Ultra-precision machining technology has always kept pace with technological advances to continuously improve machining accuracy and processes. As technology evolves, so does the definition of “ultra-precision”. Currently, the technology usually refers to machining methods that achieve sub-micron size and shape accuracy and nanometer surface roughness (Ra). The range of applications has been gradually extended to the nanometer scale, and the machining precision has approached the atomic level.
Theoretically, the limit of ultra-precision machining is the atomic level, i.e., the surface fluctuation is between 0.1 and 0.2 nanometers, which is called an “ultra-smooth surface”. To achieve this goal, it is necessary to ensure that the physical properties of the workpiece material remain unchanged, to achieve the ultimate shape and dimensional accuracy, and to achieve perfect surface integrity (no defects such as cracks, residual stresses, etc.).
Ultra-precision machining currently includes four areas: ultra-precision cutting; ultra-precision grinding; ultra-precision polishing; and special processing. This article will focus on ultra-precision cutting, grinding, and polishing technology.
What is ultra-precision machining?
1. Ultra-precision cutting
The use of diamond and other super-hard materials as cutting tools for cutting technology can achieve nanoscale surface roughness (Ra can reach tens of nanometers). This technology includes ultra-precision turning, boring, milling, and compound cutting, such as ultrasonic vibration turning.
2. Ultra-precision grinding
Using high-precision grinding machines and ultra-fine-grained grinding wheels to process materials, the surface roughness can be as low as Ra<0.025 μm, while ensuring that the machining accuracy reaches or is better than 0.1 μm.
3. Ultra-precision polishing
Through the mechanical and chemical action of fine abrasive particles, the processing surface precision can reach several nanometers, and the roughness Ra can be as low as the nanometer level. This is currently the most common means of final processing, especially for products with extremely high requirements for surface quality.
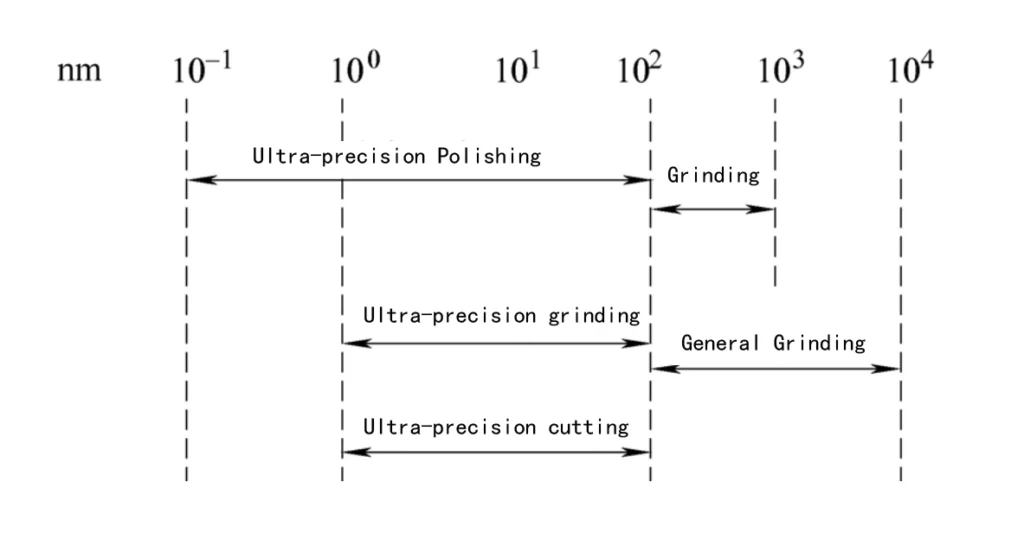
Fig. 1 Accuracy range of current ultra-precision machining methods
Why is ultra-precision machining so important?
Ultra-precision machining technology supports the development of modern high-tech industries [2]. It is widely used in the manufacture of high-performance weapons, semiconductor devices, precision experimental instruments, etc., and promotes the progress of electronics, information, and science and technology. For example, ultra-precision technology is vital to the fields of national defense, aerospace, and nuclear energy, and its application marks a country’s scientific and technological level and comprehensive national power.
Wide range of applications:
Metallic materials: including soft metals, stainless steel, hard alloys, etc.
Non-metallic materials include glass, ceramics, semiconductors, and other hard and brittle materials.
By improving machining accuracy, this technology enhances product performance and quality and promotes miniaturized design and automated production. The interchangeability of high-precision machined parts makes assembly more efficient and energizes modern manufacturing.
Challenges and Development Direction
Although China ranks fourth in the world in terms of manufacturing output, it still relies on imports for high-end machining technologies. For example, in 2003, China imported 4.16 billion U.S. dollars worth of machine tools, including high-grade CNC machine tools. However, the average export price of domestically produced machine tools was only 1/550th of that of imports, showing the technology gap in the field of ultra-precision machining.
In addition, due to the embargo on key equipment and gaps in machining technology, it is difficult to give full play to the potential of advanced equipment even after it has been imported. This exposes the lack of core competitiveness in China’s manufacturing industry and the urgent need to vigorously develop local ultra-precision machining technology.
International vision of ultra-precision machining
Various industrial powers have launched several R & D programs to promote the progress of ultra-precision machining technology:
The United States launched the National Nanotechnology Initiative (NNI) in 2001.
The United Kingdom and Japan have also launched multidisciplinary collaboration and support programs.
These programs are not only helping the industry but also signaling the future of manufacturing as it moves from the macro to the micro.
About the Future
To break away from its dependence on imports, China needs to make efforts in the following areas:
Strengthen research and development of ultra-precision machining equipment and processes.
Enhance local high-end manufacturing capacity, especially in the field of core components.
Promote industrial upgrading with technological innovation to enhance international competitiveness.
Ultra-precision machining technology has become the forefront of modern manufacturing technology, but also the cornerstone of future technology. Through continuous investment and innovation, China is expected to realize a breakthrough in this field and contribute a more powerful force to the global manufacturing industry.
International development status and comparative analysis
1. International development status of this field
Ultra-precision machining development to today has made significant progress, ultra-precision machining is no longer an isolated processing method and purely process issue and has become a systematic project containing a wide range of content.
The main factors affecting the accuracy of ultra-precision machining include ultra-precision machine tools, ultra-precision machining tools (cutting tools, abrasives, abrasives, etc.), ultra-precision machining process, processed materials, fixtures, online testing, and error compensation, ultra-precision machining environment (including constant temperature, vibration isolation, clean control, etc.). Only by integrating the latest technological achievements in each field, it is possible to realize ultra-precision machining.
1.1 International development status of basic research in this field
Ultra-precision machining is embodied in the sum of microscopic deformation or removal of material localized at each machining point. The machining mechanism varies with the machining unit (the range of machining stress action) and the degree of inhomogeneity of the workpiece material (material defects or defects due to machining), as shown in Fig. 2 [3].
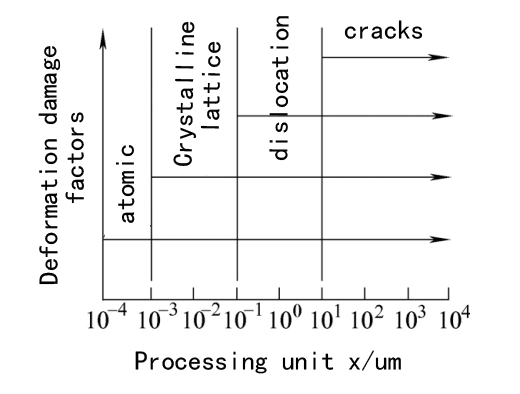
Fig. 2 Deformation damage in different processing units
If an indentation is made on the surface of hard and brittle materials (e.g. ceramics, silicon single crystals, etc.) with a diamond cutting edge, the hard and brittle material undergoes brittle damage, leaving numerous microcracks on the surface of the material. Fig. 3 shows a model of the range of deformation damage caused by indentation[3]. In Fig. 3 rs is the radius of the indentation, Rs is the length of the crack on the surface, and c is the boundary of the elastic deformation range. According to this model, it can be explained why there are not only abrasive marks with cracks in the grinding process of brittle materials but also mixed with some abrasive marks caused by plastic deformation.
However, if the processing unit is reduced during grinding and polishing, then it becomes a destructive way of processing with plastic deformation due to slip. Although plastic domain machining can obtain surface roughness comparable to polishing, the sub-surface damage (e.g., dislocation, slip, etc.) is larger. If the machining unit is further reduced to molecular or atomic level units and machining is realized within the elastic domain of the material, when the chemical properties of the material will dominate the machining, damage-free machining is possible.
