In today’s machining industry, Computer Numerical Control (CNC) machines have become indispensable due to their speed, accuracy, and user-friendly nature. However, despite their numerous advantages, achieving optimal quality control with CNC machines is crucial. Unfortunately, many facilities still lack robust CNC quality control systems.
CNC Quality Control: Ensuring product quality is of paramount importance in CNC machining, and organizations employ quality control measures to meet customer demands and industry regulations. This involves the use of specialized tools and instruments to measure and evaluate various components and aspects of the manufacturing process.
Why Quality Control is Essential: While CNC machines reduce errors compared to manual processes, they are not immune to mistakes. Errors can lead to bottlenecks, waste, and damage to client relationships due to subpar product quality. Implementing an effective quality control program is vital to identify and address errors promptly, enhancing the entire machining process.
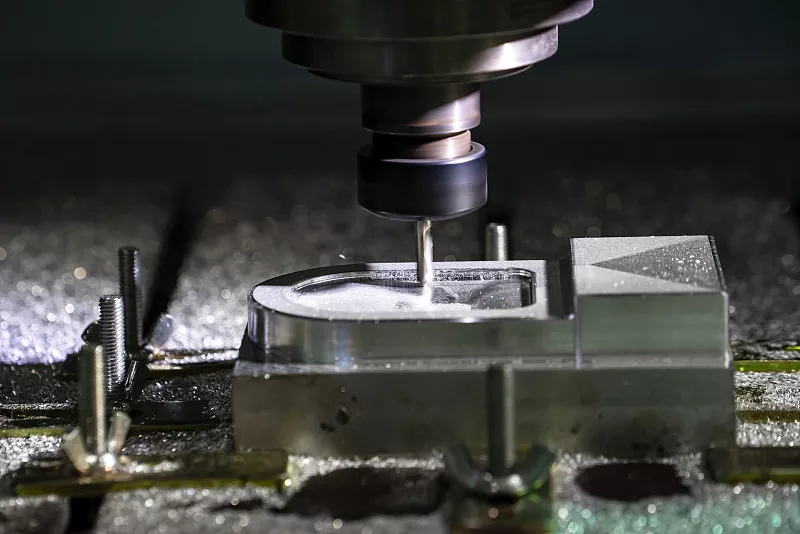
Capable Machining’s Recommended CNC Quality Control Techniques:
- Establish Quality Control Processes:
- Clearly define quality standards and specifications for machined parts.
- Create detailed inspection plans with specific inspections and tests at various stages.
- Provide comprehensive training to personnel on inspection procedures and equipment usage.
- Implement effective communication systems to report and address potential issues.
- Proper Machine Maintenance:
- Develop a maintenance schedule based on manufacturer recommendations.
- Regularly clean the CNC machine from chips, debris, and coolant residues.
- Monitor and maintain proper spindle lubrication and cooling systems.
- Inspect and maintain cutting tools, holders, and tool changers regularly.
- Stay updated with the latest machine control software versions and firmware updates.
- Tooling and Workholding:
- Choose cutting tools appropriate for specific machining operations and materials.
- Regularly inspect and maintain cutting tools to ensure good condition.
- Implement effective workholding techniques to securely hold the workpiece.
- Ensure accurate workpiece positioning and alignment within the workholding device.
- Enhance rigidity and stability of the workholding setup to minimize vibrations.
- Final Inspection and Testing:
- Establish clear inspection criteria based on product specifications and customer requirements.
- Utilize appropriate inspection tools and equipment for accurate measurements.
- Measure critical dimensions and inspect surface finish against specified tolerances.
- Perform functional testing to validate the performance of the machined parts.
Benefits of Quality Control: Implementing a robust CNC quality control system offers several advantages, including reduced waste, improved efficiency, cost savings, and enhanced customer satisfaction. Adhering to stringent quality control standards sets companies apart from competitors and cultivates a strong reputation among customers.
Conclusion: CNC machining’s potential can only be fully realized when companies uphold stringent quality control standards. By following the recommended techniques and investing in a strong quality control program, machining processes can ensure accuracy, efficiency, and superior product quality. For valuable CNC machining services, companies can rely on Capable Machining for expert advice and assistance.