History of the Industrial Revolution
The Industrial Revolution is the starting point of modern civilization, marking a fundamental change in human production. Each industrial revolution has driven tremendous social, economic, and technological progress. Below is an overview of the four industrial revolutions:
1. The First Industrial Revolution – The Age of Steam
At the end of the 18th century, the first industrial revolution began the “Age of Steam.” Steam power boosted factory production, and machines replaced manual labor.
2. The Second Industrial Revolution – Electrical Age
At the start of the 20th century, the second industrial revolution ushered in the “electrical age.” Widespread electricity use boosted production efficiency and mass production.
3. The Third Industrial Revolution – Digital Control Era
In the mid-20th century, computers and programmable controllers enhanced both human strength and brain power. Digital control made machines more independent, transforming the relationship between humans and machines. This marked the third industrial revolution of automation, making manufacturing electronic and more flexible.
Industry 4.0 – The Fourth Industrial Revolution
Entering the 21st century, the rapid development of the Internet, new energy, new materials, and biotechnology is driving a new industrial revolution. This revolution is creating vast industrial capacity and markets, raising global production to a new level.
The German Academy of Technical Sciences (ACDTECH) and others introduced the “Industry 4.0” strategy to secure Germany’s manufacturing competitiveness and lead global industrial trends. Its core is the deep integration of information-physical systems, marking a shift from previous industrial revolutions.
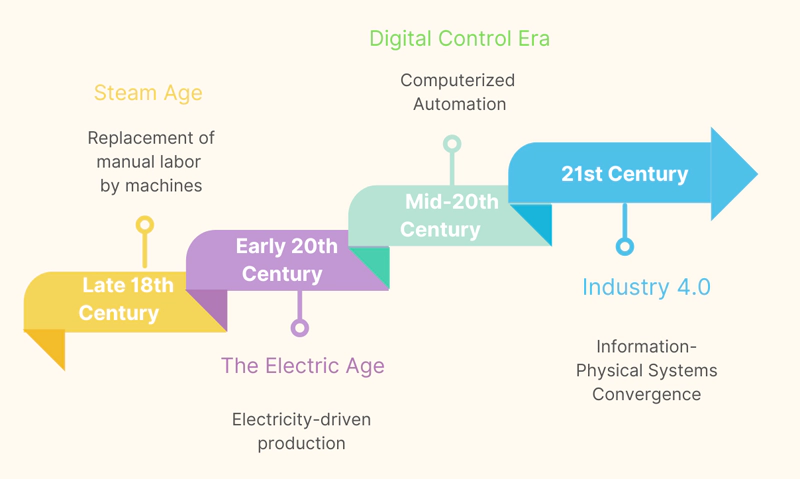
Fig. 1 Characteristics of the Four Industrial Revolutions
Information-physical fusion system
In the modern Internet age, almost all physical products made of atoms are inseparable from bits (data). These products may feature a barcode, be computer-designed, display working status, or even connect to the Internet of Things. Market competition shows that products lacking software or with minimal software have lower value and competitiveness.
1. The combination of bits and atoms
Even though the software itself may be “free”, the value of the hardware increases dramatically. For example, the iPhone and iPad, designed in California and made in China, are priced 1/3 for hardware and 2/3 for software and smart features. The value of software has made Apple the world’s richest company, while Foxconn earns low profits at the expense of workers’ health and the environment.
This phenomenon shows that product innovation and profitability cannot be achieved without the combination of atoms and bits. This combination constitutes the Cyber-Physical System (CPS) in which “human-machine” and “machine-machine” communicate with each other. The popularization of smart products depends on the continuous development of this system.
The future application of the CPS model
In the next decade, the CPS model will become a key component of industrial and urban development. Here are a few application scenarios:
(1) CPS factories and intelligent robots
The CPS model factory, consisting of intelligent machine tools, intelligent robots, and inte, and intelligent logistics, will become the mainstream of the manufacturing industry. Through the collaborative work of these intelligent systems, the productivity and flexibility of factories will be greatly enhanced.
(2) Smart Grid and Decentralized Energy
Decentralized smart power generation devices (e.g. wind power) will constitute the CPS mode smart grid. Through the smart grid, the distribution and utilization of energy will be more efficient and precise.
(3) Construction of Smart Cities
CPS systems in various industries and different fields will work together to build the digital smart cities of the future. These cities will be based on IoT technology to realize the intelligence of infrastructure, resource environment, municipal management, medical care, security, economy, and industry.
3. Pilot and Future Prospects of Smart Cities
China has launched smart city pilots in Beijing, Shanghai, and Tianjin, connecting infrastructure, resources, public services, and people’s lives via the Internet and IoT to enhance urban management.
