In modern manufacturing, the demand for high-precision and complex-shaped parts is increasing, which places higher requirements on processing technology. As a cutting-edge manufacturing technology, 5-axis machining has completely changed the traditional machining method with its unique multi-axis collaboration capabilities.
Compared with traditional three-axis machining, 5-axis machining can not only achieve more complex geometries but also greatly improve processing efficiency and part quality. From aerospace to medical devices, 5-axis machining is used everywhere, and its advantages in high-precision manufacturing are obvious.

What is 5-axis machining?
5-axis machining is an advanced CNC technology that achieves high-precision cutting of complex parts by simultaneously controlling five degrees of freedom (X, Y, Z axes and two rotation axes) of the workpiece and tool. This multi-axis collaborative motion allows processing to be performed from multiple angles, significantly improving processing flexibility and accuracy. Compared with traditional three-axis processing, it can complete more complex parts in one clamping, significantly shortening processing time and reducing costs. Error.
By using 5-axis machining technology, the manufacturing industry can achieve the production of more complex geometries and precision parts. It can effectively handle processing tasks such as complex curved surfaces, inclined surfaces, and deep cavities. It also improves tool life and processing efficiency, making the production process more efficient and economical. 5-axis machining not only creates a new era of machining capabilities but also provides strong support for high-precision and high-performance manufacturing needs.
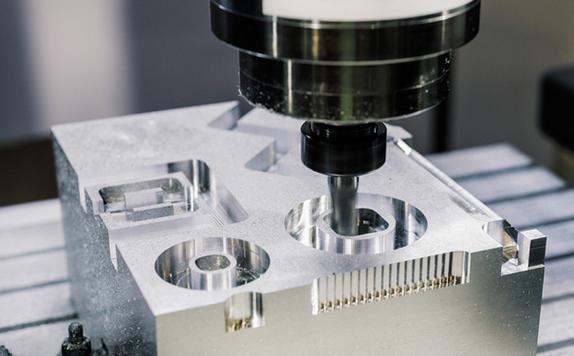
Why use CNC for 5-axis machining?
Using CNC for 5-axis machining has significant advantages because this technology enables precise control of five degrees of freedom on the CNC machine tool, including three linear axes (X, Y, Z axes) and two rotary axes. With these five axes working together, engineers and machinists can machine up to five sides of a workpiece in a single operation, enabling the manufacture of highly complex parts.
5-axis CNC machining brings significant benefits to manufacturers. It significantly shortens manufacturing time and reduces production costs because multi-faceted processing can be completed in a single clamping. This technology improves machining accuracy and ensures products are brought to market faster. The specific type and configuration of CNC machine tools will directly affect their processing speed and direction, further affecting overall production efficiency.
How do 5-axis CNC machines work?
5-axis CNC machines enable complex part processing by controlling five degrees of freedom—three linear axes (X, Y, Z) and two rotary axes (A, B)—for coordinated movement, allowing the tool to contact the workpiece from multiple angles. The CNC system controls these movements to achieve precise, complex shaping.
In actual operation, the workpiece is fixed on the workbench, which can rotate around one or two rotational axes, while the spindle can move along three linear axes. With the cooperation of these movements, the tool cuts the workpiece from different angles and completes multi-faceted processing tasks in one clamping. This multi-axis collaboration capability greatly improves processing flexibility and efficiency and is suitable for manufacturing complex parts and high-precision components.
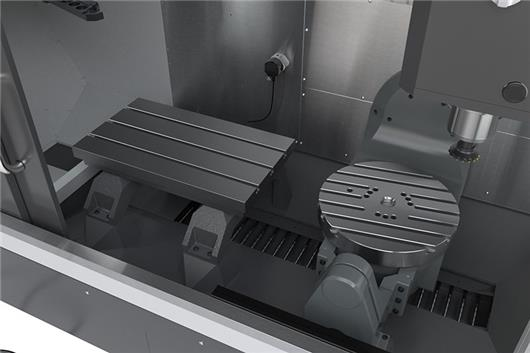
Advantages of Shaft CNC Machining
1. Improve processing accuracy
5-axis CNC machining reduces errors by allowing the tool to contact the workpiece from multiple angles, improving accuracy and consistency, especially for complex, precision parts.
2. Reduce processing time
5-axis CNC machining reduces clamping times by processing multiple faces and complex shapes in one setup, saving time and minimizing errors, thus improving efficiency.
3. Reduce workpiece deformation and clamping errors
By completing multiple facets in one setup, 5-axis CNC machining can reduce workpiece movement and deformation during machining. This integrated processing method avoids errors that may occur in traditional clamping and ensures the consistency and accuracy of parts.
4. Machining complex geometries
5-axis CNC machining handles complex geometries, such as curved surfaces, inclined surfaces, and deep cavities, that traditional methods can’t achieve. It makes manufacturing complex molds, aerospace parts, and medical devices more feasible and efficient.
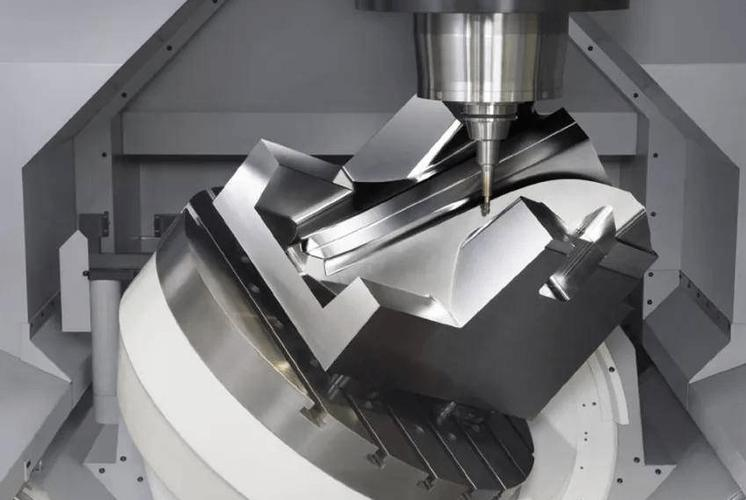
5. Improve surface quality
5-axis CNC machining reduces lateral forces, improving surface finish and quality while minimizing the need for further machining.
6. Improve tool life
5-axis machining can optimize the cutting angle of the tool, and reduce unnecessary wear and load, thereby extending the service life of the tool. This not only reduces tool costs but also reduces downtime and increases productivity.
7. Enhance flexibility and adaptability
5-axis CNC machine tools can handle a variety of materials and part shapes and are highly adaptable. This flexibility suits various manufacturing needs, offering efficient solutions from low-volume production to complex projects.
8. Reduce manual intervention
The automated 5-axis CNC system reduces manual reliance, and human error, and enhances production stability and consistency.
Conclusion
5-axis machining has greatly enhanced the precision, efficiency, and capability to process complex parts, making it a key technology in high-end manufacturing. With advancements in CNC technology and machining centers, it will continue to drive the industry’s progress.