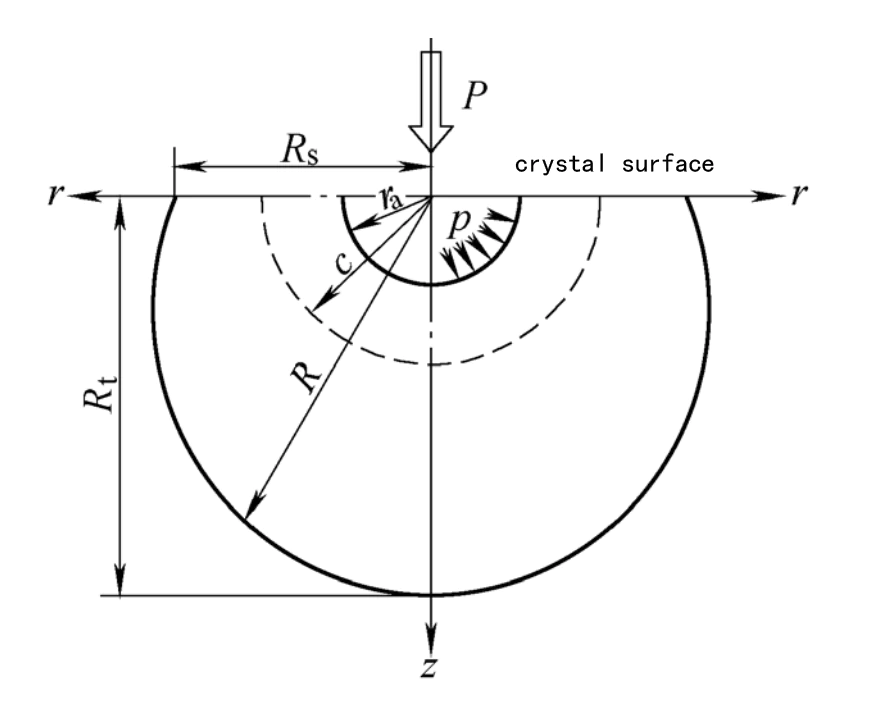
Fig. 3 Modeling of the damage zone for indentation deformation
The study of this machining process leads to the establishment of a theory of nanoscale machining processes to guide the practice of nanoscale ultra-precision cutting and machining. Molecular dynamics simulation is not limited by machining equipment and machining conditions, and the settings of machining conditions, material properties, and tool geometry can be changed as needed.
Therefore, the study of nano-cutting mechanisms based on molecular dynamics has been widely emphasized by researchers. U.S. Lawrence Livermore (Lawrence Livermore, LL) National Laboratory in cooperation with Osaka University in Japan 1986 in the world successfully realized the cutting thickness of a 1nm stable cutting test [4], and in the late 1980s first U.S. scholars began to apply molecular dynamics to simulate the nano-cutting process, and then scholars in other countries such as Japan also Later, scholars from other countries such as Japan carried out research in this area [5].
In China, Harbin Institute of Technology and other organizations have also carried out relevant basic research. However, the current molecular dynamics research on the nano-cutting mechanism is limited by the computational scale, and there are problems such as a small number of analyzed atoms, single object material (mostly ideal defect-free single product material, and very little research on multi-product material), and only limited to the geometric and mechanical properties of the machined surfaces, and so on, which are unable to widely explain the actual nano-cutting machining mechanism reasonably, and are unable to when the machining scale When the machining scale reaches the nanometer level, a series of mesoscopic physical phenomena will be generated.
Such as small scale effect, quantum size effect, etc., at this time and then use the macro cutting principle to describe the machining process and a variety of mesoscopic phenomena, to explain the surface formation mechanism has been incompetent, must be used in molecular dynamics, quantum mechanics, atomic physics, and other recent basic theories to analyze the results of the actual cutting test for comparison.
Therefore, it is also necessary to study the material removal mechanism from the perspective of micromechanics, create a new theoretical system of nanoscale cutting and cutting surface formation mechanism, and establish an accurate theoretical model of nanoscale machining, to realize the theoretical guidance for the actual nanoscale ultra-precision cutting and machining technology.
1.2 International development status of technology and industry in this field
The development of ultra-precision machining has gone through the following three stages.
Technology pioneering period (1950s-80s)
The United States took the lead in developing single-point diamond-cutting technology (SPDT) for aerospace, national defense, and astronomy. The United States United Carbide Corporation, the Netherlands Philips launched the ultra-precision diamond lathe, mainly for copper, aluminum, and other soft metal processing, and the processing workpiece shape is mainly axisymmetric.
Early stage of application (1980s-1990s)
Companies in the United States, Europe, and Japan began to promote the commercialization of ultra-precision machining equipment under the support of the government, widely used in the production of civilian precision optical lenses. At this time, ultra-precision equipment is still scarce and expensive, mainly in the form of specialized machines. The United States also developed a large optical diamond lathe for micro-inch ultra-precision machining.
Maturity (late 1990s to the present)
With the promotion of automotive, medical, information, and other industries, ultra-precision machining technology began to be applied to a wider range of fields, such as optical lenses, molds, disk drives, semiconductor substrates, and so on. The precision of machining equipment is gradually approaching the nanometer level and larger-sized workpieces can be processed, with the emergence of ultra-precision 5-axis milling and fly-cutting technologies.
At present, ultra-precision machine tools, ultra-precision cutting, grinding, and technologies have been increasingly perfected.
(1) Ultra-precision machine tools. Ultra-precision machine tools are the first basic conditions for realizing ultra-precision machining. For cutting and grinding, to realize ultra-precision machining is to realize the ultra-micro removal of materials, in addition to extremely sharp tools or micro-grinding tools, the dynamic stiffness and accuracy of the machine tool and micro-feeding system are very important.
Ultra-precision machine tool technology has now developed into a comprehensive systems engineering, its development makes comprehensive use of the basic theory (including cutting mechanism, suspension theory, etc.), key unit component technology, related functional device technology, tool technology, measurement and test analysis technology, error processing technology, cutting process technology, motion control technology and reconfigurable technology, environmental technology, etc.
Therefore, a high degree of integration of technology has become the main feature of ultra-precision machine tools, and at present ultra-precision machine tools have reached a very high level. Now the United States and Japan have dozens of factories and research institutes to produce ultra-precision machine tools, the United Kingdom, the Netherlands, Germany, and other units in the research and development of ultra-precision machine tools, have also reached a high level.
At present, the main international manufacturers of ultra-precision machine tools are: the United States Moore, Pritec, and Taylor Hopson, these companies occupy the vast majority of the market share. Japan’s Toshiba Machinery, Fujikoshi, Toyota Koki, Fanuc, etc.. Germany’s first generation of Slaughter, Opter is the production of ultra-precision CNC milling grinding and polishing equipment by famous manufacturers.
Currently the highest level of ultra-precision machine tools in the United States, not only do several factories produce small and medium-sized ultra-precision machine tools but also due to the needs of national defense and cutting-edge technology, research and development of large-scale ultra-precision machine tools, the representative of which is the LL National Laboratory in 1983 ~ 1984 developed a successful DTM-3 and LODTM large-scale ultra-precision diamond lathe, the two machines are by far the world’s highest recognized level of large-scale ultra-precision machine tools. These two machines are recognized as the world’s highest level of large-scale ultra-precision machine tools.
Britain is one of the countries that engaged in the research of ultra-precision machining technology at an early stage. The British Cranfield company is famous for its precision machining technology and has produced ultra-precision lathes such as HATC 300, etc. In 1991, the Cranfield company successfully developed a large ultra-precision machine tool of 2.5 mx2.5 m for processing the reflector of X-ray astronomical telescopes, which can be used for precision grinding and coordinate measurement. This is the second organization capable of manufacturing large-scale ultra-precision machine tools to date.
Although Japan’s research on ultra-precision machining technology started late compared to the U.S. and the U.K., in the mid-1970s, it has developed rapidly due to the attention and concerted efforts of all parties concerned and is now basically on par with the U.S. in the production of small- and medium-sized ultra-precision machine tools. Multi-functional and high-efficiency specialized ultra-precision machine tools in Japan to develop better, and promote the development of Japan’s microelectronics and home appliance industry.
(2) ultra-precision cutting technology. The use of micro-cutting can obtain a smooth and processing less metamorphic layer of the surface. Minimum cutting thickness depends on the cutting edge of the diamond tool blunt circle radius, the smaller the cutting edge blunt circle radius, the smaller the minimum cutting thickness. Therefore, the design and manufacture of ultra-precision cutting tools with nanoscale edge sharpness is one of the key technologies to realize ultra-precision cutting.
Ultra-precision cutting tool materials are currently used in natural single-product diamonds. Foreign diamond tool manufacturers are mainly the British company Kanto, and Japan’s Osaka Diamond Industry Co. At present, the highest sharpening level of foreign high-precision circular-edge diamond tools has reached several nanometers.
China has not been able to manufacture high-precision diamond tools with rounded edges, and the blunt radius of the cutting edge can only reach 0.1~0.3 um, and the high-precision rounded edges of the tools used in the production are dependent on expensive imports. Theoretically, the blunt radius of the cutting edge of the diamond tool tip can reach 3nm, but it can’t be measured directly at present.
As diamond tools in cutting ferrous metals such as steel when the wear is serious, so in the ultra-precision cutting of ferrous metals in the ultra-precision cutting process can also be used in high-performance ceramic tools, TN, CBN, diamond-coated carbide cutting tools, and CBN blades, but because of its processing surface quality is not as good as natural diamond, only for the occasions where the surface quality is not very strict.
The future development trend is to use diamond tool material surface modification or composite cutting technology (such as low-temperature cutting technology, ultrasonic vibration cutting technology, etc.) to reduce the wear of diamond tools in cutting ferrous metals.
Microstructure surface cutting processing is a new research direction of ultra-precision cutting, Germany and Japan are currently in the field of research at the international leading level. Germany Fraunhofer Institute of Production Technology with tiny single product diamond tools to process the surface characteristics of the structure of the size of less than 100 um pyramid micro-prism arrays and wall thickness of 1.5 um, high 200 um micro-thin-walled structures, the use of fast servo tool holder is also processed with a micro-reflective surface arrays with the integration of the lenses [6] (Fig. 4).