As information and communication technologies advance, sensors and smart devices will be widely used across industries. These devices will be embedded in environments like power grids, transportation, buildings, and factories, forming a massive IoT system. The IoT will then integrate with the Internet through supercomputers and cloud computing, merging human activities with physical systems.
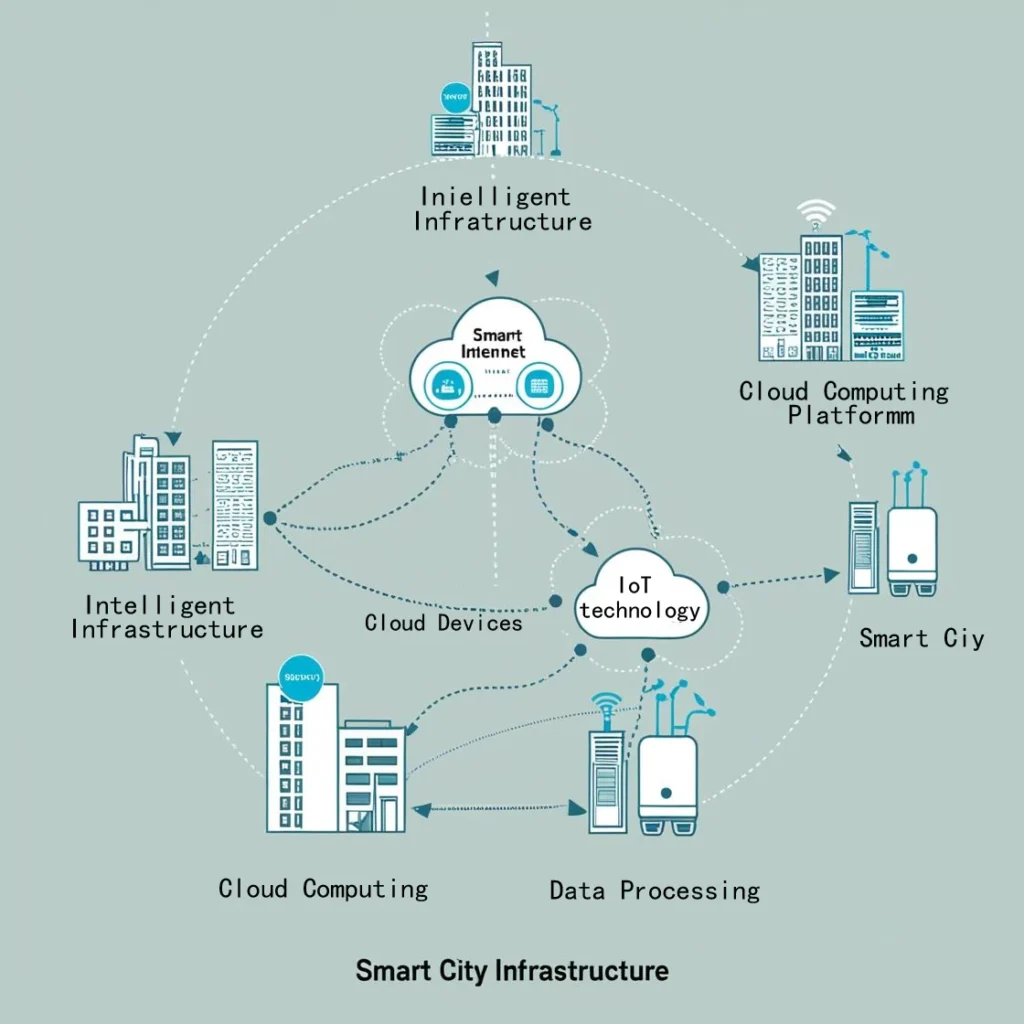
Fig.2: Smart city based on Internet and IoT
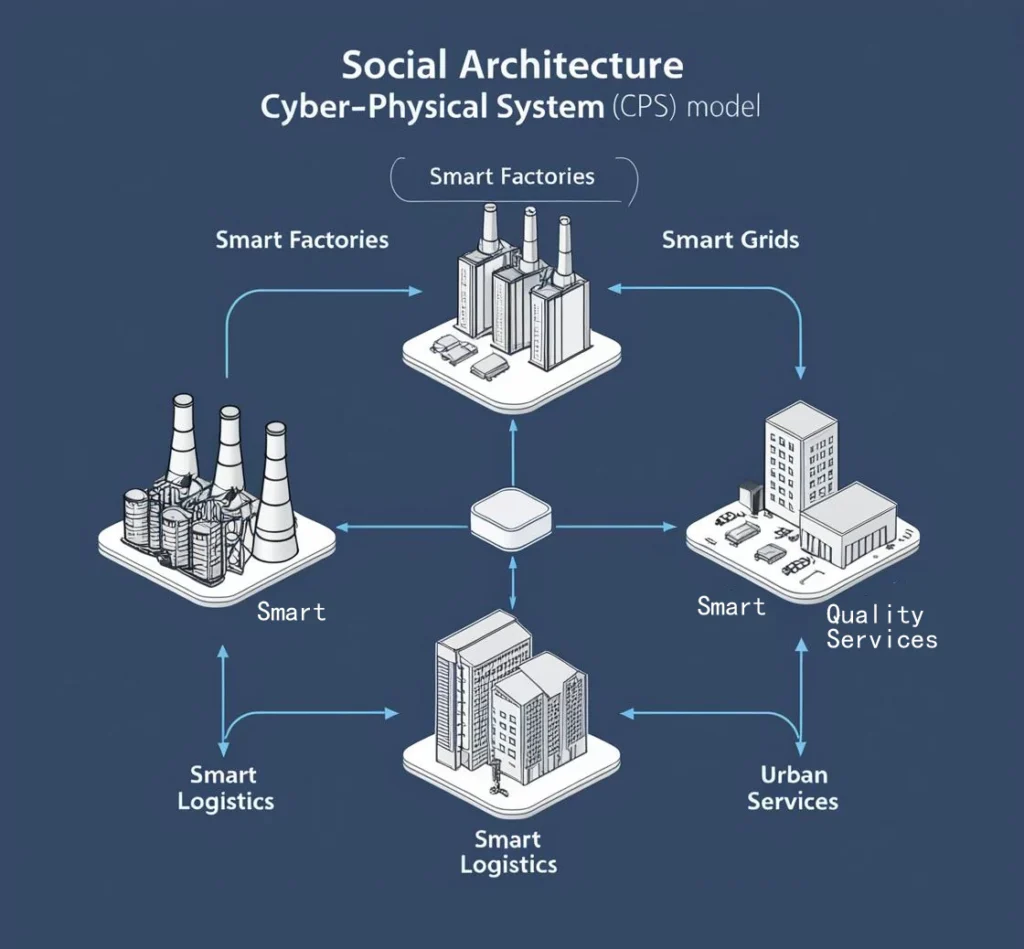
Fig.3: Social architecture based on the CPS model
Tomorrow’s Manufacturing: Smart Factory
Industry 4.0 represents the transformation and change of industrial technology, and the proposed smart manufacturing is oriented to the whole life cycle of products and realizes informationized manufacturing under the condition of ubiquitous perception. Intelligent manufacturing technology is based on modern sensing technology, network technology, automation technology, and artificial intelligence, through perception, human-computer interaction, decision-making, implementation, and feedback, to promote the product design, manufacturing process, as well as the intelligence of enterprise management and service, is the deep integration of information technology and manufacturing technology.
1. The difference between intelligence and automation
The biggest difference between intelligent manufacturing and traditional automated manufacturing is the content of knowledge. Intelligent manufacturing relies on scientific knowledge rather than experience alone. Scientific knowledge provides the basis for intelligent manufacturing. Therefore, intelligent manufacturing includes not only material handling processes, but also involves non-material handling, and contains a perfect material supply chain and a strong knowledge supply chain. Through the support of industry-university-research alliances alliances gett manufacturing can continuously promote the transformation and upgrading of industries and develop new products with high added value.
2. Sustainable Intelligent Manufacturing
Intelligent manufacturing is a sustainable manufacturing model. It optimizes the product design and manufacturing process through the potential of computer modeling, simulation, and ICT, thereby significantly reducing the consumption of material resources and energy, and reducing the generation of waste. At the same time, intelligent manufacturing also realizes the recycling of resources, reduces emissions, and protects the environment.
3. Information Physical Production System (CPPS)
Based on the conception of Industry 4.0, the smart factory will be composed of physical systems and virtual information systems, forming the Cyber-Physical Production System (CPPS).
As can be seen from the figure, the production process of the physical system is controlled and managed by a virtual information system, which acts as the “soul” of the physical system. The physical system and the information system interact with each other through the mobile Internet and the Internet of Things. Therefore, a smart factory is not necessarily limited to a physical workshop within a wall. It can utilize idle social equipment scattered in different places through the network to form a “global localized” factory. Just like shopping on Taobao, consumers don’t need to know the exact location of the store, they can just place an order and the goods will be delivered quickly.
This new production model will promote the business model, management model, and enterprise organization model, as well as the demand for talent has changed dramatically.
