With societal progress, mechanical industrial technology has advanced rapidly, especially with automation and precision machining enhancing production efficiency and accuracy.
The development of precision machining technology, both the market competition environment on the machine processing industry requirements, but also an important guarantee for the development of the national economy, has become an inevitable trend.
The author analyses the types of precision machining, processing technology and technical advantages, as well as the main factors affecting precision machining, and finally its development trend to be discussed.
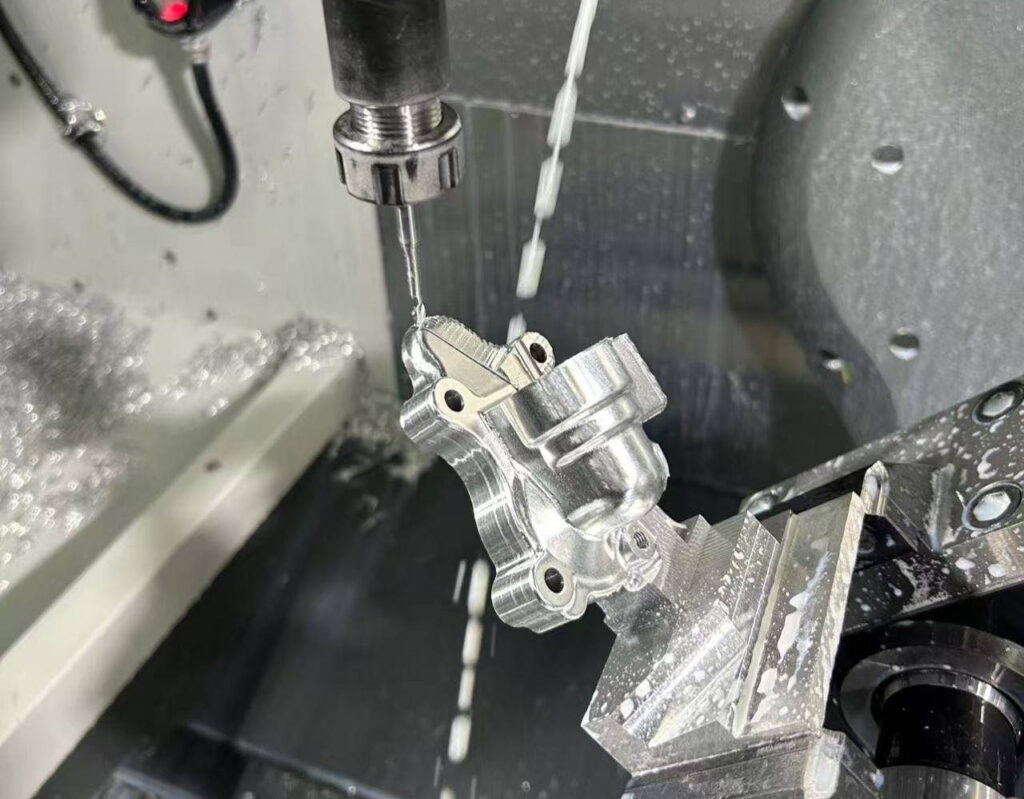
Cnc machining
Types of precision machining and technical advantages
Machining can generally be categorized based on its characteristics and technical principles into four main types: composite processing, special processing, abrasive processing, and tool cutting processing. With ongoing advancements in industrial technology, machining is evolving toward automation and modularization. Refined and precise machining has become the mainstream. According to the specific requirements of part applications and forming mechanisms, machining can also be classified into precision machining.
Deformation processing, combined processing and removal of three main forms of processing.
One of the deformation processing is to rely on extrusion, traction, centrifugal force and other external forces, as well as raw material processing of molecular movement and other internal forces, to promote the shape of the material, volume, the overall performance of the change.
The common processing technology are:
Precision discharging, forging, casting, rolling, cold extrusion, and powder metallurgy are all advanced techniques. Among them, cold extrusion is particularly well-suited for complex parts. It significantly improves raw material utilization—up to 90% or more—and provides excellent rigidity in molded components.