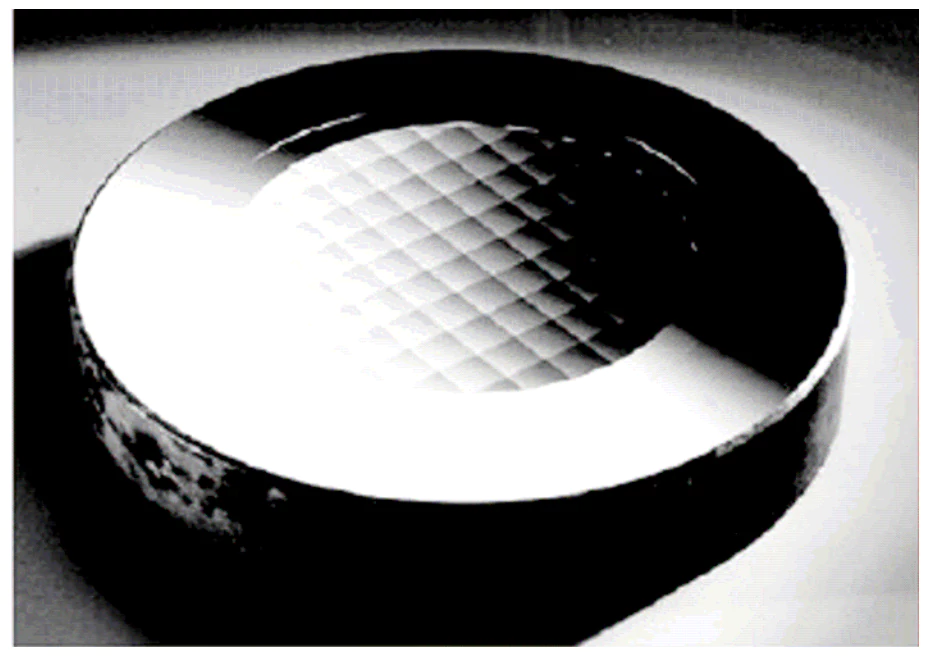
Fig. 4 Integrated lens with micro-reflective surface arrays
University of Bremen, Germany, precision machining laboratory with the tip of the arc radius of 5um tiny single-point diamond tool processing out with a small plane and surface waveform characteristics of the Fresnel lens, as well as with a small sinusoidal structure surface characteristics (amplitude of 5 μm, the period of 100 μm) of the stylus-type surface roughness detector of the calibration of the block molds; they also diamond lathe machining with a two-stage stepped They also used the diamond lathe to process a laser fusion target with a two-stage stepped surface, the height of the steps is 7.5 um, and the diffraction grating and micro prism arrays were processed by the method of flying cutter cutting.
Tohoku University in Japan in a single product diamond lathe mounted fast servo tool holder, machined a tiny sinusoidal grid surface [7] (Fig. 5), can be used as a multi-axis position measurement encoder measurement standard, the surface is in the x and y direction of the sinusoidal superposition of the wavelength of the two directions and the peaks and valleys of the height of the difference between the two directions are 300 um and 0.3 um, respectively [8].
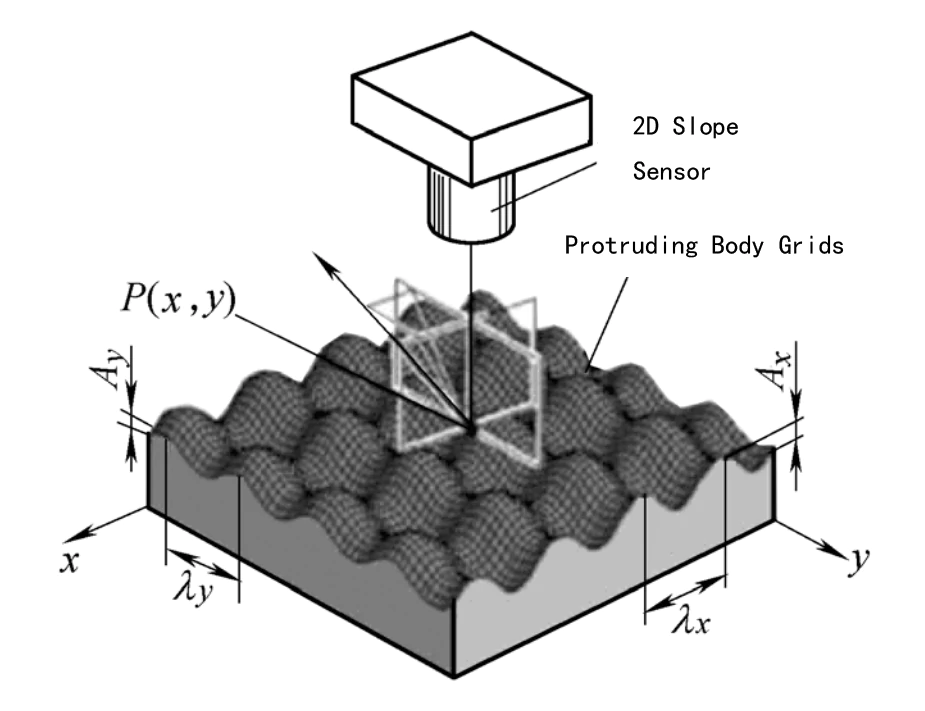
Fig. 5 Surface with tiny sinusoidal lattice
In addition, the manufacturing technology of special diamond tools for microstructure machining is also an internationally competitive research and development technology. These diamond tool manufacturers such as UK’s Kanto Company, Japan’s Osaka Diamond Industry Co., Ltd., and so on have successively carried out the research and development of this kind of tool design and manufacturing process. St. Still, due to commercial confidentiality, very few research reports on the related technology, and China has not yet researched the related technology of micro diamond tools. China has not carried out any research on micro diamond tools.
(3) Ultra-precision grinding technology. Ultra-precision cutting processing technology can be aluminum, copper, and other soft metal optical parts processing to the required accuracy, but ultra-precision cutting is not suitable for processing hard brittle materials. With the continuous development of science and technology, in machinery, electronics, communications, space, optics, and other cutting-edge technology and defense industries, hard brittle materials, high precision, high surface quality parts have been widely used.
Such as single-product silicon wafers, engineering ceramics, optical glass, optical products, sapphire substrates, etc., ultra-precision grinding technology to adapt to the high precision and high surface quality of these materials processing needs and the development of hard brittle materials, ultra-precision grinding can be obtained with a high degree of the mirror surface, has great potential for development. However, because grinding is the role of the face tool and the workpiece, therefore, compared with the single-edged tool, it produces several times or even a hundred times greater grinding resistance. To obtain high grinding accuracy, high-stiffness grinding wheels and grinders are necessary.
For the grinding of hard and brittle materials, a grinding wheel with micro-fine grits must be used to generate tiny cuts, and self-sharpening must be generated to increase the possibility of grit dislodgement. Resin-bonded grinding wheels are better than metal-bonded wheels because the bond is softer and the self-sharpening of the wheel is significantly improved. However, the grinding resistance causes deformation of the grinding wheel surface and deterioration of accuracy. To solve the problem of the high rigidity of the grinding wheel, the use of glass glass-cured micro-fine diamond grinding wheel with air holes and easy chip removal is suitable for high-quality, high-precision grinding.
(Electrolytic in-processdressing, ELID) Grinding technology is a new grinding process proposed by OHMORI et al [8] of the Institute of Physical Chemistry, Japan in 1987, which utilizes online electrolysis to dress metal-based grinding wheels, so that the grinding wheels are always in the optimal grinding condition for continuous grinding processing, thus achieving ultra-precision mirror grinding. ELID grinding process is a good solution to the passivation of metal grinding wheels and dressing problems, to maintain the sharpness of the grinding wheel.
The most important feature is that the ELID technology with coarse grain size can replace the usual grinding technology; the use of 1~10um micro-grains can replace the general ultra-precision grinding and lapping; the use of 0.1~1.0 μm ultra-micro-grains grinding wheels of the ELID technology can be ultra-precision mirror grinding. Now has produced a particle size of 0.5 nm, with iron powder as a bonding agent diamond grinding wheel, grinding surface roughness of 0.5 nm, suitable for grinding fine ceramics, glass, and single product materials.
Ultra-precision grinding requires high precision and rigidity of the machine tool The high-speed rotation of the grinding wheel axis necessitates the use of expensive bearings, and a certain degree of vibration is always unavoidable. The grinding process requires constant dressing of the grinding wheel to maintain the sharpness of the abrasive grains, to prevent the abrasive chips from clogging the grinding wheel burns the surface of the workpiece, chip space and its retention have become the production of ultra-fine abrasive grinding wheels of the main problems; In addition, the grinding process, the workpiece and the grinding wheel is mainly for the line of contact, the processing of unidirectional, it is difficult to ensure that the processing of the surface of the homogeneity of the non-magnetic conductivity of the workpiece clamping difficulties. These problems have limited the surface quality that can be obtained from grinding processing.
If you can control the normal load of a single abrasive grain on the workpiece and make it smaller than the critical load generated by the median radial crack or lateral crack, the workpiece may only have elastic deformation, then the machining of no subsurface damage can be realized or plastic domain machining. However, since the critical load of a median radial crack is much smaller than the critical load of a lateral crack, the plastic processing of ceramic materials, although it is possible to obtain a high surface quality, inevitably there will be large processing of the deterioration layer (nonpinched layers, dislocations, plastic deformations, etc.), the depth of which is about a few micrometers to a few tens of micrometers. That is, with the use of 0.01 um diamond abrasive ELID processing of monocrystalline silicon wafers, the surface roughness can reach Ra 2.8nm, but there is still 1μm of processing deterioration layer.