4. Separation of product design and production
Today, product design and production are often separated, whether for large aircraft or small cell phones. In the future, information technology and networks will further optimize the design and production processes, improving resource organization and efficiency.
A smart factory’s production environment includes smart products, equipment, a pleasant workspace, skilled workers, and intelligent energy supply, all communicating internally. This includes data collection, work condition analysis, and manufacturing decisions. Multiple smart factories, connected via middleware, cloud computing, and services, will form a vast manufacturing network. Intelligent logistics will optimize the entire system, enabling global production integration.
5. The elemental conditions for building a smart factory
To build such a decentralized and networked smart factory system, there must be certain basic conditions, including the following five elements:
Intelligent production and products: Utilizing advanced information-physical fusion equipment to producehigh-value-addedd intelligent products combining software and hardware.
Real enterprise environment: the current transformation and upgrading path and planning of enterprises.
Macro and microeconomic environment: industrial policies and market demand support.
Human factors: a new generation of managers, technicians, workers, and other high-quality talents.
Technical factors: including the security and reliability of network and communication infrastructure, intelligent production technology, etc.
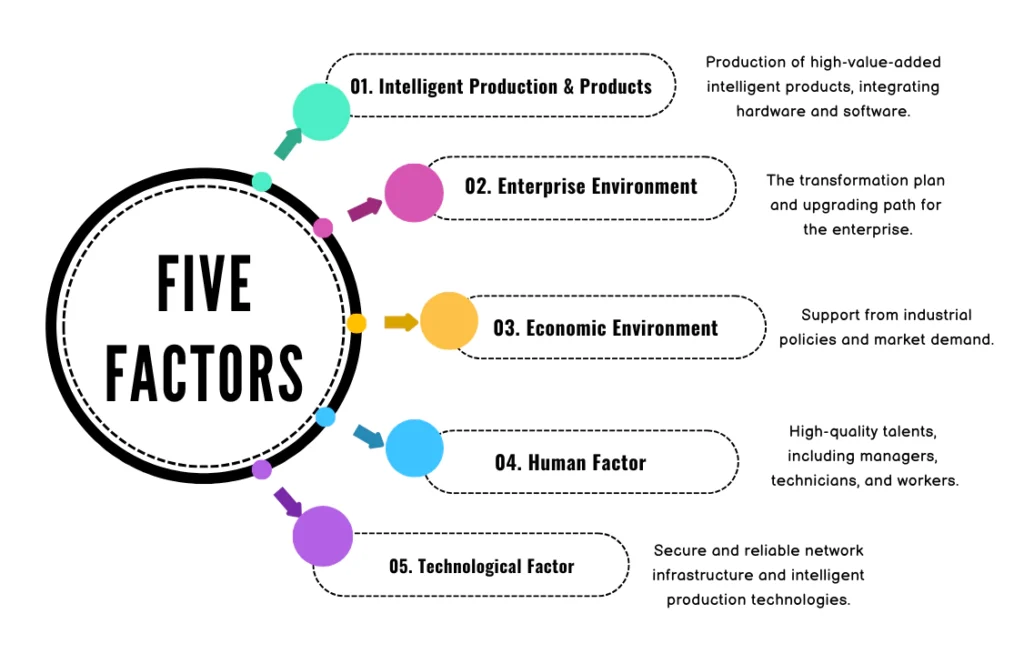
Fig.4: Component conditions of intelligent factory
Synergistic operation of information-physical systems
The determining factors that enable synergistic operation between different information-physical fusion systems include:
Semantic compatibility: information between different applications must be semantically compatible to communicate with each other.
Real-time sensors and actuators embedded in the system: the physical environment needs to be equipped with real-time sensors and actuator systems.
Network embedded “system of systems”: connecting different subsystems through a network.
Adaptive and cooperative: all systems need to be adaptive, locally autonomous and have cooperative and distributed control systems.
Human-machine cooperation: extensive human-machine cooperation and collaboration.
Smart Factory Demonstration Projects
The Industry 4.0 project proposes a demonstration project for smart factories and uses the production of liquid products (e.g. washing liquids) as an example. This project consists of two main stages: liquid preparation and liquid filling. In the production process, different liquid products are prepared by mixing different components, and the filled products need to use different color caps and labels to indicate the ordering information and sending destination.
1. Application of wireless network and RFID technology
A wireless network covers the entire production system and radio frequency identification (RFID) technology is widely used. The application of these technologies makes the production process more efficient and precise. In the control mode of intelligent equipment, the human-machine interface will change significantly. With the improvement of network performance such as WiFi broadband and Bluetooth proximity communication, networked mobile control methods based on tablet PCs, cell phones and wearable devices will become increasingly popular.