Combined processing, is through the physical and chemical methods of other materials attached, injected or welded to the surface of the parts, is a combination of processing methods, common types of welding, adhesion, plating and so on;
Removal processing, also known as separation processing, involves cutting, grinding, planing, chiseling, punching, and dividing raw materials or parts according to forming requirements. Common methods include CNC machine tool cutting and drilling, as well as laser cutting and drilling by industrial robots.
Precision machining places extremely high demands on processing equipment. The machine tools integrate functions such as drilling, milling, grinding, cutting, and embossing. These tools feature a high degree of automation and operate 4 to 6 times faster than conventional machines. Additionally, they require less manual labor, which helps reduce production costs and improve the economic efficiency of machining enterprises.
In short, compared with the traditional machining process, precision machining is more delicate, higher quality, more efficient, and its technical advantages are significant.
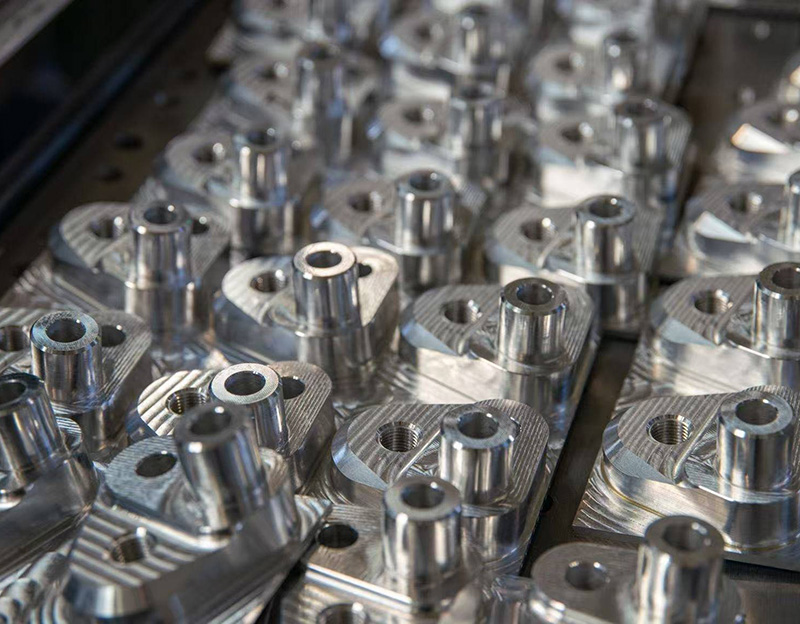
Machining parts
Main factors affecting precision machining
The quality of machined products depends on several key factors. These include the level of equipment advancement, raw material quality, and the skills of technical personnel. The production and processing environment also plays an important role. Precision machining mainly targets core components. As a result, it requires higher standards in multiple areas. These include processing equipment, techniques, operator experience, environmental conditions, and material quality. The specific requirements are reflected in the following aspects:
1.Raw material quality
Material quality is the foundation of precision machining. It directly affects the final product’s accuracy and performance. High-quality raw materials must meet chemical and physical standards. These materials should also have good processing properties. If the material does not meet technical requirements, machining accuracy will suffer. This can result in product defects and performance issues.
2.Processing mechanism
Precision machining generally has two types, one is to improve on the traditional machining process, optimize the process structure, to achieve refinement; the second is a special machining technology.
Precision machining process based on traditional processing technology such as: precision abrasive belt cutting, diamond tool cutting, precision high-speed cutting, etc., special processing technology such as: laser cutting, electron beam processing, laser engraving, electrochemical processing, etc..
In addition, there are ultrasonic honing, magnetic polishing, electrolytic grinding and other advanced processes.
3.Quality Inspection
All machined parts must undergo quality testing, testing methods including offline testing, online testing or in-situ testing, the higher the level of testing technology, the higher the accuracy of the test, the better the quality control of parts and components, and the better its precision.