Ibaraki University, Japan, ZHOU et al [9] with 1 ~ 3 mm CeO2, the phenolic resin grinding wheel (abrasive grain volume fraction of 70%) on single crystal silicon chemical-mechanical grinding (Chemical mechanical grinding, CMG), compared with the CMP processing of monocrystalline silicon wafers, the surface roughness and flatness is similar (CMP: Ra 0.76 nm, P – V5.22 nm; Ra: Ra 0.76 nm, P-). V5.22 nm; Ra 0.79 nm, P-V 5.42 nm), but no processing deterioration layer (CMP after the damage layer of 3 nm). The principle of CMG is that, in the dry processing state CeO2, a solid-phase reaction with Si occurs, the hardness of CeO2, between Si and the reaction products, CeO2, abrasive grains can be removed from the reaction products without forming damage to the workpiece.
At present, the application of soft abrasive grinding technology for thinning silicon wafers with a thickness of less than 50 mm is being studied. Therefore, it can be said that CMG is based on chemical action in the elastic domain to realize ultra-precision processing, from this point of view, based on the principle of soft abrasive solid-phase reaction of ultra-precision processing can be classified into the category of elastic domain processing.
Determining the amount of micro-grinding technology is the use of high stiffness, high precision, high stability machine tools, through precise control of the depth of cut of the grinding wheel, grinding speed, feed, as well as the relative vibration between the grinding wheel, and the workpiece and other parameters, reduce the uncertainty of the grinding process, reduce the surface of the workpiece surface of the sub-surface damage, to achieve high precision, high surface quality, and high-efficiency machining. Initially proposed by the Optical Research Center of the University of Rochester in the United States, is divided into rough grinding, semi-fine grinding, fine grinding, and the other three stages of grinding, the surface roughness of its molding can reach the root mean square value of RMS 3 nm, superior to the quality of the grinding process, the processing efficiency of the traditional grinding efficiency of several times.
In recent years, some Japanese scholars according to the electrophoretic deposition (Electrophoretic deposition, EPD) principle, the use of ultra-fine abrasive grains of electrophoretic properties of the production of grinding wheels feasibility of a large number of studies, that this method can effectively solve the traditional manufacturing of grinding wheels produced by the micro-fine abrasive easy to agglomerate, poor homogeneity, no porosity, easy to whole piece of the shortcomings of the shedding and so on. Japan’s Junichi Ikeno use of this method of silica abrasive grinding wheels on single product silicon, sapphire substrate grinding test obtained Ra 0.6 nm of ultra-smooth surface.
Some Japanese companies have been able to produce particle sizes of 1.3 um, 1.0 μm or finer grain size of the ceramic bond diamond grinding wheel (usually made into a pill in the installation of the substrate to form the abrasive tool), and in the field of silicon wafers, sapphire substrate ultra-precision grinding field has been popularized and applied to the processed silicon wafer surface roughness Ra <20 nm.
(4) Ultra-precision polishing technology. To ensure the performance of electronic and optical devices made of various functional ceramic materials, it is necessary to carry out ultra-smooth and non-destructive processing of their surfaces. The non-destructive surface polishing technology of crystalline materials is a method of micro-excision processing of materials with a processing unit that does not destroy the crystalline structure of the polar surface layer [10].
The mechanical action of the abrasive micro powder with the polishing disk plays a direct influence on the surface roughness of the workpiece. Only by minimizing each mechanical action, it is possible to ensure that an ultra-smooth workpiece surface is obtained. Any elastic material on the surface of the polishing disk can be regarded as an abrasive fixture, the softer limiting substances should be water or gas. Elastic emission machining (EEM) and floating polishing is the gas or liquid as an abrasive fixture, which can be polished to minimize the mechanical action. The processing deterioration layer that occurs in polishing is caused by the mechanical action of the abrasive grains and the friction action of the polishing disk.
Such as the mechanical role of the small liquid grinding method, chemical mechanical polishing, EEM, floating polishing, and other polishing methods can be realized without damage to the processing. In particular, EEM and floating polishing, micro-fine abrasives in the workpiece surface when the role of a shallow scratch is only atomic or molecular level of orderly processing. If atomic or molecular chips are formed from the processing surface, they have to be analyzed and studied by introducing quantum mechanical theory.
At present, the polishing process in the removal of material units has been in the nanometer or even sub-nanometer scale, in this processing scale, the processing area atmosphere of the chemical action of the polishing process can not be ignored part [11].
Physical action and chemical action composite processing methods [1]have become an important development direction of ultra-precision machining technology. For example, in the polishing of optical glass, the mechanical action of oxide abrasive grains produces a soft metamorphic layer, resulting in a high material removal rate. Chemical-mechanical polishing of silicon wafers (Chemical-mechanical polishing, CMP), the processing fluid on the surface of the silicon wafer to generate a hydrated film, can reduce the processing of the occurrence of the metamorphic layer. Therefore, the result of the chemical reaction during the process is favorable for the removal of material and the reduction of the process deterioration layer. Dry chemical-mechanical polishing of sapphire is carried out using a quartz glass polishing disk and 0.01um diameter SiO2 grains in the dry state. An interfacial solid-phase reaction occurs between the abrasive grains and the sapphire, resulting in aluminum-rich rhodochrosite, which is then stripped from the sapphire surface by the friction of the glass polishing discs to achieve the polishing process.
Over the past 30 years, many scholars have developed a series of ultra-precision polishing methods without processing metamorphic layer and surface damage (without disturbing the atomic arrangement of crystallization) using various principles or methods. These ultra-precision polishing methods, such as processing conditions are properly controlled, and polishing surface roughness can reach sub-nanometer level. The most widely used and mature technology is CMP technology.
YASUNAGA et al [11] proposed and verified the concept of CMP by polishing sapphire with SiO2, polishing single product silicon with BaCO3; CeO2 and CaCO3; polishing quartz with Fe203; and MgO and obtaining nm-level surface roughness of polished surfaces.CMP processing through the abrasive particles – the workpiece – the machining environment of the mechanical and chemical interaction between the realization of the workpiece material micro-removal, and can obtain ultra-polished surface roughness. CMP processing through the mechanical and chemical interactions between abrasive particles – workpiece – processing environment, to achieve the micro-removal of the workpiece material, can obtain ultra-smooth, less / no damage to the processed surface; processing trajectory shows multi-directional, conducive to the processing of the surface of the uniformity and consistency of the processed process, the processing process to follow the principle of “evolution”, without the need for high-precision machining equipment. Because CMP technology can provide the comprehensive flattening required for the manufacture of ultra-large-scale integrated circuits, it has become one of the leading technologies in the semiconductor industry and is constantly expanding its application areas.
(1) Ultra-precision non-destructive polishing. Ultra-precision non-destructive polishing is a processing method that removes trace amounts of material in a processing unit that does not destroy the crystalline structure of the pole surface layer. According to the processing state, non-destructive polishing can be regarded as a mechanical and chemical action, and their combination forms a variety of polishing methods. These methods can be categorized into mechanical micro-removal polishing, chemical polishing, and chemical-mechanical compound polishing. Mechanical micro-removal, mechanical polishing is limited to the area of abrasive action (Fig. 6). Its polishing effect depends on the hardness of the processed material and abrasive grains, the shape of the abrasive grains, polishing disk to maintain the performance of the polishing agent and other physical characteristics.
Chemical polishing (chemical corrosion polishing, disk chemical polishing), is a soft polishing disk on the chemical solution for corrosion polishing. Its biggest advantage is that there is no deformation damage layer, but the disadvantage is that there is a corrosion damage layer, the need for a special process to remove the chemical etching agent and surface corrosion damage layer. For porous materials such as cast iron, sintered materials, chemical etching solutions, and chemical corrosion layers that will enter a certain depth of the surface layer, removal is extremely difficult. Chemical-mechanical composite polishing with the help of mechanical energy exerted by the role of causing physical and chemical changes in the surface of the processed material, there are solid-phase reactions of the dry mechanical-chemical polishing, but also in the mechanical action and then apply the chemical action, with the help of frictional heat in the processing and the local stress strains, and by the processing fluid to promote the chemical action of the wet chemical-mechanical polishing.