2. Innovation of human-machine interface
With the progress of technology, touchscreen n, seen, and multi-touch graphical human-macinterfacesrface will gradually replace the traditional buttonsswitchce mic,e, and keyboards. Especially for young people, have become accustomed to the operation of intelligent electronic consumer products, able to respond quickly, switch the screen, and upload or download data. This new type of interaction not only enriches the content of human-computer interaction but also greatly reduces the incidence of misuse.
3. Deep integration of information and physics
In the operation of smart factories, information is more important than matter. Machines are not only production tools and equipment but also nodes of the factory information network. They not only extend human physical strength but also expand human brain power. Machines are capable of recognizing workpieces, interacting with people, and operating according to control programs programmed by people.
Machines and devices (things) can connect and communicate through the network, sensing real-time changes in equipment and the environment. They collaborate to complete tasks, creating an intelligent workshop based on the Internet of Things.This deep integration of information and physics is the basis for the efficient and flexible operation of smart factories.
How far away from us?
The smart factory may seem distant, but it’s already in development worldwide. Major companies are racing to gain a technological edge, and intelligent manufacturing is becoming a reality, shaping the future of manufacturing.
1. Intelligent forerunner
For example, Ningxia small giant machine tool company is the pioneer of intelligent information management. The company integrates data from product design, manufacturing, orders, and customer management. It also establishes an intelligent production center, linking the production scheduling system with machining equipment, on-site terminals, and tool rooms to ensure smooth production coordination.
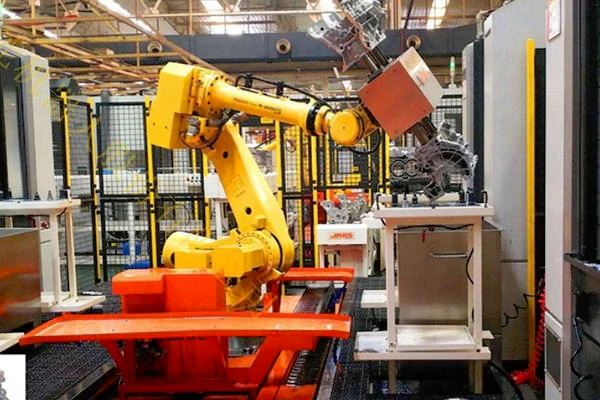
Fig.5: Workshop terminals of Ningxia Small Giant
Through this information platform, staff can view real-time information on assembly tasks, parts supply, and product assembly accuracy, thus greatly improving production transparency and efficiency.
2. Smart factory changes the working environment
Intelligent factories will transform the manufacturing work environment, keeping operators safe. For example, at a U.S. automobile company’s body welding line, workers use tablet computers to remotely control robots, avoiding direct contact with dangerous equipment. This allows for efficient, safe operations and reduces workplace risks.
3. Smart Services: Remote Management and New Business Models
Intelligent management and intelligent services are an important part of smart manufacturing. The smart factory of the future will no longer be confined to the traditional walls and plants, it will be “online in the air”, no matter where you are, you can keep in close contact with colleagues and customers and deal with all kinds of production problems, just like in the office or workshop.
Intelligent services are not limited to remote troubleshooting and tetechnicalupportbalso provide new business models. For example, Germany’s Volkswagen has established an integrated car city (Autostadt) in a picturesque location near its headquarters. This venue integrates multi-functional services such as new car display and delivery, automobile museum, production line tour, five-star hotel, and training, creating a new model of intelligent service integrating 4S service, leisure, and tourism.
Future Manufacturing: Cloud Manufacturing
Manufacturing has entered the era of big data, requiring strong computing power and network infrastructure for intelligent manufacturing. Traditional equipment control and information processing methods can’t meet the growing demand. Based on cloud computing, “cloud manufacturing” has become the future trend. It supports all manufacturing stages by sharing computing resources, including networks, servers, and storage.
1. Cloud Computing for Smart Manufacturing
Cloud computing provides a shared pool of resources for smart manufacturing, connecting production equipment to the cloud via the Internet. Using a SCADA system, local computers send production data to the cloud for processing, storage, and distribution. When needed, the cloud platform can send commands to local equipment to control the production process.
2. From vertical to flat: transformation of industrial structure
With the widespread use of the Internet and mobile communication technology, industrial, economic, and social structures will undergo profound changes. The shift will move from vertical to flat structures and from centralization to decentralization. This transformation will impact the manufacturing industry, especially micro and small enterprises. Increasingly, small businesses are forming alliances online, competing with larger companies and potentially becoming pioneers in intelligent factories.