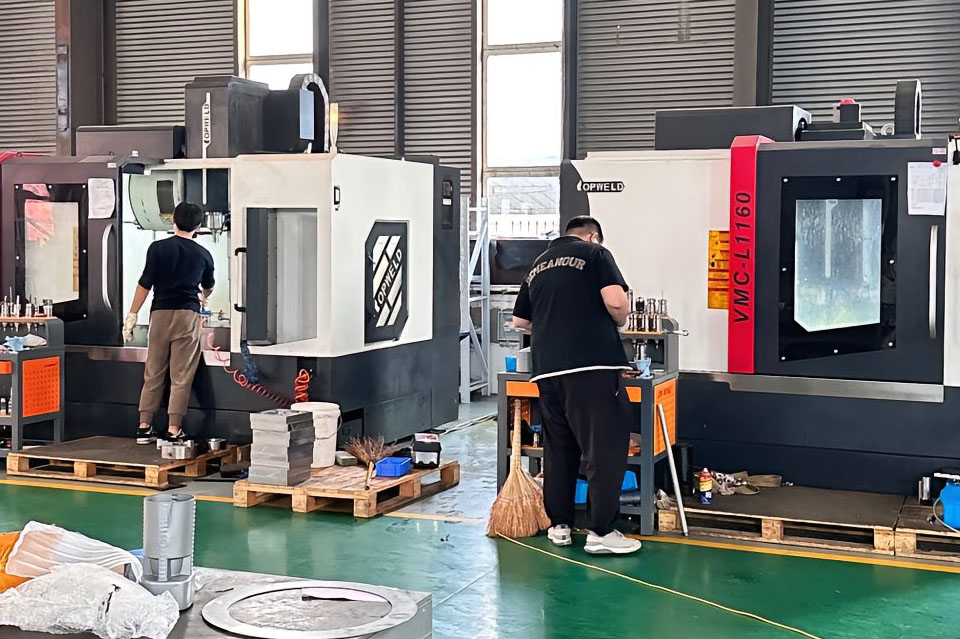
2. Data management, optimization of machining
In modern enterprises, effective data management plays a crucial role in CNC machining. By leveraging data collection and processing, businesses can monitor equipment conditions, optimize machining activities, and improve decision-making.
A data-driven approach starts with comprehensive data collection and analysis. Operators can utilize sensors and monitoring tools to gather real-time information, build databases, and develop analytical models.
This enables better tracking of processing parameters, early detection of anomalies, and proactive issue resolution, ultimately enhancing machining stability and reliability.
2.1 Data-Driven Efficiency Improvement
Analyzing machining data allows enterprises to optimize processes, improve efficiency, and reduce resource waste. By examining processing parameters and equipment conditions, operators can refine cutting strategies, select optimal tools, and enhance machining precision.
Additionally, quality data analysis helps identify machining deficiencies. By adjusting process parameters based on these insights, enterprises can enhance product performance and maintain consistency in manufacturing quality.
2.2 Leveraging AI and Big Data for Optimization
The integration of artificial intelligence and big data further refines CNC data management. Advanced optimization algorithms enable real-time monitoring, intelligent decision-making, and predictive maintenance, reducing equipment failures and downtime.
For example, predictive models can analyze abnormal equipment behavior, allowing for timely maintenance and process adjustments.
Enterprises can also utilize big data analytics to identify trends, optimize machining strategies, and improve overall decision-making, ensuring continuous advancements in CNC machining efficiency and precision.
3. Improve the machining process, improve machining efficiency
3.1 Optimizing the Machining Process
Improving the machining process is essential for enhancing CNC machining efficiency. Enterprises can refine product processing methods to shorten cycles, reduce costs, and improve overall productivity.
The first step is to analyze machining objects and requirements. Based on this analysis, companies can optimize cutting activities by adjusting parameters such as feed rate, speed, and cutting conditions.
This prevents excessive cutting and ensures optimal results. Practical experiments and real-world applications help determine the best materials and cutting parameters, maximizing the potential of CNC machine tools.
3.2 Optimizing Process Allocation
A well-structured machining process improves efficiency by minimizing redundant work and extending tool life. Enterprises should analyze machining workflows and allocate resources effectively. Optimizing process sequencing reduces unnecessary tool changes and repetitive tasks, improving overall efficiency.
For example, selecting an effective clamping method can reduce tool replacement frequency, streamline machining, and enhance precision.
3.3 Choosing the Right Cutting Method
Selecting the appropriate cutting method is crucial for optimizing machining outcomes. Enterprises must consider material properties and processing requirements when determining the best approach.
Key cutting methods include:
- High-speed cutting: Utilizes high-speed tools and feed rates to boost machining efficiency.
- Full cutting: Enhances tool stability, ensuring smooth and precise operations.
- Efficient cutting: Involves strategic parameter adjustments to optimize machining speed and effectiveness.
By integrating these methods and continuously refining processes, enterprises can significantly improve CNC machining efficiency and overall production quality.
4. Automation production technology
The application of automated production technology helps ensure quality in the machining process. Enterprises can integrate automation into production and enhance the use of CNC machine tools.
Mechanical enterprises can use automated production technology to optimize the machining process. This supports automation implementation and improves the quality of parts production.