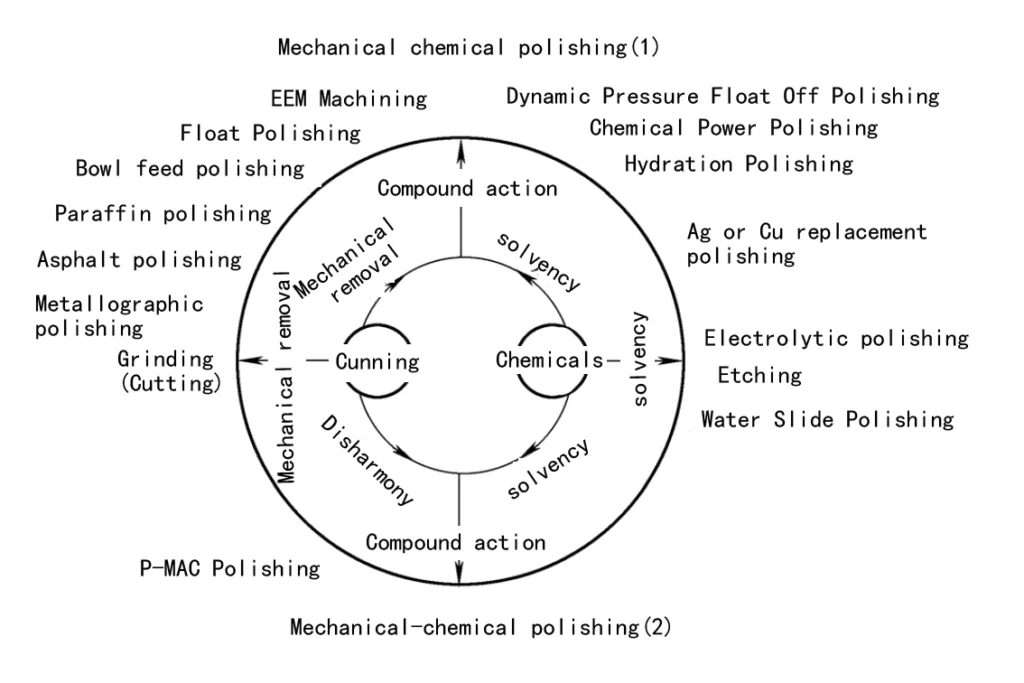
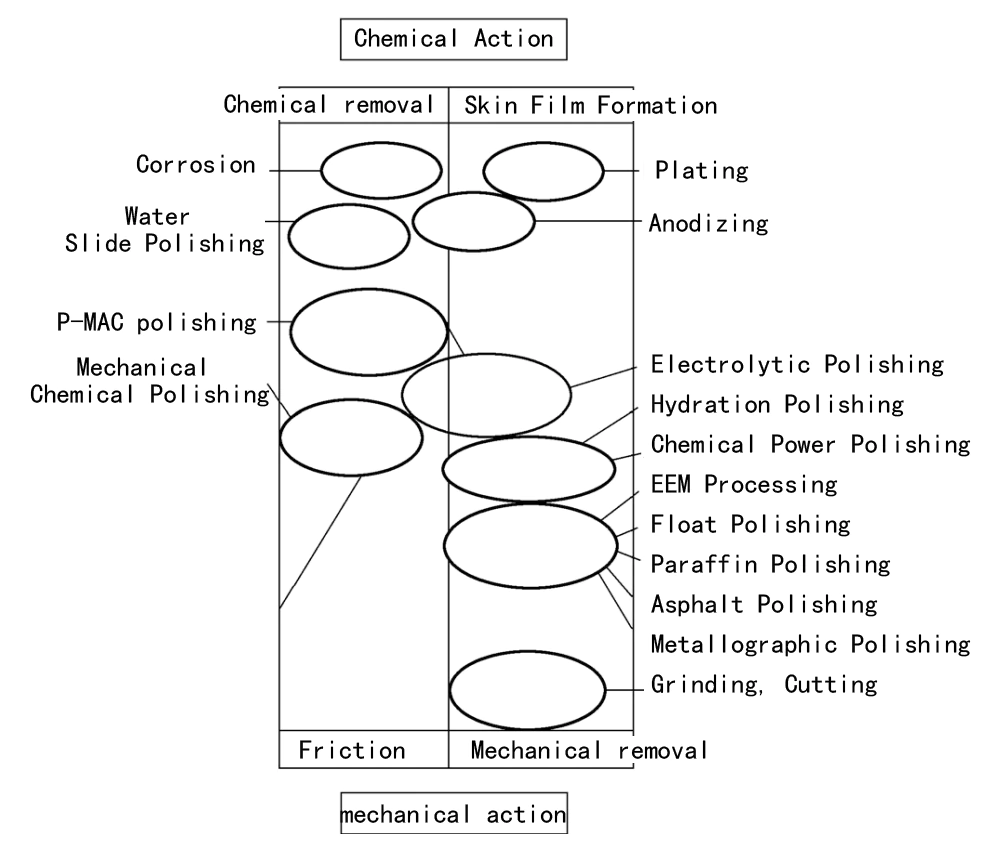
Fig. 6 Classification of the processing principle of various polishing methods
In Fig. 6, the mechanical action is trace removal and friction, and the chemical action including electrolytic action is dissolution and film formation. For example, electrolytic compound polishing for stainless steel mirror processing. With an aqueous solution of sodium nitrate, a nonconducting chemical film is formed by electrolytic action and then processed by the rubbing action of the fixed abrasive and the free abrasive. Even more extreme is the chemical polishing method that does not use abrasives at all.
Such as progressive mechanical and chemical polishing (Mechanical and chemical polishing, P-MAC), its mechanical action through the polishing disc friction to obtain, the removal of material through the chemical solution of the polishing fluid to carry out the P-MAC polishing can be automatically realized in a process from the mechanical action to the transfer of chemical action. The etching effect of the final stage of the layer of the polishing solution leaves the surface completely free of the processed metamorphic layer. When this method is used for mirror processing of CaAs substrates, a surface roughness of Ra 0.3 nm can be obtained using bromomethanol polishing solution.
(2) non-contact polishing. Non-contact polishing refers to the workpiece and polishing disk in the polishing does not occur in contact, only with the polishing fluid in the micro-particle impact on the surface of the workpiece, to obtain the processing of the surface of the perfect quality and precise shape, removal amount of a few to dozens of atomic level polishing method. Take EEM as an example, as shown in Fig. 7, in the micro-particle suspension, so that the polyurethane ball processing head while rotating close to the surface of the workpiece, the micro-particles with a nearly horizontal angle and the collision of the processed material to complete the process.
The action area of the fine particles is very small (φ1~2 mm), and the maximum shear stress is generated close to the surface of the material, so that the dislocations and defects within the substrate do not move (plastic deformation), and a small amount of elasticity can be damaged to remove the process. If the machining head and table for polyurethane balls are equipped with numerical control, curved surfaces can be machined.
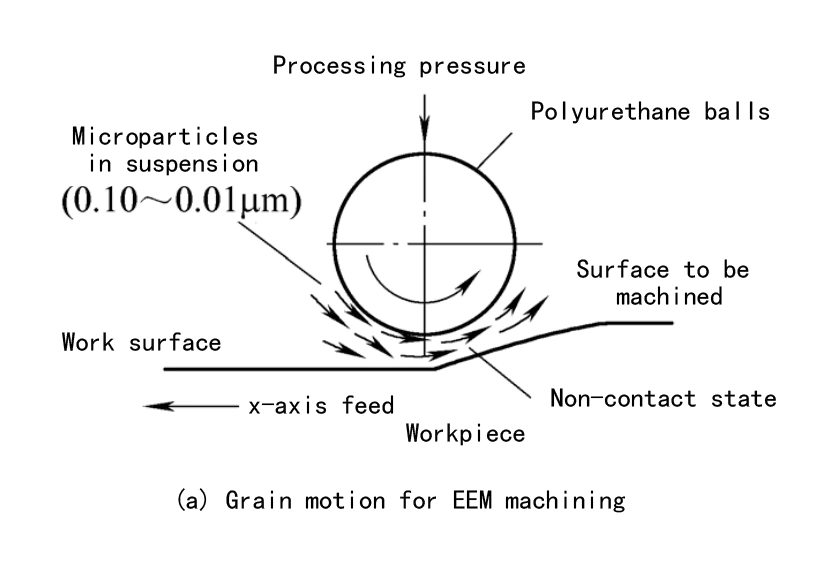

Fig. 7 Schematic diagram of EEM machining principle
- suspension 2. polishing liquid container 3. center of gravity 4. infinitely variable motor 5. polishing headstock connection mechanism 6. bed for polishing headstock fixing 7. polishing head cage 8. polishing head 9. workpiece 10. retaining ring 11. workpiece fixture CNC table 12. load tray
Non-contact polishing can be used for both functional crystal material polishing (focusing on crystalline integrity and physical properties), can also be used for polishing optical parts (focusing on surface roughness and shape accuracy).
(3) Interface reaction polishing. In the past, the processing of hard and brittle electronic functional ceramic materials was the use of hard abrasive particles of mechanical indentation, scribing action-based grinding, and polishing. Usually left on the surface of the workpiece processing deterioration layer. To eliminate the processing of the deterioration layer, the general use of chemical polishing and electrolytic polishing processing will cause the shape of the precision to be reduced. To overcome these drawbacks, new polishing methods must be developed to achieve high-precision and high-quality polishing processing of functional ceramics.
In the friction interface between the workpiece and the abrasive part of the mechanical energy is converted into thermal energy, so that the interface of the real contact parts of the high temperature and high-pressure state, in this state of the interface, is unstable, the substances can easily penetrate each other, the compound is easy to produce and decomposition. This interface reaction is generally known as a mechanochemical reaction. If the reaction product control in the surface layer of the workpiece within a very small depth (generally only a few), because its processing unit is very small, it can be in the case of the parent material without injury to the case of the mother material to make it off, you can get the general machining absolutely can not reach the ultra-precision surface. This is an interface reaction polishing method that generates localized soft products that are easy to remove while processing.