4.Processing equipment
Advanced processing equipment is an important basis for ensuring precision machining, the rigidity of the machine tool, precision, stability, degree of automation and other requirements are also very high. Common equipment includes diamond grinding wheels, cutting tools and cubic boron nitride tools.
5.Operating environment
Precision machining requirements for the operating environment is very strict, the operating site temperature and humidity, shock resistance, cleanliness, anti-electromagnetic interference and other factors will affect the processing quality, general precision machining needs to be carried out in a professional precision machining workshop.
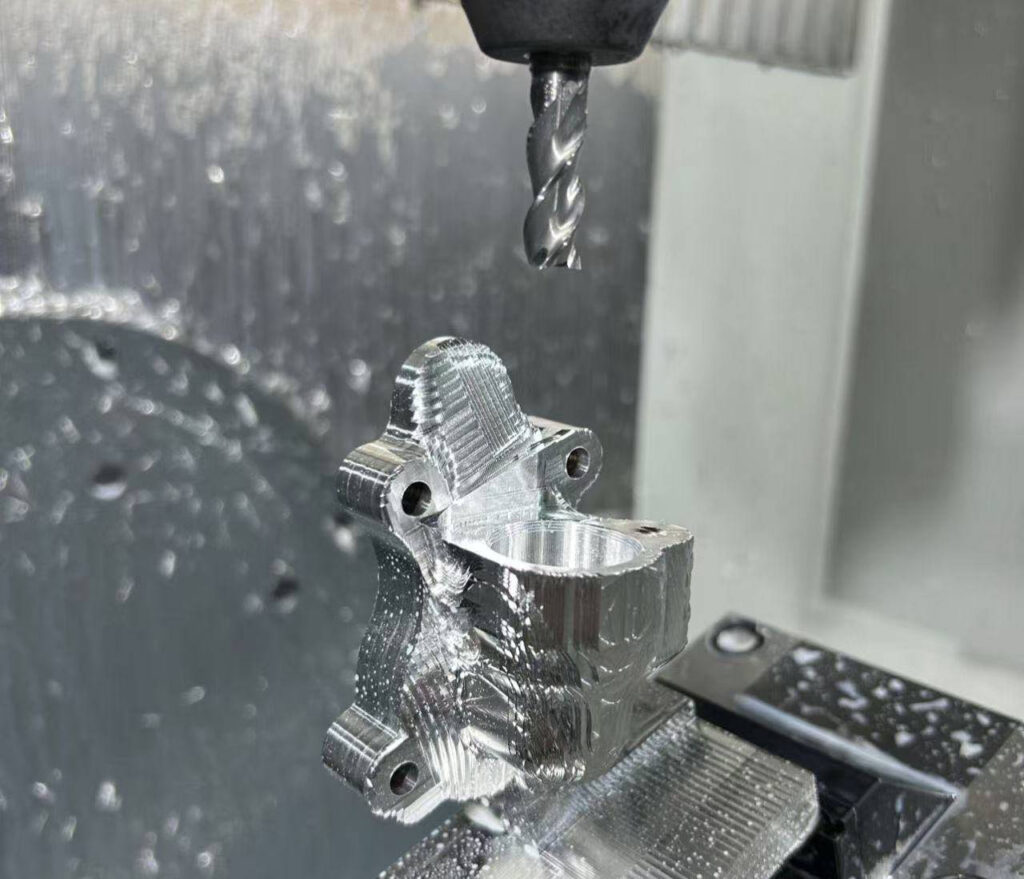
Cnc machining
Development trend
Precision machining is a natural outcome of production technology development. It continues to advance alongside scientific and technological progress. In the new era, the rise of industrial automation, artificial intelligence, nanotechnology, and new energy technologies has injected fresh vitality into the precision machining industry. As a result, machining precision continues to improve. The main development trends are as follows:
1.High precision development trend
With the continued growth of the industrial market, machining products now face higher quality demands. Among these, machining accuracy is the most critical. High-precision machining improves product performance and boosts production efficiency. It also increases the production capacity of manufacturing companies, helping them gain stronger market competitiveness.