4.1 Improving Processing Efficiency
First of all, the enterprise cleverly use automatic clamping, tool change and other tools, can significantly improve the processing efficiency.
As traditional machining cannot be separated from the support of manpower and time to avoid the emergence of errors and delays.
The automatic clamping and tool change can improve the speed of tool replacement, reduce the impact of human factors, and enhance the processing continuity.
Enterprises can also adopt automatic clamping to enable continuous machining. This supports cutting operations and helps improve cutting quality.
4.2 Optimizing the Machining Process
Secondly, enterprises can use automation technology, system optimization, set up machining, thereby improving the processing effect.
Traditional machining cannot be separated from human participation, which inevitably leads to time-consuming and labor-intensive problems.
Enterprises should focus on using automation technology to optimize machining activities. Proper parts clamping practices can help minimize the impact of human factors.
4.3 Enhancing Resource Utilization
Mechanical enterprises can make clever use of automation systems according to production plans and process demands. The implementation of automation optimizes machining processes and improves resource utilization, ensuring smoother and more efficient production.
4.4 Real-Time Monitoring and Data Collection
Finally, mechanical enterprises can utilize CNC machine tools, data collection activities, and monitoring systems for real-time tracking. This ensures insight into the operation, processing, and quality of CNC machine tools.
Through automation technology, can guarantee the implementation of data collection and monitoring, clear equipment failures and abnormalities, and carry out targeted adjustments.
Machinery enterprises can use machining process data for real-time monitoring. This helps identify problems and make targeted adjustments to improve processing quality.
Data collection and monitoring, help to integrate the production and implementation, promote the development of full-cycle data management, so that enterprises are clear about their own machining activities, so as to carry out more accurate decision-making, but also for the development of the manufacturing industry to inject vitality.
5. Enhance the maintenance of machine tools, carry out management work
CNC machine tools have complexity characteristics, based on this feature, mechanical enterprises need to be based on the actual processing effect, according to the production capacity, and the integration of CNC machine tool facilities, to carry out good maintenance activities, the implementation of machining management, to enhance the effect of education.
In order to better carry out mechanical processing, mechanical enterprises need to focus on CNC machine tools, and the implementation of CNC machine tool maintenance activities.
5.1 First, enterprises can implement machine tool lubrication activities.
CNC machine tools are equipped with lubrication devices. During lubrication, operators should follow actual equipment needs and add suitable lubricants. This helps reduce poor-quality products and improves machining effectiveness.
5.2 Second, enterprises need to carry out regular maintenance activities.
Through the operator’s settings, carry out CNC machine tool refurbishment activities, and set a fixed time for regular equipment inspection, and from the actual situation, improve the CNC machine tool technology, effectively reduce the frequency of various types of problems, in this regard, the mechanical enterprise needs to be combined with the actual situation, to carry out the equipment processing activities, and significantly improve the efficiency of CNC machine tool machining.
To improve management, enterprises should adapt to current demands and focus on processing tasks. A clear production management plan should be established to ensure smooth operations. Setting daily and weekly tasks helps achieve production goals more effectively.
Secondly, enterprises need to combine CNC machine tool technology to optimize on-site management. Enterprises according to the actual processing needs, combined with machining activities, so as to implement management, effectively reduce the frequency of problems in CNC machine tool machining;
Finally, enterprises should focus on CNC machine tools, adjust human resources and equipment as needed, and optimize the use of various production resources. Strengthening CNC machine tool application will promote the overall development of the enterprise.
6. Focus on machining equipment, carry out selection and configuration
In order to enhance the application of CNC machine tools, mechanical enterprises need to pay attention to the implementation of staff training to enhance the comprehensive quality of operators.
Also need to use CNC machine tools, improve processing efficiency, and according to the flow of funds, machining and other circumstances, focus on selection and configuration, improve processing quality.
6.1 First, companies need to focus on machine tool brands.
In today’s industrial environment, mechanical enterprises can choose well-known CNC machine tool brands, such as TRUMPF Tongxue or SMTCL Shenyang Machine Tool. Based on production needs, they should select suitable models. Regular maintenance and inspection of equipment help ensure processing efficiency and reliable mechanical performance.
6.2 Second, enterprises need to look at the characteristics of the machine tool.
Mechanical enterprises in accordance with the characteristics of CNC machine tools, the reasonable allocation of tools.
Compared with traditional machine tools, CNC machine tools in the application of machining, help to improve the movement and feed speed, expand the cutting accuracy, paving the way for good machining.
However, CNC machine tool technology has higher requirements for cutting tools, and the previous carbon steel cutter is difficult to meet the needs of CNC machine tool processing.
Operators should assess the actual situation and select high-hardness alloy tools. Optimizing CNC machines helps prevent tool damage and improves processing efficiency.
Conclusion
In summary, in the development of modern manufacturing industry, the application of CNC machine tool technology helps to improve machining efficiency.
In the future development of enterprises, enterprises can take staff training, improve the processing technology, strengthen the machine tool maintenance and machining equipment selection, etc., to improve the application of CNC machine tools, enterprises with the application of diversified ways to improve the efficiency of machine tool processing.
With the development of CNC machine tool technology, not only improve the machining efficiency, but also promote the development of the manufacturing industry.