Interfacial reaction phenomena that can be used for polishing are mechanochemical solid-phase reaction and hydration reaction phenomena, and the corresponding polishing methods are called mechanochemical polishing and hydration polishing. These new methods are completely different from the traditional polishing method in terms of processing mechanisms. The accuracy of the processed surface shape is improved by eliminating the need for elastic polishing discs. Due to the use of chemical reactions, the formation of processed metamorphic layers is minimal. Interfacial reaction polishing is likely to become the main method for ultra-precision processing of functional ceramic component substrates. So far, the possibility of using this new method has been demonstrated for sapphire, crystal, silicon, etc.
(4) Electric and magnetic field-assisted polishing. Electricity, magnetic field-assisted polishing (Field-assisted fine finishing, FF), or field polishing is by controlling the strength of the electric and magnetic fields to control the force of abrasive grains on the workpiece, the processing method of polishing. Magnetic field-assisted polishing mainly includes magnetic abrasive processing, magnetic fluid polishing, and magnetorheological processing of three kinds. Magnetic abrasive processing and magnetorheological processing will be introduced in the next section, magnetic fluid polishing has two types of suspension and separation, the former will be mixed into the magnetic fluid abrasive particles, through the magnetic fluid in the magnetic field under the action of the ‘floating’ effect of polishing: the latter abrasive particles are not mixed into the magnetic fluid, but the use of magnetic fluid to the direction of the strong magnetic field to the movement of the characteristics of the direction of the abrasive particles through the rubber and other elastomers extruded abrasive. Rubber and other elastomers to squeeze the abrasive, polishing the workpiece. Electric field-assisted polishing mainly refers to electrophoretic polishing, which uses the colloidal particles in the electric field under the action of electrophoresis phenomenon for polishing.
(5) Surface ultra-precision polishing. Ultra-precision polishing is also used in a large number of final finishing of surfaces, various optical lenses, and mirrors final finishing, generally uses ultra-precision polishing, so that can be processed Ra 2 ~ 10 nm mirror. Manual polishing efficiency is very low and is not easy to ensure the geometric accuracy of the surface, so foreign countries have developed a variety of precision surface polishing machine tools. This kind of precision surface polishing machine tool, has a precision online measurement system, in the machine tool to detect the geometric accuracy of the processed workpiece, according to the measured error to continue the polishing process. Processed surface mirror, not only the surface is a high-quality mirror while having very high geometric accuracy.
The United States for the processing of large optical mirrors, specially developed a large precision 6-axis CNC polishing machine. Fig. 8 shows a large-scale CNC precision polishing machine developed by Canon Japan. The polishing machine table for x and y direction movement, and can be rotated, the polishing head can automatically control the amount of downward processing. After the workpiece is polished at the front of the machine, it can be moved to the back of the machine, where there is a precision probe that measures the geometric accuracy of the workpiece. The z-direction vertical movement of the probe has air guides and an optical measuring system to ensure the accuracy of its measuring movement. The frame and seat are made of low-expansion cast iron and the whole machine is supported by air vibration isolation pads to prevent vibration.
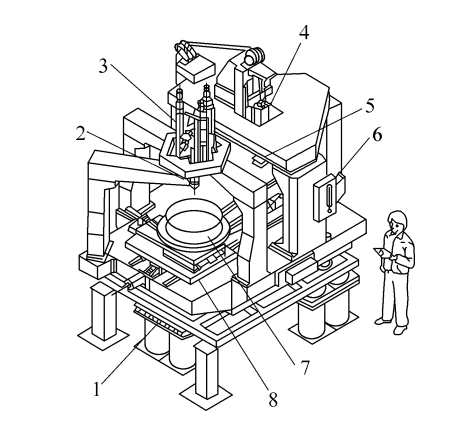
Fig.8 Precision surface polishing machine
- Air vibration isolation pad 2.Polishing head 3.Polishing head lifting mechanism 4. Z-direction air guide 5.Measuring head 6. z-direction optical measurement 7. working table 8. xyθ working table
In recent years, the emergence of new surface grinding and polishing methods are magnetic abrasive processing, magnetorheological processing, airbag polishing, stress disc polishing, and several others.
(1) Magnetic abrasive processing (Magnetic abrasive finishing, MAF) is the use of magnetic abrasive particles (made of abrasive particles and iron powder by mixing, sintering, and then crushing to a certain particle size) on the surface of the workpiece grinding and polishing processing methods. Processing in the workpiece and magnetic poles filled with magnetic abrasive particles, as shown in Fig. 9, magnetic abrasive particles in the magnetic field under the action of the magnetic lines of force along the formation of the ‘brush’, through the workpiece and the magnetic poles of the relative motion of the completion of the processing. The characteristics of magnetic abrasive processing can be summarised as follows.
① It is almost not restricted by the geometric shape of the workpiece, and can grind and polish various surfaces such as planes, cylinders, inner surfaces of round tubes, outer spherical surfaces, complex curved surfaces, inner surfaces of necked gas cylinders (inner spherical surfaces), etc.;
② It does not require high equipment accuracy and rigidity, and does not have the vibration or tremor problems of traditional precision equipment;
③ There is no rigid contact between the abrasive particles and the workpiece surface, so even if there are a few large abrasive particles or uneven hard spots appear on the workpiece surface by chance, the workpiece surface will not be scratched due to sudden changes in cutting resistance;
④ The cutting edge of the magnetic abrasive particles is constantly replaced during processing, and has a self-sharpening function;
⑤ The processing pressure can be determined by the magnetic field intensity controlled by the excitation current, and the entire processing process can be fully automated;
⑥ It can generate residual compressive stress on the workpiece surface and improve the fatigue strength of the workpiece. However, the main problem is that the preparation process of magnetic abrasive particles is complicated and therefore costly, which limits the application of this method.
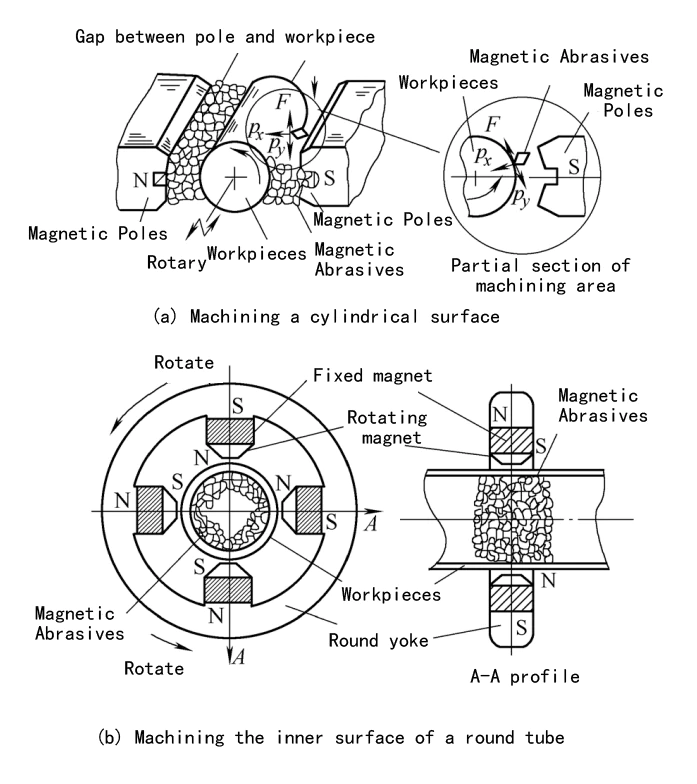
Fig. 9 Schematic diagram of magnetic abrasive processing
(2) Magnetorheological finishingMRF technology was invented in the early 1990s by KORDONSKY and others [12], which uses the magnetorheological fluid (composed of magnetic particles, base fluid, and stabilizer suspension) in the magnetic field of the rheological properties of the workpiece grinding and polishing process.MRF has the advantages of a fluid polishing method, no subsurface damage layer after polishing, small residual stress caused by polishing, obtaining a good ultra-smooth surface, MRF polishing efficiency than fluid polishing MRF has the advantages of the fluid polishing method, no damage layer after polishing, caused by the polishing of the surface the stress small, you can get a very good ultra-smooth surface, MRF polishing efficiency is much higher than the efficiency of the fluid polishing. The rheological properties of the magnetorheological fluid can be controlled by adjusting the strength of the applied magnetic field. The magnetorheological processing equipment is shown in Fig. 10.
