With the improvement of consumer demand and consumption level, the demand for mold products has also become higher, promoting the prosperity of the injection mold industry.
In order to better meet consumer demand, enhance the enterprise’s own comprehensive competitiveness and strength, enterprises must pay attention to the injection mold in the product design and manufacturing process deficiencies, take measures to make up for and improve.
Also continue to innovate and improve the manufacturing process standardization of products, build a standardized system conducive to the overall production process, and the use of the production process, an effective solution to the conflict between the quality and cost of the production process, to accelerate the overall pace of the injection mold industry exhibition.
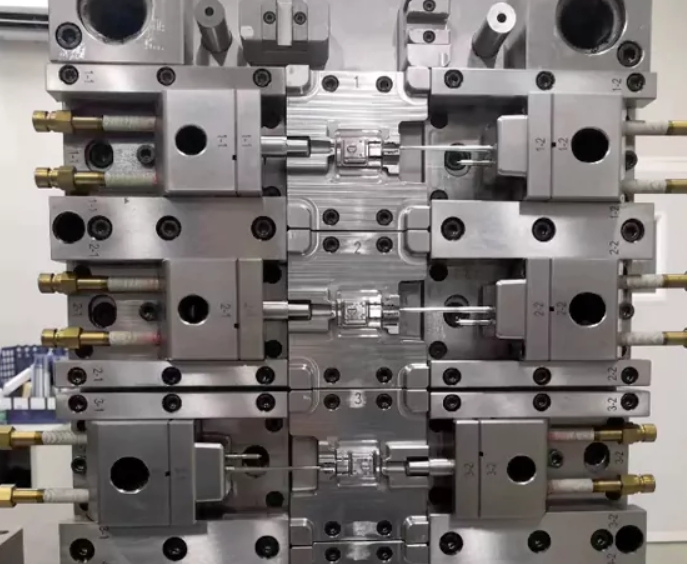
Injection mold design and manufacturing standardization system role
1. Cope with the production process time and quality of the conflict problem
Injection mold industry is currently the most prominent shortcomings manifested in the quality and cost of the conflict. Due to the product in the production process in a general state of hurry, to meet market demand most companies in the product production process are not enough time problems, and time conflicts can not guarantee its quality, easy to cause the situation of the quantity but not the quality.
However, to truly meet consumer demand, the quality of the problem can not be sloppy, must be put in place, so only the injection mold design and manufacturing of the two major aspects of standardization, it is possible to maximize the solution to the conflict between time and quality.
The realization of design and production process standardization can effectively shorten the manufacturing time. Standardizing the design work allows for specialization.
With standardized designs, product manufacturing can use them as an effective reference. Based on the design concept of production and manufacturing, high efficiency in manufacturing can be achieved.
This not only ensures production quality but also reduces production time. As a result, it successfully resolves the conflict between time and quality.
2. Improve enterprise competitiveness, promote enterprise development
2.1 The importance of standardization in a competitive industry
The injection mold industry is highly competitive in today’s rapidly evolving manufacturing sector. To gain an advantage, enterprises must implement standardized systems for mold design and production.
Standardization ensures coordination, establishes technical procedures, and integrates efficient methods into real production processes, improving overall consistency and quality.
2.2 Enhancing efficiency and reducing costs through standardization
A well-structured standardization system provides clear design guidelines, leading to a more systematic and scientific design process. This improves manufacturing efficiency by reducing production time, optimizing workflows, and lowering costs.
Additionally, standardization minimizes quality issues, ensures resource optimization, and enhances the overall production process, helping enterprises boost profitability and competitiveness.
2.3 Strengthening enterprise management and supporting long-term growth
Standardization clarifies responsibilities across departments, enhances collaboration, and ensures an orderly workflow. It simplifies inspections, reduces errors, and improves operational efficiency.
By establishing a well-defined standardization system, enterprises can strengthen their market position, increase competitiveness, and achieve sustainable growth in the industry.
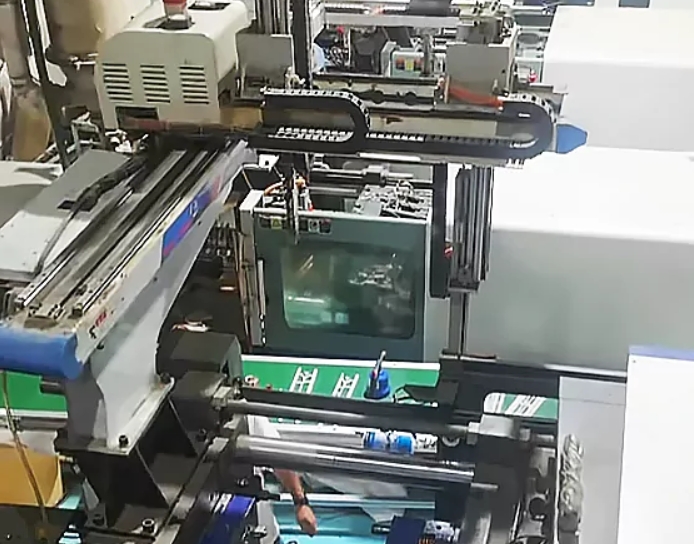
Realize the standardization of injection mold design and manufacture
1. The use of injection molding technology in the design and production of injection molds
Injection molding is now commonly used in plastics processing and production methods, from the end of the 19th century, the technology has been gradually applied, and now has become an important method of plastics processing and production. The method can be applied to the processing of thermoplastics and other thermosetting plastics.