On one hand, precision is gradually improving. The continuous development of the machinery manufacturing industry promotes advances in precision machining technology. Machining accuracy is moving toward micron and sub-micron levels. In the future, development will follow a transition: from ordinary processing, to precision machining, and then to ultra-precision processing. Accuracy will improve from 1μm to 0.01μm, then to 1nm, and even reach 0.1nm.
On the other hand, process integration is becoming more important. Facing fierce international and domestic competition, machining and manufacturing companies focus on improving production efficiency and product quality. In precision machining, a trend has emerged called “grinding instead of research” or even “grinding instead of throwing.” This means using one machine to perform multiple processes such as turning, drilling, milling, grinding, and finishing. The use of such multifunctional equipment is becoming increasingly common.
2.Intelligent development trend
The current big data technology, artificial intelligence technology in the industrial field has been widely used, the traditional production process gradually transitioned to full automation and intelligent machining, further optimising the form of the process and improving the efficiency of production operations.
For example, intelligent numerical control machine tools (CNC), industrial robots laser welding and cutting are the development trend of precision machining.
These precision devices have been widely used in the aerospace manufacturing field, satellite communications field, shipping and shipbuilding industry, medical devices, intelligent automobile manufacturing field, etc., and have become a core part of the enterprise to cope with international market competition.
3.Development trend of customisation
Customization will be a key trend in the future of mechanical parts processing. Intelligent mechanical parts processing will expand into aerospace, shipping, robotics, rail transportation, electric power, new energy, agriculture, and many other industries. As a result, CNC parts processing will face more diverse and complex demands. The need for customization will become increasingly important.
At the same time, customised precision machining is also the key to maximize customer satisfaction, improve the accuracy of machining services.
4.Large-scale and miniaturisation trends
Based on the growth of emerging special industries, precision machining must meet diverse production and assembly needs. There is a trend of simultaneous development in large-scale precision machining and miniaturization. For example, processing large optoelectronic devices in aviation, aerospace, and astronautics requires establishing large-scale ultra-precision machining equipment to meet production demands.
And processing of home appliances, micro-electronic machinery, optoelectronic information and other areas of micro devices, but the need to use micro ultra-precision machining platform.
According to the processing needs of flexible selection of appropriate precision machining equipment and technology is to ensure industrial product quality, maximise to meet the needs of the times the key to development.
5.Green development trend
The traditional crude industrial economic development model, resource consumption for economic development, environmental damage for efficiency, leading to increasingly serious ecological problems, threatening the harmonious development of man and nature.
With growing ecological awareness, people began exploring models that balance economic development and environmental protection. Using advanced technology to replace traditional processing methods ensures efficient and reasonable resource use. This led to the emergence of the theory of “green processing and manufacturing.”
Nowadays, ecological and environmental protection has become a global problem, ‘green manufacturing’, ‘sustainable development’ is the focus of the entire industrial sector to consider, green machining manufacturing will become the future direction of development.
The introduction of the most advanced machining technology, the use of environmentally friendly new materials, clean new energy, processing new technologies can further reduce production pollution, reduce resource waste, energy saving and emission reduction, and promote the harmonious unity of economy and ecology.
Common green machining technologies and processes such as: MQL lubrication quasi-dry cutting technology, ion beam coating technology and environmental protection surface coating technology, water jet processing technology, air-cooled cutting technology.
Conclusion
Precision machining technology is the source power to promote the deepening development of the machinery manufacturing industry, is the core kinetic energy of the industry 4.0 era, the future of precision machining technology will continue to develop in the direction of high precision, intelligence, customisation, green.
Mechanical processing manufacturing industry economic subjects should recognise the development situation, accelerate the transformation of business management concepts, keep up with the trend of the times, and constantly improve their own precision machining technology, to produce more high-precision mechanical parts, so as to obtain a larger market production space.