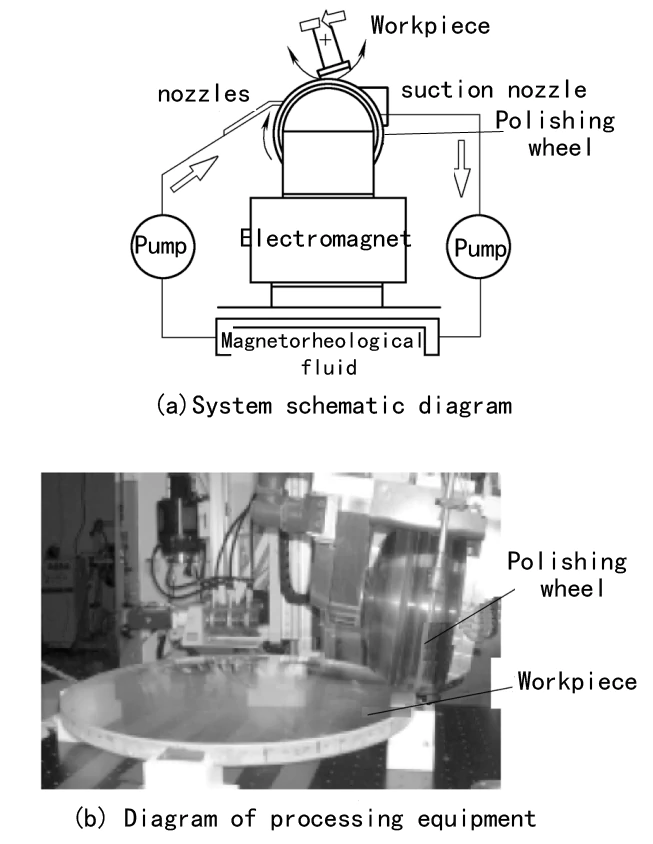
Fig. 10 Magnetorheological processing system
The magnetorheological fluid is sprayed on the rotating polishing wheel by a nozzle, and the magnetic pole is placed under the polishing wheel to form a high gradient magnetic field near the narrow gap formed between the workpiece and the polishing wheel. When the magnetorheological fluid on the polishing wheel is transported to the workpiece and the polishing wheel formed near the small gap, the high-gradient magnetic field so that the cohesion, hardening, viscous plasticity of the Bingham medium (similar to the ‘solid’, the apparent viscosity coefficient increased by more than two orders of magnitude). Bingham medium with a high speed of movement through the narrow gap, the surface of the workpiece in contact with the region generates a large shear force so that the surface material of the workpiece is removed, and leaves the magnetic field area of the medium into a flowable liquid again.
The magnetorheological polishing method can be regarded as a magnetorheological polishing fluid under the action of the magnetic field, in the polishing area within the scope of the formation of a certain degree of hardness of the ‘small grinding head’ on the workpiece to be polished. The shape and hardness of the ‘small grinding head’ can be controlled by the magnetic field in real-time. Magnetorheological polishing is a flexible polishing method, that does not produce a sub-surface damage layer, has high processing efficiency, and low surface roughness, and can achieve complex surface polishing; by controlling the shape of the magnetic field distribution and the residence time of the processing area, it can be realized to determine the amount of polishing.
In 1998, the University of Rochester’s Optical Processing Centre, in cooperation with QED, launched the first magnetorheological polishing machine Q22-X, making MRF technology commercially available. At present, QED produces MRF equipment, the size of the processed parts expanded to 750 mmx1 000 mm, aspheric optics processing accuracy can reach P-V λ/20, surface roughness of 0.5 nm or less, with off-axis aspheric surface processing capabilities.
(2) Liquid jet polishing ( FP) is through a specially designed nozzle containing abrasive particles of liquid shot to the workpiece, relying on the abrasive high-speed impact and flushing to achieve a method of material removal.FIP technology is not sensitive to the polishing distance, so it is suitable for high steepness aspheric surfaces and large aspect ratios of the inner cavity of the complex surface such as deterministic polishing. Liquid jet polishing technology has been commercialized with the introduction of the FJP600 liquid jet polishing machine from Zeeko in the UK.
FJP600 polishes free-form surfaces with surface accuracy better than P-V 60 nm, and surface roughness up to RMS1 nm; Canadian Light Machinery’s water jet polishing machine FJP-1150F can process workpieces with a maximum size of 150 mmx150 mm, with a surface accuracy of ±3 nm, and surface roughness up to RMS 1 nm [14]. Since the liquid stream of the FIP technique is easily disturbed, a new technique, magnetorheological jet polishing (MIP), combining FIP and magnetorheological finishing (MRF), has recently emerged.
MIP technology makes use of the low viscosity magnetorheological fluid under the action of the external magnetic field will occur magnetorheological effect, the apparent viscosity increases to increase the stability of the surface of the jet beam, so that the stability of the magnetic jet polishing is better than the stability of the ordinary liquid jet. OED has already verified the application of the magnetic jet polishing technology in the conformal optics, the use of the MIP technology will be a concave glass (curved surface radius of 20 mm, diameter of 23 mm) to improve the accuracy of the precision. 23 mm) by a factor of 8.
(3) Computer-controlled optical surfacing (CCOS) is one of the technologies commonly used in recent years. The basic idea is to use a much smaller polishing tool than the processed device, according to the results of the optical surface shape detection, computer-controlled processing parameters, and processing paths to complete the processing. At present, many large astronomical observation mirrors around the world are processed using the CCOS method and the stress disc polishing method. As computer-controlled polishing can precisely control the amount of material removed during the polishing process, it greatly improves the processing efficiency, shortens the processing cycle, and increases the yield compared with traditional polishing.
For example, the Steward Observatory Large Mirror Laboratory in Arizona, USA, has successfully applied this technology to process a series of large mirrors, and has successively completed the processing of the 1.8 mf/1.0 VATT primary mirror, the 3.5 m f/1.5 SOR primary mirror, the 3.5 m f1.75 ARC primary mirror, the 6.5 m f/1.25 MMT primary mirror and the 6.5 m f1.25 Magellan primary mirror. Magellan primary mirrors; in 2005, the LargeBinocular Telescope (LBT) 8.4 m f1.14 primary mirror was completed, with a back profile error of only RMS 20 nm.
In 2006, Tinsley polished a sub-mirror (beryllium) of the JWST primary mirror in just over three months, converging from an initial P-V value of 250.57 μm to 22.40 μm, and an RMS value of 49.101 μm to 1.460 um, 41d ahead of the projected completion date. 2.4 m primary mirror: Perkin-Elmer undertook the machining of the first light primary mirror, achieving a final profile of 12 nm RMS. The REOSC Space Optics Fabrication Centre in France successfully machined the 8 m VIT mirror using the CCOS technique, achieving a profile accuracy of 8.8 nm RMS, which is far better than the required 35 nm.
Computer-controlled polishing has become the mainstream of ultra-precision polishing technology, specifically computer-controlled polishing, including CCOS, and SLP.MRF, IBF, BTP, and FJP, etc., foreign countries, such as the Optics Centre of the University of Arizona, the Optical Manufacturing Centre of the University of Rochester, the Itek Corporation, the Tinsley Corporation, the LL National Laboratory, the Eastman Kodak Company, QED, the University of London in the United Kingdom, Zeeko, the French Space Optics Manufacturing Centre, the Russian Vavilov State Optical Research Institute, Germany Zeiss and Japan’s Canon Company, etc. are a large number of computer-controlled polishing technology.
(4) Airbag polishing. Fig. 11 was jointly proposed by the Optical Sciences Laboratory of the University of London and the British Zeeko company in 2000 [13]. Its motion is different from the ordinary computer numerical control polishing, using a unique way into the action, the principle of which is shown in Fig. 12: Into the polishing is a novel polishing method of optical devices, it has a Gaussian shape convergence of the removal function, gyroscopic rotation makes the workpiece in the polishing area at any point to produce different directions of friction, so that the polished texture intricate and cross-sectional, so that the texture of the texture is fine and non-directional scratches, to flexible head The use of a flexible head as a polishing tool and the combination of CNC polishing technology make it easy to process optical devices with high precision and surface quality.
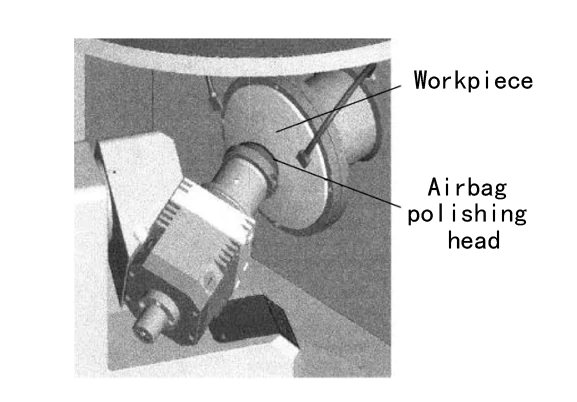
Fig. 11 Schematic diagram of airbag polishing device for curved surfaces
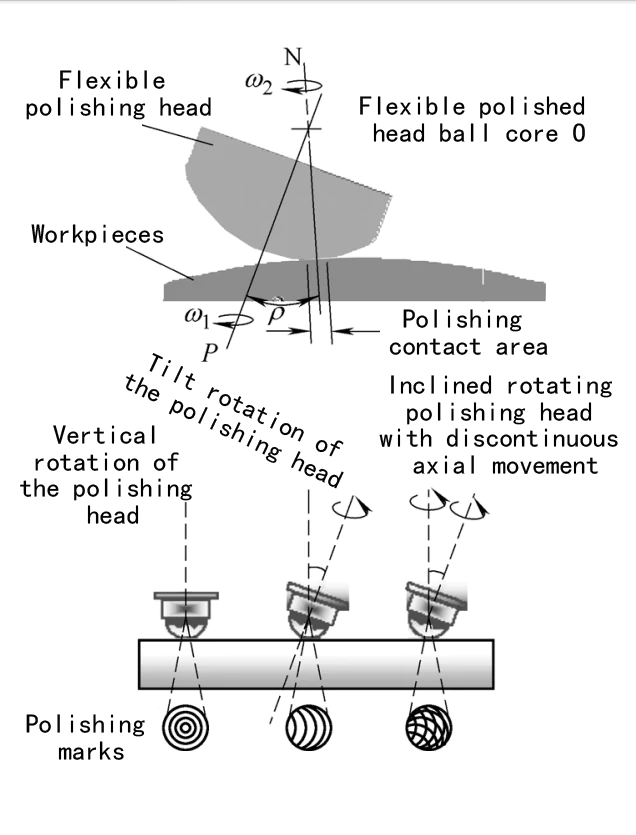
Fig. 12 Principle of airbag polishing
The polishing tool it uses is a special flexible airbag, which has a ball crown shape, and a special polishing mold, such as a polyurethane polishing pad and polishing cloth, which is pasted on the outside. It is mounted on the rotating working part to form a closed cavity, which is filled with low-pressure gas and can control the pressure of the gas. The polishing head itself rotates to create the polishing motion. The workpiece can be rotated and can be x, y, and z direction of the CNC linkage movement. In the workpiece for the surface of the rotating body, the workpiece rotation, and for x, z to the CNC linkage movement; in the workpiece for the free surface, the workpiece does not rotate, and for XYZ to the CNC linkage movement.