The rational application of injection molding can realize various processing of plastics, molding into different shapes, and realize injection mold processing to meet the requirements of precision and quality. Actively apply this technology to the design of injection molds and product production, can better realize, product manufacturing, conducive to the standardization of product manufacturing.
2. Application of parallel engineering foundation in product design
In recent years, with the rise of parallel engineering, mold production has adopted rapid production as the standard mode. To meet tight deadlines, mold enterprises must integrate the concept of “parallel” production into their operations.
This involves coordinating design, production, and later sales across different divisions. By achieving parallelism, companies can further improve their original production methods.
Enhancing the traditional production mode plays a crucial role in improving mold manufacturing efficiency.
For the mold production, the standardized design of the mold is to achieve parallel engineering as the basis for the realization of its standardized design, is conducive to the unification of the database, the file transfer format adjustment, and to achieve the exchange of information and resources, communication and sharing, and promote the production and processing to high-speed, high-quality direction.
3. Achieve a clear division of labor in all aspects, the standardization of process distribution
Enterprises to achieve the standardization of mold design and manufacturing process, you need to make certain standard procedures, so that each department in the production process to do specific, orderly.
(1) In the design process, the design department should receive process design tasks, design work, the design process should consider the operability of the production, design humanization, in line with consumer demand and facilitate the processing operation, the distribution of the design, the steps will be implemented.
(2) After completing the product production, the process department should communicate and exchange with the design department in time to confirm the feasibility analysis of the product production, send the information of the process regulations to the production department, and summarize and analyze the feedback from the production department in time.
(3) After completing the product design and process procedures, the production department should be in accordance with the concept and method of production and manufacturing, in the manufacturing process, if there is a conflict with the design of the initial concept, we should communicate with the design department in a timely manner to feedback, timely solution to the reality of the problem, improve production efficiency.
To achieve standardization of injection mold design and manufacturing technology analysis
1. Product design standardization technology
1.1 Principles of coordination and modular manufacturing
To achieve standardization in injection mold design, it is crucial to maintain coordination and unity in design principles. The design process should be concise and well-defined, with specific requirements.
Additionally, modular manufacturing should be promoted, allowing product manufacturing to become systematic and forming the foundation for standardized design and production.
1.2 Enhancing efficiency and reducing production costs
In production, enterprises must ensure that mold products meet factory requirements while minimizing production time and shortening the production cycle. Improving efficiency is essential for reducing costs.
To achieve these goals, companies must establish a standardized design classification system, providing a structured framework for design and production processes.
1.3 Establishing design classification codes and image databases
A key aspect of standardization is the creation of a design classification code system. This requires the use of the CCSIM system for classification and coding. Additionally, an image database must be established, incorporating fully parametric design to record and analyze mold components.
By utilizing technical and dimensional parameters, this database significantly enhances the efficiency and scientific accuracy of the design process.
2. Product manufacturing standardization technology
In addition to the standardization of product design, it is more important to achieve the standardization of the product manufacturing process, product manufacturing determines the quality of the product as well as the use of the effect, because the standardization of the product manufacturing is the injection mold production of the most important.
To achieve the standardization of injection molds first of all need to carry out professional training of employees, employees for professional knowledge of the guidance, so that employees in the production process to master the norms, the correct operating methods, to achieve standardization.
Secondly, to achieve the standardization of production, but also on the product parts and components to carry out a rigorous audit, do a good job of standardization of the selection of parts, to do from the beginning of the parts of the precise, from the precision to improve the standard of production technology.
In addition, it is also necessary to make further efforts in the manufacturing process, do a good job in the formulation of the process, improve production efficiency, achieve cost reduction and revenue enhancement, from the economy as well as production efficiency with the technology to achieve the standardization of technology.
Conclusion
In the increasingly competitive situation of the mold industry, the realization of the standardization of injection mold design and manufacturing can not only achieve product quality improvement, product design is beautiful, and more to meet the needs of consumers, for the long-term development of enterprises and the injection mold industry to provide greater help in the long term.