In recent years, CNC machining technology has experienced an evolution from simple machine tools to complex machine tools, and five-axis CNC machining technology has become one of the most advanced machining technologies today. The technology utilizes cutting tools that move in five axes to subtractively manufacture complex parts, offering unlimited design possibilities.
Five-axis machining has significantly improved machining accuracy, efficiency and reliability, has better performance than traditional machine tools, and can achieve full automation and precise control. It has become a key technology in modern CNC machine tool workshops, promoting technological progress in the manufacturing industry and development in application fields. Extension.
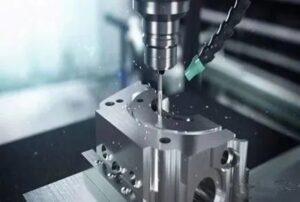
Advantages of 5-axis CNC machining
1.Higher machining accuracy
By precisely controlling the movement of the cutting tool on five axes, 5-axis CNC machining can achieve high-precision machining of complex geometries and curved surfaces, with superior machining accuracy than traditional three-axis or four-axis machine tools.
2.Enhanced machining capabilities
5-axis CNC technology allows the cutting tool to move freely at multiple angles and planes, and can handle more complex and three-dimensional workpieces, providing greater design freedom and innovation space.
3.Improve machining efficiency
Compared with traditional machine tools, 5-axis CNC machining reduces the repeated clamping and adjustment of workpieces during machining, thereby saving production time and improving machining efficiency.
4.Reduce production costs
Despite the high initial investment, 5-axis CNC machining can complete the machining of complex parts in a single machining process, reducing the need for manual operation and secondary machining, and reducing overall production costs.
5.Wide range of applications
5-axis CNC technology is suitable for a variety of materials, including metals, plastics and composites, and is widely used in high-end manufacturing fields such as aerospace, automotive manufacturing, and medical equipment, providing customized, high-precision machining solutions for various industries.
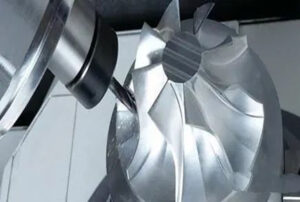
Disadvantages of 5-axis CNC machining
1.High initial cost
The cost of purchasing a 5-axis CNC machine and its basic software is high. It is much higher than that required for a 3-axis machining center. Similarly, the maintenance requirements of the machine are more challenging than those of traditional machines. This aspect also directly increases the machining cost of 5-axis machined parts.
2.Difficult programming
The two additional rotational movements and the spatial trajectory of their movements are abstract and complex. For example, to process free-form surfaces, you need to transform coordinates multiple times; perform complex spatial geometric operations; and consider the coordination of the movements of each axis.
All of this is necessary to avoid collisions and interferences and to ensure the correct amount of interpolated motion. Therefore, programming is more difficult to achieve the required machining accuracy and surface quality.
3.Higher requirements for operators
5-axis CNC milling is an advanced technology that involves advanced programming, machine tool setup, and operation. Therefore, the process requires highly skilled technical operators. This usually means an increase in labor costs.
4.Make full use of 5-axis CNC machining
Underutilization of 5-axis functions is a common situation. Some operators do not understand the full capabilities of the machine. Others may not have the programming knowledge for cutting-edge operations.
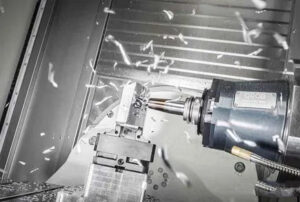
Common Applications of 5-Axis CNC Machining
1.Aerospace Components
The aerospace industry requires components with organic shapes, contoured edges, and compound shapes. The unique and geometrically complex parts make 5-axis machining an ideal technology choice. The process achieves a high level of detail and reduces the need to re-fixture the cutting head. As a result, parts for aerospace applications remain as precise as possible and meet industry standards.
2.Medical Devices
When manufacturing medical devices, quality and precision cannot be compromised. The high-precision capabilities of the 5-axis manufacturing process help produce implants, devices, and other equipment to meet stringent healthcare requirements. Most components are small and complex, or sophisticated electronic scanning and monitoring equipment. 5-axis technology provides an efficient and cost-effective method for producing these parts.
3.Energy Production
The energy industry often requires complex and advanced components, including solar power systems and power stations. The rapid emergence of 5-axis machining ensures CNC precision machining of detailed and specific parts for energy equipment. These parts are machined to be durable and provide stability to the workspace.
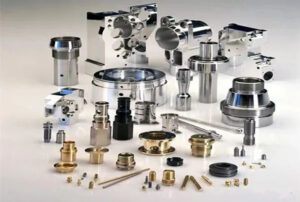
Conclusion
Five-axis CNC machining technology, with its high precision, complex geometric processing capabilities and wide application areas, is suitable for machining parts that require high precision, complex design, and variable surfaces. Especially in industries such as aerospace, automobile manufacturing, and medical equipment, this technology can provide key support for innovative design and high-quality production.
Whether it is complex structural parts, fine parts, or surfaces and apertures that require high-precision machining, five-axis CNC machining can effectively respond, providing companies with reliable machining solutions and driving the manufacturing industry forward.