To make the polishing head airbag surface polishing die wear uniform, in the polishing, polishing head for a certain swing (but the center of the balloon position remains unchanged). The airbag polishing method is suitable for plane, spherical, aspheric, and even arbitrary surface polishing (quality control) and finishing (face shape control). It is possible to process aspherical surfaces (including off-axis aspherical surfaces), free-form optical surfaces, and so on. It is possible to polish optical glass, nickel-plated aluminum, stainless steel, graphite fiber, and many other materials.
Zeeko company produced the IRP series of multi-axis polishing equipment, processing workpiece caliber from 200 ~ 2 000 mm, face shape accuracy up to P-V80nm, surface roughness up to Ra 3 nm, the rough polishing material removal rate of 2.0 mm3/min, the fine polishing material removal rate of more than 0.25mm3/min.
(5) Stressed-lap polishing (SLP). CCOS processing is a closed-loop control process, the correction of local errors is very effective but prone to local high-frequency residuals (processed surface shape can be viewed as a requirement for the surface shape of the superposition of the residuals of the low, medium, and high-frequency), which has an impact on the quality of the final optical system. For this reason, the emergence of the stress disc polishing method, the method uses a large size elastic disc as a tool base plate, in the periphery of the role of variable stress, the disc’s surface shape can be real-time change into the required surface shape, with aspheric workpiece local surface shape coincides with the grinding and polishing process. Stress disc polishing technology has the characteristic of preferentially removing the highest point or part of the surface, and tends to smooth the middle and high-frequency difference, which can well control the appearance of middle and high-frequency differences and effectively improve the processing efficiency[15].
Stress disc surface shape control of a way as shown in Fig. 13, the stress disc is equipped with 12 drives, and linkage devices around the 12 drives are divided into 4 groups, each of which constitutes a group of three equilateral triangular distributions, each drive is equipped with a point of impact and force sensors, 4 groups of equilateral triangles combined force can produce the required bending moment and torque. Under the action of 12 variable moments, the stress disc can produce the required deformation.
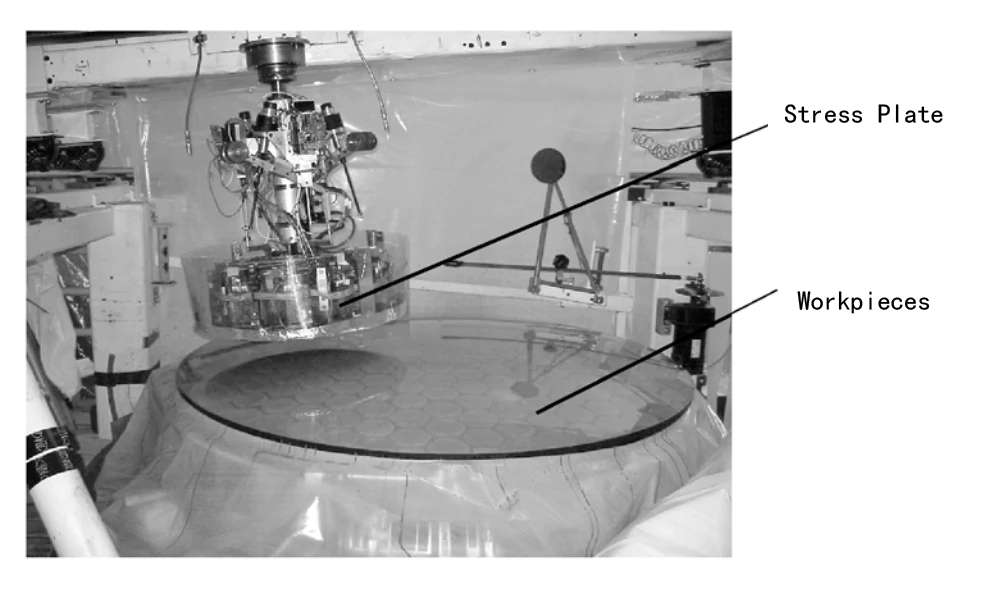
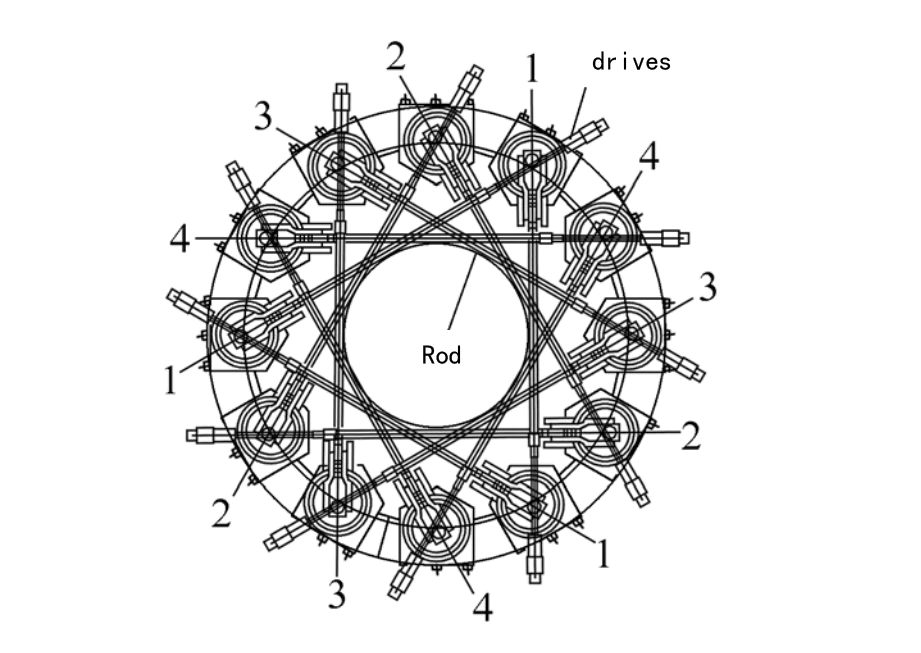
Fig. 13 Stress disc polishing equipment and stress disc realization
References
- [1]YUAN Julong. Ultraprecision machining of functional ceramics[M]. Harbin: Press of Harbin Institute of Technology,2000.
- [2]YUAN Zhejun,WANG Xiankui. The technology of precision machining and ultra-precision machining[M]. 2nd ed. Beijing: China Machine Press,2007.
- [3]Editing Committee of Microfabrication Technology. Microfabrication technology [M]. Beijing: Science Press,1983
- [4]IKAWA Naoya,SHIMADA Shoichi. Accuracy problems in ultra-precision metal cutting [J]. Journal of the Japan Society of Precision Engineering,1986,52(12):2000- 2004
- [5]SHIMADA S. Feasibility study on ultimate accuracy in micro-cutting using molecular dynamics simulations[J]. Annals of the CIRP,1993,42(1):91-94.
- [6]WECK M, KLOCKE F. Manufacturing and applications of non-rotationally symmetric optics[J]. SPIE,1999, 3 739:94-107.
- [7]GAO W. Precision nano-fabrication and evaluation of a large area sinusoidal grid surface for a surface encoder[J]. Precision Engineering,2003,27:289-298.
- [8]OHMORI H, NAKAGAWA T. Mirror surface grinding of silicon wafers with electrolytic in-process dressing[J]. Ann. CIRP,1990,39(1):329-332.
- [9]ZHOU Libo,JUN S,HIROSHI E. A novel fixed abrasive process: Chemo-mechanical grinding technology[J]. International Journal of Manufacturing Technology and Management,2005,7(6-7):441-454.
- [10]KASAI Toshio, DOY Toshiro. Grinding, lapping, and polishing technologies under nanometer-scale working conditions [J]. Journal of the Japan Society of Precision Engineering,1993,59(4):559-562.
- [11]YASUNAGA N, OBARA A, TARUMI N. Study of mechanochemical effect on wear and its application to surface finishing[J]. Res. Electrotech. Lab.,1977,776:50-134.
- [12]KORDONSKY W I, WILLIAM I, PROKHOROV I V. Magnetorheological polishing devices, and methods: US,5449313 [P]. 1994-04-15.
- [13]WALKER D, BROOKS D, KING A, et al. The precessions’ tooling for polishing and figuring flat, spherical, and aspheric surfaces[J]. Opt. Express,2003,11(8):958-964.
- [14]WANG J. Abrasive waterjet machining of engineering materials[M]. Switzerland: Trans. Tech. Publications Ltd.,2003.
- [15]MARTIN H M, ALLEN R G., BURGE J H. F Fabricaction of mirrors for the Magellan telescopes and large binocular telescope [J]. Proceeding of SPIE,2003,4 837:1-10.